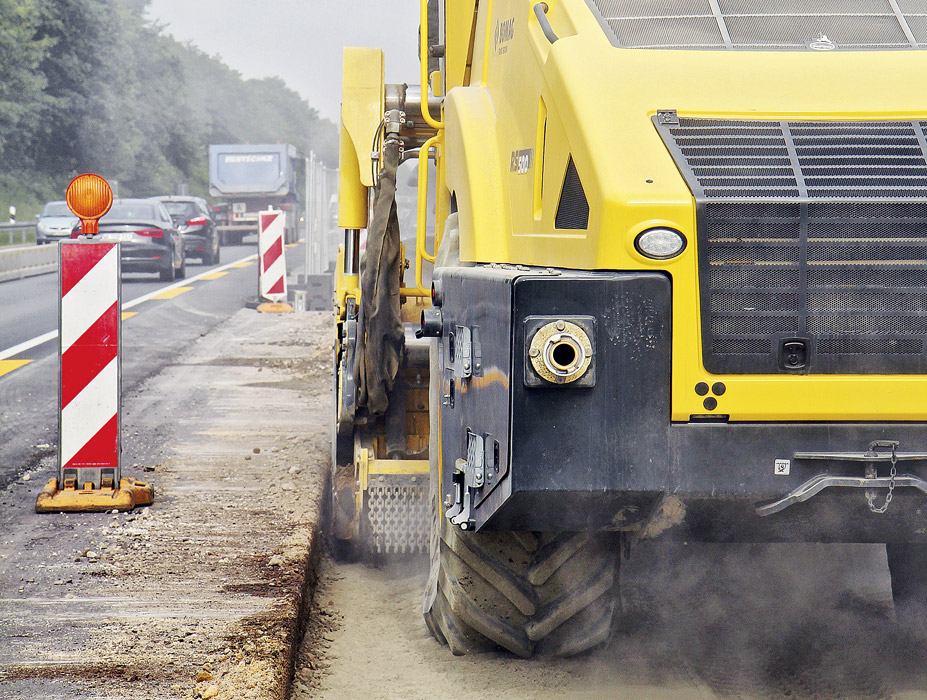
Применение колесных и гусеничных холодных ресайклеров
Преимущества и недостатки холодного ресайклинга
Прежде всего это высокая экономичность. Технологии ХР дешевле традиционных методов ремонта за счет вторичного использования материалов (экономии на стоимости материалов) и экономии на их транспортировке. При традиционной технологии снятый старый материал дорожных одежд необходимо вывозить, утилизировать (платить за это) и приобретать новый. ХР предполагает практически 100%-ное использование старого материала, и если применяется технология «на месте», не нужно его перевозить. По некоторым приблизительным оценкам, экономия может составить 20–30%, причем, чем выше интенсивность движения по ремонтируемой дороге, тем выше экономический эффект метода ХР.
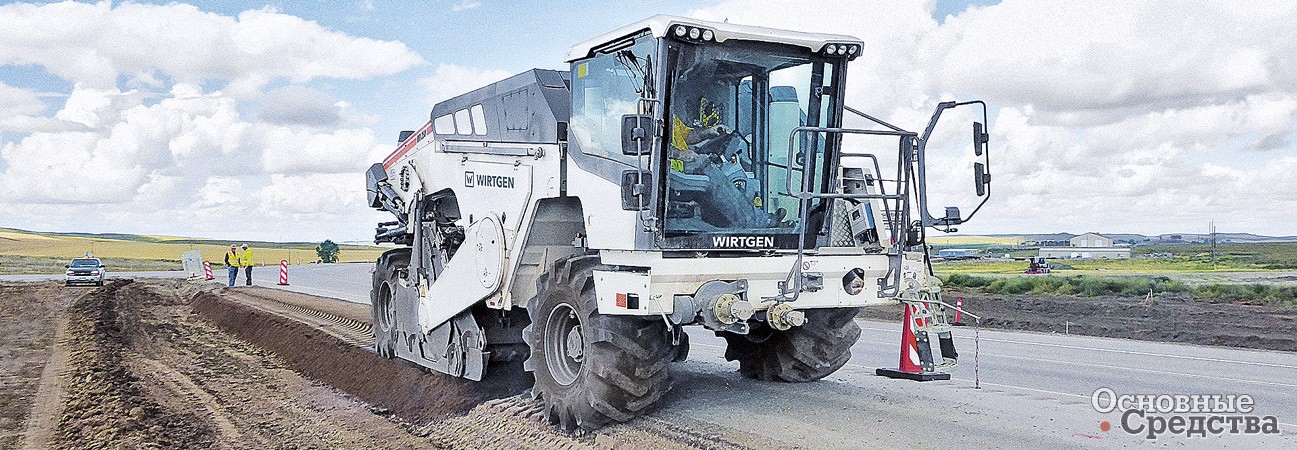
Экономится рабочее время за счет ускорения темпов ремонтных работ: комплекс машин холодного ресайклинга может обработать около 700–1000 пог. м. за смену. Технология ХР не предъявляет жестких требований к выбору материалов и применения той или иной технологии, возможен выбор разных вариантов для того, чтобы получить нужный результат, т. е. определенные физико-механические свойства отремонтированного слоя дорожной одежды. Можно использовать не только асфальтобетон, но и цементобетон, который добавляется в слои основания. Могут быть улучшены физико-механические свойства материала, вплоть до того, что дорогу после ресайклинга можно перевести в более высокую категорию. Эта технология удобна для применения в удаленных регионах нашей страны, где недостаточно развита инфраструктура.
