
Автогрейдеры
Типичные автогрейдеры оснащены тремя осями. Двигатель и привод установлены в задней части, и кабина водителя находится над задней тандемной тележкой осей. Передняя, третья ось является управляемой.
В середине рамы между передней и задними осями расположен широкий средний отвал. Этот отвал способен поворачиваться на 360°, изменять угол резания. Отвал дополнительно можно перемещать вбок и переворачивать вертикально на 90° в обе стороны. Таким образом возможно обрабатывать наклонные поверхности. Множество моделей автогрейдеров, кроме того, оснащены передним отвалом для того, чтобы распределять сыпучий материал или расчищать рабочие площадки от неровностей. Также можно найти у многих моделей автогрейдеров рыхлители-кирковщики с задней навеской, чтобы разрыхлять грунт.
На открытых горных работах автогрейдеры применяются при строительстве технологических дорог, где с их помощью проводят планировку проезжей части. Автогрейдер за счет своей конструкции способен также работать на наклонных площадках и откосах.
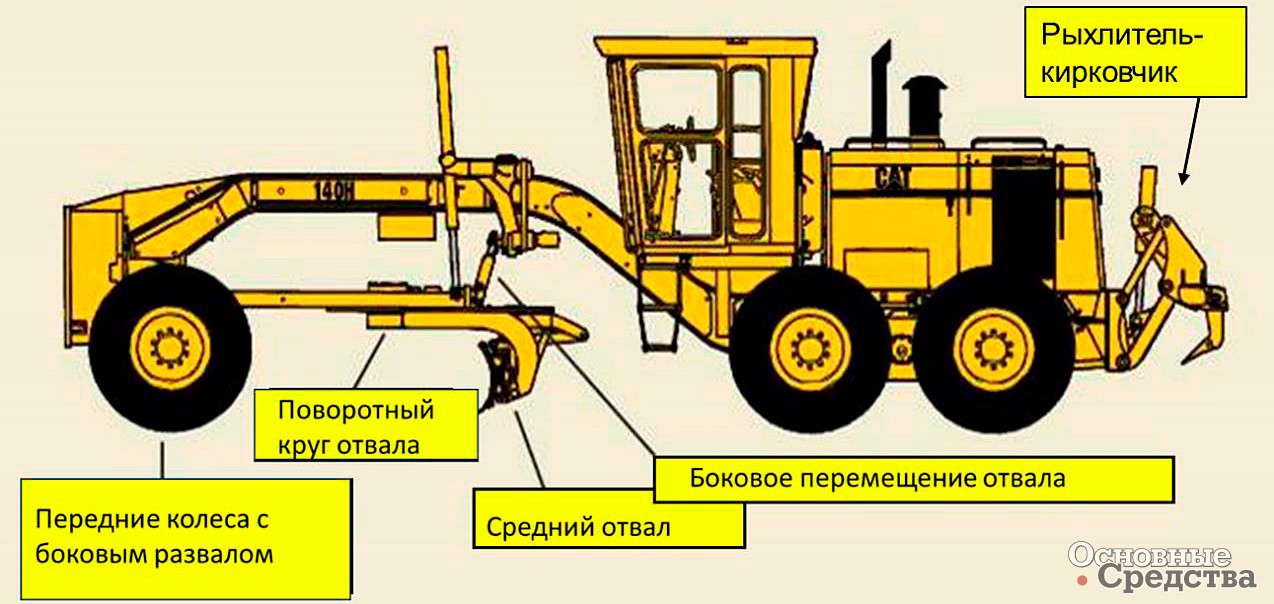
Модели автогрейдеров отличаются эксплуатационной массой. Другие характеристики – мощность двигателя, ширина главного (среднего) отвала и тип привода. Определяющий показатель – масса. Все остальные факторы связаны с главным показателем – эксплуатационной массой.
