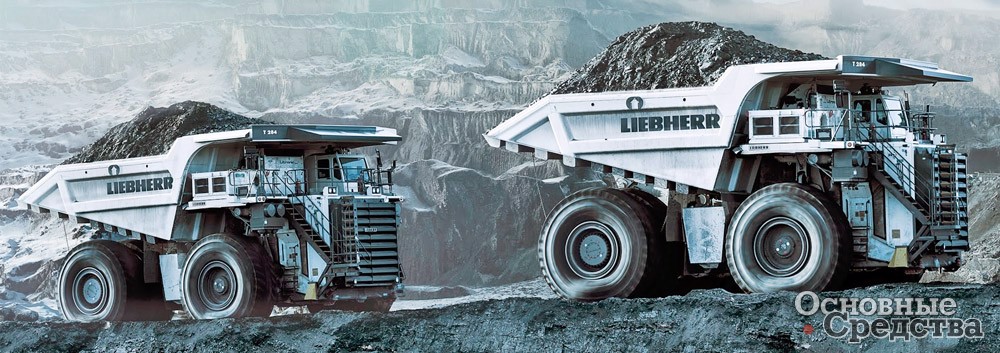
Тенденции в развитии современных карьерных самосвалов на жесткой раме
Liebherr расширяет свою линейку карьерных самосвалов
Компания Liebherr специализируется на проектировании и производстве горной техники на протяжении многих десятилетий. Новым воплощением этого отраслевого опыта стал карьерный самосвал T 236, основанный на современной дизель-электрической трансмиссии Liebherr с системой управления Litronic Plus AC второго поколения. Все ключевые компоненты самосвала Т 236 были изготовлены на предприятиях Liebherr в расчете на самые тяжелые условия работы в карьерах. В результате карьерные самосвалы Liebherr отличаются длительными межсервисными интервалами, долговечными компонентами и высокой технической готовностью. Сочетание этих преимуществ позволяет сэкономить время и сократить эксплуатационные расходы.
Для обеспечения безопасной работы сервисного персонала, водителей и других сотрудников карьера в T 236 были предусмотрены двухполюсные выключатели массы, стартера и системы подъема/опускания кузова. В дополнение к этому новый самосвал оборудован системой блокировки приводов с заземлением каждого электрического соединения и силового модуля. Рабочее напряжение самосвала составляет 690 VAC/ 900 VDC, что облегчает обслуживание машины в карьере. Также инженеры Liebherr интегрировали в модели Т 236 систему изоляции Litronic Plus Isolation, обеспечивающую дополнительную защиту персонала за счет превентивного устранения источников опасности. Новая линейная конструкция дизель-электрической трансмиссии самосвала позволила уменьшить протяженность электропроводки.
Силовые модули электроприводов хода после монтажа не требуют дополнительной настройки и дальнейшего обслуживания, но при этом обладают степенью защиты IP 68 и надежно работают в любых погодных и климатических условиях. Многие точки обслуживания нового самосвала доступны с уровня земли. При этом машина отличается длительными межсервисными интервалами. Всё это способствует сокращению времени простоев на ТО и высокому коэффициенту технической готовности T 236.
