
Влияние конструктивных особенностей гидравлических экскаваторов и выбора типа рабочего оборудования на производительность
Определение производительности
Производительность Р – это результат соотношения продуктов работы к затраченному времени в единицах «тонны в час» (т/ч).

Р – производительность (т/ч);
Q – масса полученного матриала (т);
t – время, за которое материал был получен (ч).
Факторы и величины воздействия
Производительность экскаваторов зависит от множества факторов, которые более или менее весомо влияют на конечный результат работы. Размеры статьи не позволяют проанализировать все воздействующие факторы. Поэтому в следующих разделах статьи мы опишем лишь наиболее важные из них.
Грунты 6-й и 7-й категорий, как правило, взрываются или разрыхляются кирковочным оборудованием бульдозеров, прежде чем их можно будет разрабатывать экскаватором. Остальные грунты можно копать без предварительной подготовки.
Твердость и трещиноватость грунтов влияют на процесс заполнения ковша. Чем более крупнокусковой грунт, тем больше время заполнения ковша и, следовательно, тем ниже производительность эксакаватора.
Другая характеристика, на которую надо обращать внимание, это плотность грунта. От нее зависит не только его твердость и прочность, но и масса. Чем больше масса грунта в ковше, тем меньше скорость и ускорение ковша при копании.

Виды грунтов
Различные виды грунтов и скал разделяют на категории грунтов. Чем выше номер категории, тем тверже и крепче грунт. Под грунтами подразумеeтся полный состав почвенного основания, т.е. грунтом считается и скала, и болотная почва.
Усилие отрыва
Усилие отрыва FL – то усилие, которое воздействует на кромку зубъев от гидроцилиндра ковша. Измеряется оно тангенциально по радиусу поворота ковша. Ковш при этом устанавливается в такое положение, при котором момент копания, созданный гидроцилиндром ковша и рычагом поворота ковша (при обратной лопате), наибольший.
На рисунке 1 изображено положение, когда гидроцилиндр поворота ковша создает наибольшее плечо рычага. Для копания твердого грунта лучше всего выбирать ковш с небольшим радиусом поворота, чтобы тем самым увеличивать усилие отрыва.
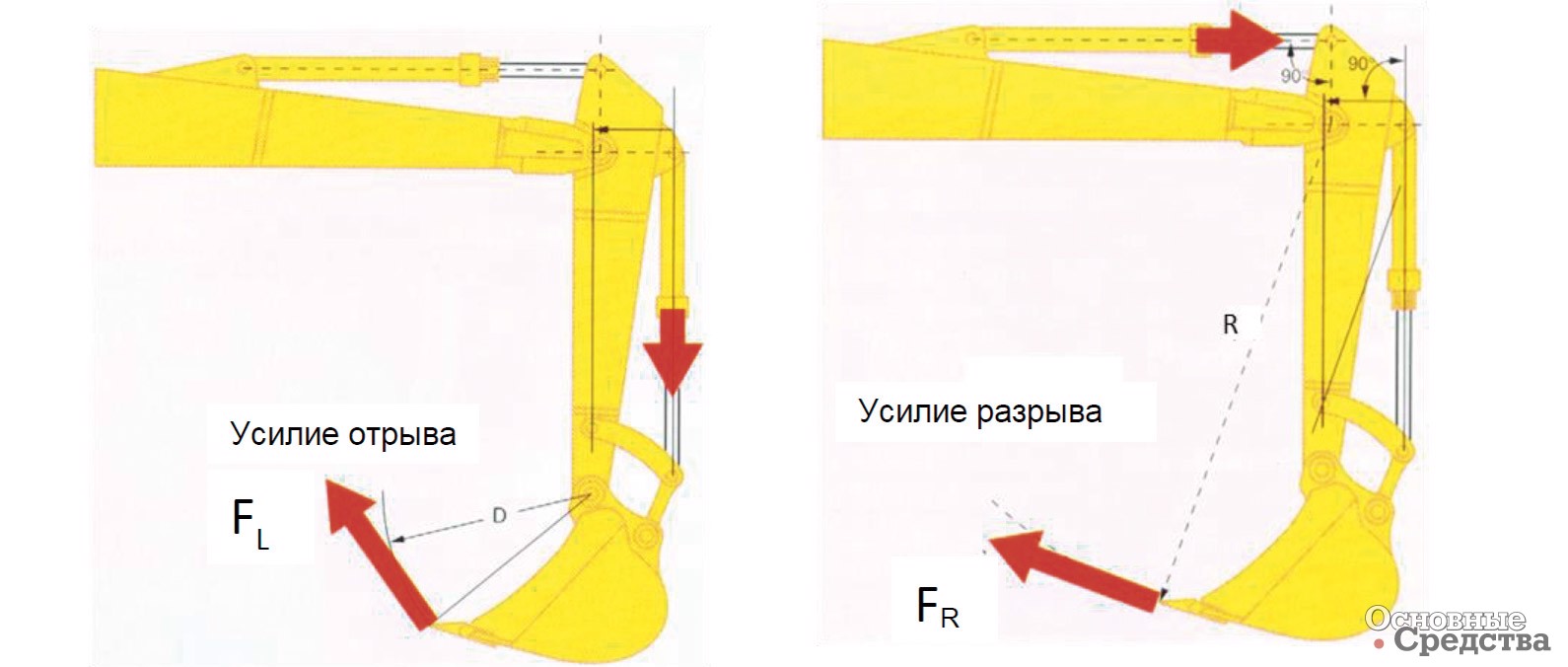
Усилие разрыва
Усилие разтрыва FR экскаватора – это усилие, созданное гидроцилиндром рукояти на режущей кромке или зубъях ковша. Это усилие высчитывают или измеряют тангенциально к радиусу R. Максимальное усилие разрыва возникает, когда гидроцилиндр рукояти располжен перпендикулярно (90°) к плоскости, которая проходит через точку вращения рукояти на стреле. Ковш и в этом случае должен находиться в положении максимального усилия отрыва.

Ковш
Ковш – главный инструмент каждого экскаватора в горнодобывающей промышленности. Он имеет решительное значение для работы экскаватора, потому что без него экскаватор не работоспособен. При выборе конструкции ковша необходимо соблюдать следующие условия, оказывающие решающее влияние на эффективность ковша при копании.