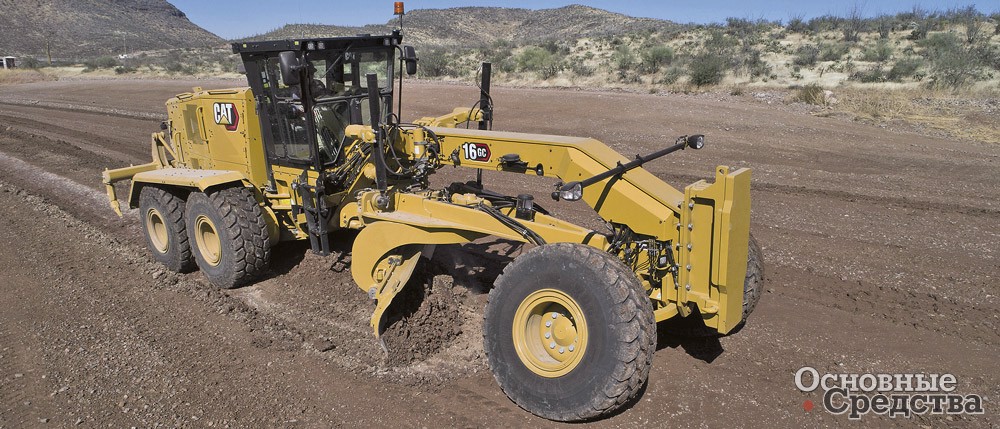
Современные автогрейдеры почти все оснащены шарнирно-сочлененной рамой. Такое решение позволяет машине передвигаться так называемым «собачьим ходом» (со смещением передних колес в поперечном направлении), чтобы поставить главный отвал вне рамы. Это весьма важно при обработке обочин дорог.