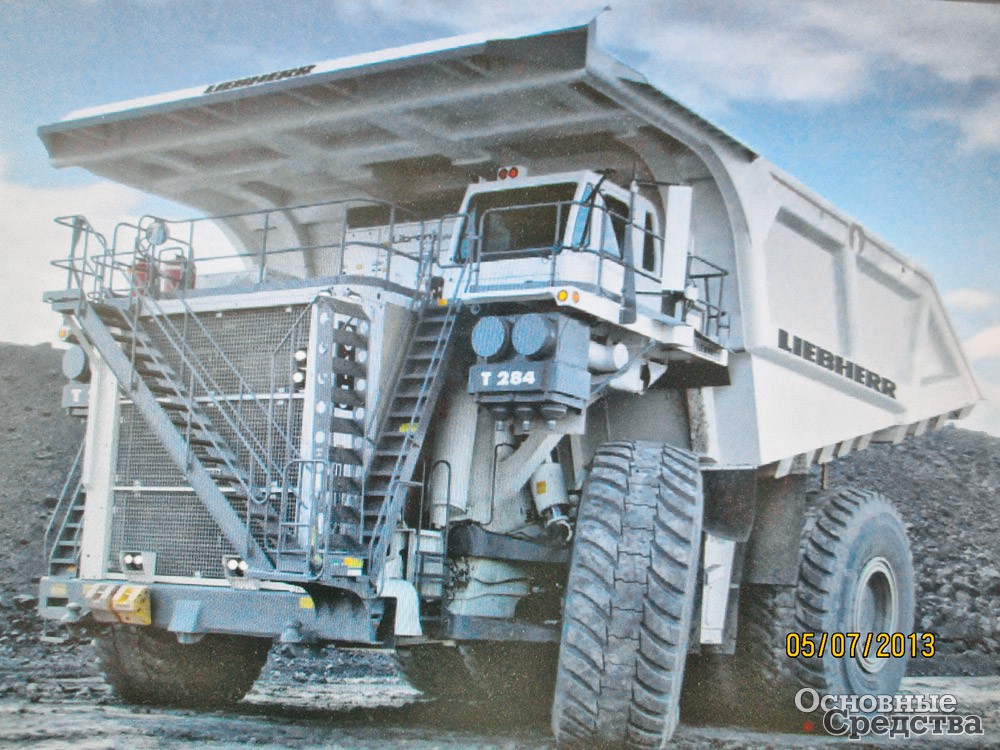
При проектировании карьерных самосвалов инженеры Liebherr всегда учитывали мнение и потребности водителей. T 236 не стал исключением: просторная и удобная кабина самосвала оборудована по последнему слову техники, в то время как интеллигентная система управления, динамичное ускорение, высокая маневренность шасси и надежная подвеска передних полуосей гарантируют безопасное и продуктивное вождение.
В самосвале Т 236 была реализована система управления электроприводами Liebherr Litronic Plus AC второго поколения с технологией активных преобразователей частот Active Front End. Благодаря эффективному использованию электрической энергии во время замедления/ торможения машины, трансмиссия обеспечивает равномерную работу двигателя с минимальным расходом топлива. Все ключевые компоненты дизель-электрической трансмиссии самосвала Т 236 являются собственными разработками Liebherr. Это гарантирует их слаженную и эффективную работу. Трансмиссия Т 236 обеспечивает не только большую мощность, но и ощутимую экономичность машины в разнообразных условиях эксплуатации.
Вместе с тем регулируемая гидравлическая система самосвала T 236 автоматически адаптируется к конкретным режимам работы, развивая максимальную мощность лишь по мере необходимости. Это решение способствует дополнительной экономии топлива. Благодаря высокому крутящему моменту, энергичному ускорению и непрерывности тягового усилия, трансмиссия T 236 способствует быстрому движению вверх по склонам даже при большой загрузке кузова. По скорости выполнения рабочих циклов новые самосвалы соответствуют самым высоким отраслевым стандартам. Вместе с тем модель T 236 стала первым дизель-электрическим самосвалом с тормозами, погруженными в масляную ванну, и 4-контактным тормозом-замедлителем (ретардером). Сочетание этих решений способствует надежному торможению и более безопасному движению машины в тяжелых условиях эксплуатации. В результате новые самосвалы отличаются высокой эффективностью, обеспечивая особенно низкие затраты в расчете на каждую тонну транспортируемого материала.
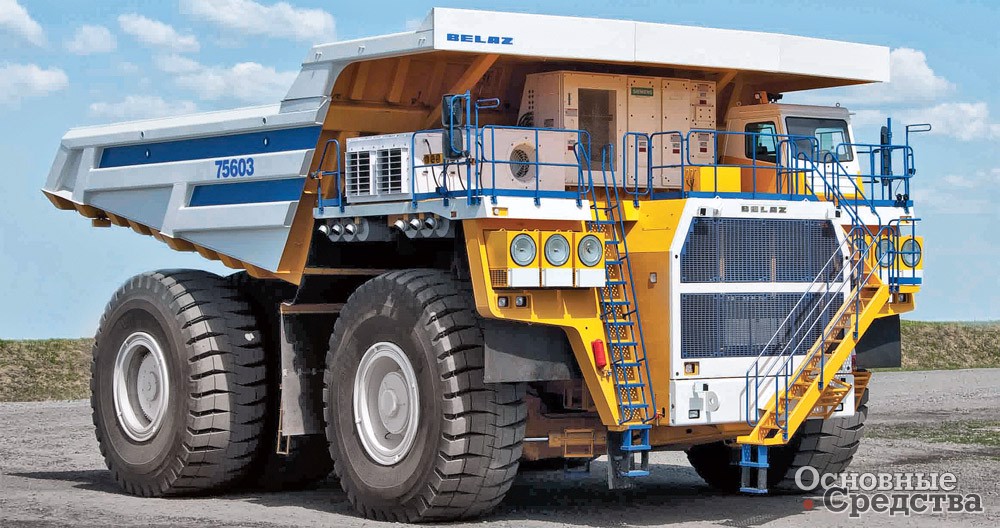
Карьерные внедорожные самосвалы российской сборки
Россия не производит самостоятельно внедорожные карьерные самосвалы – так сложилось еще со времен Советского Союза, в котором все производство тяжелых машин было сосредоточено в Белоруссии. В современной России нет желающих строить крупные машиностроительные заводы, как это было в сталинские времена на заре советской власти. Однако попытки создать совместные предприятия по сборке крупногабаритных самосвалов случались неоднократно.