Сопротивление копанию – жизненно важный фактор для производительности экскаватора. При большом сопротивлении копанию экскаватор нуждается в большой мощности, чтобы заполнить ковш. В случае недостаточной мощности для заполнения ковша оператору придется выполнять дополнительные вспомогательные действия, чтобы заполнить ковш. Но от этого увеличивается время заполнения ковша и существенно сокращается производительность. При низком сопротивлении копанию время, необходимое для заполнения ковша, уменьшается.
Сопротивление копанию – это сила, которую можно посчитать по следующей формуле:

ka – удельное сопротивление копанию [H/cм2];
A – площадь поперечного сечения ковша [м2].
Удельное сопротивление копанию зависит от категории грунта (см. таблицу 1).
Категория грунта | Состав грунта | Удельное сопротивление копанию (резанию) [Н/cм2] |
1 | Песок; супесь; мягкий и средний влажный и разрыхленный суглинок без включений | 0,98–5,4 |
2 | Суглинок без включений; гравий мелкий и средний; мягкая и влажная или разрыхленная глина | 5,6–20,6 |
3 | Суглинок крепкий; глина средняя, крепкая, влажная или разрыхленная; очень мягкие аргиллиты и аллевролиты; уголь очень мягкий, рыхлый | 15,7–29,4 |
4 | Суглинок крепкий со щебнем или галькой; глина крепкая и очень крепкая влажная; уголь мягкий; конгломерат очень слабосцементированный (мягкий) | 25,5–43,15 |
5 | Сланцы средние; глина и лёсс крепкие, сухие отвердевшие; глина спондиловая; мел; гипс; опоки; мергель; песчаники мягкие; конгломераты и уголь средней крепости; руда фосфоритовая и марганцевая мягкая; скальная порода, хорошо взорванная (куски не более 0,3–0,4 ширины ковша) | 32,4–58,8 |
6 | Ракушечник; известняк мягкий, пористый; мел; сланцы; мергель и гипс средней средней крепости; уголь крепкий Уголь очень крепкий; руда марганцевая крепкая | 29,4–53,94 49,0–107,9 |
7 | Сланцы; мергель; мел и гипс средней крепости; песчаник мягкий, мерзлые грунты | 98,1–343,2 |
8 | Скальные и мерзлые породы, хорошо взорванные | 2,2–3,5 |
Другой фактор, от которого зависит удельное сопротивление копанию, поперечное сечение ковша А. Оно зависит от высоты кромки, высоты зубъев, числа зубъев, ширины боковой стенки и глубины копания (см. рис. 2).

В общем, можно сказать, что удельное сопротивление копанию увеличивается с возрастанием категории грунта.
Ширина ковша имеет особое влияние на работоспособность экскаватора. От ширины ковша зависит величина сопротивления копанию, которая связана также с типом грунта и вязкостью грунтовой массы (см. рис. 3).
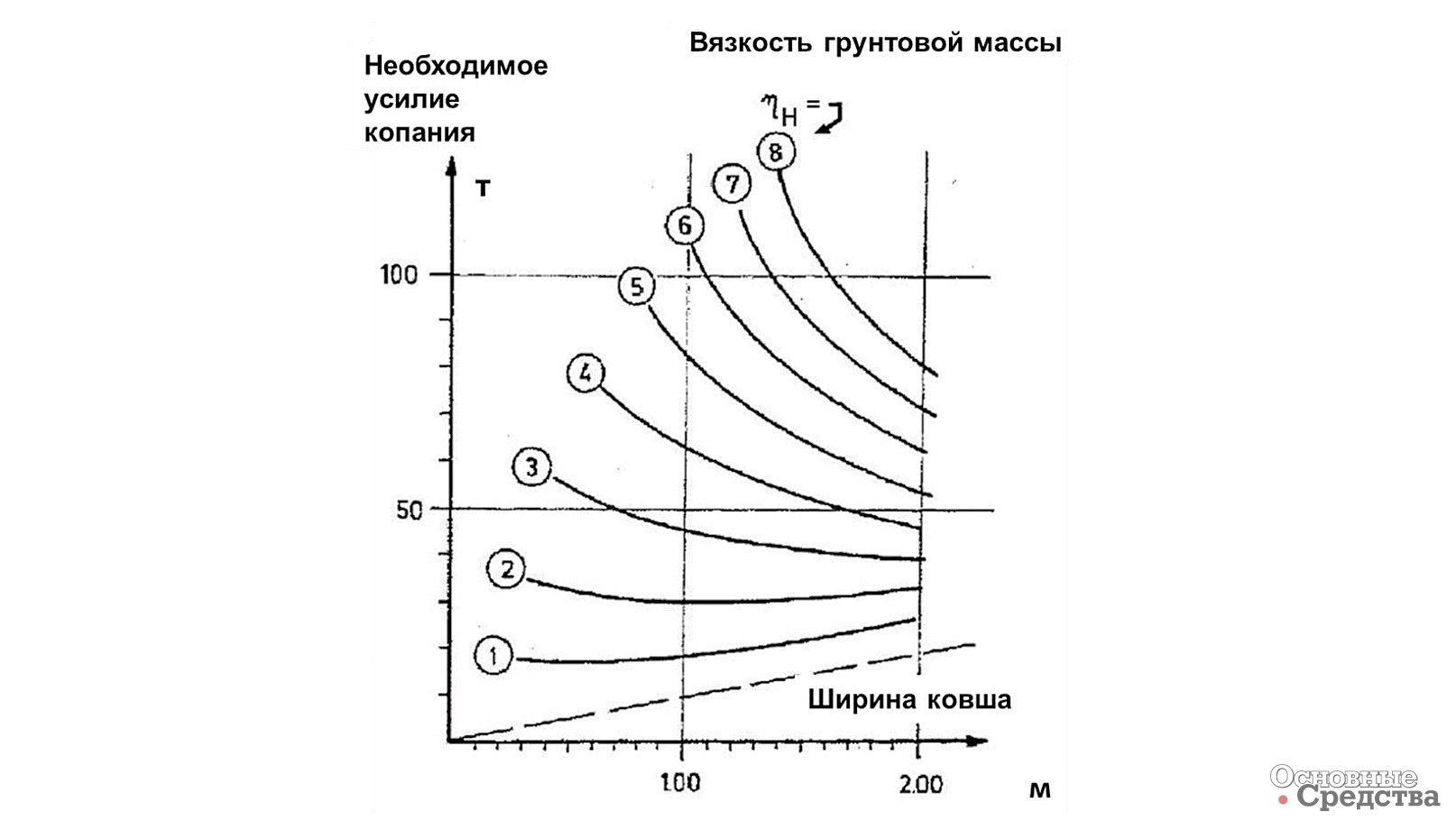
Вязкость грунтовой массы зависит в основном от категории грунта и его трещиноватости. Грунт, имеющий вязкость 1, очень мягкий. Грунт, имеющий вязкость 8, скалистый и сильно трещиноватый, это означает, что он содержит крупнокусковые обломки скалы с малой долей малoзернистых фракций. Горную массу с показателем вязкости 3 можно легко грузить с меньшим усилием более широкими ковшами.
