
Подготовка, организация и освоение массового производства узлов и агрегатов к автомобилям ЗИЛ-131
В первой части статьи было рассказано о том, с какими сложностями пришлось столкнуться специалистам Брянского автомобильного завода (БАЗ) на первых этапах работ по организации массового производства ведущих мостов, раздаточных коробок, балансирных подвесок, коробок отбора мощности и других автокомпонентов для автомобиля ЗИЛ-131. Была проведена огромная работа по созданию на БАЗе первых автоматических линий. Но перед тем, как завод вышел на плановые показатели производства, еще предстояло решить множество проблем...
Специфика советского периода
Это сейчас все просто: есть необходимость в заказе, есть деньги, езжай, заключай договор – и дело сделано. Раньше все было иначе: на основании технических заданий составлялась сводная заявка, которая проходила целый ряд экспертиз в Гипроавтопроме, НИИТавтопроме. Последний рассматривал каждое техническое задание, проверял целесообразность заказа и технический уровень станка. Далее – Минавтопром и защита каждой позиции в СоюзГлавАвтотракторкомплекте, который, в свою очередь, защищал принятые заявки в Госплане СССР. Автоматические линии заказывались по Именному перечню Госплана СССР, и приходилось несколько раз добиваться совещаний в Госплане с нашим участием, чтобы решать вопросы выделения фондов и поставки автоматических линий.
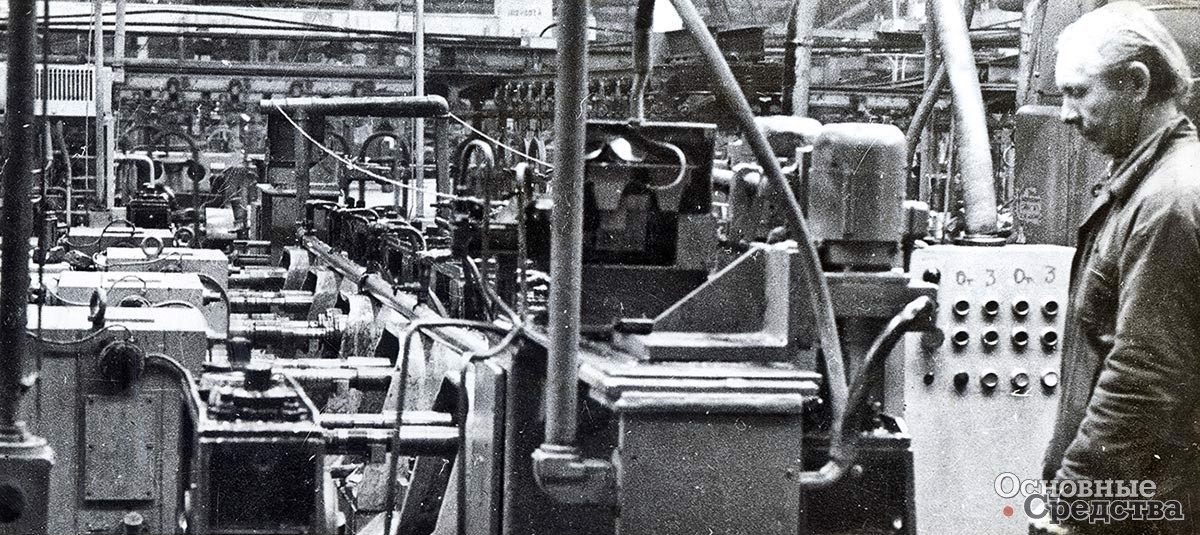
Выматывали поездки по станкозаводам для согласования технических заданий и составления протоколов. Но несмотря на все трудности, нам удалось добиться поставки необходимого оборудования, в том числе и 15 автоматических линий, таких как 1Л340А, 1Л340Б, 1Л341А, 1Л341Б, 1Л355, 1Л356А, 1Л356Б – для обработки корпусных деталей.
Очень сложно обстояли дела с заказом оборудования по импорту – здесь требовалось получить еще и заключение Минстанкопрома о невозможности изготовления оборудования на его заводах. Но мы смогли обеспечить поставку оборудования и по импорту, особенно на финишные операции, такие как алмазно-расточные, многокамневые шлифовальные станки и др., в том числе много станков ЧПУ и обрабатывающих центров для автомобильного производства.
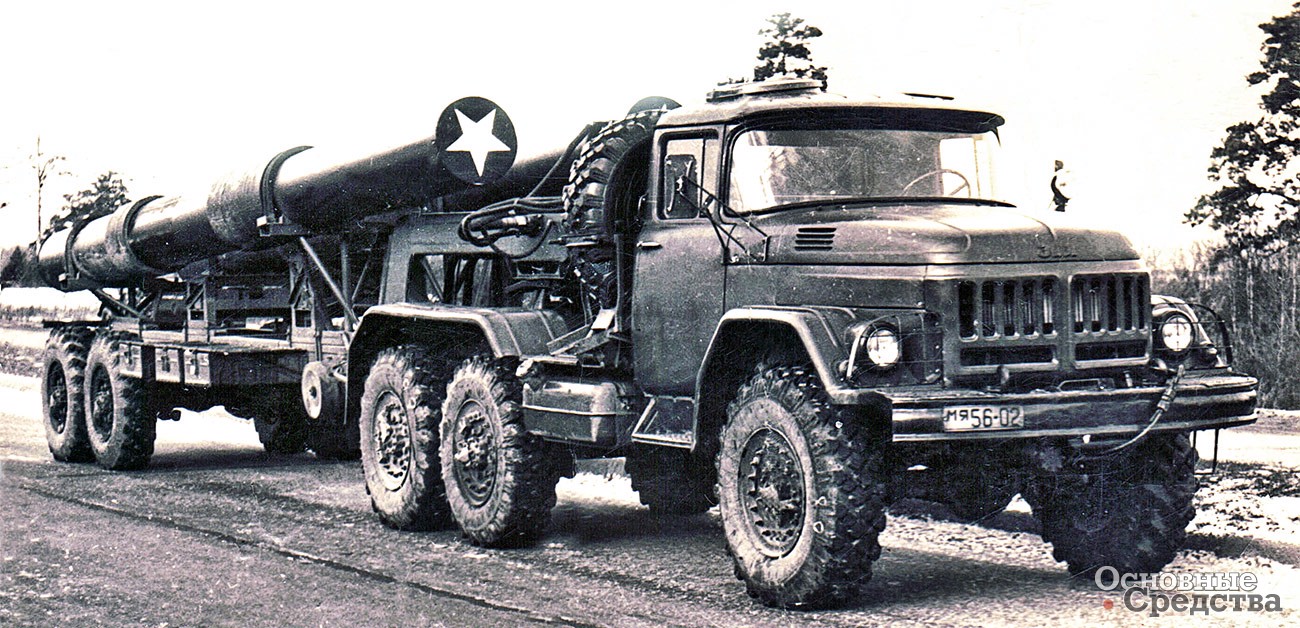
Одним из «узких» мест в автоагрегатном производстве было изготовление барабана ножного тормоза. Поначалу Управление оборудования Минавтопрома предложило нам заказать в Румынии линию для изготовления этой детали и организовало встречу в румынском посольстве в Москве. При обсуждении вопроса с представителями фирмы под «коньяк» мы пришли к выводу, что предложение румынской стороны нам не подходит.
Автоматические линии для обработки барабанов ножного тормоза изготавливались в двух странах: в США и Великобритании, причем США заказывали балансировочные станки в Англии. Руководством завода: директором К.К. Ярошевичем, главным инженером И.Н. Лештаном, главным технологом В.С. Ячменёвым в Минавтопроме и Госплане СССР после многочисленных согласований и обоснований был решен вопрос поставки импортной автоматической линии «Кросс» из США для обработки барабана ножного тормоза. Большую подготовительную работу по заказу автоматической линии проделал начальник технологического бюро МСЦ-4 Э.Г. Галкин.
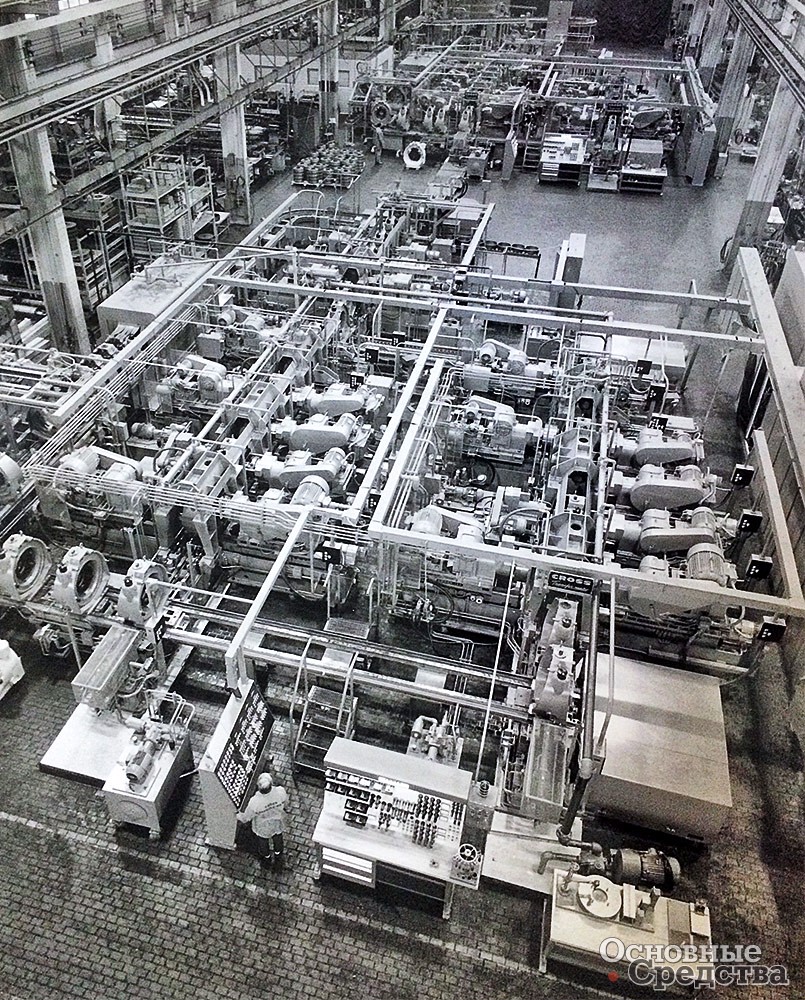
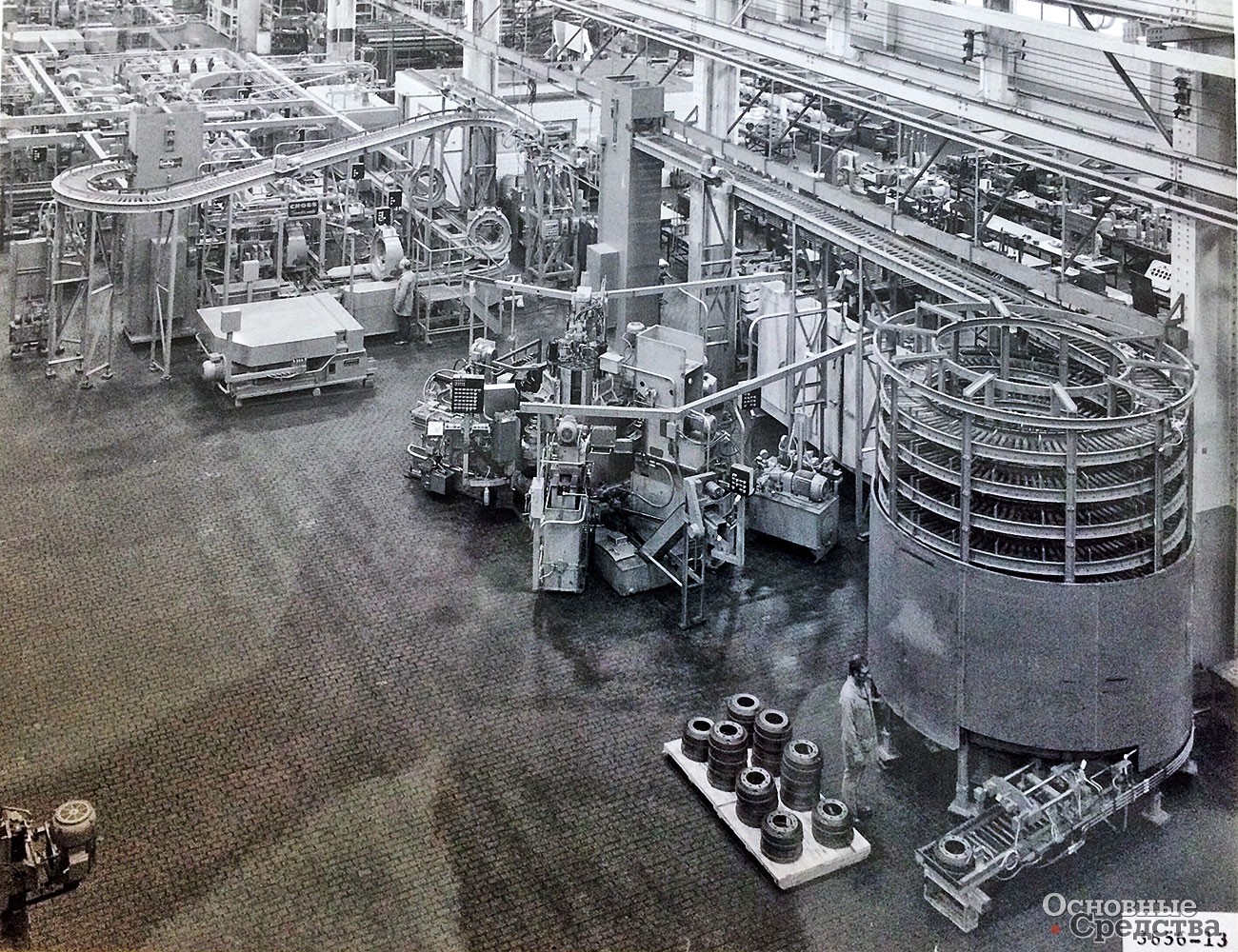
На приемку автоматической линии в США был направлен специалист из Центральной заводской лаборатории технологических исследований и наладки (ЦЗЛТИН) Э.А. Лагерев, от отдела главного механика – А.Т. Щедривый, от отдела главного энергетика – В.И. Разводов, а в Англию – А.Ф. Ковалёв, от отдела главного механика – В.И. Колянов. Э.Г. Галкин обиделся, что его не послали на приемку автоматической линии, и ушел с завода.