Так, переговоры о создании совместного предприятия по производству БЕЛАЗов в России велись с 2007 г. Рассматривались различные территории Урала и Сибири. Выбор был сделан в пользу Челябинской области, поскольку в регионе находятся основные покупатели машин, в том числе крупная золотодобывающая компания «Южуралзолото», металлургические гиганты. С 2010 г. Коркинский экскаваторно-вагоноремонтный завод приступил к сборке белорусских грузовиков. Их производство было организовано на совместном российско-белорусском предприятии «УралБелАЗ», учредителями которого выступили ООО «КЭВРЗ», ЗАО «УралБелазСервис» и «БЕЛАЗ». Грузовики под брендом «БЕЛАЗ» начали собирать на производственной площадке ООО «КЭВРЗ» из агрегатов и комплектующих, присланных из Беларуси. В планах СП было производство 180 машин в год грузоподъемностью 30, 45 и 55 т. Кроме сборки новое предприятие организовало сервисное обслуживание грузовиков «БЕЛАЗ», работающих на промышленных объектах Челябинской области. По разным подсчетам, их количество оценивалось в 800 с лишним машин. Первые южноуральские БЕЛАЗы собирались из привезенных узлов и деталей. Со временем коркинцы планировали часть из них изготавливать на месте. Велись переговоры об организации сборочного производства БЕЛАЗов с представителями ООО «ЧТЗ-Уралтрак». Но не нашлось промышленных площадок, которые бы удовлетворили белорусских машиностроителей. Со временем производство БЕЛАЗов на Урале сошло на нет.
В ноябре 2010 г. в «Кузбасской вагоностроительной компании» был освоен выпуск кузовов для БЕЛАЗов грузоподъемностью от 130 до 320 т, которые поставлялись на предприятия Кемеровской области и Сибири.
В августе 2012 г. в Прокопьевске Кемеровской области на площадке завода «Подземтрансмаш» (ХК «СДС-Маш») открылось сборочное производство карьерных автосамосвалов БЕЛАЗ-75570 грузоподъемностью 90 т. Планировалось, что общий объем инвестиций в организацию производства составит около 1,4 млрд руб., а объем выпуска продукции к 2015 г. достигнет 250 машин в год. Это был первый этап долгосрочного проекта, реализация которого началась в рамках соглашения между правительством Республики Беларусь и администрацией Кемеровской области.