Однако при выполнении ХР получаемый профиль полностью повторяет профиль предыдущего покрытия, все неровности и неправильные углы уклона. Чтобы исправить эти дефекты, на стадии проектирования ремонта участков с неровным профилем рекомендуется предусматривать устройство слоев выравнивания из щебня перед ресайклированием или предусматривать устройство выравнивающих слоев из пористого асфальтобетона после ресайклирования.
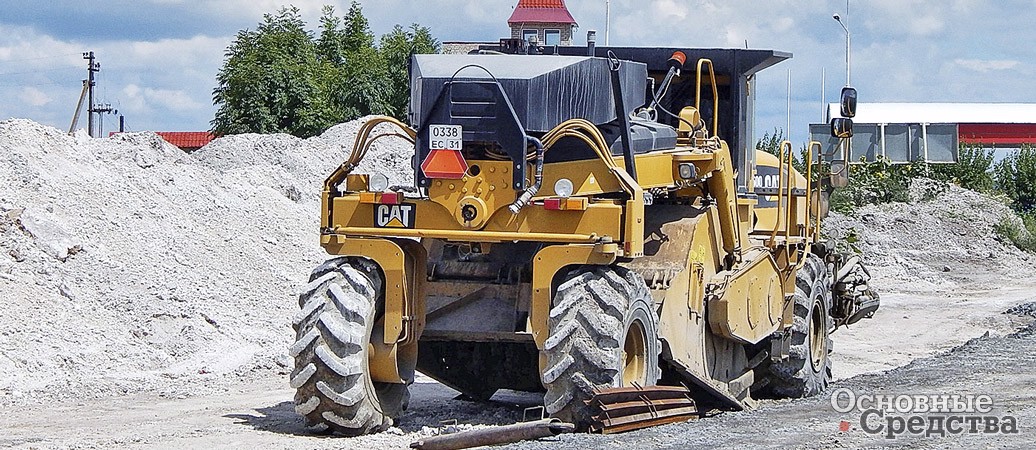
Холодный ресайклинг «на месте» и «на заводе»
В технологии ХР можно выделить два основных метода производства новой смеси: «на месте» и «на заводе».
Технология смешивания «на месте», как видно из названия, предполагает проведение работ непосредственно на месте ремонта. Существенный плюс смешивания «на месте» – экономия на транспортных расходах. Однако при выполнении ХР дорожных одежд с неоднородным составом материалов по горизонтали, ресайклирование «на месте» не позволяет повысить однородность. Материал перемешивается практически только по вертикали, по горизонтали перемещение частиц материала составляет не более 200 мм.
Для того чтобы исправить этот недостаток и повысить однородность смеси в горизонтальном направлении, рекомендуется перед производством работ через каждые 400–600 м определять содержание в существующем покрытии вяжущего и минеральных составляющих, а также гранулометрический состав для корректировки в дальнейшем состава рециклированной смеси.
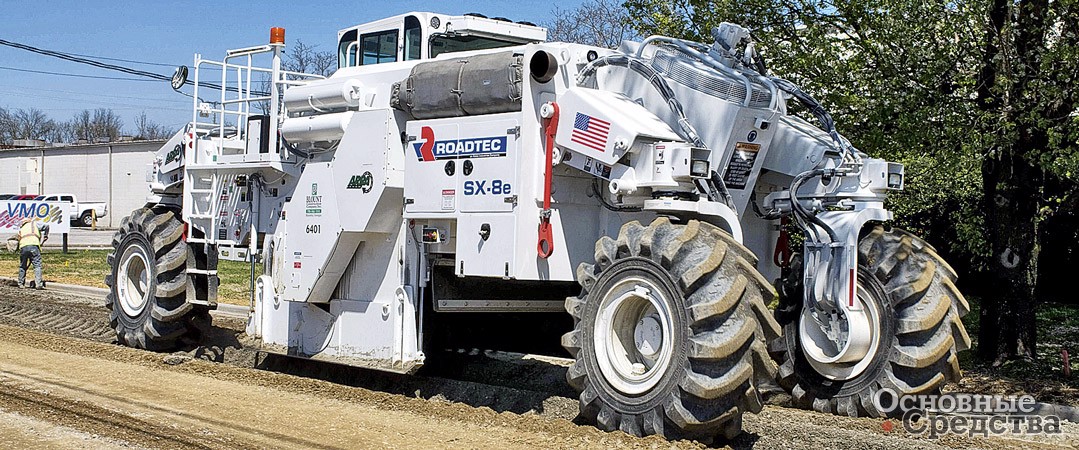
Технология «на заводе» предполагает вывоз сфрезеровованного материала на завод или на площадку, удаленную от места работ, где крошка перемешивается с вяжущими в специальной установке и приготовленная смесь возвращается обратно на место работ, где из нее укладывают слой. Данный метод используется преимущественно в случаях, когда предъявляются повышенные требования к качеству смешивания (например, при высокой неоднородности состава материала по длине ремонтируемого участка), требуется сортировка материала или устройство дополнительных слоев. Преимущество смешивания «на заводе» в том, что материалы можно хранить и использовать, когда нужно.