Вывод: ширину ковша нужно подобрать как можно больше. Но при этом, конечно, подбор ширины ковша должен согласоваться с общей геометрией ковша.
Боковые стенки или боковые кромки могут поглощать до 30% от суммарной энергии копания. Это значит, что сопротивление копанию сильно зависит от конфигурации боковых стенок ковша. Важную роль при этом играет угол наклона, т.е. угол между боковой кромкой и главной режущей кромкой (см. рис. 4).
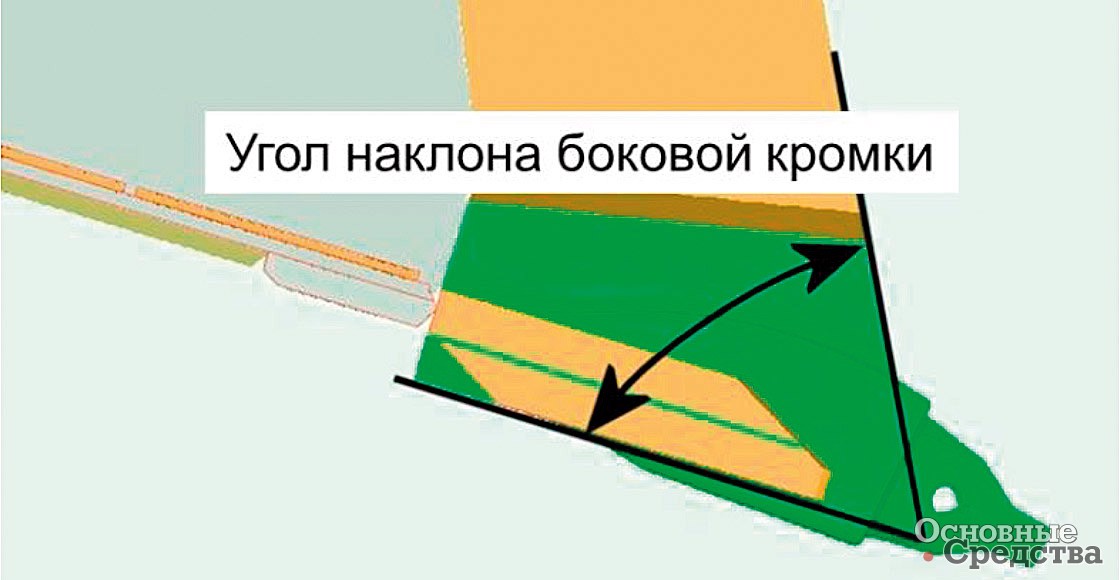
По результатам исследований, угол наклона боковой стенки должен быть не меньше 54° и не больше 65°, чтобы снизить затраты энергии.
Также необходимо учесть при выборе конструкции ковша сужение боковых стенок, это видно на рис. 5.
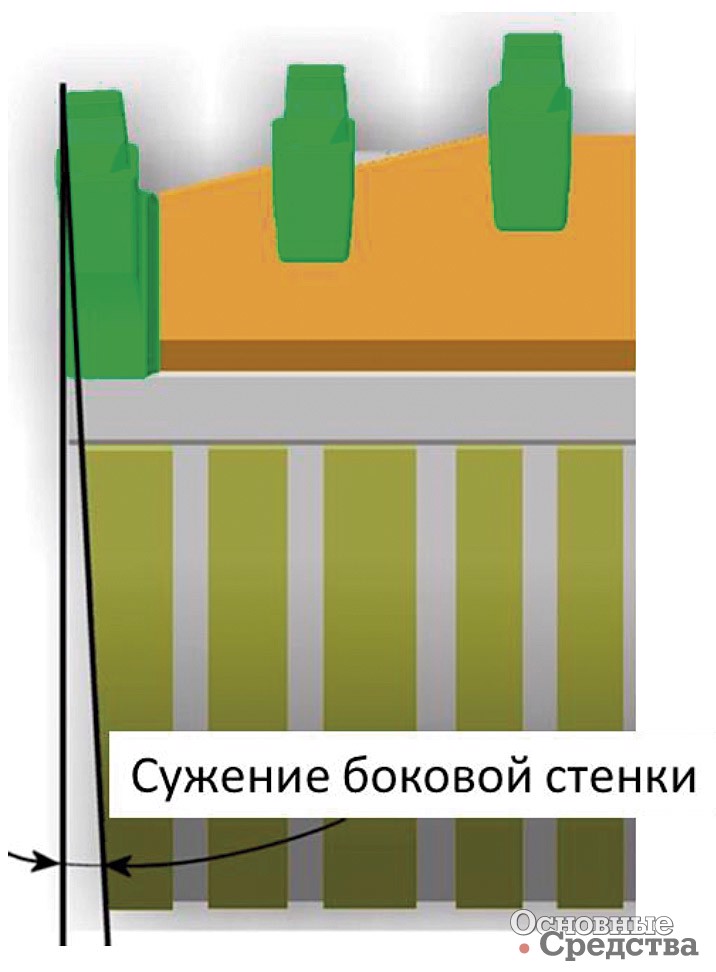
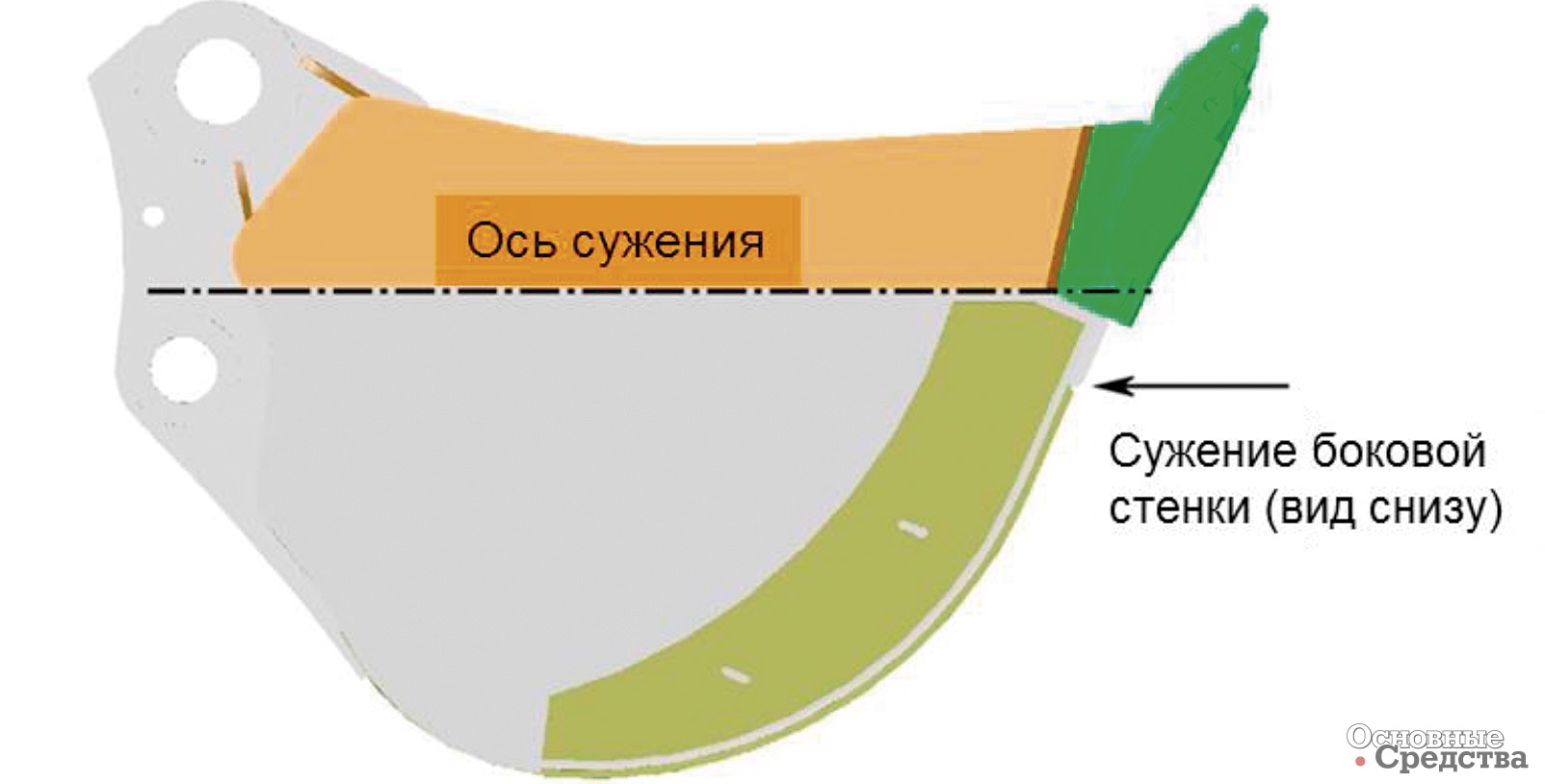
Сужение боковых стенок положительно влияет на разгрузку ковша, особенно у сильно связных и мокрых грунтов. Эти грунты, например суглинок и супесь, очень интенсивно прилипают к стенкам ковша. С целью уменьшения этого эффекта прилипания боковые стенки сужаются.
Дополнительная причина сужения – уменьшение трения грунта о боковые стенки. Уменьшение трения грунта всегда уменьшает сопротивление копанию.
Трение грунта опять же зависит от категории грунта и его влажности. При копании скалистых грунтов сужение боковых стенок играет малую роль, т.к. трение остается равномерным. При копании песчаных грунтов, наоборот, можно рассчитывать на уменьшение сопротивления копанию на 14% при сужении боковых стенок на 2°.

Главная режущая кромка – основная часть каждого ковша. Она подвергается наибольшим нагрузкам и наиболее интенсивному износу. Когда кромка оснащена зубъями, наибольший износ приходится на зубья. При плохом техобслуживании кромки и зубъев износ кромки вынуждает часто заменять ковш, что увеличивает простои экскаватора и тем самым снижает его производительность.
Опыт показал, что наилучший угол стреловидности режущей кромки составляет около 20°, чтобы ковш легко мог внедряться в скалистую породу (см. рис. 7).