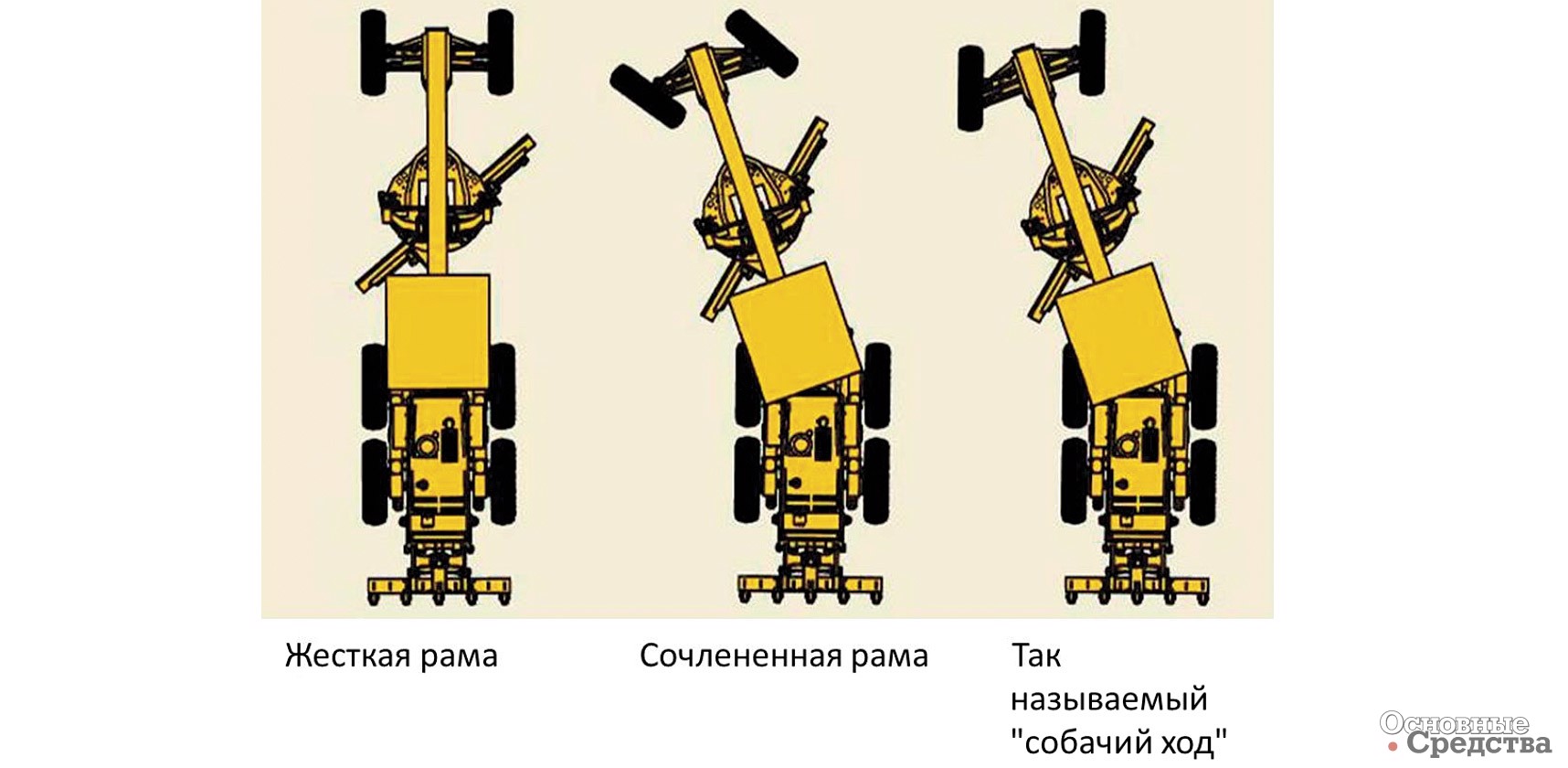
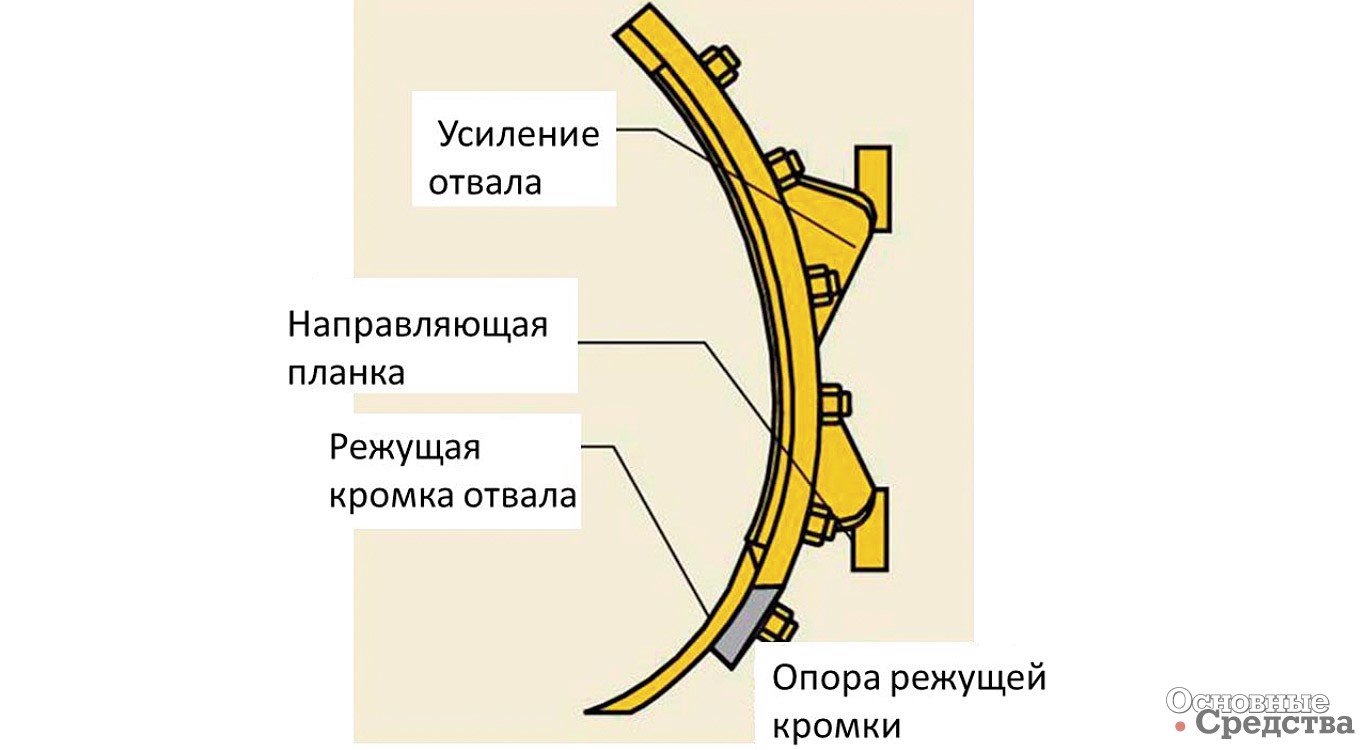
При планировке важно соблюдать определенные правила настройки главного отвала:
- верхняя кромка отвала должна находиться перед нижней;
- режущая кромка должна быть установлена под углом 90° к грунту.