При капитальном ремонте федеральных магистралей 1-й категории, когда затрагиваются либо полностью заменяются слои основания, по-видимому, наиболее практичным будет комбинированное использование обоих методов: «на месте» и «на заводе» – верхний слой на глубину 150 мм сфрезеровывается, вывозится и складируется на площадке. Производится ресайклинг дорожных одежд на глубину 200 мм со стабилизацией вяжущими. На площадке крошка перемешивается с вяжущими и затем укладывается толщиной 150 мм на ресайклированный слой. Сверху укладывается защитное покрытие из горячей асфальтобетонной смеси толщиной 40 мм.
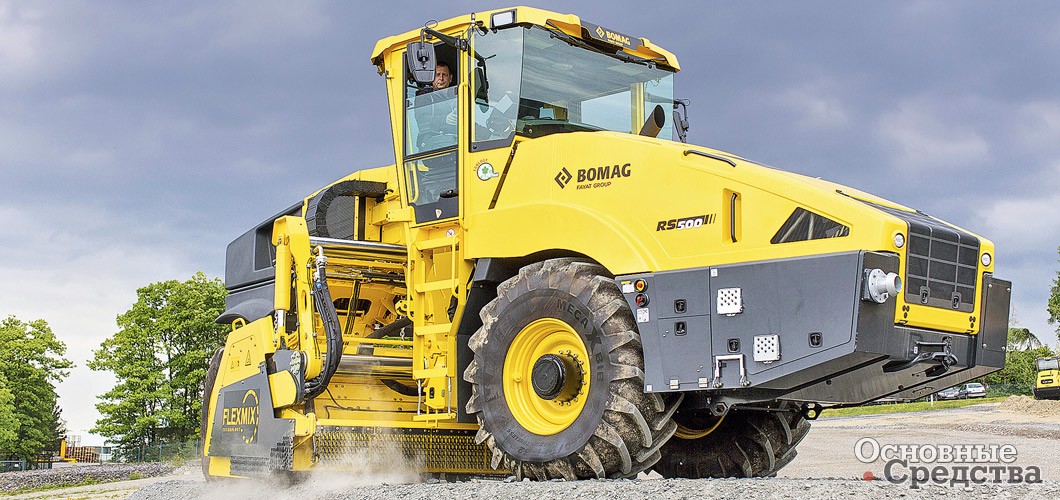
Глубокий и мелкий ресайклинг
Различают ресайклинг глубокий и на небольшую глубину.
Если нет больших разрушений дорожных одежд, возможно провести ресайклинг на глубину до 10–15 см слоя асфальтобетона. В этом случае можно придать нужные физико-механические свойства свежеобразованным слоям путем добавления небольшого количества комплексного вяжущего.
ХР на больших глубинах, например 24–26 см, производится, когда разрушения уже проникли в глубину пакета слоев дорожных одежд. При ресайклировании с захватом нижних слоев рекомендуется добавлять в смесь не более 4–5% цемента. Опыт показывает, что при содержании в смеси 6% цемента на следующий год весной на покрытии возникают отраженные трещины из-за высокой жесткости материала.
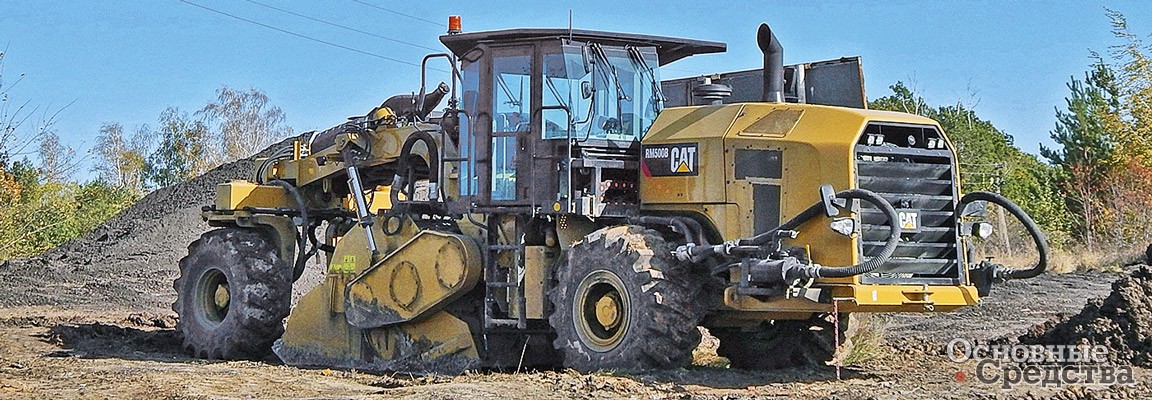
Вяжущие
При ХР в гранулят добавляют вяжущие: «неорганические» (цемент, известь) и «органические» (битумная эмульсия, вспененный битум).