Автоматическая линия «Кросс» была смонтирована в южном пролете корпуса № 6 на месте, где прежде размещался цех раздаточных коробок (ЦРК). Под руководством заместителя начальника ОПСМ А.С. Бойко начальником КБ Ю.А. Антиповым и другими конструкторами была спроектирована автоматизированная система подачи барабанов к автоматической линии со склада заготовок, благодаря которой руки человека в процессе обработки уже не прикасались к барабану. Это был настоящий прорыв в технологии обработки и транспортировки барабана ножного тормоза.
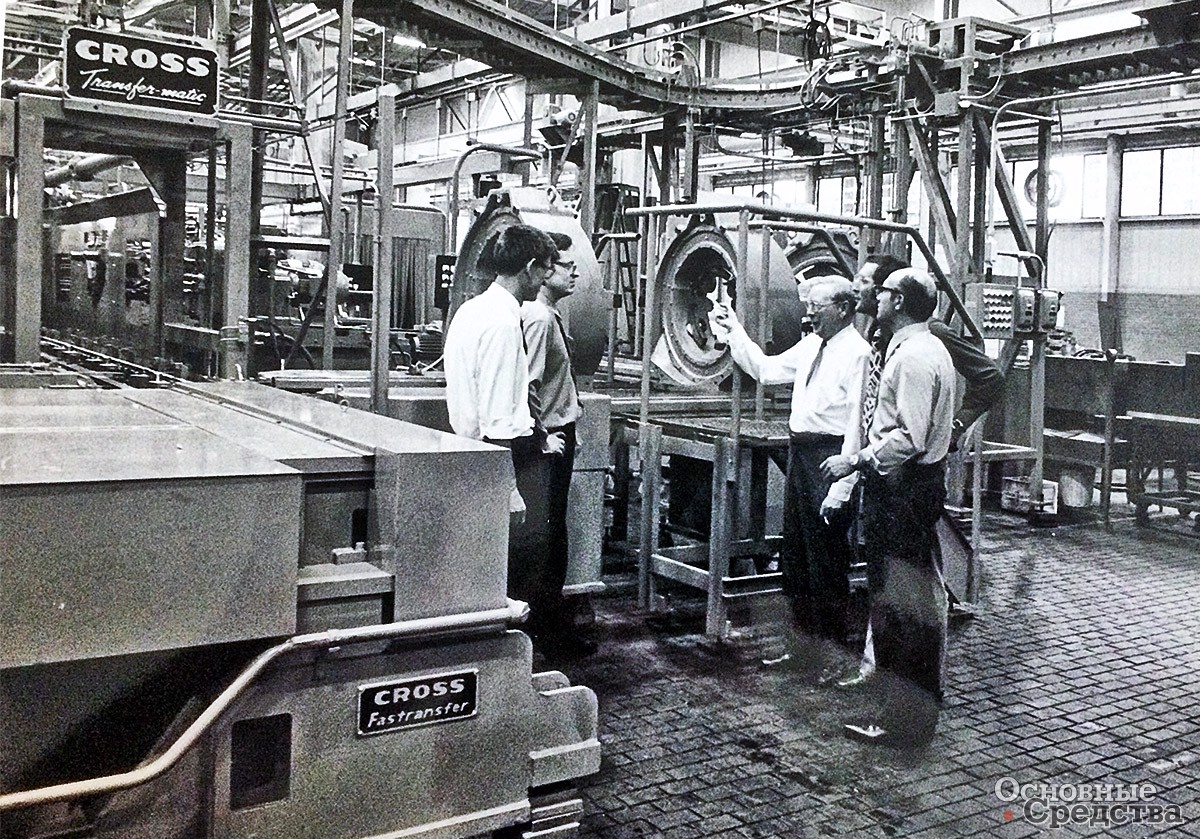
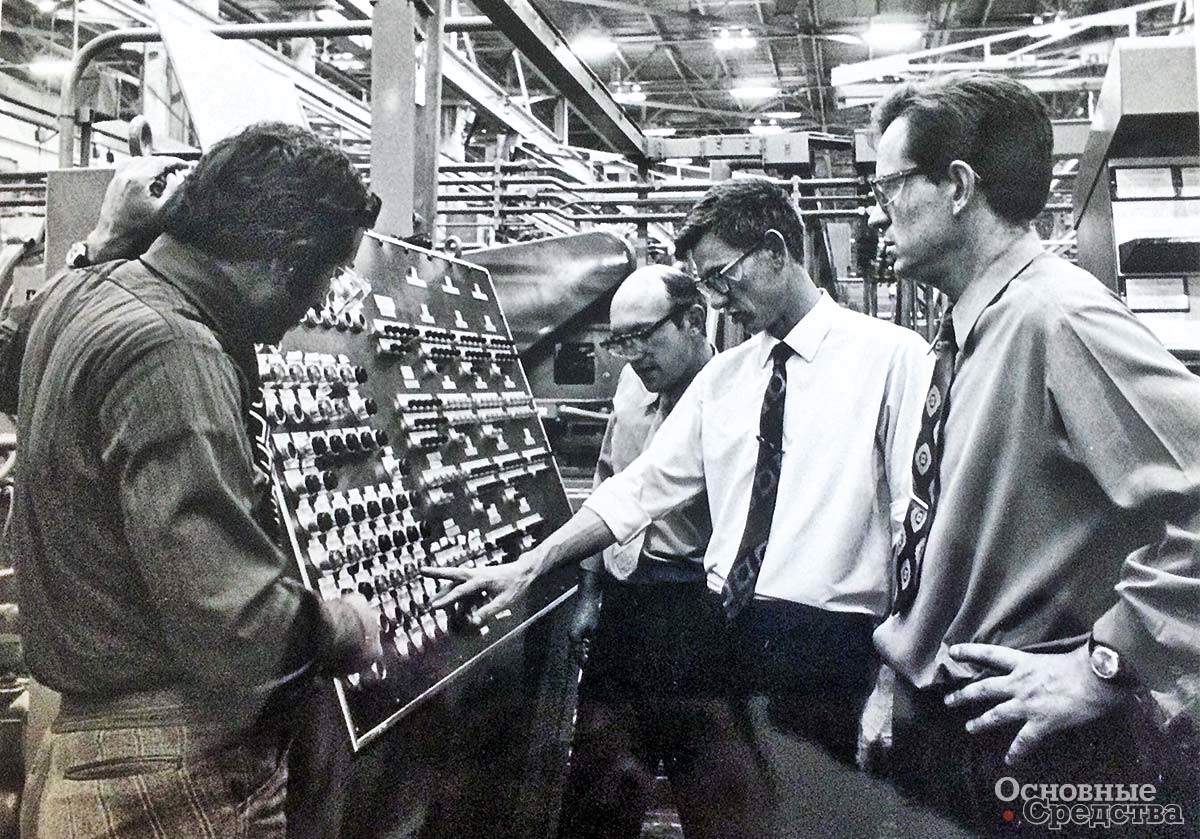
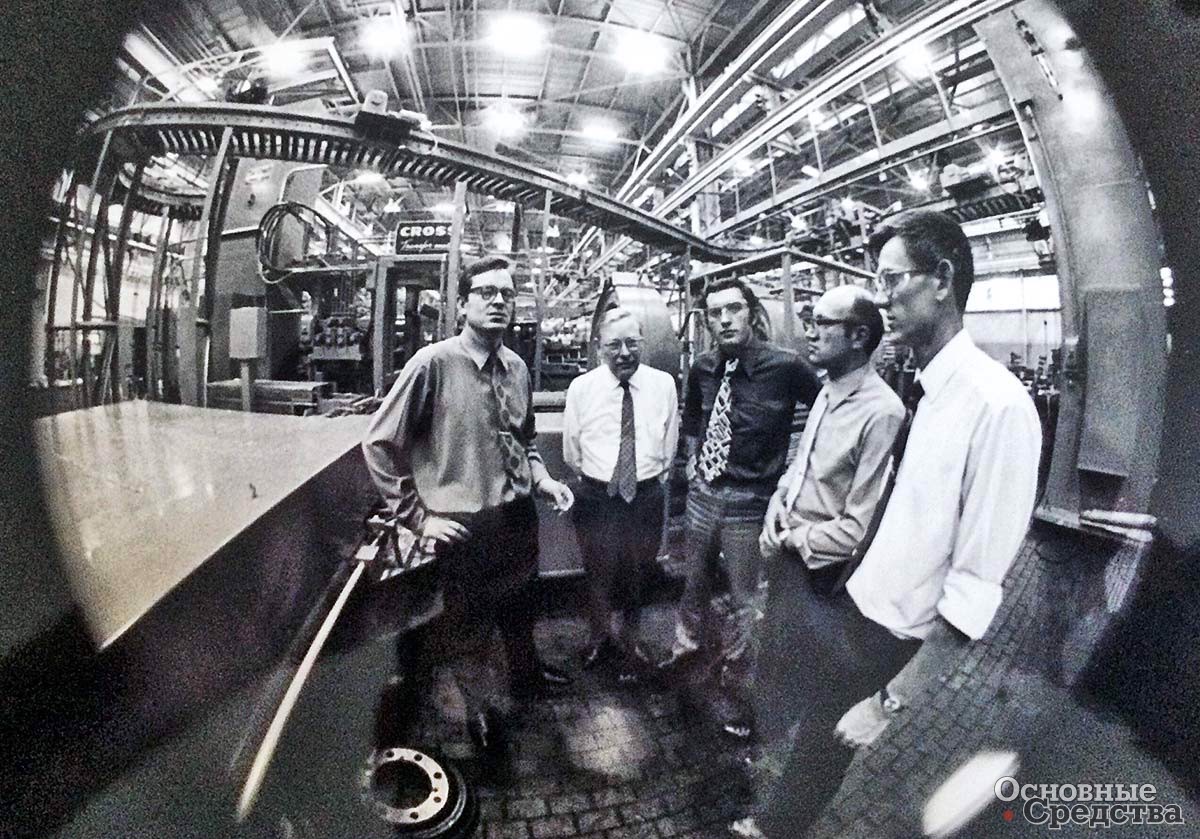
В связи с тем, что для размещения автоматической линии «Кросс» требовалось освободить пролет корпуса от цеха раздаточных коробок, была проделана огромная работа по подготовке производства и площадей в корпусе № 7 для размещения ЦРК. Проектно-технологическое бюро автоагрегатного производства (ПТБ ААП) разработало очень хорошую планировку цеха. Были удачно построены поточные линии обработки деталей, которые после финишных операций как бы сами «подходили» с двух сторон к сборочному конвейеру, который был расположен посреди цеха. Были спроектированы, изготовлены и смонтированы подвесные цепные конвейеры для передачи деталей от станка к станку, изготовлен фундамент для монтажа автоматической линии 1Л-131 для обработки картера раздаточной коробки. Если в корпусе № 6 сборка раздаточной коробки осуществлялась на стендах, то для корпуса № 7 был спроектирован и изготовлен сборочный конвейер. Была спроектирована и изготовлена окрасочная камера с подвесным цепным конвейером с подачей готовых коробок на эстакаду склада готовой продукции и многое-многое другое нестандартное оборудование. Перемонтаж оборудования ЦРК из корпуса № 6 в корпус № 7 производился очень оперативно, без остановки производства.