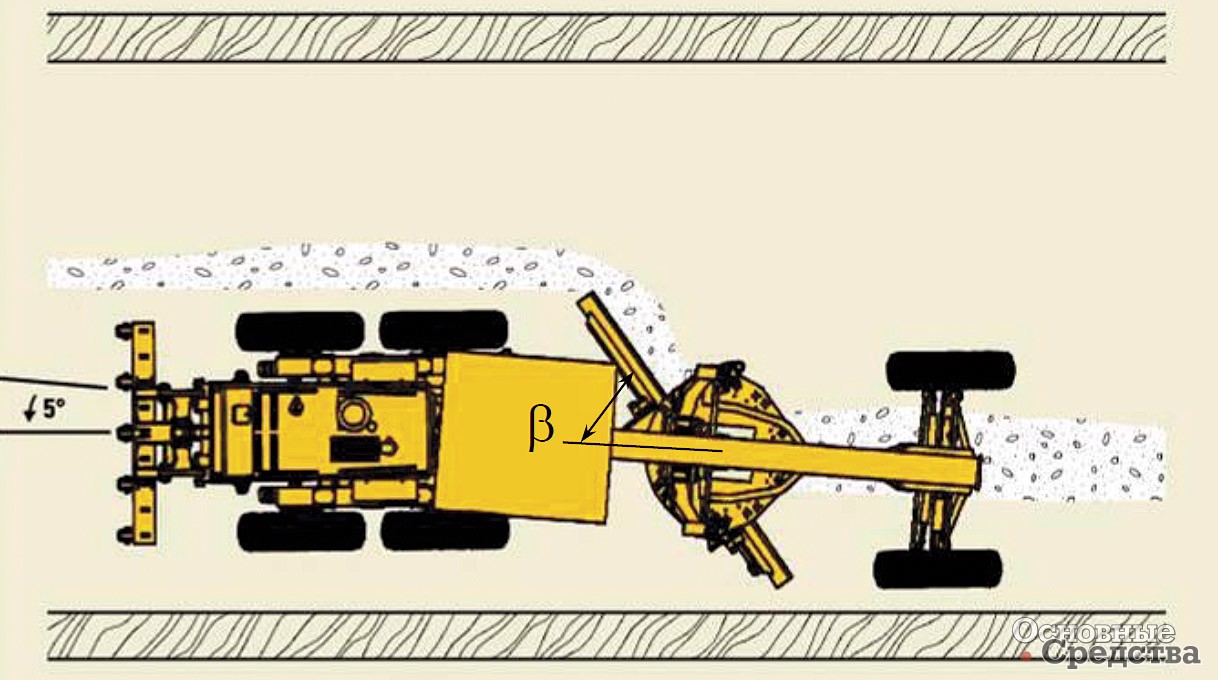
При разравнивании материалов отвал надо устанавливать под углом b не меньше 10° к направлению движения. Угол захвата, при котором достигается наибольшая эффективность планировки материала на площадке, зависит от вида обрабатываемого материала.
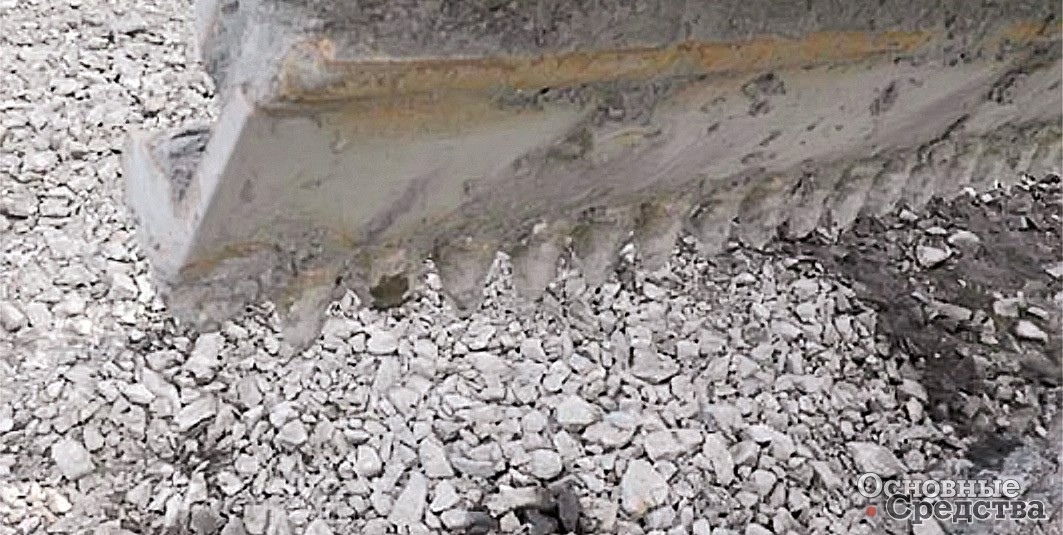
Для обработки абразивных грунтов, например щебня, на отвал устанавливаются сменные наконечники. На рис. 7 изображена режущая кромка с расходными наконечниками. Эти наконечники предотвращают быстрый износ режущей кромки отвала. Как правило, эти наконечники устанавливаются на болтах и без проблем могут быть заменены.