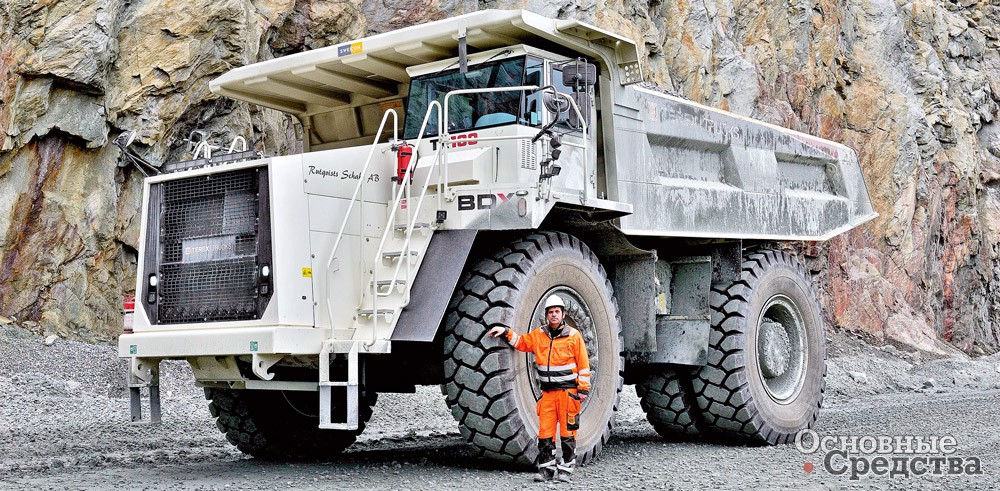
Второй этап кузбасско-белорусского сотрудничества в 2013 г. предусматривал строительство нового производственного комплекса по сборке большегрузных автомобилей. Сначала сборка карьерных самосвалов-гигантов намечалась из деталей белорусского производства, а потом значительную часть комплектующих должны были выпускать заводы холдинга «СДС-Маш» в Прокопьевске (ООО «Электропром», ООО «Подземтрансмаш») и в Кемерово (ООО «Кузбасская вагоностроительная компания»). К настоящему времени грандиозные планы российско-белорусского сотрудничества в области сборки карьерных самосвалов БЕЛАЗ и производства кузовов сошли на нет. Официальные лица по этому поводу никаких комментариев не дают. Возможно, наш сосед справедливо решил, что нет смысла забирать рабочие места у своих граждан и отдавать часть доходов бюджета другому государству. К тому же по большому счету «БЕЛАЗ» ничего не выигрывал от реализации проектов российской сборки – в любом варианте гигантские машины поступают в Россию в разобранном виде и собираются непосредственного на месторождениях дилерами или силами предприятий, закупивших карьерные самосвалы.
В октябре 2012 г. на заводе «Челябинские строительно-дорожные машины» (производство организовано на базе завода им. Колющенко) было запущено совместное предприятие российского холдинга «Русские Машины» и многоотраслевого мирового производителя Terex Corporation (США) – компании ООО «РМ-Терекс». Первый карьерный самосвал Terex TR100-RM челябинской сборки прошел необходимые испытания и получил российский сертификат соответствия. В 2013 г. был намечен выпуск 30 самосвалов, а при выходе на полную мощность в 2014 г. – по 100 машин ежегодно. В проект предполагалось инвестировать 400 млн руб. и создать 300 новых рабочих мест. Локализация сборки карьерных самосвалов должна была составить почти 60%.
Покупка в 2014 г. компанией Volvo CE производственной площадки Terex в Шотландии, на которой ведется выпуск карьерных самосвалов, оказалась фатальной для российского проекта – выпуск самосвалов в Челябинске был прекращен.
И все-таки импортные карьерные самосвалы российской сборки смогли прочно завоевать рынок стран СНГ благодаря ведущим мировым компаниям – Caterpillar и Komatsu. В конце 2011 г.они обе на своих российских заводах запустили в производство самосвалы средней и крупной грузоподъемности.
Еще в 2000 г. в городе Тосно Ленинградской области вступил в строй завод, принадлежащий Caterpillar. Выбор площадки в Тосно был обусловлен рядом факторов: удобным расположением транспортных путей, доступностью земельных ресурсов и коммуникаций, благоприятным инвестиционным климатом в Ленинградской области. Это предприятие с филиалом в Новосибирске вначале производило в основном металлоконструкции, которые поставлялись на заводы американской компании в Западной Европе. В 2008 г. оно стало переходить и к сборке, освоив выпуск экскаваторов и погрузчиков. А в конце октября 2011 г. с конвейера сошел первый 55-тонный самосвал Cat 773Е. Локализация в России пока ограничивается металлоконструкциями, но здесь производится одна из важнейших деталей машины – рама, составляющая основу самосвала. Российская сталь оказалась вполне конкурентоспособной для производства ответственных узлов, из нее же выполняется сборка кузовов в новосибирском филиале. Остальные узлы и комплектующие, в том числе двигатели и коробки передач, поставляются с различных заводов компании в Европе, США и Индии – в ближайшее время перенос их производства в Россию компания не планирует.