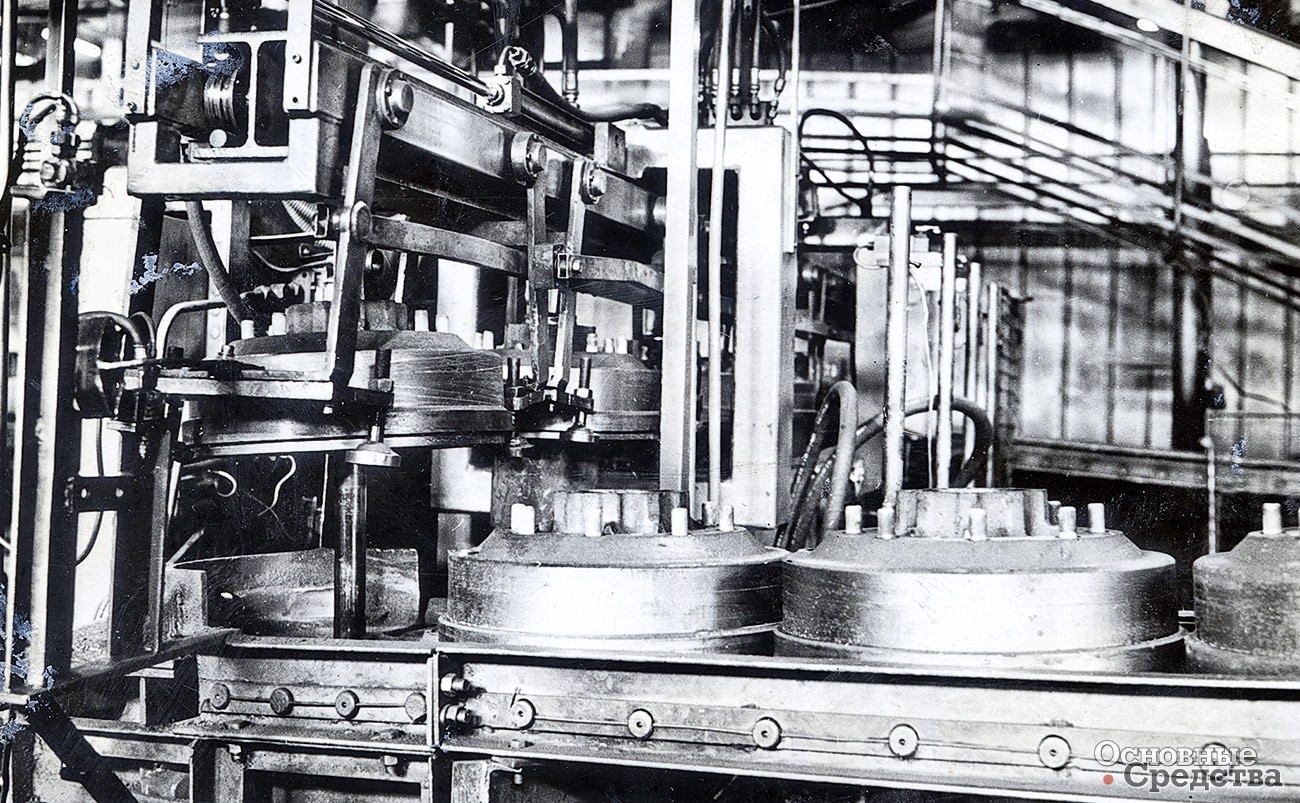
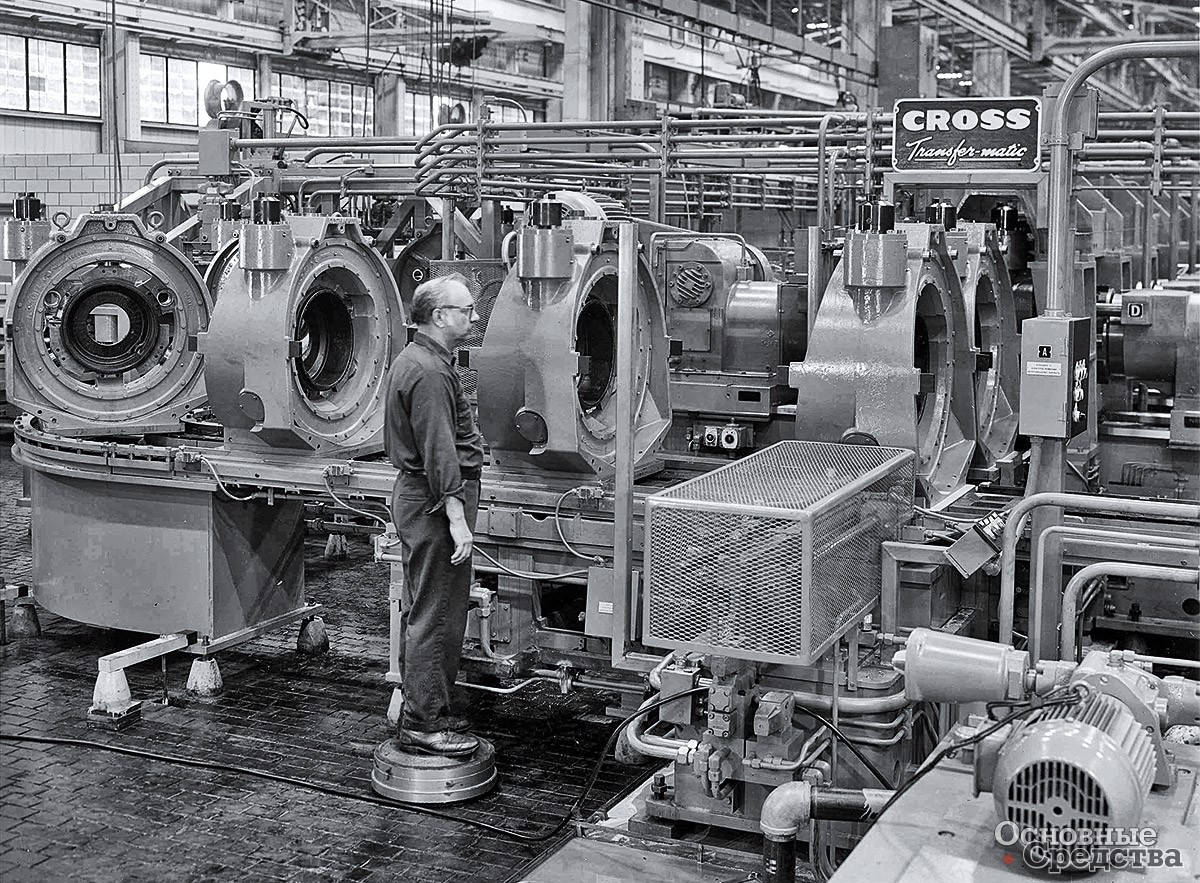
В организации слаженной работы ЦРК была большая заслуга всего коллектива цеха: начальника В.Г. Краснянского, заместителя начальника цеха по подготовке производства В.Н. Пищикова, заместителя по производству В.Н. Пономарёва, главного технолога производства В.С. Корнеева, начальника технологического бюро В.Н. Шалатонова, энергетика В.В. Разводова, механика П.П. Кузина и всего состава вспомогательных служб цеха, а также начальника механомонтажного цеха П.И. Рыжикова и его коллектива. Что касается изготовления и освоения производства раздаточной коробки, то следует также отметить активную работу ТБ ЦРК (А.С. Ермакова – он ранее был одним из начальников бюро, технологов В.А. Фетисову, А.Г. Сухову).
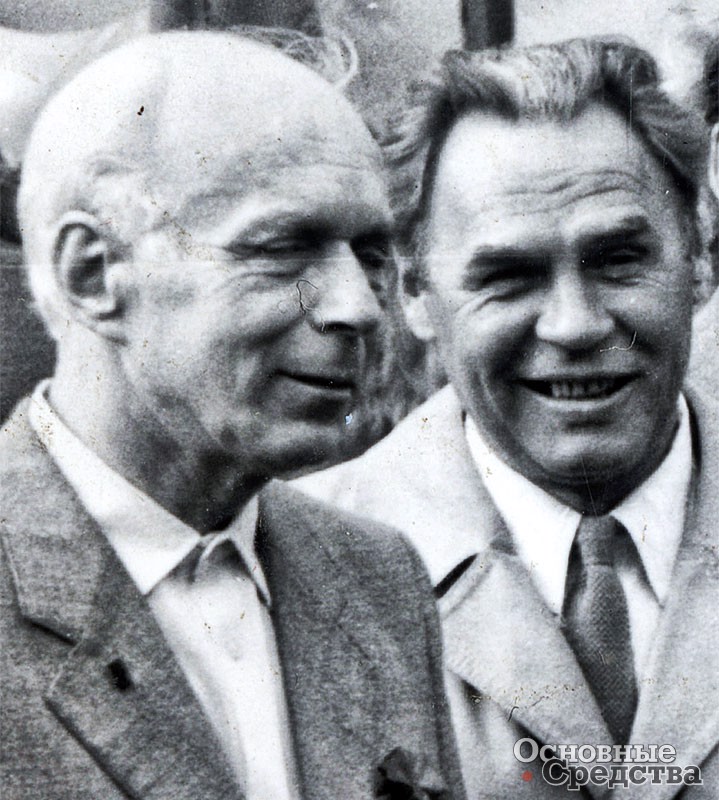
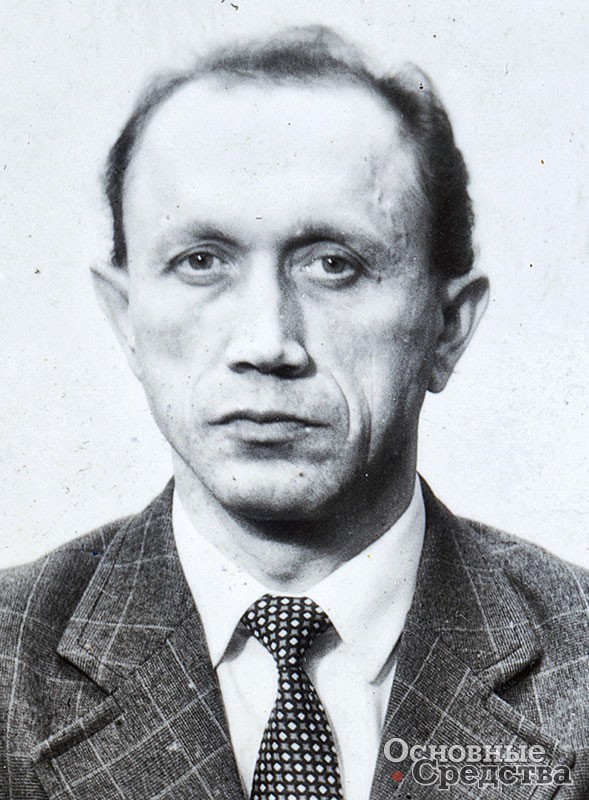
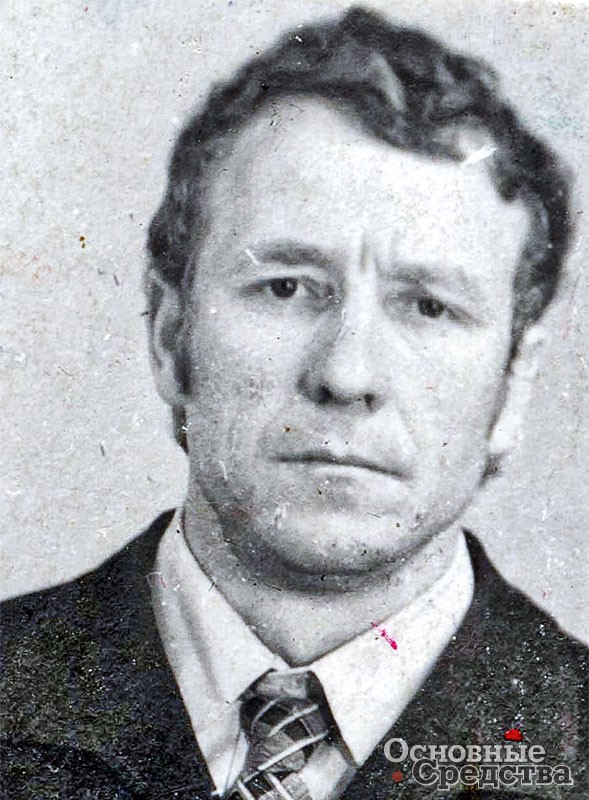
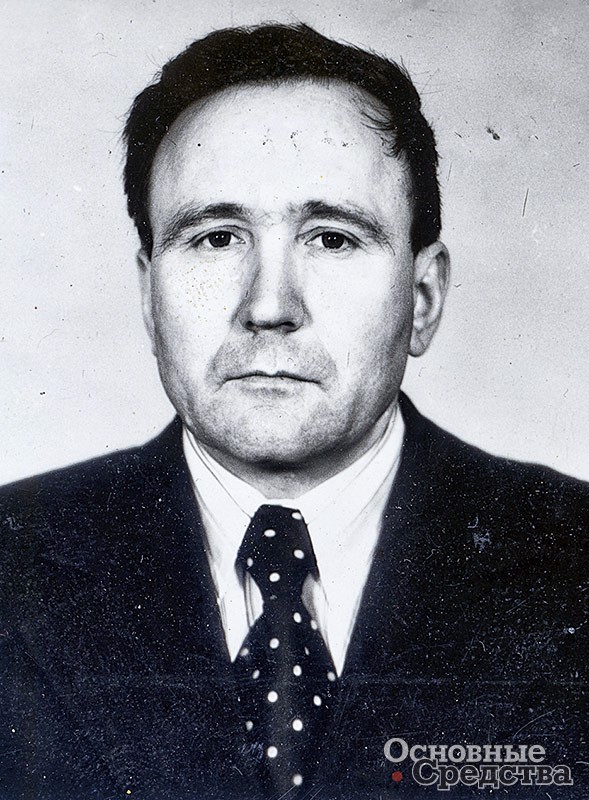
Большой вклад в создание и развитие производственных мощностей внесли специалисты бюро оборудования отдела главного технолога завода – руководитель группы Н.Е. Азовцев и старший инженер-технолог Л.А. Родкина. Они работали в тесном контакте с начальниками технологических бюро и главными технологами производства. Собирали заявки и технические задания на проектирование и изготовление оборудования, составляли сводную заявку. Участвовали в защите заявок в Гипроавтопроме, НИИТавтопроме, Минавтопроме, СоюзГлававтотракторкомплекте. Направляли технологов на заводы Минстанкопрома для составления протоколов согласования на проектирование и изготовление специального оборудования.
Специалисты отдела подготовки производства ОГТ – М.Г. Петрушина, В.Г. Гришина, В.И. Вдовченко, Д.Д. Дунаева и начальник бюро А.Г. Бондарев составляли графики на проектирование специальной оснастки и инструмента, нестандартного оборудования, согласовывали сроки изготовления с исполнителями – КОСТО, ОПСМ, инструментальным отделом, цехом средств механизации и осуществляли контроль за выполнением графиков.