На следующем рисунке 8 показан автогрейдер, который обрабатывает склон. Углы наклона передних колес и рамы выбираются в зависимости от вида грунта, а наклон отвала – в зависимости от угла откоса (см. табл. 2).

Автогрейдеры помимо выравнивания площадок могут, конечно, применяться при выполнении других работ. С помощью главного отвала, к примеру, они могут убирать снег (см. рис. 9).
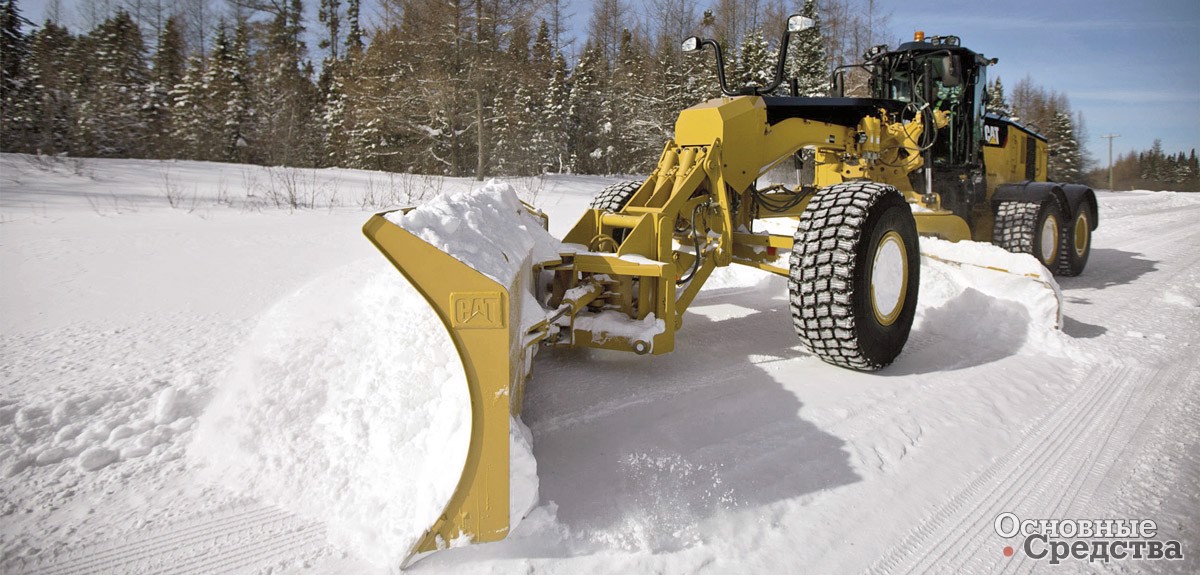
Применение специальных снегоочистительных отвалов дает возможность лучше убирать снег, чем с помощью отвалов для выравнивания грунта. Специальные передние отвалы ставят на грейдеры в местностях, где надо рассчитывать на большие и частые скопления снега.