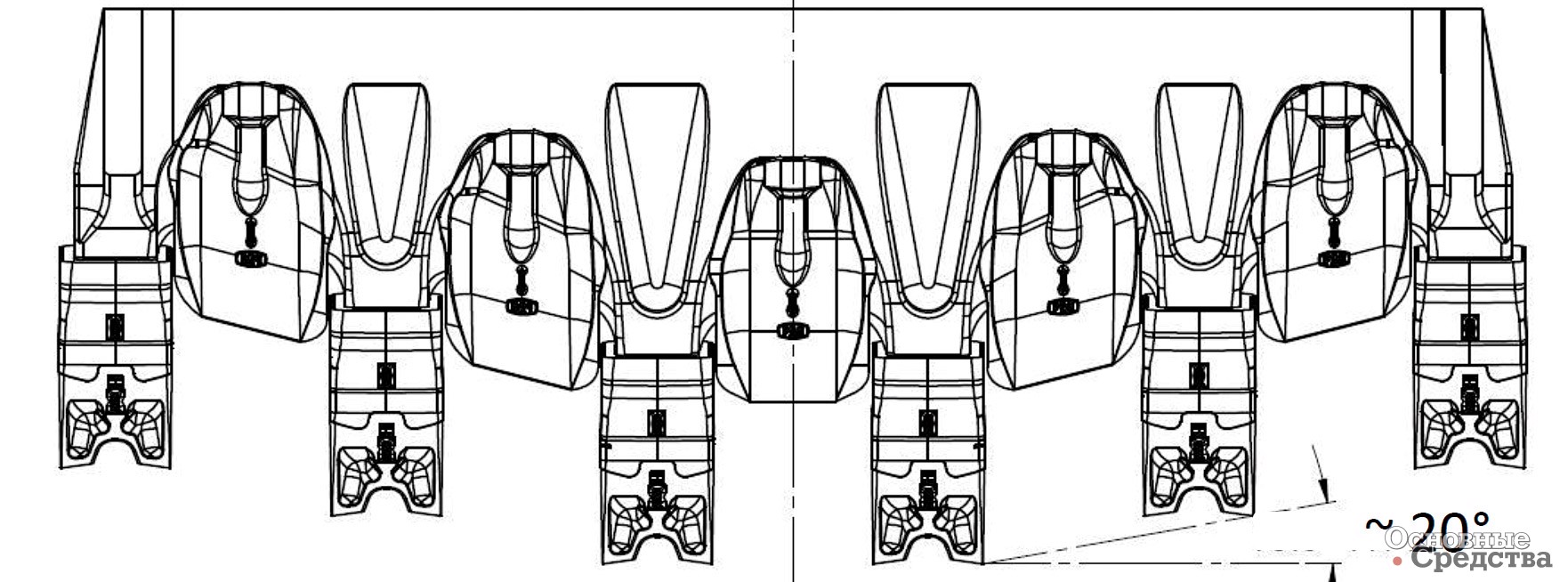
Зубъя. Задача зубъев – способствовать внедрению режущей кромки в породу. Это становится возможным потому, что зубья оказывают намного более высокое давление на породу, чем кромка без зубьев.
Грунты характеризуются величиной удельного сопротивления копанию KА, размерная единица которого Н/cм2.
Общая формула силы давления:

А – площадь поперечного сечения зуба (зубьев) (cм2);
F – усилие копания, созданное экскаватором (Н).
Для того чтобы зуб (зубья) мог внедряться в грунт, давление зуба должно быть больше удельного сопротивления копанию KА.
Усилие F – максимальное усилие копания, а А – площадь поперечного сечения зуба (зубьев). Площадь поперечного сечения зубьев намного меньше, чем площадь поперечного сечения режущей кромки. Исходя из того, что в определенном положении рабочего оборудования усилие копания не изменяется, давление на вершине зуба всегда больше, чем на вершине режущей кромки:

Условие успешного копания. В том случае, когда эта законномерность действует, экскаватор в состоянии успешно копать породу.
Следующим аргументом в пользу применения зубьев является то, что износу подвергаются зубья а не режущая кромка. По этой причине очень часто применяется нечетное число зубьев, чтобы сконцентрировать износ и большее давление на среднем зубе.

Оператор (экскаваторщик)
Этот фактор воздействия – весьма значительный. Оператор в зависимости от его состояния, знаний, опыта может существенно повлиять на результаты работы. Оператор должен хорошо знать все функции своей машины, и поэтому его обучение – самая важная предпосылка для достижения высокой производительности.
Из опыта практической работы: на производительность может отрицательно влиять намерение оператора увеличить коэффициент заполнения ковша, удлиняя время заполнения, или же, несмотря на неполную загрузку ковша, сокращать цикл копания и тем самым повышать количество разгруженных ковшей за определенный период загрузки.

Еще один фактор – стиль управления экскаватором. Опытные операторы выполняют все движения копания одновременно. В таких случаях движения при копании выглядят плавными. У других операторов получается, что каждая операция выполняется отдельно, друг за другом, и в результате понижается производительность.
Подводя итог, можно сказать, что подбор операторов существенно влияет на результаты погрузочно-транспортных работ и на износ и содержание рабочих органов экскаваторов.
Организация открытой разработки при работе с экскаваторами
В этой главе мы рассмотрим все факторы, которые не связаны с экскаваторами, материалами и операторами, т.е. вопросы организации погрузочно-транспортных работ экскаваторов с самосвалами.
Наиважнейший фактор эффективности – время обмена самосвалов под экскаватором. Это время измеряется от того момента, когда последний ковш при погрузке одного самосвала опорожнился, и до момента, когда первый ковш начал разгружаться в следующий самосвал. Для этого цикла обычно считается эффективным время от 45 до 50 секунд. Сокращать время обмена самосвалов можно с помощью так называемой «двойной погрузки», т.е. когда второй самосвал уже находится в погрузочном положении во время погрузки первого.
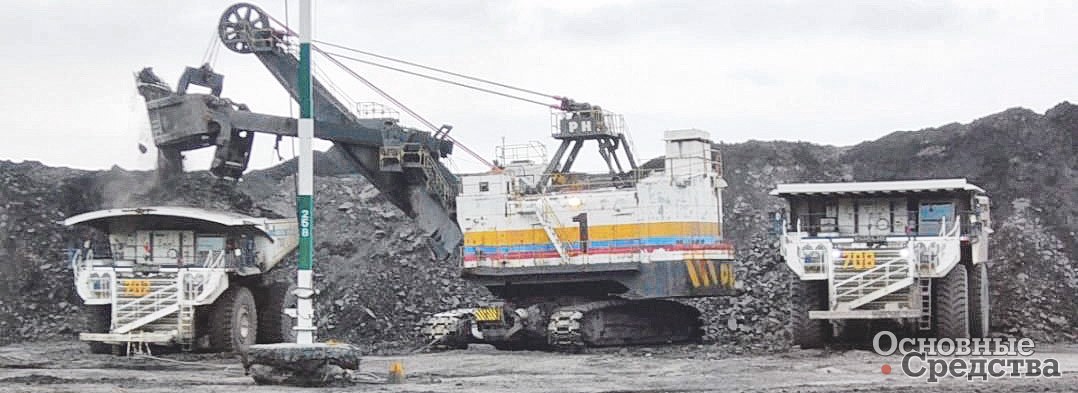
Двусторонняя погрузка сильно сокращает цикл погрузки. Самый короткий цикл при этом может совпадать с циклом копания экскаватора. Обычно двусторонняя погрузка применяется у экскаваторов с обратной лопатой. Экскаватор с обратной лопатой при работе в открытых разработках, как правило, находится на возвышении.