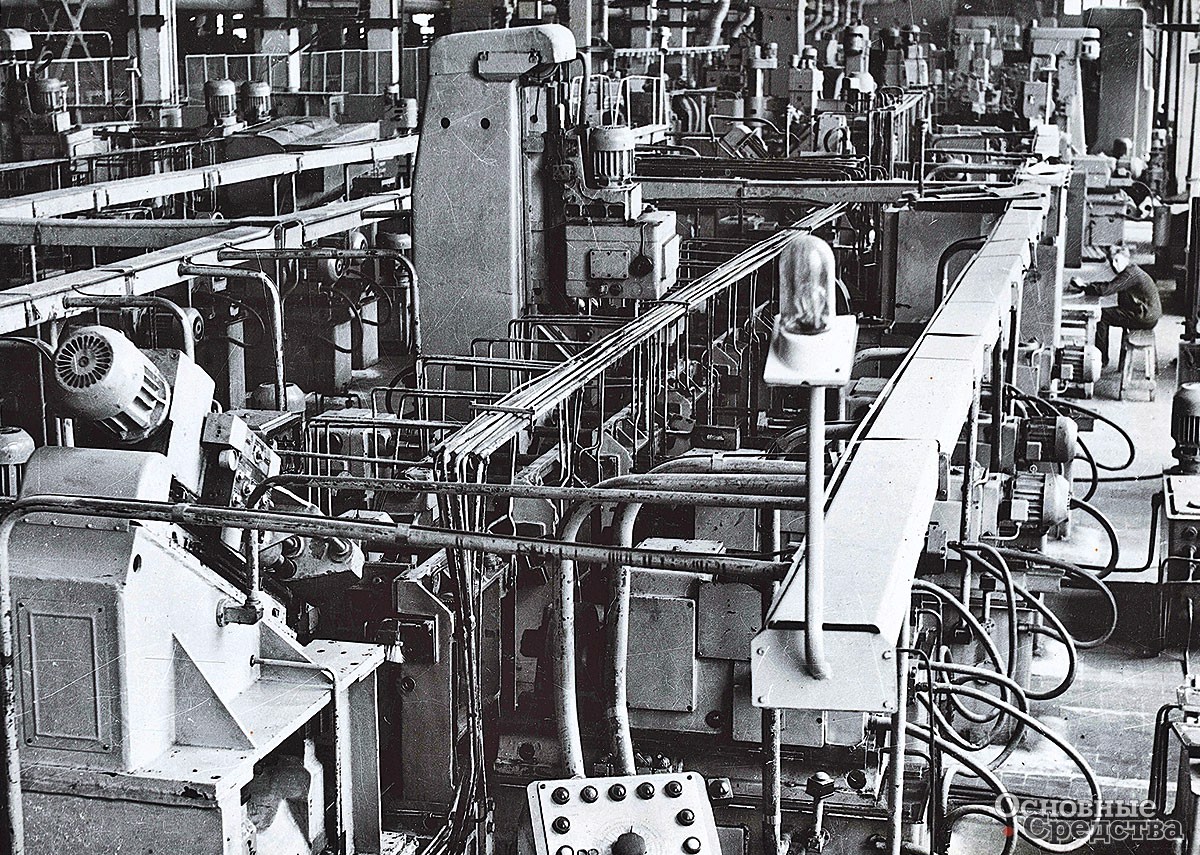
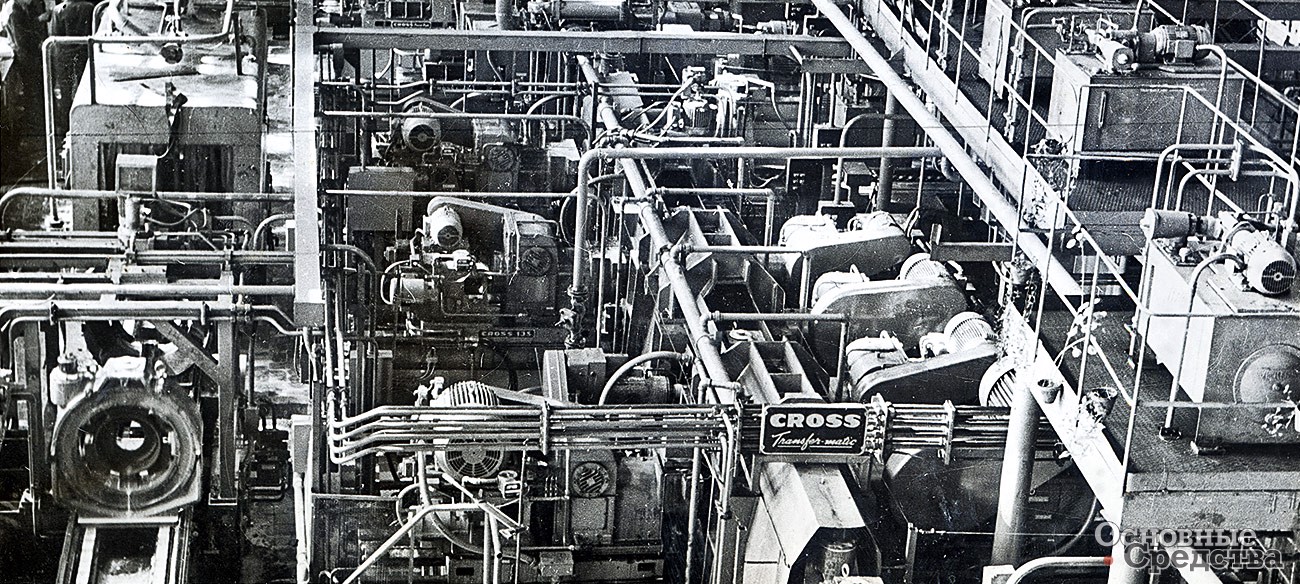
Руководили отделом подготовки производства М.Е. Непомнящий и после его ухода на пенсию А.А. Ковалёв.
Необходимо отметить активную работу по внедрению специальной оснастки и инструмента, нестандартного оборудования, «доводке» технологических процессов и внедрению их в производство начальников технологических бюро А.С. Ермакова, Э.Г. Галкина, А.К. Попова, М.С. Борисова, В.Н. Власкина, И.С. Качура, В.Ф. Глытова, А.Н. Шершнева, В.Н. Шалатонова, А.В. Плаксина, Ю.М. Ромахина, Н.С. Буненкова, П.В. Евтуха, который впоследствии стал заместителем начальника механосборочного цеха № 5, а затем и заместителем главного инженера автоагрегатного производства по полуторатонному автофургону (после ухода с БАЗа он работал начальником отдела в проектном институте ГПИCтроймаш).
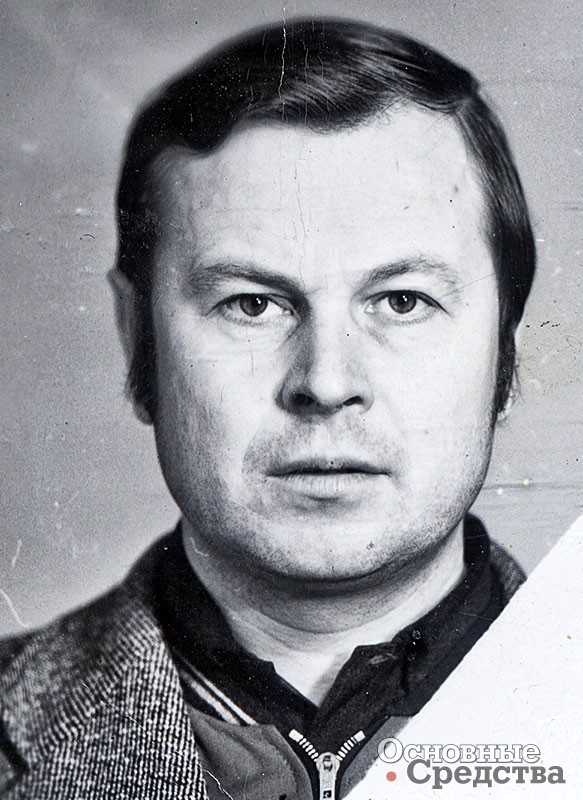
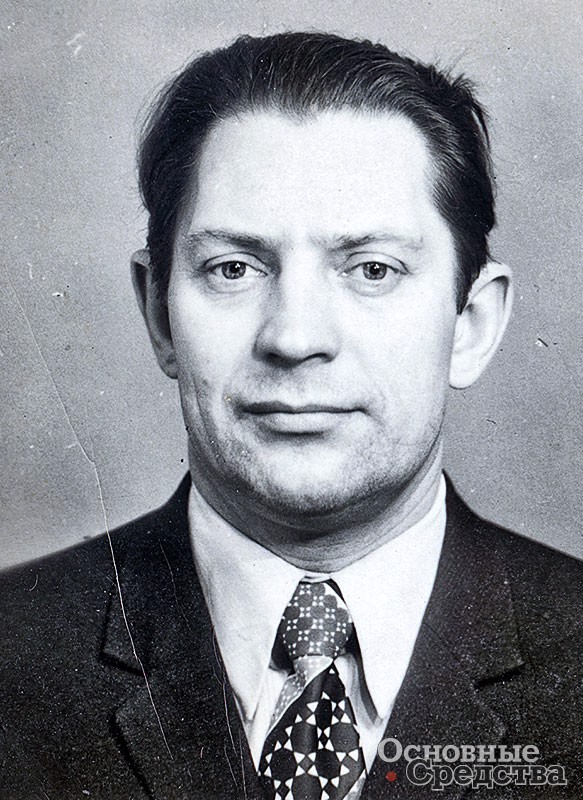
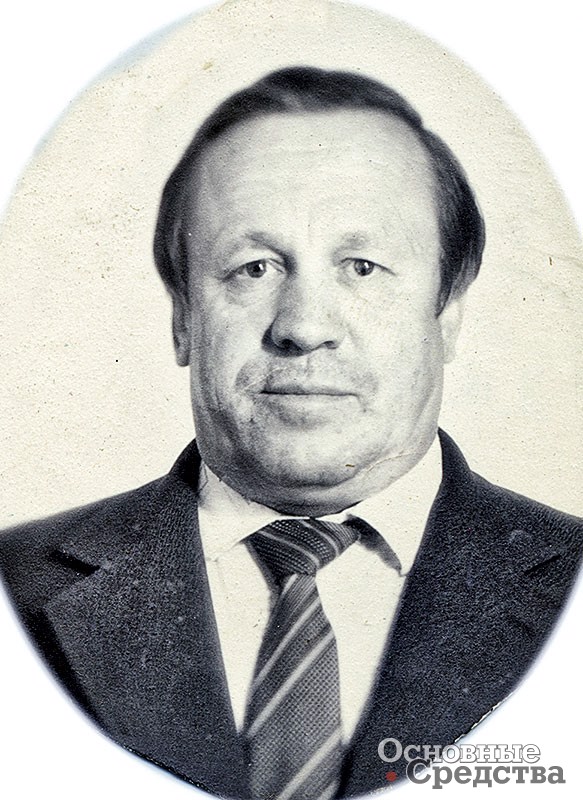
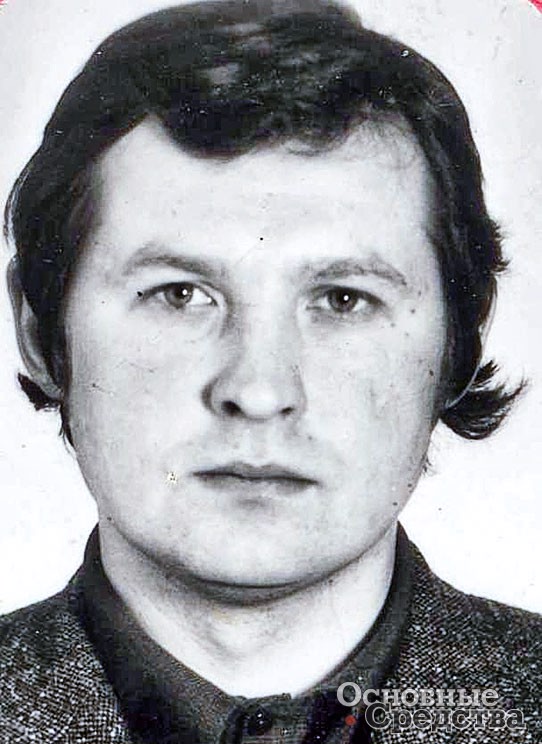
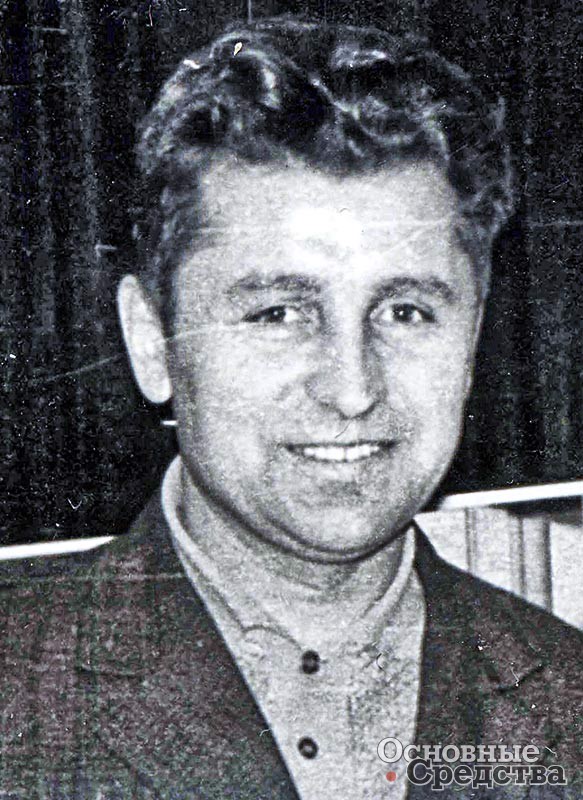

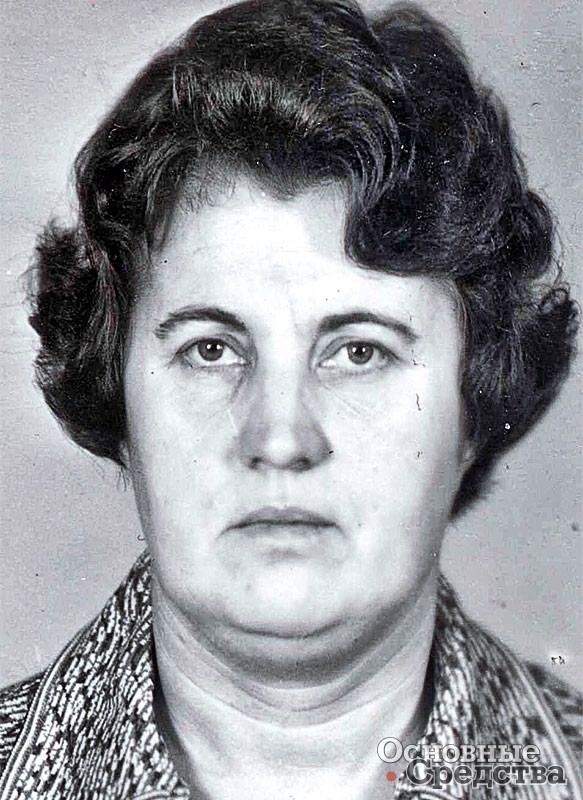
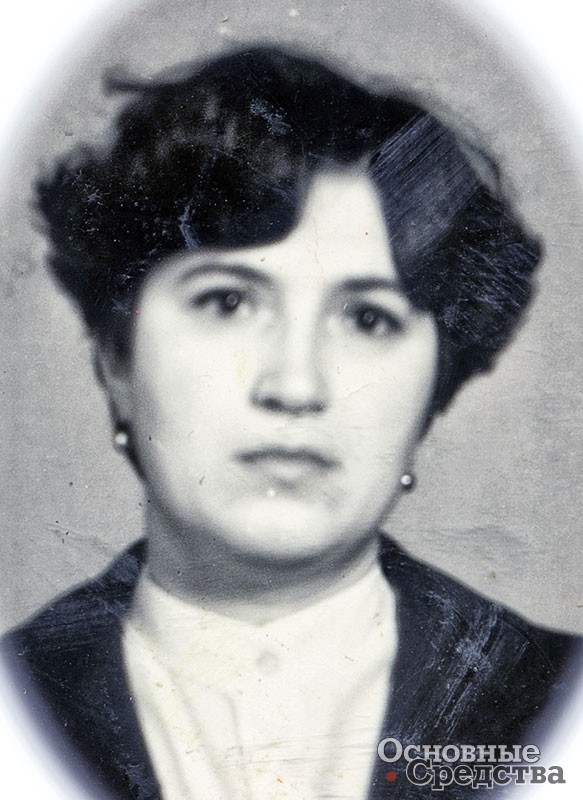
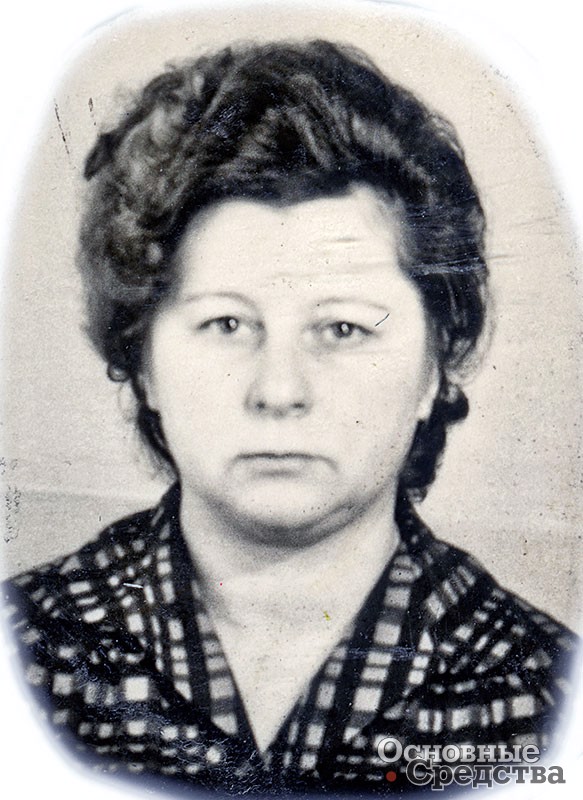
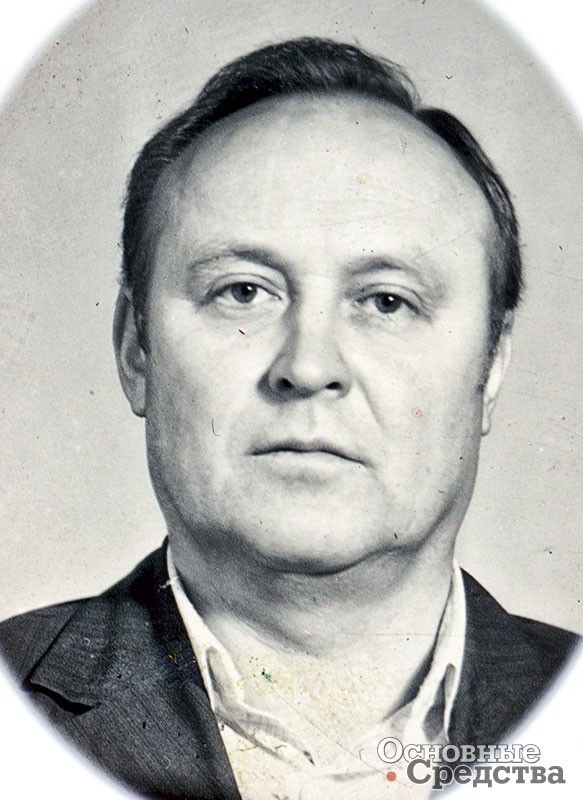

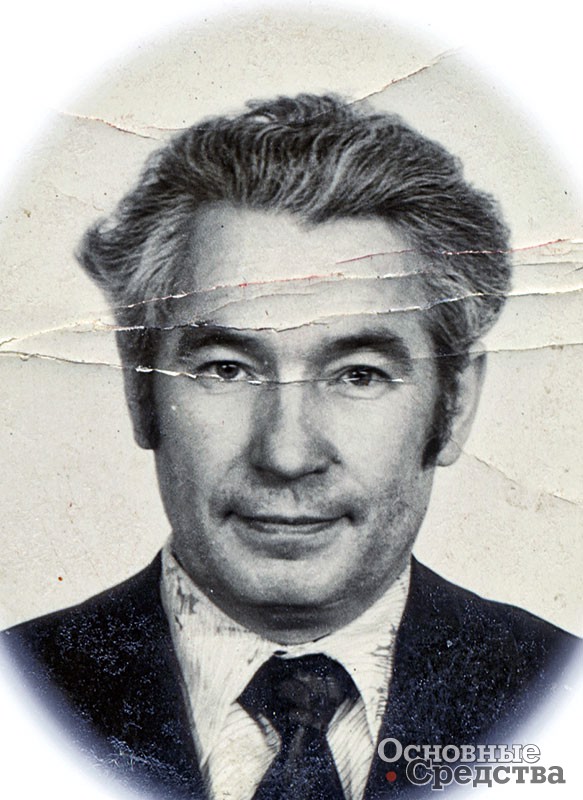
Также самоотверженно работали и их технологи, порою сутками не выходили из цехов: Ю.С. Трусов, А.И. Штырхунов, П.И. Одринский, Л.А. Родкина, В.М. Прудников, Л.А. Савинов, Г.И. Кузнецова, В.В. Воробьёва, Г.П. Лосунова, А.И. Семёнов, Э.В. Соловьёв, Т.В. Тарасенкова, Т.А. Королёва, В.А. Фетисова, А.Г. Сухова, Н.А. Цыгунова, М.В. Фролов, А.Э. Смирнов, В.Н. Колягин, Я.И. Козлова и др.
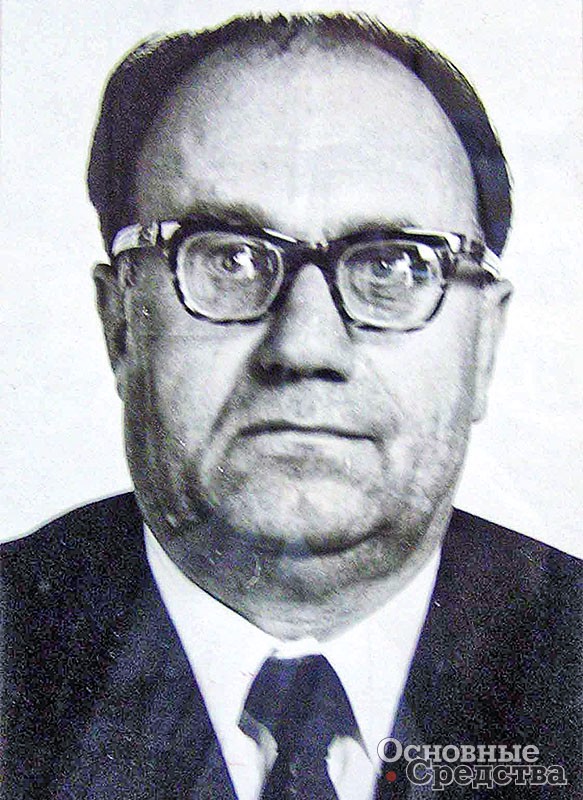