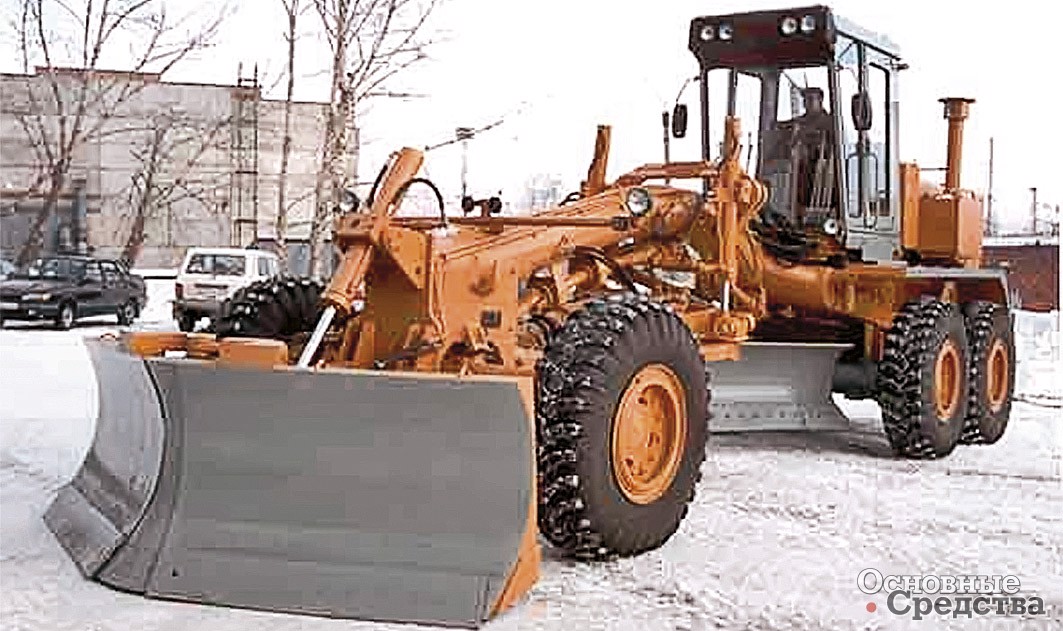
Во многих случаях целесообразно уплотнять обработанные площади после планировки. Для таких работ годятся виброплиты, которые ставятся вместо переднего отвала. С их помощью в большинстве случаев достигается достаточное уплотнение (рис. 11).
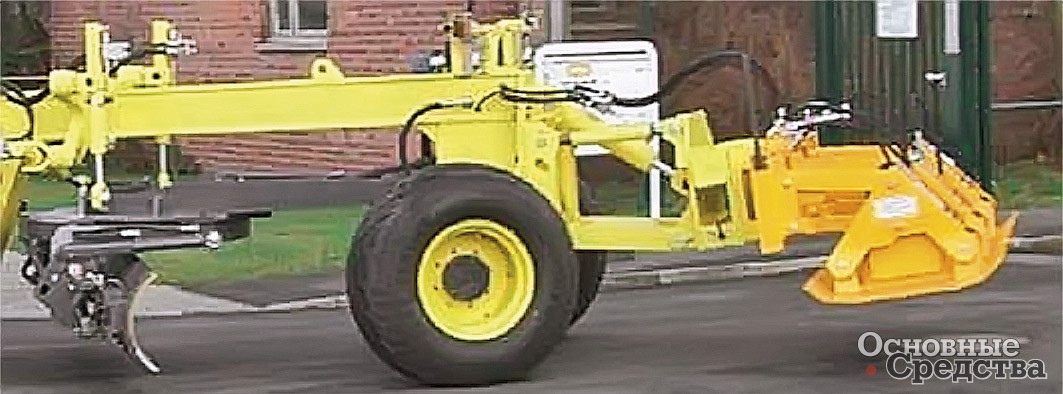
Прежде всего при обслуживании и ремонтных работах на дорогах может быть полезно разрыхлять материал посредством рыхлителя-кирковщика с задней навеской. После рыхления можно спланировать новую поверхность (см. рис. 12).