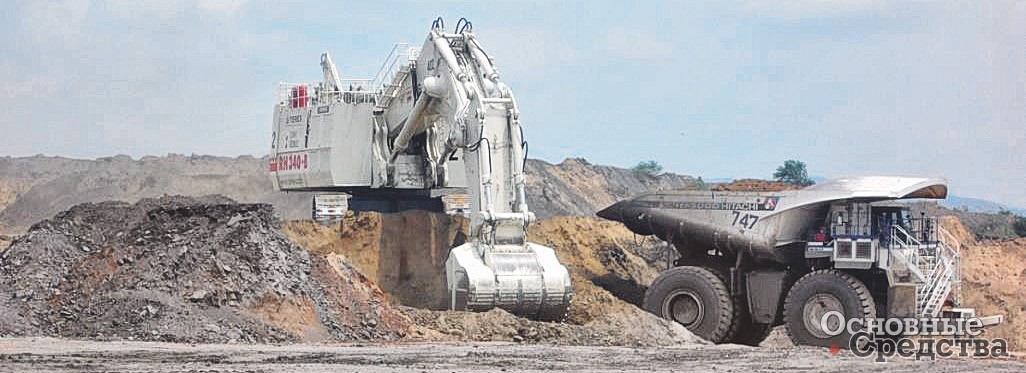
И при обычном режиме односторонней погрузки, а также, что еще важнее, при двусторонней погрузке необходимо, чтобы водители самосвалов строго согласовывали свои действия, во избежание столкновений машин.
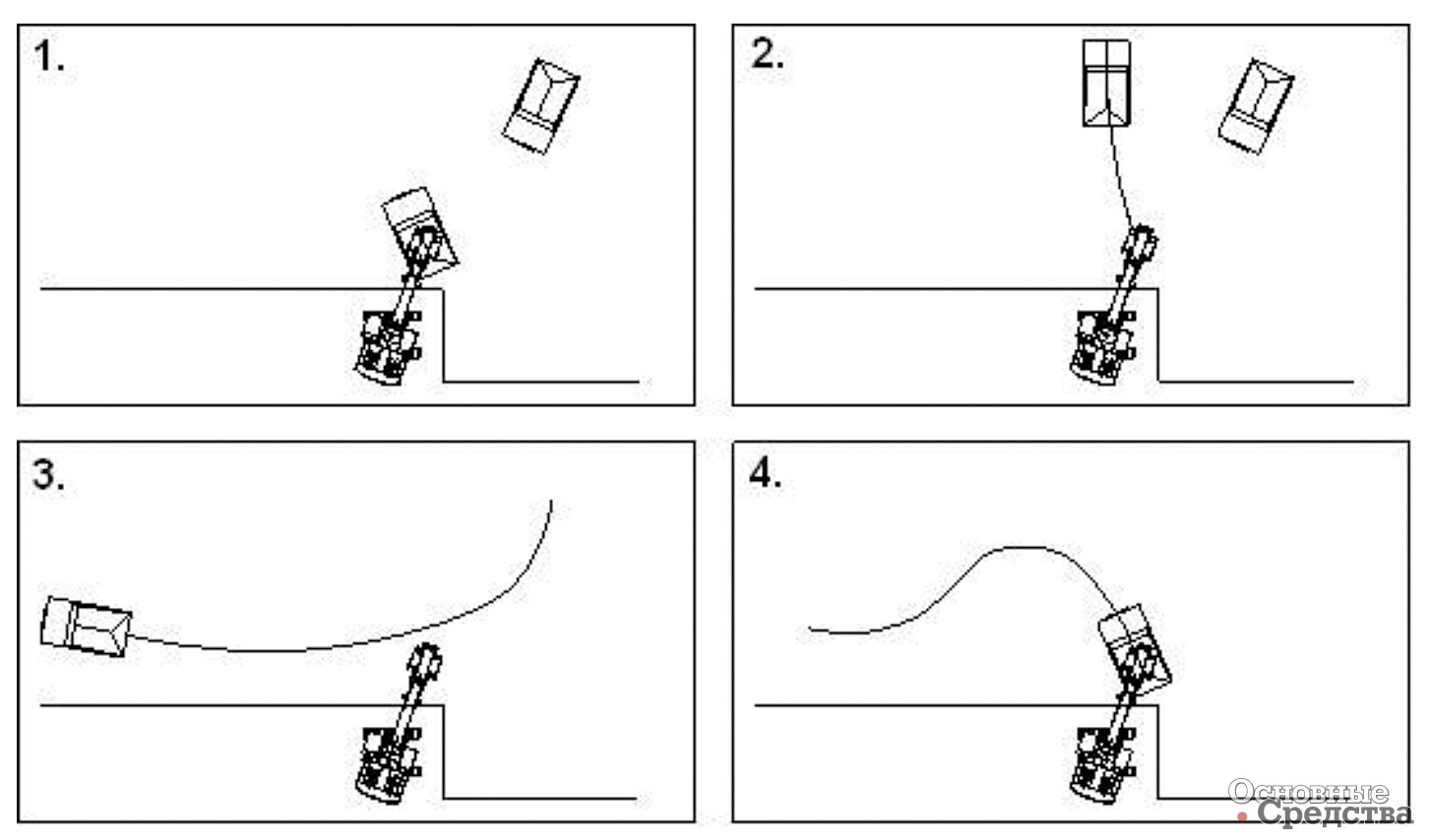
Оптимальный процесс погрузки самосвалов: ожидающий самосвал во время погрузки другого самосвала находится уже в таком положении, что ему нужно всего лишь двигаться назад после того, как погрузка первого самосвала завершена.