Руководили автоагрегатным производством В.С. Титов, В.М. Старкин, В.Н. Пономарёв. Главными технологами производства были В.С. Корнеев, В.М. Пустовойтов, Е.Н. Дятлов, главными инженерами – И.Н. Лештан, И.Е. Зуев, В.И. Колянов, В.С. Корнеев, В.Н. Пищиков.
Особо надо сказать о генеральном директоре Брянского автозавода В.Х. Чекулаеве. Это был настоящий руководитель, организатор, грамотный инженер и талантливый технолог, с которым было приятно и легко работать. При нем началось освоение первой очереди корпуса № 9. Виталий Харитонович очень серьезно относился к предстоящим перепланировкам и перемонтажам оборудования. Неоднократно рассматривал наши планировки и никогда не вызывал нас с кипами чертежей и другими документами к себе в кабинет, а сам приходил в отдел, и если что-то не нравилось, говорил, что сейчас он не имеет времени детально все просмотреть, а вот в выходной давайте соберемся и еще раз посмотрим. В воскресенье приходил в бюро, брал в руки «габаритки» станков и строил разные варианты поточных линий. Рассмотрев несколько вариантов, еще раз очень внимательно изучал наши предложения, задавал много вопросов и в конце концов соглашался, что наша планировка самая удачная, и давал добро на перемонтаж.
Главные технологи завода В.С. Ячменёв, Е.А. Токарев и главный инженер завода И.Н. Лештан уделяли большое внимание развитию и становлению Брянского автозавода, созданию производственных мощностей.
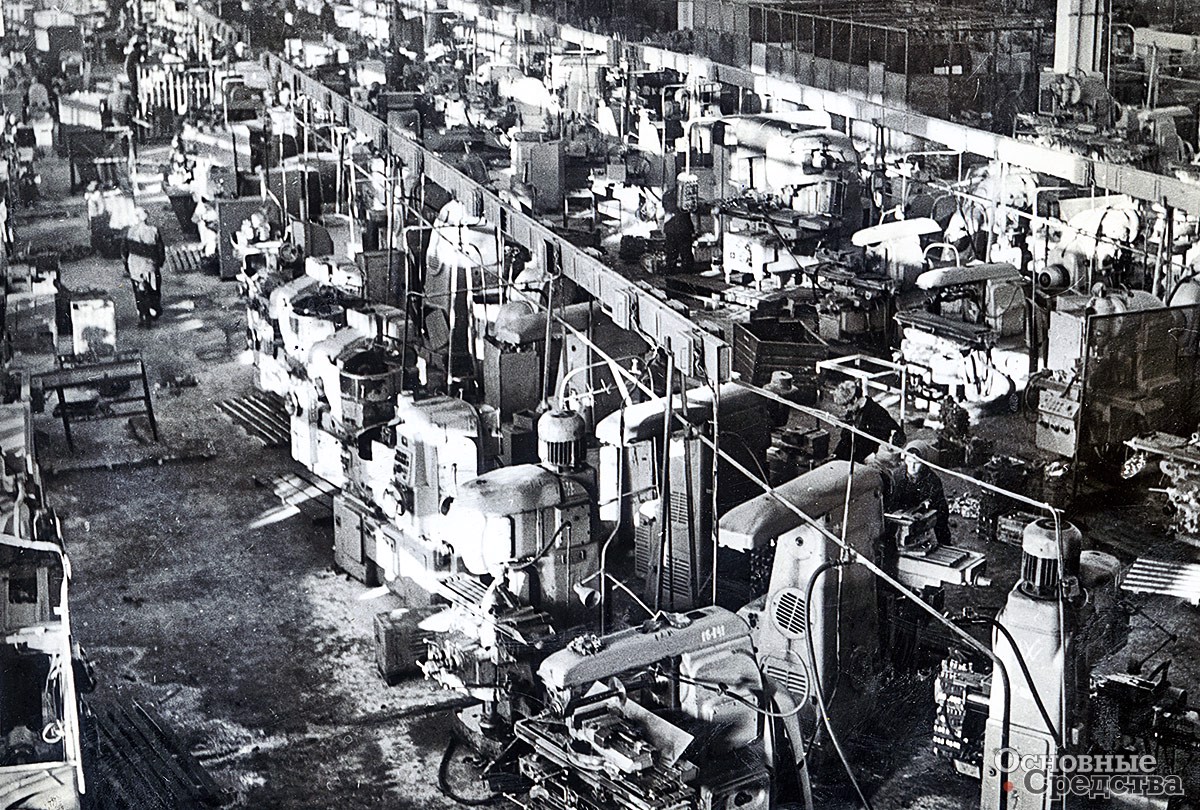
Выход на плановые показатели
В результате осуществления мероприятий, предусмотренных проектом, в 1978 г. были созданы производственные мощности на выпуск 55 тысяч комплектов агрегатов к автомобилям ЗИЛ-131.