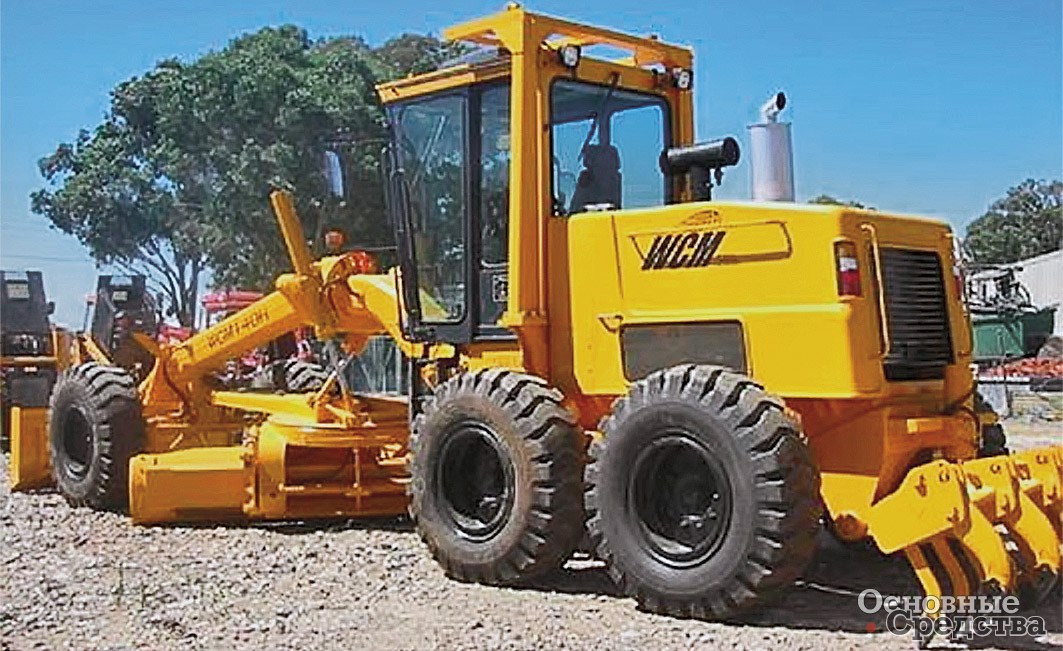
Современные автогрейдеры, работающие в карьерах, комплектуются главным образом коробками передач с переключением под нагрузкой, с гидротрансформатором. Гидротрансформатор оснащается блокирующей муфтой, которая жестко соединяет насосное и турбинное колеса. Автогрейдеры более легких классов, массой примерно до 10 т, часто оборудуются гидростатическим приводом.
При включении фрикционной блокирующей муфты КПД трансформатора становится равным 100%. В случае возникновения препятствия при работе автогрейдера, когда частота вращения двигателя падает, муфта отключается и гидротрансформатор работает в гидродинамическом режиме.
Более точные значения производительности автогрейдера рассчитываются с учетом типа привода и обработанной площади.
Обработанная площадь в свою очередь определяется шириной отвала и углом захвата отвала b (относительно направления движения). Далее производительность зависит от скорости планировки грунта, уклона рабочей площади и в конце концов от типа грунта.
![(м[sup]2[/sup]/час)](/article/28509-avtogreydery/F1.jpg)
при этом:
QMG – производительность автогрейдера (м2/час),
b – ширина отвала (м),
L – длина участка, на котором производится планировка (м),
b – угол наклона отвала (°),
tzykl – период рабочего цикла (сек),
klock – коэффициент разрыхления грунта рабочей площади,
fV – фактор вида привода,
kErg –коэффициент эргономики.
Длинные рычаги управления | 0,80 |
Джойстиковая система управления | 0,95 |
Тип грунта | Категория грунта | Плотность грунта (т/м3) | Коэффициент разрыхления грунта |
Рыхлый, сухой песок | I | 1,2–1,6 | 1,05–1,15 |
Мокрый песок, суглинистый | I | 1,4–1,7 | 1,1–1,25 |
Глина, мелкий гравий | II | 1,5–1,8 | 1,2–1,27 |
Тяжелая, твердая глина | III | 1,6–1,9 | 1,25–1,35 |
Сланец, суглинистый сланец, гравий, скалистый грунт | IV | 1,9–2,0 | 1,35–1,5 |
В последние годы увеличивается число автогрейдеров с управлением с помощью джойстика (рычажный указатель). Помимо улучшения эргономики джойстиковое управление предоставляет возможность применения GPS/ГЛОНАСС – системы глобального позиционирования. Это существенно упрощает управление грейдером. С другой стороны, улучшается возможность координации отрезков планировки.