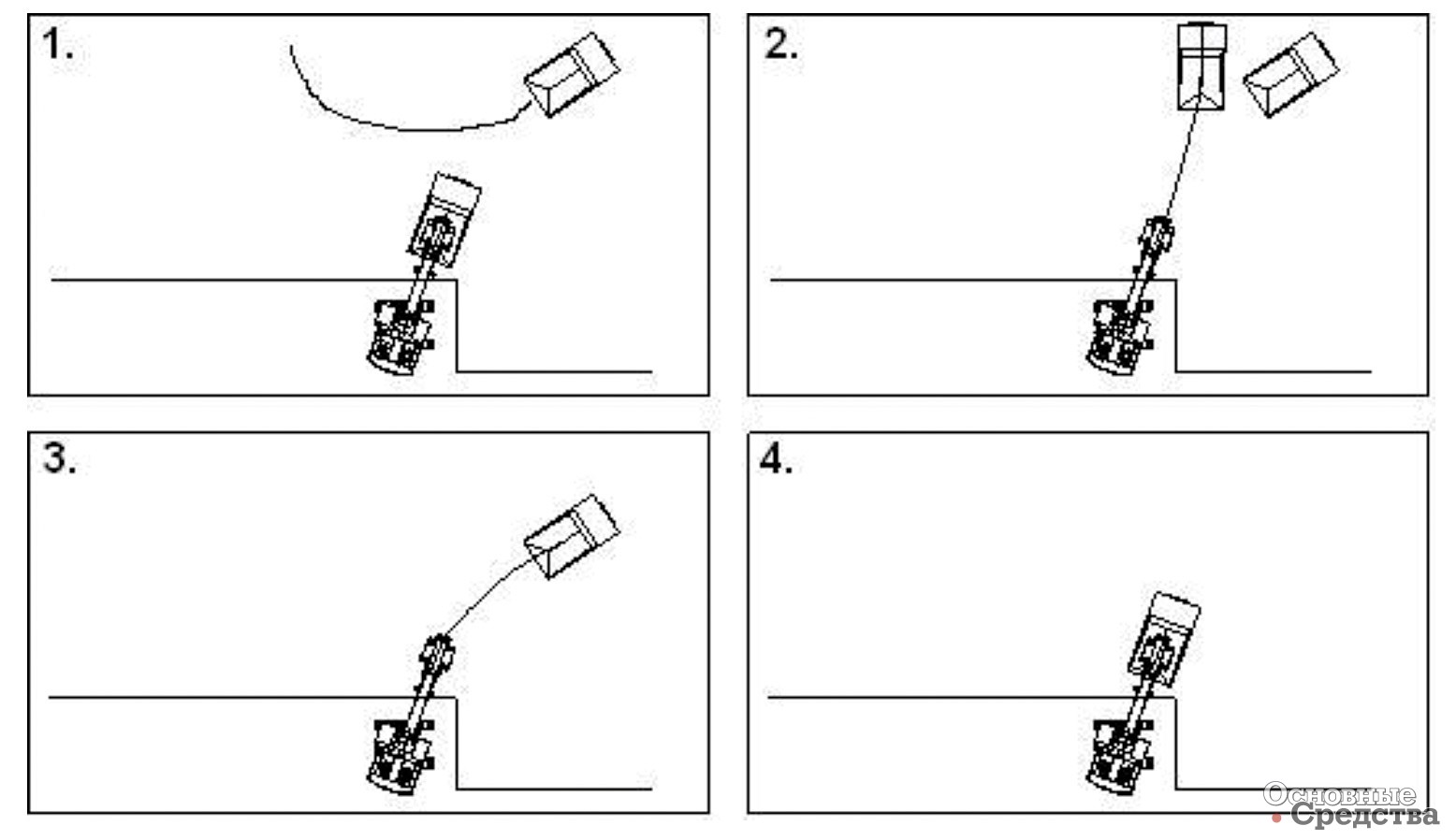
Очевидно, что при увеличении времени обмена самосвалов уменьшается их производительность. А следовательно, падает производительностъ экскаваторов.
Кривые показывают совместную производительность экскаваторов и самосвалов при обработке различных грузов. Полный рабочий цикл погрузки в этом случае – 32 секунды и емкость ковша – 30 м2 (60 т). Полный рабочий цикл – время, затраченное на погрузку самосвала.
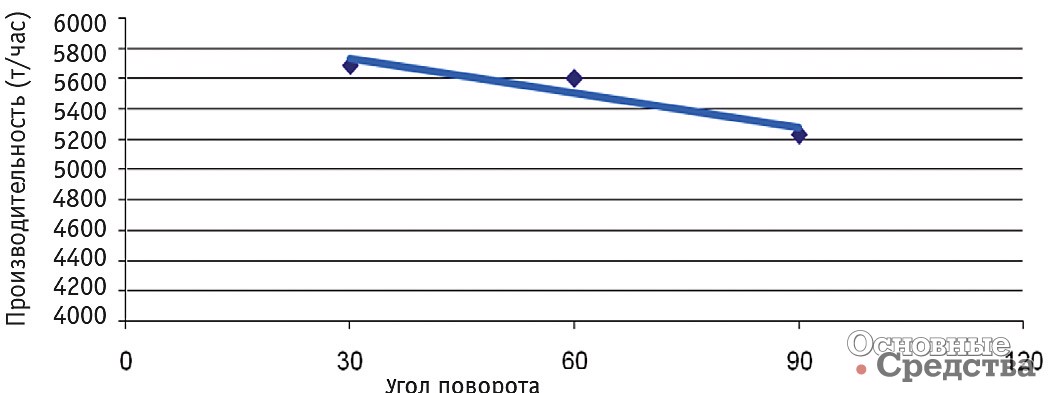
Если по внутризаводским причинам в карьере нельзя улучшить время обмена самосвалов, нужно увеличить их грузоподъемность. Это позвляет увеличить производительностъ при нeизменном времени обмена.
Смысл этого мероприятия в том, что доля погрузочных работ повышается, потoму что нужно меньше самосвалов для такого же объема вскрыши и породы. Также обсуждается вопрос и о том, должен ли самосвал уже стоять перед забоем в ожидании погрузки, когда предыдущий самосвал еще грузится, или нет.
В случае стоянки самосвала, когда предыдущий самосвал еще грузится, он, конечно, потеряет эффективное производственное время. В оптимальном случае самосвал как раз приедет в тот момент, когда погруженный самосвал уезжает.