В том же году фактический выпуск составил 48 669 комплектов. Постепенно плановые задания увеличивались, и в 1988 г. автоагрегатное производство полностью освоило производственные мощности, изготовило и поставило ЗИЛу 55 039 комплектов агрегатов к автомобилям ЗИЛ-131.
По вопросам проектирования оснастки и инструмента мне приходилось работать с руководителями КОСТО, начальниками конструкторских бюро и их коллективами: А.Н. Налётовым, Е.А. Токаревым, И.Д. Нестеровым, бывшим фронтовиком В.А. Прониным, Т.В. Волковой, Н.В. Гуренковым и др. Все они были высококвалифицированными специалистами, талантливыми инженерами, хорошо знавшими свое дело.
Большую помощь в освоении, наладке и внедрении специального оборудования оказали специалисты ЦЗЛТИН под руководством С.И. Житницкого. Это был хороший инженер и опытный руководитель. Начальники лабораторий ЦЗЛТИН О.С. Андрейчиков, В.Ф. Чистов, А.И. Гдалевич, А.Н. Серваровский, Л.М. Натапов, А.М. Есин, Е. И. Жучков и их специалисты вместе с технологами активно занимались наладкой оборудования и вводом его в эксплуатацию.
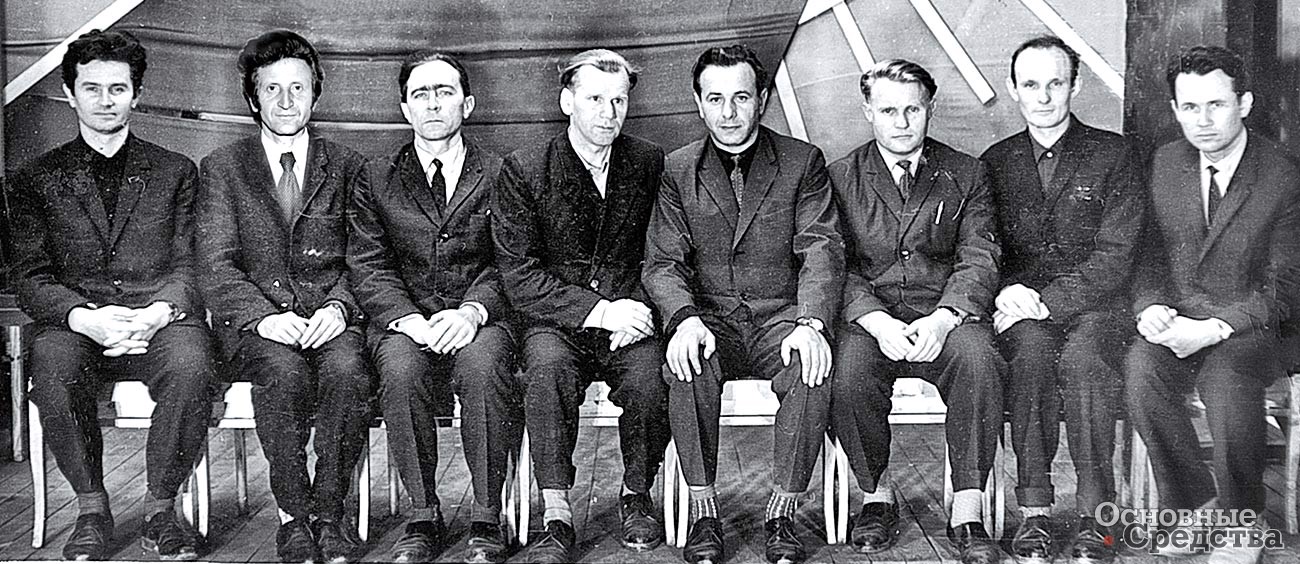
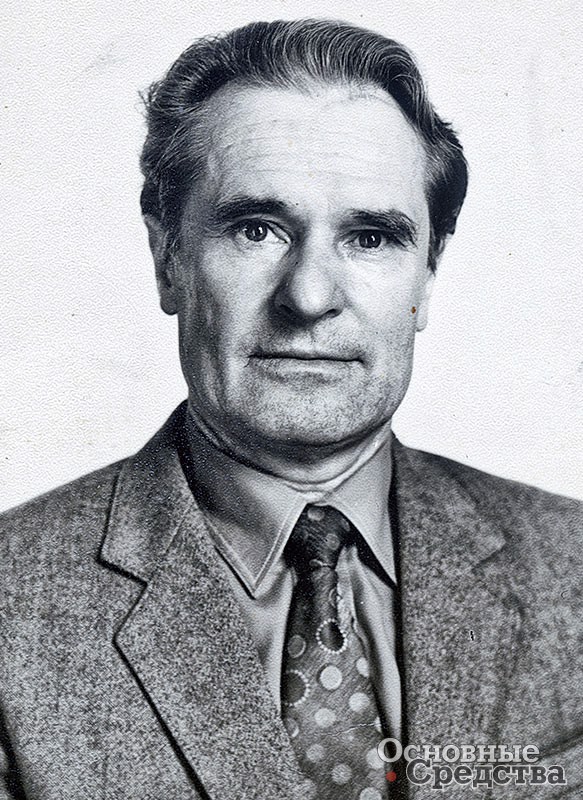
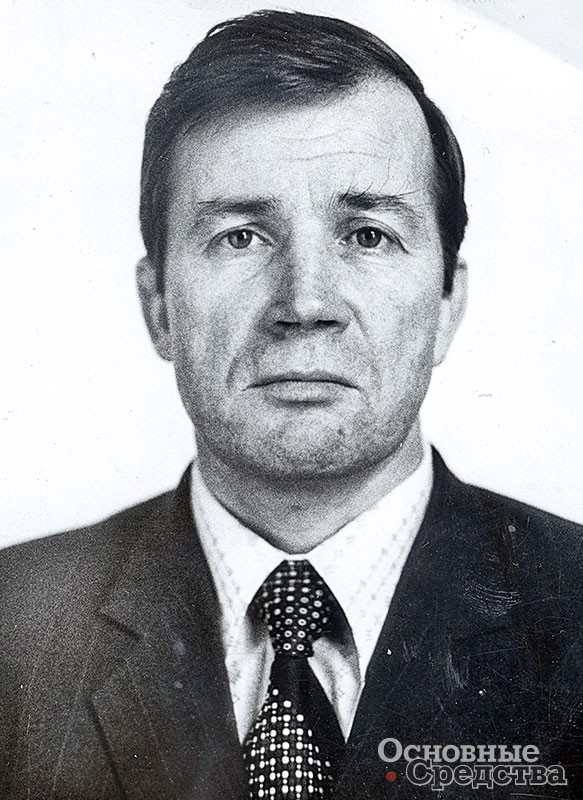
Технические службы автоагрегатного производства работали в тесном контакте с заместителем Главного конструктора завода по изделию ЗИЛ-131 Н.А. Горенковым, начальником конструкторского бюро А.И. Константиновым, В.Ф. Медведевым и др., неоднократно вместе с ними выезжали на ЗИЛ для решения технических вопросов.
Особенно запомнилась совместная работа со специалистами МосАвтоЗИЛа: начальником отдела управления главного технолога по проектированию оснастки К.И. Степановым, начальником КБ В.И. Зенкиным, начальником техчасти корпуса И.П. Перелыгиным, который впоследствии стал начальником управления главного технолога; заместителем главного конструктора и его специалистами: Г.А. Феста, Б.С. Карелиным, Г.Б. Армандом, А.Н. Алюлиным, Б.Ф. Хмелининым. Всех их отличала высокая эрудиция, человечность и дружелюбие. Они были прекрасными инженерами и всегда с пониманием относились к нашим проблемам, охотно делились своим опытом, и мы многому у них научились.
Я вспоминаю один случай: представитель заказчика очень часто «доставал» нас при приемке и обкатке конических шестерен – 131-2402017 и 131-2402060: то шумят, то пятно контакта не то. Пришлось обращаться к помощи ЗИЛа. Приехал заместитель Главного конструктора Георгий Александрович Феста – умнейший человек. Вошли мы в бесшумную комнату, где производилась обкатка, он послушал-послушал, проверил пятно контакта, никаких замечаний не сделал и сказал, что шестерни не шумят только в одном случае – когда они лежат рядом на полке. Был определен эталон по шуму и пятну контакта, и претензий по этому вопросу у заказчика больше не было.
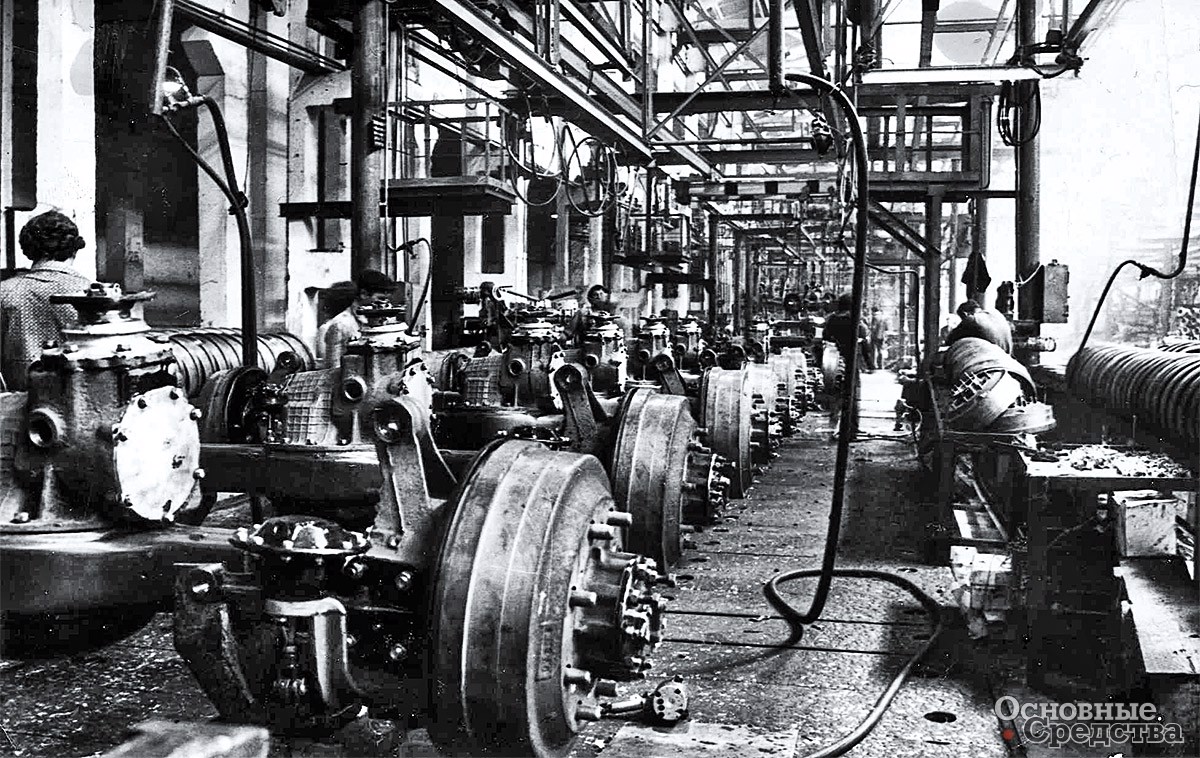
Мне приходилось постоянно выезжать в Минстанкопром и на заводы Минстанкопрома для согласования технических заданий на проектирование и изготовление специальных станков и автоматических линий, решать вопросы поставки оборудования и добиваться выделения фондов.
Основными поставщиками агрегатных, специальных станков и автоматических линий были московские станкозаводы: ЗИО и «Станкоогрегат».
Проектированием агрегатных станков и автоматических линий для обработки корпусных деталей для Московского станкозавода им. Орджоникидзе занималось Московское специальное конструкторское бюро – СКБ-1, в дальнейшем переименованное в МосСКБАЛиАС, а автоматических линий для токарной обработки валов, полуосей и других деталей тел вращения – отдел главного конструктора станкозавода.
Разработку технологии и составление протоколов согласования на проектирование и изготовление станков мы выполняли вместе с начальником отдела согласования МосСКБАЛиАС Ильей Борисовичем Амроминым, а автоматических линий для токарной обработки деталей тел вращения – с заместителем главного конструктора Московского станкозавода им. Орджоникидзе Евгением Филипповичем Соколовым.
Это были высококвалифицированные специалисты, грамотные инженеры, хорошо знали свое дело и принимали прогрессивные технические решения.