В тех регионах, где существуют трудности с доставкой органических вяжущих, но есть цементный завод, можно выполнить ХР только с цементом. Цемент дешевле битума, проще распределяется, методы его испытаний стандартизованы, хорошо знакомы и освоены, а прочность смеси получается выше. Такие смеси обычно не реагируют на изменения температуры окружающего воздуха. Но если содержание цемента будет превышено или будет неправильно выбрано соотношение воды и цемента, то в покрытии могут появиться усадочные трещины. Возможна неравномерность распределения. Повышается жесткость дорожных одежд. Приходится запрещать движение по отремонтированному покрытию от 1 до 3 суток, пока цемент не наберет прочность хотя бы 60% от нормы.
К тому же при использовании асфальтобетонных смесей с минеральными вяжущими нецелесообразно сразу же открывать движение, т. к. основание сразу после высыхания начинает пылить. В таких случаях необходимо помимо увлажнения обрабатывать поверхность пленкообразующими материалами. Замыкающий слой или слой усиления может быть уложен сразу или в течение 48 ч после ресайклирования нижележащего слоя. Устройство вышележащего замыкающего слоя из асфальтобетона не следует откладывать более чем на 3–5 дней.
Ресайклинг с органическими вяжущими тоже имеет свои плюсы и минусы. Битумная эмульсия и вспененный битум – традиционные знакомые продукты – применяются просто. В результате их использования получаются полужесткие дорожные одежды с низким водонасыщением, уложенный слой быстро набирает прочность, автомобильное движение можно открывать практически сразу после окончания работы. Битум обеспечивает изоляцию от проникновения воды внутрь материала.

Однако стоимость этих вяжущих довольно высока. Для вспенивания битум необходимо нагревать выше 160 °С, что не всегда осуществимо. Органические вяжущие плохо работают с пыльными материалами. В смеси появляется дополнительная влажность от влаги, которая содержится в вяжущих. К тому же органические вяжущие не всегда доступны в местных условиях.
Для укрепленных слоев с добавлением органических вяжущих устройство замыкающего слоя или слоя усиления из асфальтогранулобетонной смеси (АГБ) поверх рециклированного слоя рекомендуется отложить на 5–8 дней, что позволяет последнему лучше сформироваться под действием движущегося транспорта. Таким образом, при выполнении холодными ресайклерами для получения качественного основания дорожных одежд необходимо строить временные объездные дороги.
Поскольку у каждого типа вяжущих имеются свои преимущества и недостатки, опыт показывает, что лучше всего работают комбинации вяжущих.
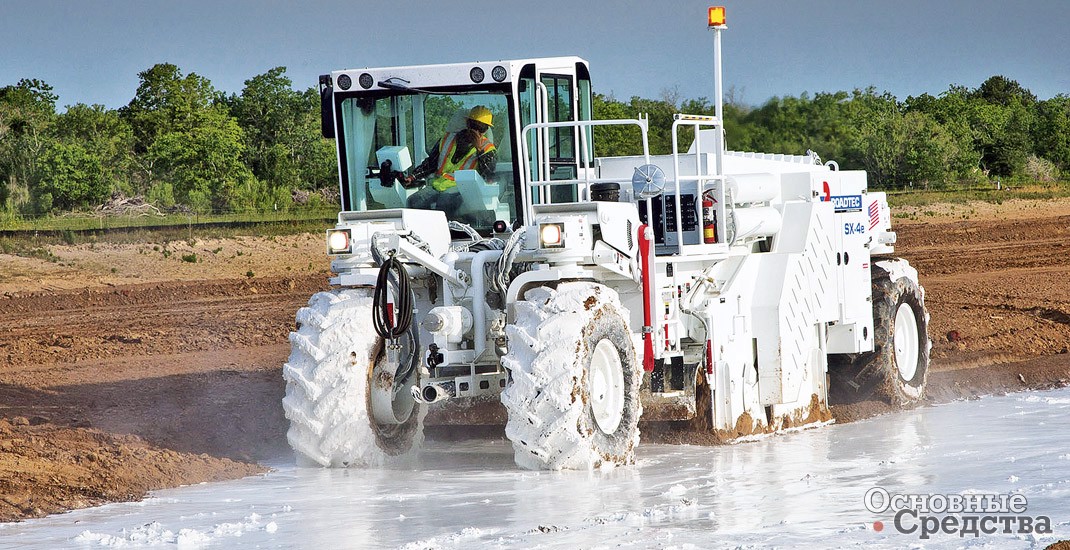
Выбор способа ремонта
Для того чтобы определить тип применяемого ХР: на малую, на большую глубину, или полная замена, выбрать материалы (вяжущие), необходимо выяснить, что потеряло необходимую прочность – покрытие, основание или земляное полотно, проанализировать наличие и вид дефектов покрытия, а также конструкцию дорожного полотна, какие физико-механические свойства желательно придать вновь полученному покрытию и какие финансовые средства отпущены на выполнение данного проекта.
После рециклирования производится укладка либо защитных слоев износа, либо асфальтобетона, потому что отрециклированный органо-минеральный слой не обладает необходимыми эксплуатационными характеристиками – коэффициентом сцепления и др.