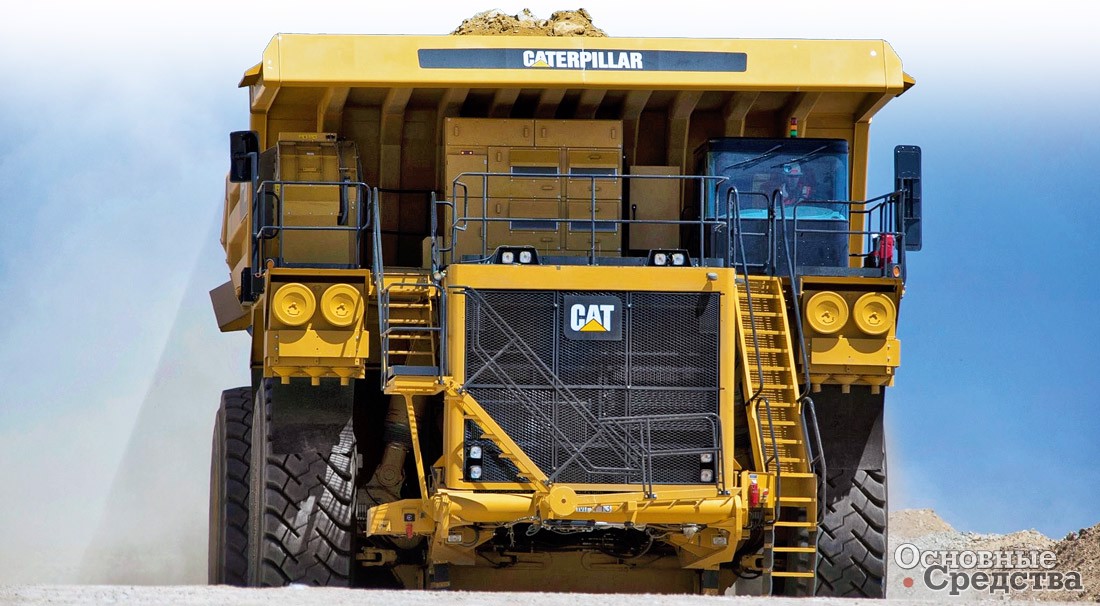
Сегодня ООО «Катерпиллар Тосно» – динамично развивающееся предприятие, территория которого составляет 24 га, при этом производственная площадь занимает 25 тыс. м2. В штате более 400 сотрудников, средняя заработная плата которых выше средней по региону и составляет порядка 80 тыс. руб. Производственная мощность завода – свыше 20 000 т металлоконструкций в год, 1600 экскаваторов и 300 карьерных самосвалов в год. На производственных линиях завода выпускается более ста видов комплектующих для гусеничных и колесных экскаваторов, которые поставляются на заводы Caterpillar в Европе и дилерам компании для удовлетворения нужд заказчиков в России и странах СНГ. В 2017 г. завод «Катерпиллар Тосно» начал выпуск новой модели внедорожного карьерного самосвала CAT 777E грузоподъемностью 91 т. Инвестиции в организацию производства CAT 777E составили $300 тыс.
Модель 777 Е – усовершенствованная версия карьерного внедорожника, который стал более экономичным, улучшились конструкционные характеристики, и повысился комфорт управления. По сообщениям прессы, в 2018 г. завод планировал произвести 160 самосвалов, что значительно больше, чем в предыдущие годы (33 машины в 2016-м и 66 – в 2017 г.). Примечательно, что все они зарезервированы добывающими предприятиями Урала, Сибири и Дальнего Востока.