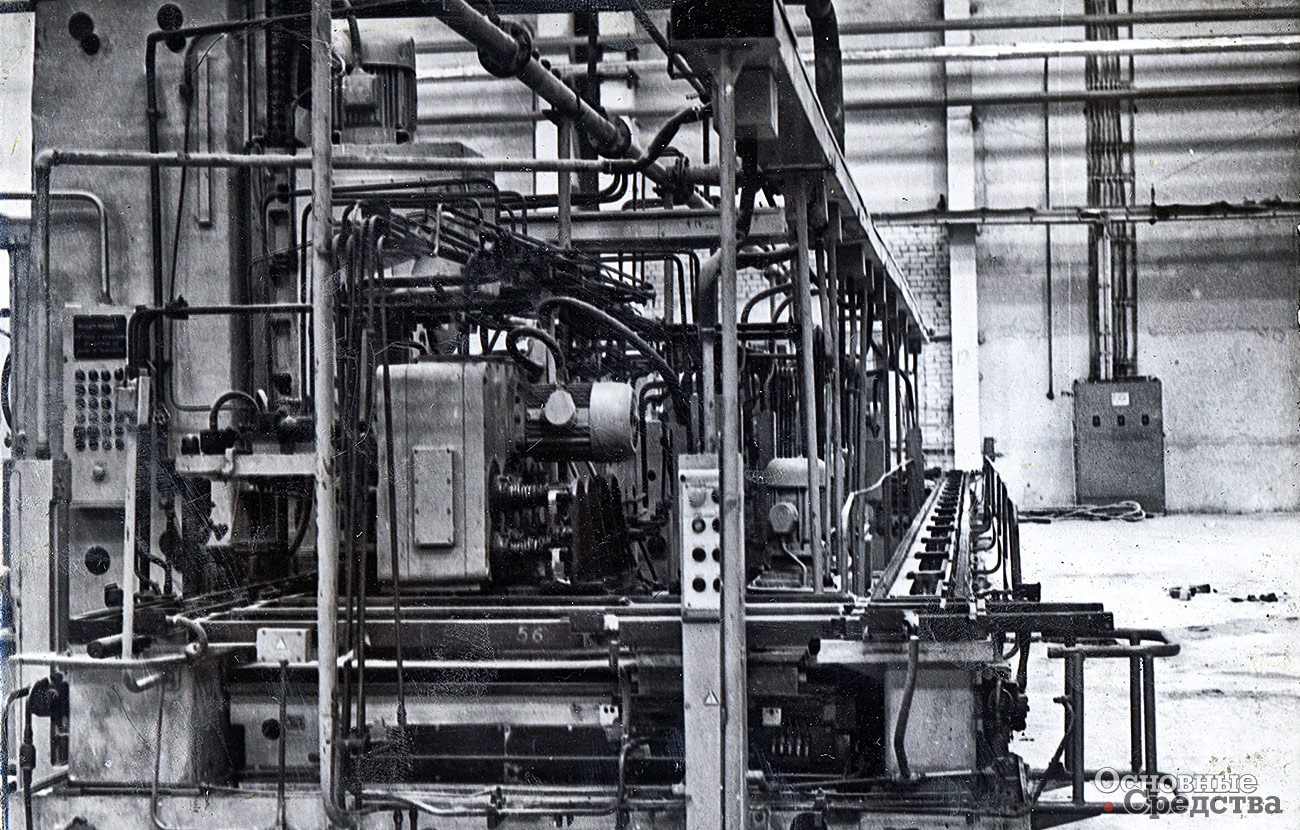
В дальнейшем проектирование и изготовление автоматических линий для БАЗа было передано Московскому заводу агрегатных станков и автоматических линий «Станкоагрегат». Считаю необходимым отметить один неприятный момент: завод «Станкоагрегат» не справился с планом, не изготовил часть автоматических линий и обратился с просьбой к руководству нашего завода пролонгировать договор на следующий год. Руководство БАЗа после консультаций с Управлением оборудования Минавтопрома в этой просьбе отказало. Станкозавод, в свою очередь, отказался изготавливать автоматические линии. И закрутилась «бюрократическая» карусель! Вот так непродуманные решения приводят к трудно решаемым проблемам завода. Кто же будет изготавливать продукцию при отсутствии договора на ее изготовление и поставку? С помощью Минавтопрома нам удалось добиться совещания в Госплане СССР с участием представителей станкозавода. Я вместе с В.И. Коляновым, главным инженером автоагрегатного производства, в Госплане отстаивал интересы нашего завода. В результате Госплан обязал завод «Станкоагрегат» линии изготовить. Мне пришлось выехать в Москву, на завод «Станкоагрегат», и участвовать в составлении договоров.
Кстати, когда был изготовлен комплекс линий 1Л355, 1Л356А, 1Л356Б для обработки башмака рессоры, мне с В.И. Коляновым пришлось выехать в Москву и принимать комплекс у станкозавода. А дело было так. По вызову Московского завода «Станкоагрегат» БАЗ направил группу наладчиков для приемки комплекса автоматических линий. И вдруг утром на другой день на БАЗ приехал на машине начальник планово-экономического отдела станкозавода А.А. Шебершнёв с известием, что наладчики БАЗа отказываются принимать автоматические линии. Тут же руководство БАЗа приняло решение командировать на станкозавод главного инженера автоагрегатного производства В.И. Колянова. Поскольку я занимался всеми вопросами по подготовке заданий на проектирование автоматических линий, определял необходимые площади и место их установки, согласовывал компоновку, то тоже решил поехать на станкозавод.
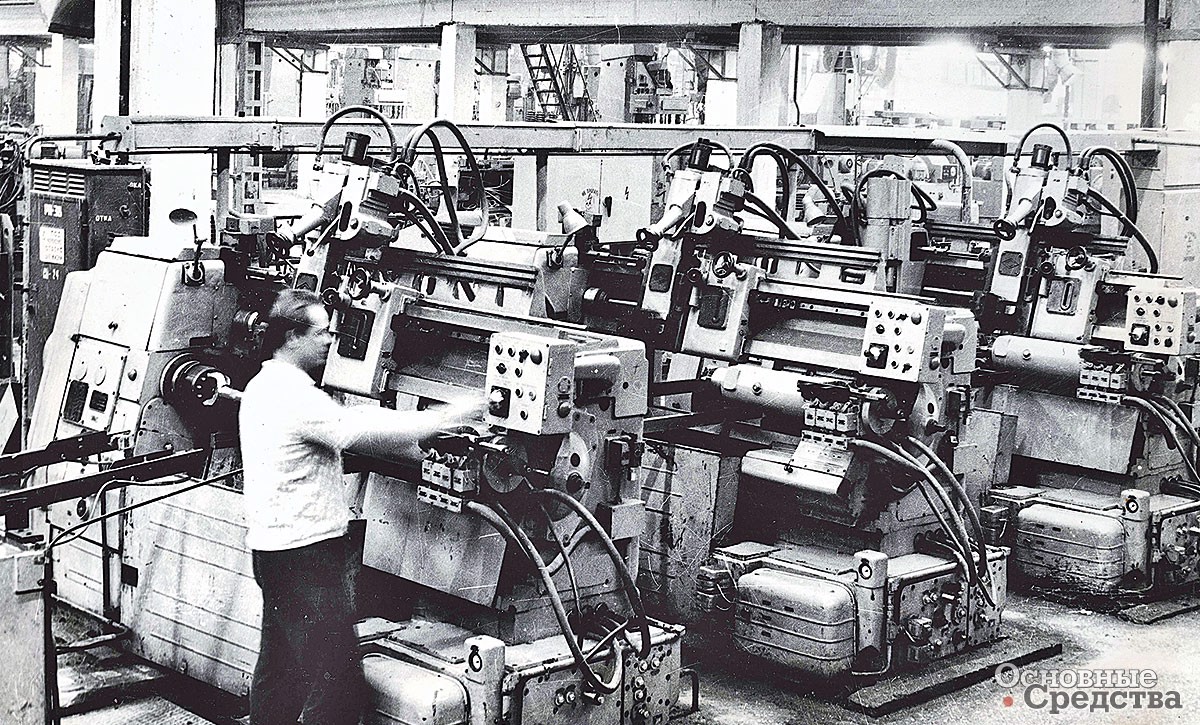
В.И. Колянов поехал вместе с А.А. Шебершнёвым на его машине, а я поездом. Утром встретились на станкозаводе – и что мы увидели? Комплекс линий был весь залит маслом и эмульсией – грязь непролазная. Первым делом мы запретили наладчикам даже подходить к линиям, пока завод не приведет их в порядок. А затем стали разбираться, в чем дело. Оказалось, что несколько стоек, на которые крепились шинные сборки, были установлены не совсем удачно и затрудняли подход к станкам и их обслуживание. Вместе с заместителем начальника СКБ С.И. Моштаковым мы определили места их установки, и тут нужно отдать должное станкозаводу: очень оперативно автоматические линии были приведены в порядок, стойки переставлены, и автоматические линии пустили в работу. Они стабильно проработали первую и вторую смены, без отказов и сбоев, показали нужную производительность и качество. Где-то часов в 11 вечера мы с В.И. Коляновым подписали документы о приемке автоматических линий. Хочу отметить, что вместе с заводчанами принимал участие в сдаче автоматических линий начальник ВПО «Союзстанколиния» Минстанкопрома В.Г. Витюгов. Я с ним был в хороших отношениях. Так вот, когда нам с В.И. Коляновым принесли из столовой обычный ужин: первое, второе и компот, и мы положили по 1 рублю на стол, В.Г. Витюгов сказал: «Завод еще не научился сдавать линии».
Необходимо сказать несколько слов о начальнике СКБ при Московском заводе «Станкоагрегат» В.С. Кутаренкове и его заместителе С.И. Моштакове, о главном конструкторе автоматических линий Г.М. Козак, А.И. Жице и других специалистах. Все они были грамотными инженерами, хорошо знавшими технику и технологию. Мне довелось очень плотно с ними работать при заказе десяти автоматических линий: для башмака рессоры – 1Л355, 1Л356А, 1Л356Б; картеров редукторов переднего, среднего и заднего мостов – 1Л340А, 1Л340Б, 1Л341А, 1Л341Б; кронштейнов балансирной подвески – 1Л357, 1Л358; цапфы – 1Л354; согласовывать компоновочные решения, технологию обработки и другие вопросы.