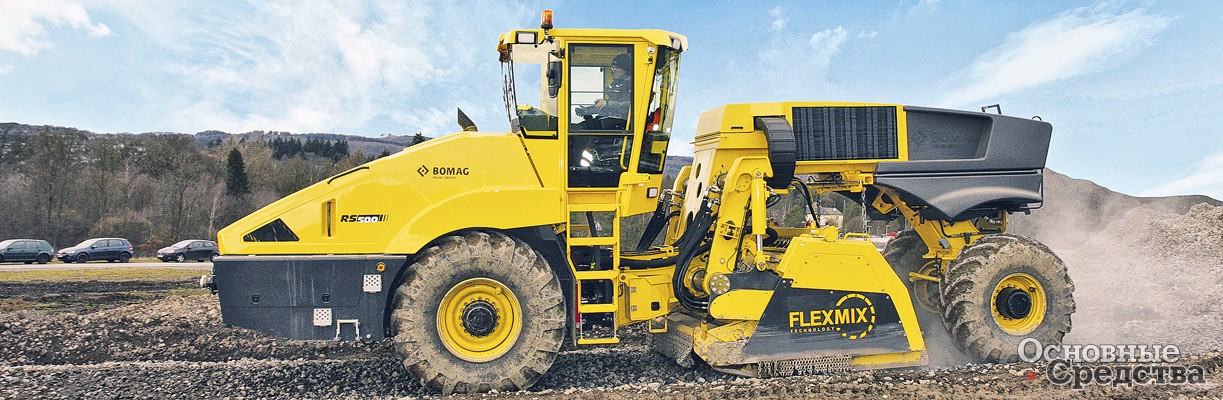
Нормативная база
В настоящее время в России существует проблема с нормативной базой по применению технологии ХР. Еще в 2002 г. Минтрансом РФ были выпущены «Методические рекомендации по восстановлению асфальтобетонных покрытий и оснований автомобильных дорог способом холодной регенерации», в которых приведены требования к механическим свойствам асфальтогранулобетонных смесей (АГБ-смесей) и другие расчетные характеристики слоев основания из различных типов АГБ-смесей. Этими данными рекомендуется руководствоваться при проектировании ремонта дорожных одежд методом холодного ресайклинга.
Однако данный документ был разработан исключительно на основе зарубежного опыта и зарубежных технических документов. При составлении этих рекомендаций не был привлечен опыт профильных российских научных учреждений и практикующих дорожно-строительных организаций. Как показывает практика, расчетные значения кратковременного модуля упругости, приведенные в методическом документе, для российских условий чаще всего не соответствуют действительности, а значения физико-механических характеристик АГБ-смесей требуют уточнения.
Например, качество обводнения слоя в этом методическом документе рекомендуется проверять с помощью радиоизотопного прибора. Однако радиоизотопные приборы для контроля плотности в нашей стране неудобны для применения, т. к. у нас очень жесткие правила радиационной безопасности. Также коэффициент уплотнения смеси рекомендуется контролировать по кернам, отобранным через 7 суток после устройства слоя. По опыту можно сказать, что из готового слоя отобрать керны через 7 суток очень сложно, т. к. материал слоя еще не набрал прочность и в процессе отбора кернов часть их разрушается.
Необходимо разработать новый нормативный документ в тесном сотрудничестве разработчиков с отечественными дорожно-строительными организациями, имеющими практический опыт применения этой технологии. Ряд ведущих российских компаний уже разработали собственные нормативные документы и рекомендации по применению ресайклинга.
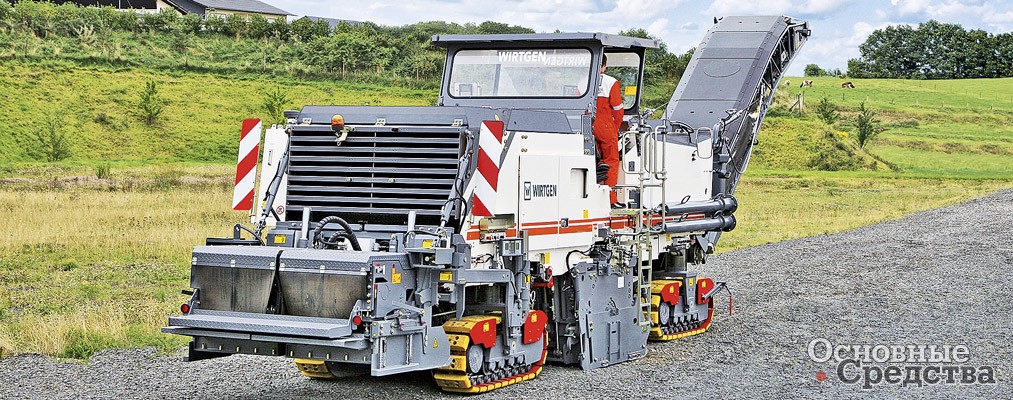
Гусеничные и колесные ресайклеры
Колесные фрезы/ ресайклеры используются, когда необходимо перемешивание с участием верхних слоев основания на большую глубину, как показывает практика, до 250 мм. В некоторых условиях возможно и больше, но предварительно требуется выполнить пробный проход, чтобы оценить, справится ли машина с рабочей нагрузкой при рециклировании существующей конструкции дорожной одежды. По результатам пробного прохода может быть, например, принято решение о дополнительном фрезеровании, чтобы облегчить работу ресайклера.