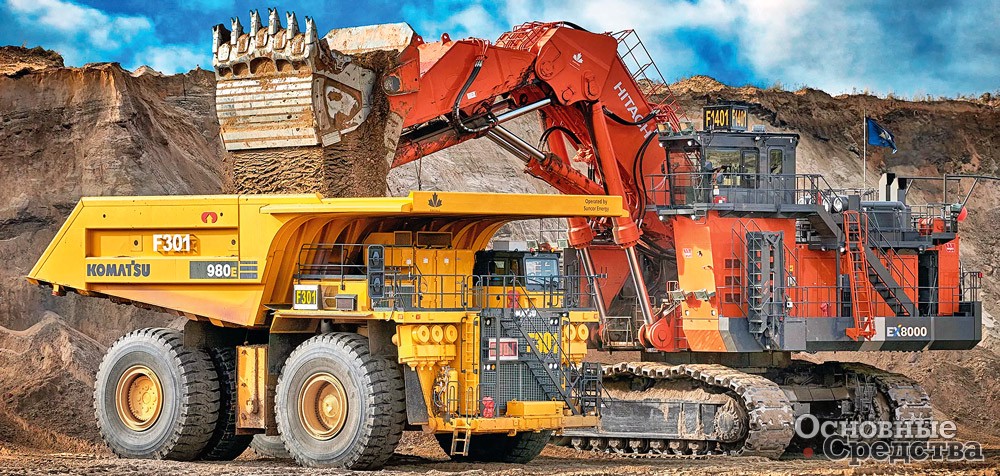
Практически одновременно с американцами на заводе японской компании Komatsu Manufacturing Rus в Ярославле начат выпуск карьерного самосвала HD785-7 грузоподъемностью 91 т. Производственная мощность нового завода планируется в объеме 50–100 единиц техники в год в зависимости от спроса на рынках СНГ. Завод специализируется в основном на производстве экскаваторов и погрузчиков. Основные компоненты самосвала поставляются из Японии. В Ярославле осуществляется полный производственный цикл, включающий в себя процессы сварки, покраски габаритных узлов (кузов, рама и другие компоненты) и окончательной сборки машины. Планируется активная работа в направлении локализации, что позволит повысить процент компонентов российского производства в технике и снизит стоимость производимого оборудования. Для машин, собранных в Ярославле, многие детали и узлы изготовляются в России и из российских материалов, например, из специальных сталей «Северстали». Часть технологических процессов производства рамы, включающих сварку штампованных и литых деталей, разработанных российскими специалистами, уникальна.
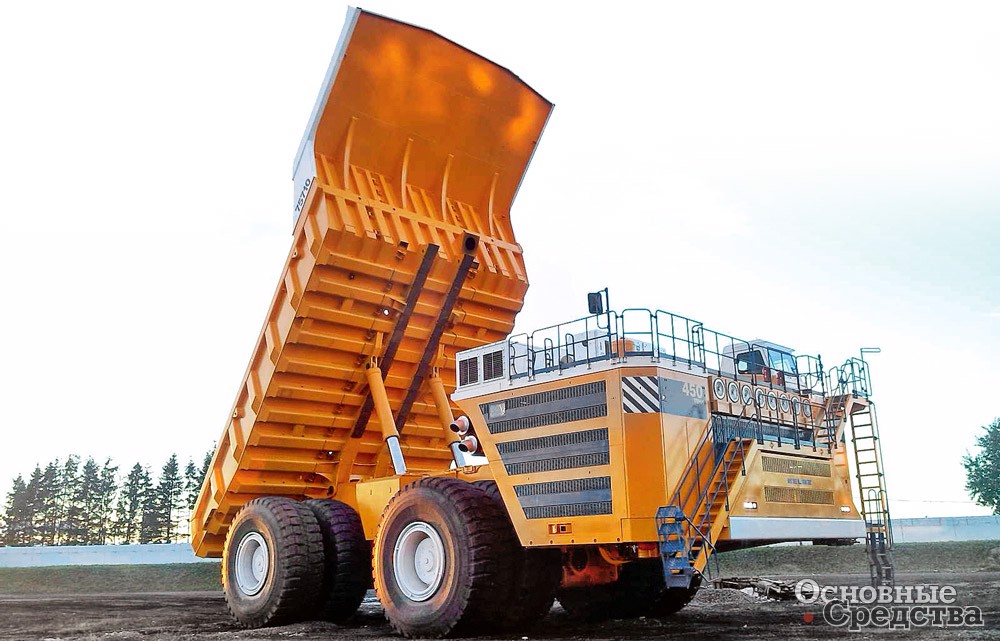
Еще в 2008 г. руководство компании Komatsu, проанализировав постоянно возрастающий экспорт самосвалов в Россию, приняло решение о строительстве завода по их выпуску. В качестве производственной площадки компании ООО «Комацу Мэнуфэкчуринг Рус» был выбран Ярославль. Инвестиции в строительство завода превысили 4,2 млрд руб., 94% которых составили средства компании Komatsu. В 2010 г. завод был введен в эксплуатацию, а с конца 2011-го началось производство самосвалов Komatsu HD785-7.
Завод Komatsu в Ярославле стал первым сборочным заводом Komatsu в России и 28-м по счету в мире. Его площадь составляет 50,2 тыс. м2. Максимальная численность персонала при выходе на проектную мощность в 3000 экскаваторов в год будет составлять 500 человек. Для подготовки специалистов и проведения практических занятий для студентов на базе Ярославского государственного технического университета компания Komatsu открыла учебный центр.