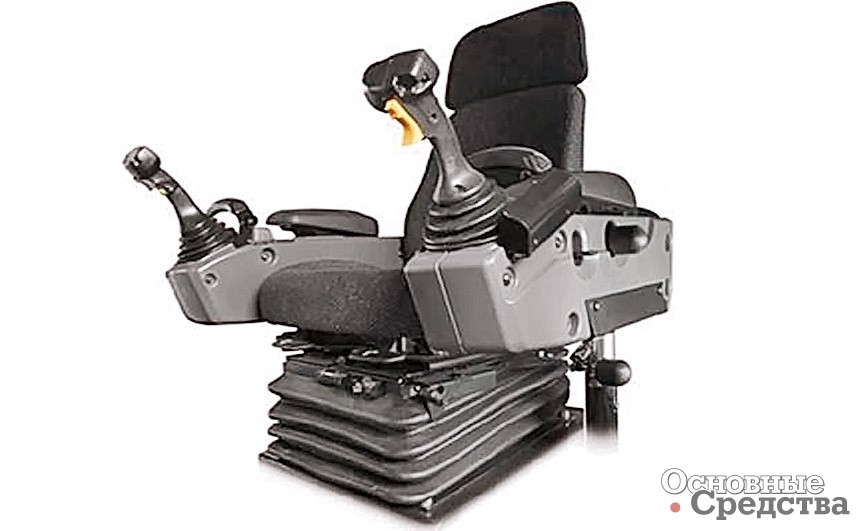
Уже некоторое время существуют полноприводные автогрейдеры. Для реализации полного привода автогрейдеров используются комбинации гидромеxанического привода на задние колеса c гидростатическим приводом на переднюю ось.
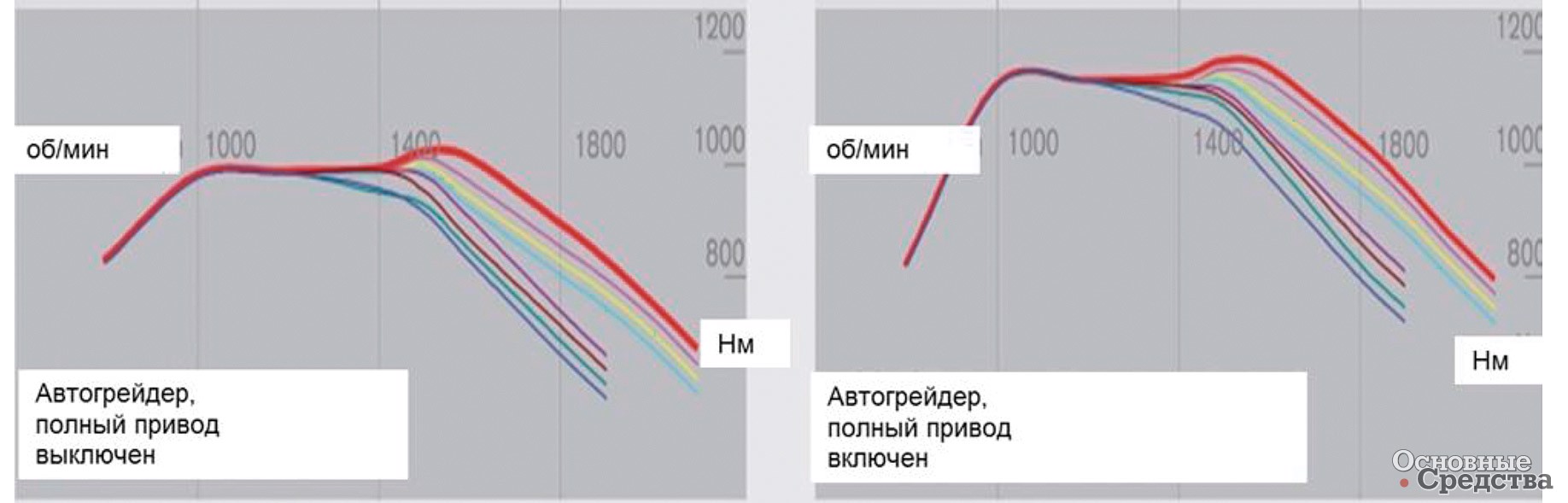
Сложности синхронизации оборотов колес, приводимые гидромеханической коробкой передач с переключением под нагрузкой и гидростатическим приводом передней оси, преодолеваются с помощью электроники. Эта система полного привода уже давно показала свою надежность и эффективность.
На рис. 12 показано существенное повышение крутящего момента у автогрейдера с приводом на переднюю и заднюю оси.
Литература
1. Dr.-Ing. Hans-Peter Zinke: Bergbaumaschinen und ihr Einsatz; Referat Konferenz Berg-baumaschinen Kemerowo, 2006.
2. W. Eymer; S. Oppermann, R. Redlich, M. Schümann, Grundlagen der Erdbewegung; Kirschbaum Verlag; 2. Auflage 2006.
3. Савочкин В.А. Тяговый расчет тягачей. МГТУ «МАМИ», Москва 1997.
4. Wikipedia, GPS System.
5. VOLVO construction machines, Booklet VOLVO A40D.