Гусеничные фрезы (они же ресайклеры, т. е. машины двойного назначения) используются при текущем и капитальном ремонте слоев дорожного покрытия и верхних слоев основания. Максимальная глубина ресайклируемого слоя за один проход – до 200 мм.
Преимущество гусеничного ресайклера в том, что существующее дорожное покрытие измельчается, непосредственно в камеру смешения добавляется вяжущее, после этого новая смесь распределяется шнеками и попадает под выглаживающую плиту. Можно сразу получить покрытие с необходимыми высотными отметками и предварительным коэффициентом уплотнения – получается чистовая ровность, в отличие от той ровности, которая получается после колесной машины. С помощью колесной машины очень сложно достичь окончательной ровности. Как правило, после колесной машины требуется еще использовать грейдер. В случае гусеничной машины грейдер можно не использовать.
Обзор техники для ресайклинга
На отечественном рынке представлены главным образом ресайклеры производства Bomag, Wirtgen и Caterpillar. В меньшей степени распространены (в основном подержанные) американские машины Terex, Roadtec и итальянские FAE, Bitelli. Выходят на российский рынок и китайские компании Sinomach и XCMG.
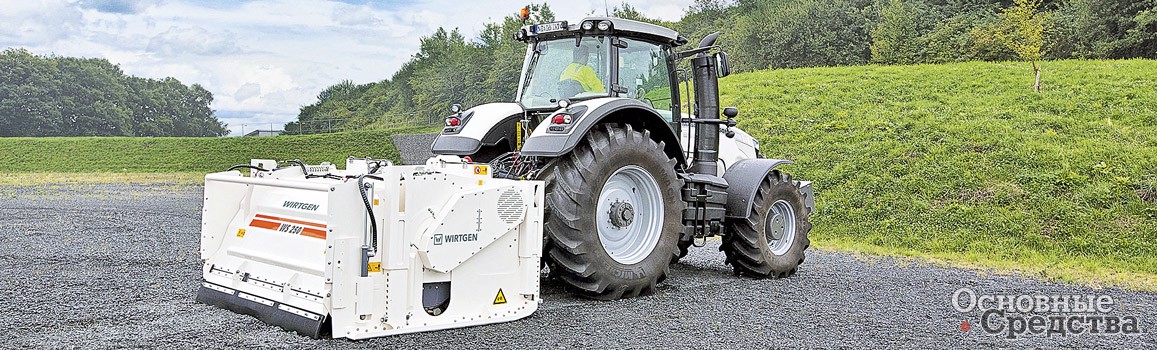
Wirtgen. Конструкторами Wirtgen разработаны прицепные стабилизаторы грунта мод. WS 220, WS 250, а также самоходные холодные ресайклеры/ стабилизаторы грунта пневмоколесные серии WR и гусеничные серии CR.
Мод. WR200, WR240 и WR250 – универсальные машины с двигателями мощностью 315–571 кВт, предназначенные для фрезерования дорожного покрытия на глубине по асфальту до 200 мм. Стабилизация грунта производится на глубину 510 мм и более.
Универсальная фреза/ ресайклер 2200CR с двигателем мощностью 597 кВт – принципиально иная машина. Резцы на барабане имеют винтовое расположение, что позволяет собирать материал в валик и перемешивать его не только в вертикальном, но и в горизонтальном направлении, повышая однородность. Благодаря большой массе она может работать с толстыми слоями асфальтобетонной смеси (АБС), производить стабилизацию грунтов на глубину до 350 мм. В мод. 2200CR есть распределительный шнек и выглаживающая плита, а также две рампы и два ряда форсунок, через которые в смесь добавляется органическое либо комплексное вяжущее.
Самая большая машина среди гусеничных ресайклеров мод. WR 4200 (несмотря на индекс WR, это гусеничная машина) – практически целый завод с двумя двигателями мощностью по 433 кВт каждый, которая самостоятельно может выполнять все операции: фрезерование, перемешивание и укладку АБС. Мощные фрезы, шнековая камера, фрезерные барабаны, причем два крайних барабана перемещаются по горизонтали, винтовое расположение резцов на барабане, которые закидывают смесь в мешалку. Мощный 2-валовый смеситель перерабатывает не менее 300 т/ч и обеспечивает высокое качество смеси – намного выше, чем у других ресайклеров. Распределительный шнек может уменьшаться в зависимости от требуемой ширины обработки, смесь предварительно уплотняется с помощью вибробруса и виброплиты асфальтоукладчика. Однако высокая рабочая масса Wirtgen WR 4200 несколько затрудняет ее доставку в отдаленные регионы.