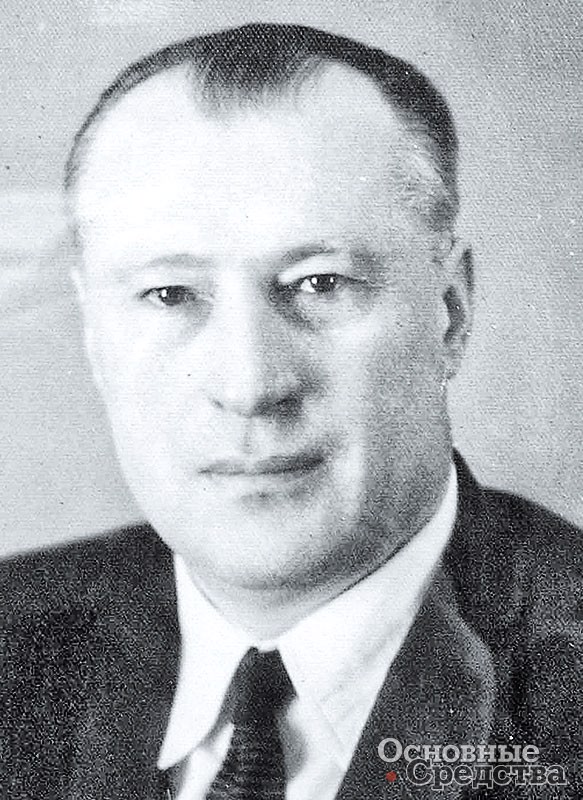
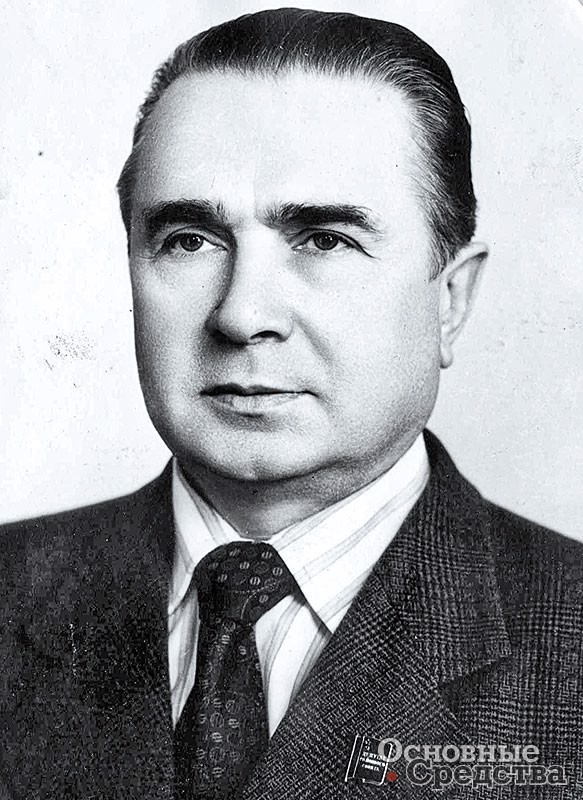
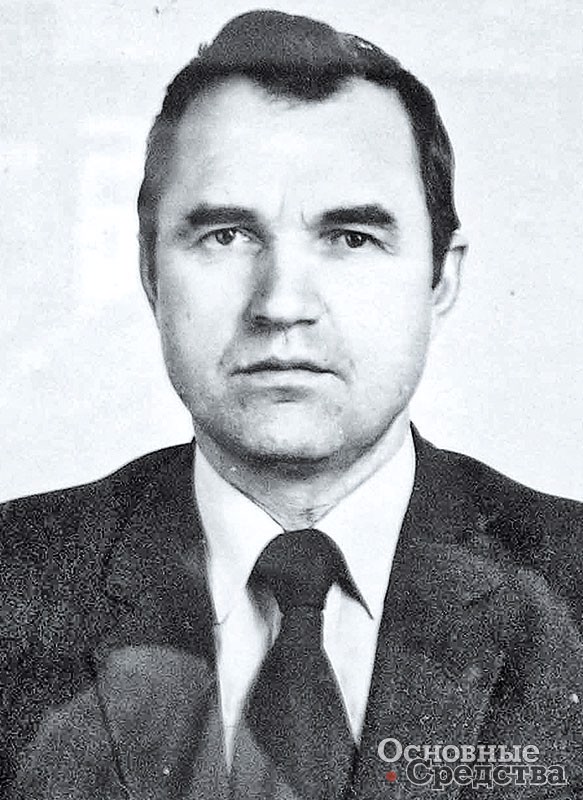
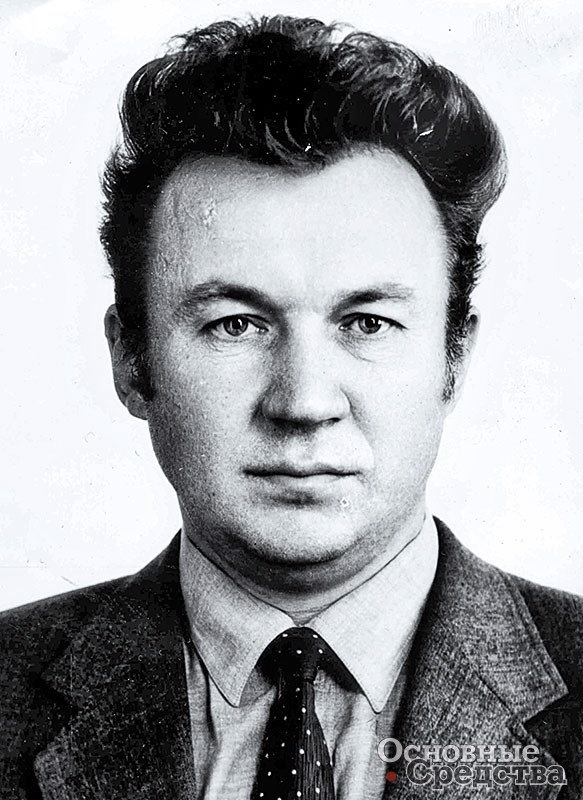
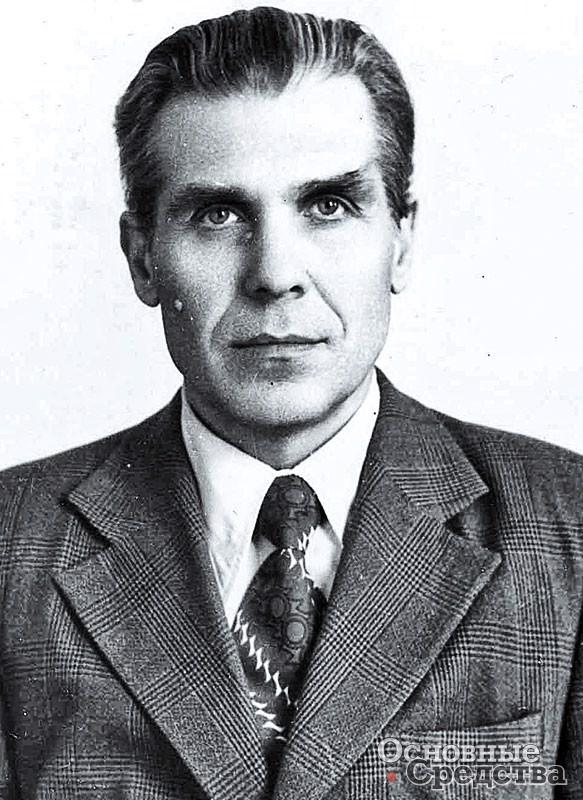
В этих линиях были заложены прогрессивные технологические и технические разработки, дающие высокое качество изготовления деталей и необходимую производительность, что явилось одним из факторов, обеспечивающим уверенную и стабильную работу автоагрегатного производства, и позволило выйти на проектную мощность по выпуску 55 тысяч комплектов агрегатов к автомобилям ЗИЛ-131.
Много сил и энергии в развитие и становление автоагрегатного производства вложили директоры завода – П.Я. Петраков, К.К. Ярошевич, В.Х. Чекулаев, Ф.С. Борисов, И.Н. Лештан, В.Б. Самарин, В.И. Гросс; главные инженеры – И.Н. Лештан, И.Ф. Ковалёв, А.В. Главинский; управляющие производством – В.С. Титов, В.М. Старкин; директор производства – В.Н. Пономарёв, главные инженеры производства – И.Е. Зуев, В.Н. Пищиков.
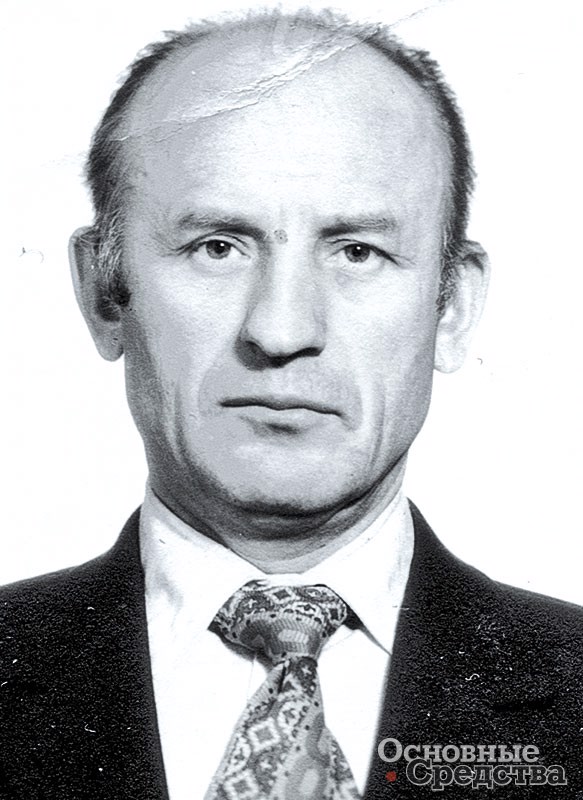
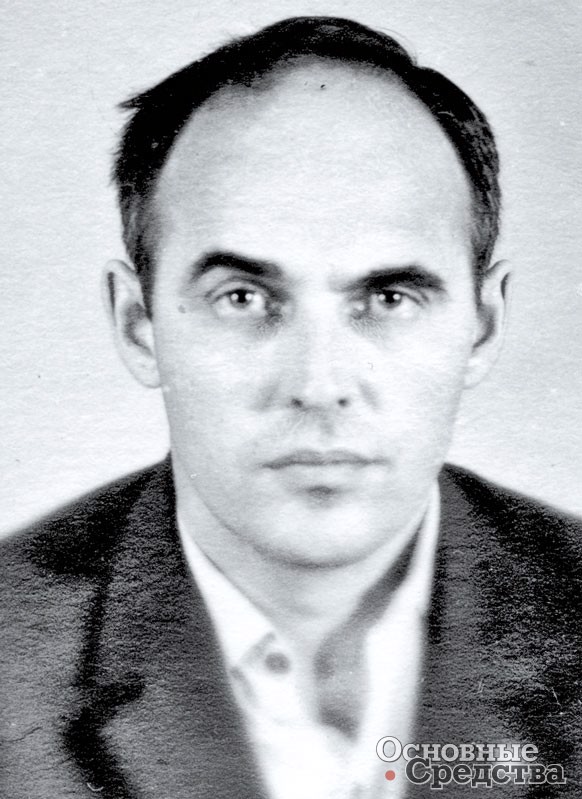
Нужно отметить директора автоагрегатного производства В.Н. Пономарёва и его главного инженера В.Н. Пищикова как грамотных инженеров, ответственных руководителей, опытных организаторов. Под их многолетним руководством были завершены намеченные мероприятия по развитию производства, освоены производственные мощности, и ряд лет автоагрегатное производство изготавливало и поставляло МосАвтоЗиЛу более 55 тысяч комплектов агрегатов к автомобилям ЗИЛ-131, что составляло свыше 60% объема продукции Брянского автомобильного завода.
В.Н. Пономарёв руководил автоагрегатным производством с 1980 г. в течение 15 лет. За годы его деятельности была проведена большая работа по реконструкции, автоматизации и механизации производства, совершенствованию передовых методов организации труда и управления производством, внедрению хозяйственного расчета. Постоянно выполнялись задания по росту производительности труда, снижению себестоимости выпускаемой продукции, сокращению численности работающего персонала. Автоагрегатное производство неоднократно занимало призовые места в заводском социалистическом соревновании.
В.Н. Пономарёв был награжден орденом Трудового Красного Знамени, медалью «За трудовое отличие», юбилейной медалью «За доблестный труд» в ознаменование 100-летия со дня рождения В. И. Ленина.
Было создано высокомеханизированное и автоматизированное массовое производство основных узлов и агрегатов для автомобилей высокой проходимости ЗИЛ-131. Производство было оснащено самым современным оборудованием – специальными и агрегатными станками, автоматическими линиями. Сборка узлов и агрегатов осуществлялась на сборочных конвейерах. На высоком техническом уровне были решены вопросы межоперационной транспортировки деталей, работали системы сбора и уборки стружки с применением отдельных конвейеров для стальной и чугунной стружки.

Эпилог
Автоагрегатному производству по выпуску ведущих мостов к тяжелым грузовым автомобилям, таким как ЗИЛ-131, не было равных заводов в Европе. Это было именно массовое производство, темп выпуска мостов и деталей был очень высоким, так, например, темп выпуска сателлита дифференциала составлял всего 22 секунды. За одну смену изготавливали более трехсот мостов.
Я перешел на Брянский автомобильный завод в апреле 1960 г. в отдел Главного технолога, в технологическое бюро цеха № 320 – цех трансмиссий трактора Т-140 инженером-технологом и ушел с завода в мае 1995 г., когда предприятие переживало не лучшие времена, а автоагрегатное производство дышало на ладан в связи с прекращением выпуска автомобилей ЗИЛ-131 на Заводе им. Лихачёва. Я отдал Брянскому автомобильному заводу лучшие годы своей жизни – 35 лет!
Я мечтал, что на заводе будет династия Буненковых: после окончания Брянского института транспортного машиностроения в 1983 г. на завод пришли мой сын С.Н. Буненков и его жена А.М. Буненкова. Сын работал в отделе технического обеспечения и обслуживания станков с ЧПУ (ОТООС ЧПУ) наладчиком станков с ЧПУ и обрабатывающих центров, затем – начальником технологического бюро в производстве серийных автомобилей. В связи с угасанием завода перешел на другое предприятие в 1994 г.
Его жена А.М. Буненкова проработала в конструкторском бюро мерительных инструментов и контрольных приспособлений (КБМИ) ОГТ 18 лет и в 2001 г. перешла на Брянский машиностроительный завод.
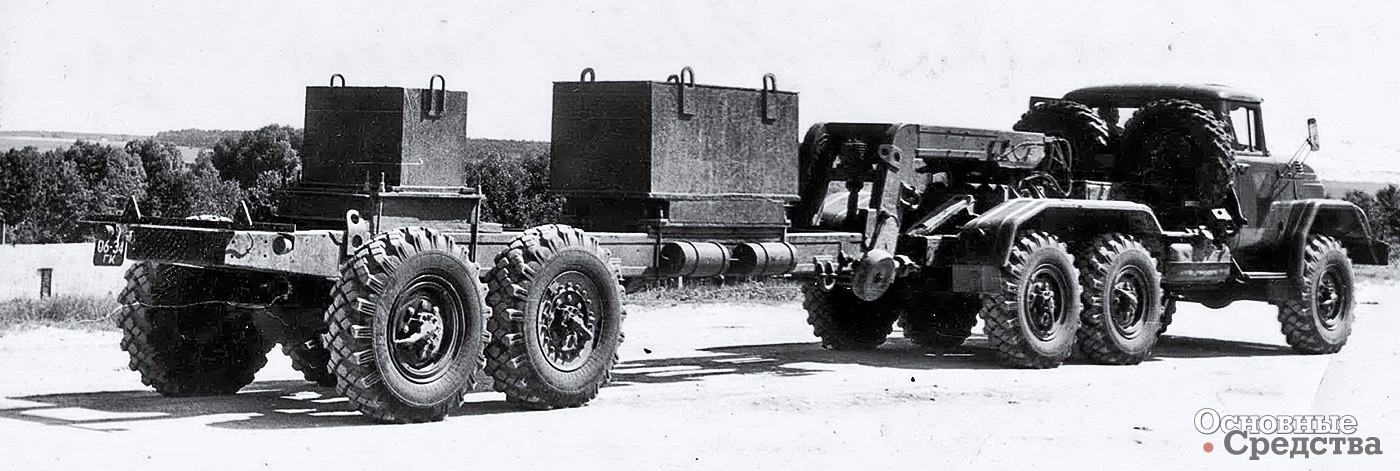
На автозаводе в 2008 г. проходила преддипломную практику моя внучка Марина Буненкова и защитила диплом по теме о Брянском автомобильном заводе.
С развалом СССР всё изменилось. Мечты многих людей не сбылись...
Но я горжусь тем, что в развитие и становление Брянского автомобильного завода, и особенно в автоагрегатное производство, вложена частичка и моего труда, частичка моей души.