Карьерные самосвалы «БЕЛАЗ» – плод содружества науки и производства
Остановлюсь немного подробнее на карьерных самосвалах белорусского производителя «БЕЛАЗ», поскольку машины этой марки занимают доминирующее положение на российском рынке.
Серия | Грузоподъемность, т | Число моделей | Наименование моделей |
---|---|---|---|
7540 | 30 | 4 | 7540A, 7540B, 7540E, 7540K |
7544 | 32 | 1 | 75440 |
7547 | 42–45 | 3 | 7547, 75473, 75476 |
7545 | 45 | 3 | 75450, 75453, 75454 |
7555 | 55–60 | 6 | 7555B, 7555D, 7555E, 755F, 7555I, 7555H |
7557 | 90 | 2 | 75570, 75571 |
7558 | 90 | 3 | 75581, 75583, 75585 |
7513 | 130–136 | 7 | 7513, 75131, 75137, 75135, 75139, 7513R, 75311B |
7517 | 160 | 4 | 75170, 75172, 75174, 75173 |
7518 | 180 | 1 | 75180 |
7530 | 220 | 5 | 75302, 75306, 75307, 75309, 7530D |
7531 | 240 | 6 | 75310, 75311, 75315, 75312, 75318, 75313 |
7532 | 290 | 1 | 75320 |
7560 | 360 | 4 | 75602, 75603, 75604, 75605 |
7571 | 450 | 1 | 75710 |
7513R | 136 | 1 | 7513R |
Среди двадцати основных производителей карьерных самосвалов на жесткой раме «БЕЛАЗ» занимает лидирующие позиции – на его долю приходится более 30% мирового рынка машин большой и особо большой грузоподъемности, он предоставляет самую широкую линейку самосвалов от 30 до 450 т. В настоящий момент на сайте завода представлено 16 серий различных карьерных самосвалов, выпускается 52 модификации! А всего за 70-летнюю историю предприятия Белорусским автомобильным заводом разработано свыше 600 модификаций карьерных самосвалов г/п от 27 до 450 т, выпущено более 160 тыс. ед. карьерных самосвалов, которые были отправлены в 80 стран мира. Более 60% продукции «БЕЛАЗа» ориентировано на российский рынок. Ежегодно «БЕЛАЗ» на треть обновляет свою продукцию за счет совершенствования систем и узлов серийной техники и создания машин нового поколения. Изготовление новых моделей техники осуществляется благодаря содружеству с наукой путем внедрения прогрессивных научно-исследовательских, опытно-конструкторских и технологических работ на всех стадиях создания машины – от разработки конструкторской и технической документации до мелкосерийного производства.
В год своего 70-летия «БЕЛАЗ» представил ряд перспективных высокопроизводительных конкурентоспособных машин и проектов.
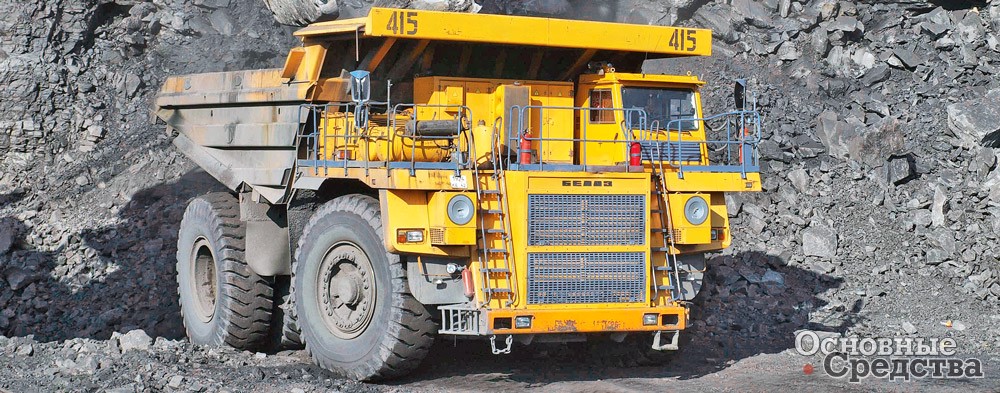
Карьерный самосвал БЕЛАЗ-75476 г/п 45 т открыл новое направление в производстве и эксплуатации карьерного транспорта, использующего в качестве топлива альтернативные источники энергии. Готовится к выпуску 136-тонный самосвал БЕЛАЗ-7513 с газопоршневым двигателем на базе двигателя компании Cummins КТА50-С. Выпущена опытно-промышленная партия БЕЛАЗ-7555Н г/п 60 т с планетарной коробкой передач, маслоохлаждаемыми тормозами и новым ведущим мостом с увеличенным ресурсом эксплуатации. Модернизированы карьерные самосвалы с электромеханической трансмиссией переменно-постоянного тока г/п 136 и 220 т. В соответствии с разработанной математической моделью энергоэффективной системы управления тягового электропривода применена инновация «БЕЛАЗа» – бесконтактный шкаф управления трансмиссией, работа которого основана на полупроводниковых приборах. Первая машина с этим узлом эксплуатируется в Кемеровской области.