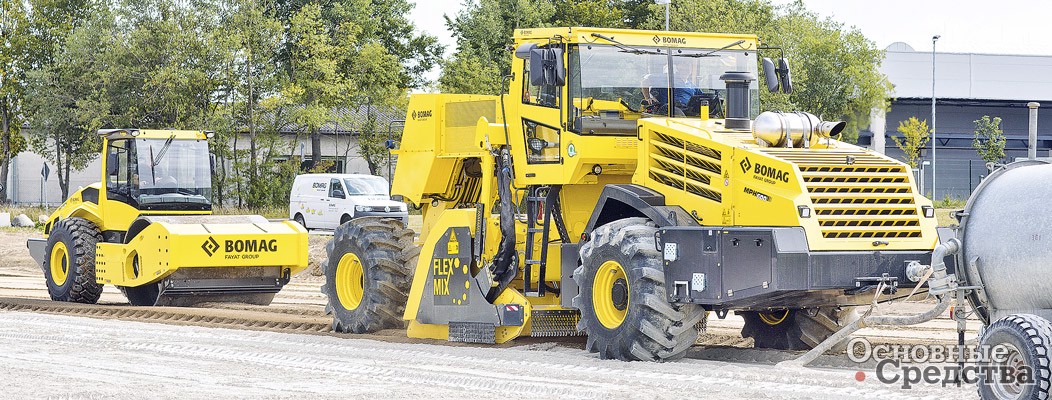
BOMAG. Компания BOMAG выпускает ряд моделей колесных ресайклеров и стабилизаторов грунта, из них в Россию поставляются модели немецкого производства MPH 364R-2, RS 460, RS 500 и MPH 600 в различных конфигурациях: с системой водяного орошения для работ по стабилизации грунта, с системой распыления битумной эмульсии, вспененного битума или цементной суспензии для работ по ресайклингу асфальтобетона. Кабины машин оснащены системами защиты ROPS/ FOPS, отопителем и кондиционером в стандартной комплектации. Сиденье оператора может перемещаться вправо и влево для удобства работы. Машины BOMAG отличаются высокой маневренностью и очень малым радиусом разворота за счет уникальной концепции выполнения поворота: с помощью сочлененной рамы и управляемых задних колес. Ротор имеет гидростатический привод с двумя планетарными редукторами и двумя гидромоторами, которые обеспечивают 11 режимов вращения ротора (с переключением режимов непосредственно во время работы), из которых всегда можно подобрать оптимальный для конкретных условий работы. Фирменная система резцедержателей BOMAG обеспечивает простую и удобную замену резцов и резцедержателей при их износе. Система смешивания материала BOMAG FlexMix обеспечивает возможность изменения величины фракции материала на выходе. Дозирование всех добавок в смесительную камеру осуществляется высокоточным компьютером, который поддерживает подачу требуемого процента добавок на единицу объема рабочего материала при любой скорости и рабочей глубине.
Отдельно стоит упомянуть новинку – модель ВОМАG RS 500. Благодаря гидростатическому приводу ротора вся смесительная камера с ротором на мощных телескопических направляющих с помощью гидроцилиндров сдвигается вправо/ влево на 30 см. Это дает возможность машине работать справа и слева с нулевым зазором, например, вплотную к препятствиям или к уже отработанному участку без перекрытия следа. Также это дает возможность машине безопасно работать на откосах без риска переворота – колеса остаются на стабильном основании, а ротор работает вплотную к откосу. К тому же эта машина находится полностью в транспортном габарите.
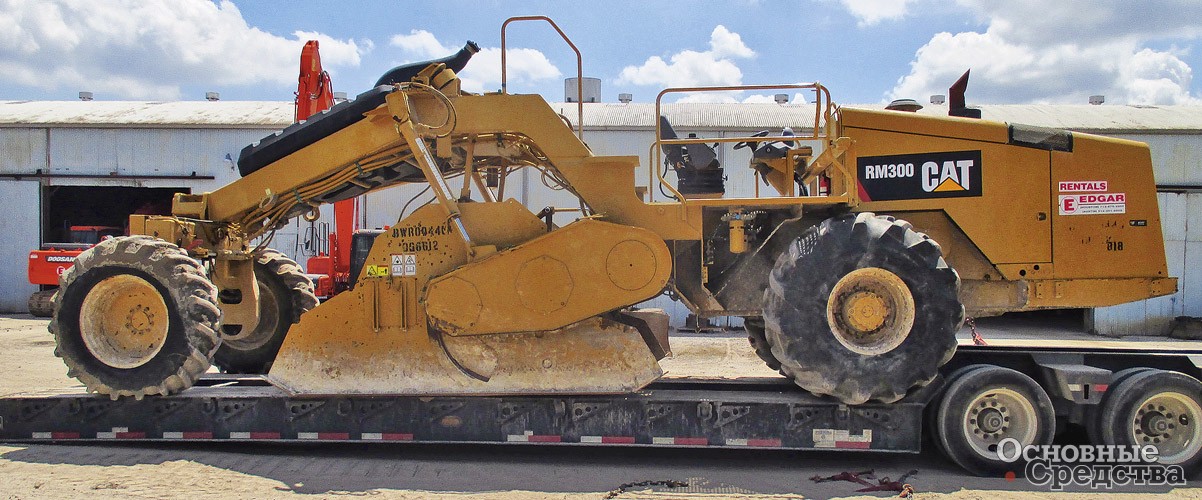
Caterpillar. На нашем рынке компания реализует универсальные колесные роторные ресайклеры/ стабилизаторы мод. RM 300, RM 500 и RM 500В. Глубина обрабатываемого слоя грунта у этих машин может достигать 500 мм. Мощность двигателя: у мод. RM 300 – 261 кВт, а у RM 500 и 500В – 403 кВт.
Кабина оснащается системой видеокамер (спереди и сзади, по заказу – в смесительной камере), защитой ROPS и может смещаться вправо-влево для улучшения обзора. Машина комплектуется телематическим оборудованием Product Link.