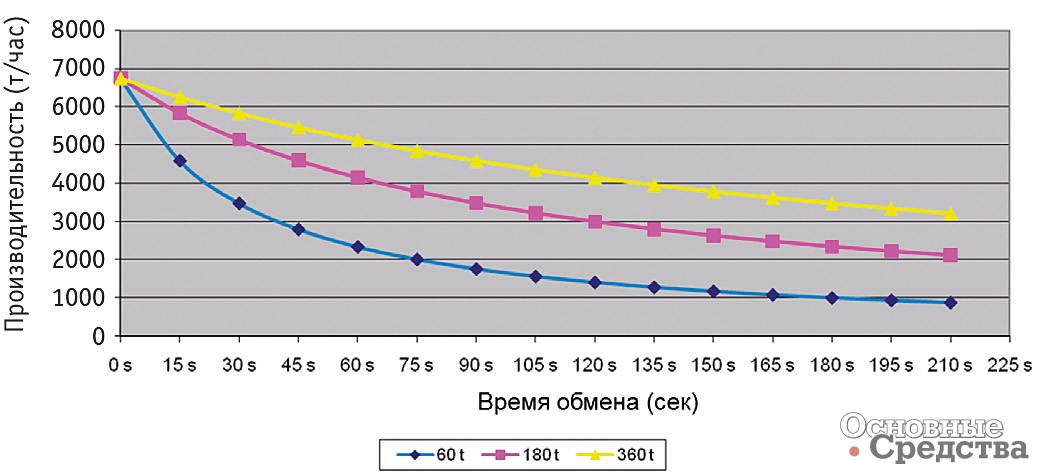

Следующий фактор – соответствие грузоподъемности самосвалов емкости ковша экскаватора. При делении грузоподъемности самосвала на емкость ковша важно получить целое число. При нецелом числе случaется, что надо грузить частично заполенные ковши, чтобы не превышать грузоподъемность самосвалов. Тем самым понижается производительность комплекса экскаватор –самосвал. В этом комплексе, по опыту, число ковшей на погрузку самосвала должно колебаться от 4 до 6.
Меньшее число ковшей означает, что самосвалы малы для данного типоразмера экскаватора. И наоборот, более высокое число показывает, что экскаватор слишком мал.
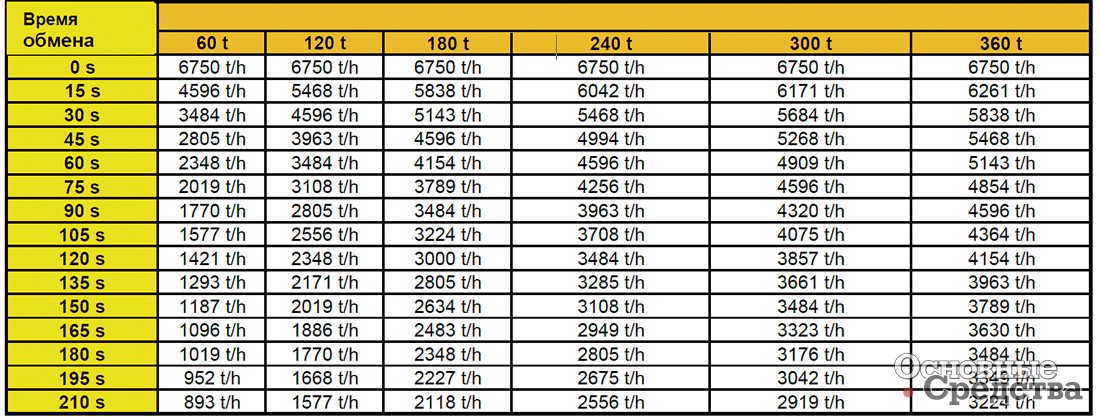

Для облегчения работы экскаваторщика применяют погрузчики или бульдозеры для расчистки и выравнивания полотна забоя. Это позволяет экскаваторщику сосредоточить все свое внимание на погрузочной работе. Пример такой процедуры представлен на рисунке 15.
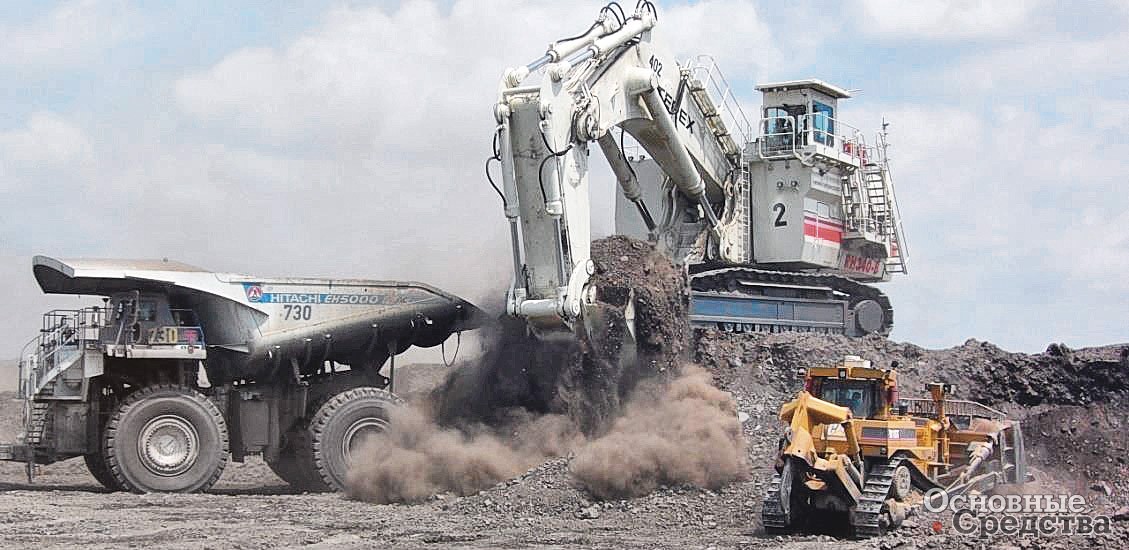
Расчистка и выравнивание полотна забоя, как и всех карьерных дорог, важное мероприятие для сохранения работоспособности и долговечности самих самосвалов. Более продробно эти вопросы рассматриваются в соответствующей статье.