Еще одной важной вехой в развитии предприятия становится введение в эксплуатацию самосвала БЕЛАЗ-75320, представляющего новый класс г/п – 290 т. Расширяется линейка выпускаемой карьерной техники в классе самосвалов максимальной г/п – 450 т. В составе серии БЕЛАЗ-7571 появится машина с электроприводом российского концерна «Электросила». Ведутся работы над созданием роботизированной техники, в 2017 г. разработана конструкторская документация на карьерный самосвал БЕЛАЗ-7513R г/п 136 т. Разработка и изготовление роботизированной мобильной системы управления самосвалом осуществлялась на ОАО «ВИСТ Групп» (Россия), а уже в апреле 2018 г. был изготовлен первый опытный образец.
Роботизированные самосвалы БЕЛАЗ-7513R предназначены для транспортировки горной массы в разрыхленном состоянии по технологическим дорогам, на открытых разработках полезных ископаемых с различными климатическими условиями. Могут работать в командном, а также дистанционном или автономном режимах в составе роботизированных горнодобывающих комплексов. Разрабатываются машины, использующие сменные аккумуляторные батареи вместо двигателя внутреннего сгорания. В числе приоритетных направлений разработка и освоение производства дизель-троллейвозов г/п 130–360 т на базе карьерных самосвалов с ЭМТ, применение которого обеспечит снижение расхода дизельного топлива не менее чем на 15%.
Начаты ходовые испытания 240-тонного карьерного самосвала БЕЛАЗ-75319 с новым двигателем из России – 12-цилиндровым 12ДМ-185, созданным на Уральском дизель-моторном заводе (УДМЗ). В конструкции двигателя воплощены передовые инженерные решения. Он снабжен современной электронной системой управления и мониторинга, газотурбинным наддувом и промежуточным охлаждением наддувочного воздуха.
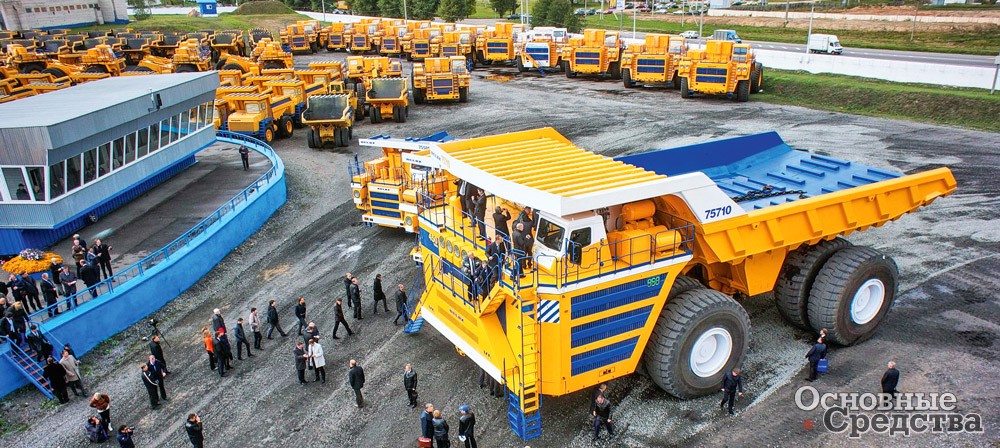
В сравнении с двигателями других производителей уральский 12ДМ-185 обладает увеличенным моторесурсом, высокой топливной экономичностью и продолжительным сроком работы. Этот силовой агрегат создан по госпрограмме «Национальная технологическая база». Благодаря легкому запуску двигателя и его устойчивой работе автомобиль можно будет использовать в разных климатических зонах.
Сейчас на сайте завода представлено 16 серий различных карьерных самосвалов.