Предлагается на выбор несколько типов роторов, которые несложно заменить. Зубья движутся снизу вверх. Привод ротора – механический с электронным управлением. Ротор имеет три скорости вращения, которые выбираются в зависимости от нагрузки, глубины фрезерования и других условий. Гидравлическая регулировка компонентов смесительной камеры позволяет получить гомогенизированную смесь с заданным размером фракции, причем как при прямом движении машины, так и при движении задним ходом. По заказу может быть установлена система дозирования подачи воды и битума. Ходовая часть имеет гидростатический привод и четыре режима рулевого управления. Рабочая скорость машин составляет 4,3 км/ч.
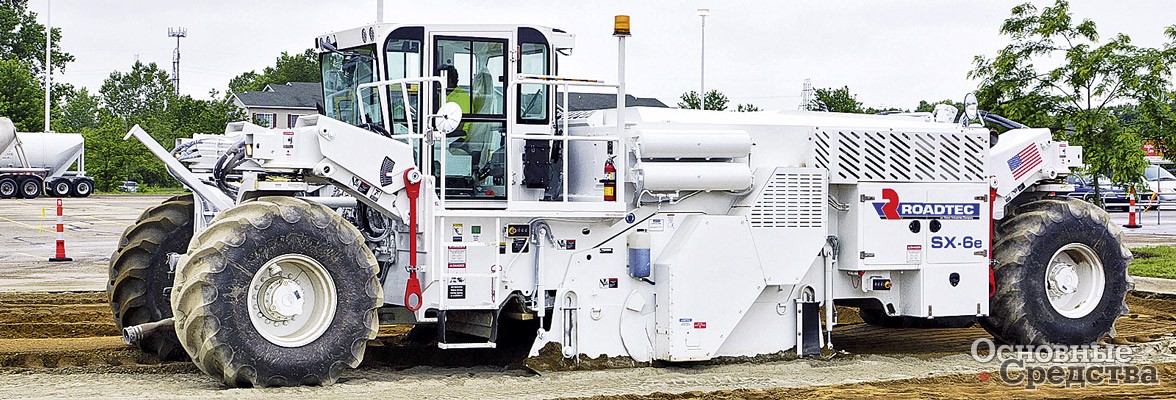
Roadtec Inc. Roadtec (входит в Astec Industries, Inc.) демонстрирует своеобразный подход к созданию оборудования для холодного ресайклинга. Американская компания предлагает гусеничные фрезы/ ресайклеры серии RX, т. е. установку комплектов оборудования для холодного ресайклинга CIR с электронным управлением на ряд моделей своих дорожных фрез. Электронное управление регулирует скорость движения машины и работу всех прочих систем, оператору достаточно ввести значения ширины и глубины фрезерования. Машины Roadtec RX оснащены двигателями мощностью 497–708 кВт, способны фрезеровать при движении вперед и задним ходом. Направление движения резцов также может изменяться: снизу вверх и сверху вниз для улучшения измельчения материала. Система управления обеспечивает подачу в смесительную камеру и дозирование до трех вяжущих одновременно (например, битум, битумную эмульсию и цементно-водную суспензию). Также обеспечивается промывка системы подачи вяжущих веществами-антиадгезивами. Промывка гарантирует исправную работу системы. Все модели предлагаются в двух вариантах: на четырех или на трех гусеничных тележках, оснащаются системой пылеподавления, по двум рампам в кожух фрезы подается и распыляется вода.
Можно еще упомянуть линейку колесных стабилизаторов грунтов SX с двигателями мощностью 283–563 кВт и гидростатическим приводом. Штатная фреза может заменяться укороченной для увеличения глубины обрабатываемого слоя грунта.
Модель | Рабочая ширина, мм | Рабочая масса, т |
---|---|---|
Модели стабилизаторов грунта/ ресайклеров Wirtgen | ||
WS 220 | 2150 | 4,44–4,75 |
WS 250 | 2500 | 4,7–5 |
WR200 | 2000 | 23,9 |
WR240 | 2400 | 29,4 |
WR250 | 2400 | 31 |
2200CR | 2200 | 49,27 |
WR4200 | 2800–4200 | 77 |
Модели стабилизаторов грунта/ ресайклеров BOMAG | ||
MPH 364R-2 | 2005 | 18 |
RS 460 | 2250 | 24 |
RS 500 | 2250 | 25 |
MPH 600 | 2400/ 2600 | 28 |
Модели стабилизаторов грунта/ ресайклеров Caterpillar | ||
RM 300 | 2300–2438 | 22,685–24,729 |
RM 500 | 2438 | 22,685–28,145 |
RM 500В | 2438 | 27–28 |
Модели стабилизаторов грунта/ ресайклеров Roadtec | ||
RX-600ex-CIR | 1900–2184 | 27,7–29,03 |
RX-700-CIR | 2010–3050 | 36,3–38,1 |
RX-900-CIR | 2184–3810 | 34,7–37,2 |
SX-2e/ex | 2000 | 19,96 |
SX-4e/ex | 2000–2540 | 24,95–25,91 |
SX-6e/ex | 2540 | 33,18 |
SX-8e/ex | 3048 | 34,09 |