
Семинар Caterpillar «Эффективные технологии дорожного строительства»
3 апреля компания Caterpillar провела в Сочи ставший уже традиционным ежегодный семинар «Эффективные технологии дорожного строительства 2017». Основная цель мероприятия — способствовать распространению среди дорожников прогрессивных технологий и оборудования для строительства и ремонта дорог.
Вниманию многочисленных гостей-профессионалов дорожной отрасли и представителей специализированных СМИ были предложены новинки оборудования Caterpilar, высокопроизводительные методы непрерывной укладки асфальтобетонной смеси с применением электронной телематической аппаратуры и другие инновационные решения.
Дорожная фреза Cat PM620
В течение 2016-17 гг. практически в два раза увеличилась линейка техники Caterpillar. Из этих новинок на семинаре была представлена первая на территории Евразии холодная фреза мод. Cat PM620, способная фрезеровать асфальтовые и бетонные покрытия на полную глубину за один проход. Поставки этой машины в регионы РФ начались с конца 2016 г. У Caterpillar изменились наименования фрез: раньше в наименование входила ширина фрезерования, а теперь входит мощность двигателя - «620» означает мощность свыше 600 л.с.

В кабине расположены сдвоенные органы управления. В ассортимент опций входят сиденья с подвеской и навес с гидравлическим приводом. Оператор может быстро выдвигать и складывать навес, не прерывая работу. Навес может быть оснащен дополнительным передним и задним стеклами, которые обеспечивают защиту по всей ширине рабочего места оператора. Если что-то мешает сверху, крышу кабины можно опустить — теперь не на платформу оператора, а впереди на водяной бак, так она не мешает работе.
Двигатель турбированный, с электронным управлением, такой же, как у фрезы предыдущего поколения, но существенно модернизирован. Частота вращения вентилятора системы охлаждения регулируется в зависимости от потребности. У конкурирующих машин могут быть двигатели подобной мощности, но преимуществом фрезы Caterpillar является электронное согласование мощности двигателя, скорости хода и частоты вращения ротора, в результате обеспечивается повышенная производительность РМ620.
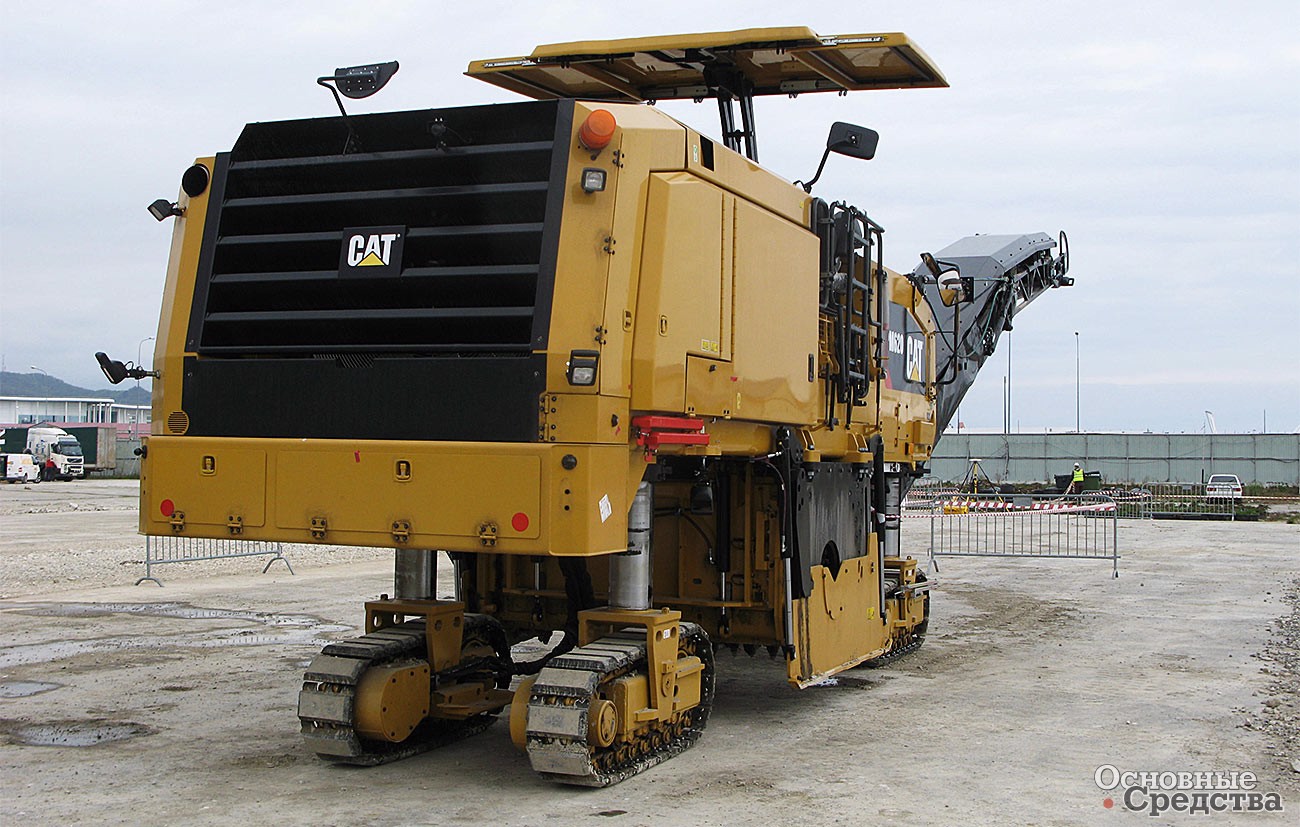
Фреза имеет кардинально новое управление, которое полностью разработано специалистами компании Caterpillar. PM620 оснащена многофункциональными сенсорными дисплеями. Информация на экране хорошо видна как днем, так и ночью, а кнопки снабжены подсветкой для удобства работы при плохом освещении. Панель управления влагонепроницаемая. Кнопки рассчитаны на 1 млн нажатий. На машине может быть установлено до 5-ти дисплеев: 1-2 дисплея располагаются на машине сверху и 3 — по желанию владельца в удобных местах. Дисплеи выполняют также роль пульта управления системой нивелирования (эта система разработана при участии Caterpillar). Полностью интегрированная в конструкцию машины система нивелирования Grade and Slope Control в форме 2D или 3D может выводить показания на любой монитор на площадке оператора или мониторы оператора на земле. Тот, что находится на земле, также видит все параметры машины и управляет фрезой: контролирует ее заглубление и поперечный уклон. Доступны все функции управления конвейером. На экран выводится информация о работе машины, не только от системы нивелирования, можно отрегулировать давление на заднюю створку и др. функции и можно управлять со всех экранов — раньше с нижних этого нельзя было делать. Таким образом второй оператор, находящийся на земле, может управлять процессом нивелирования, исправить ошибку первого.
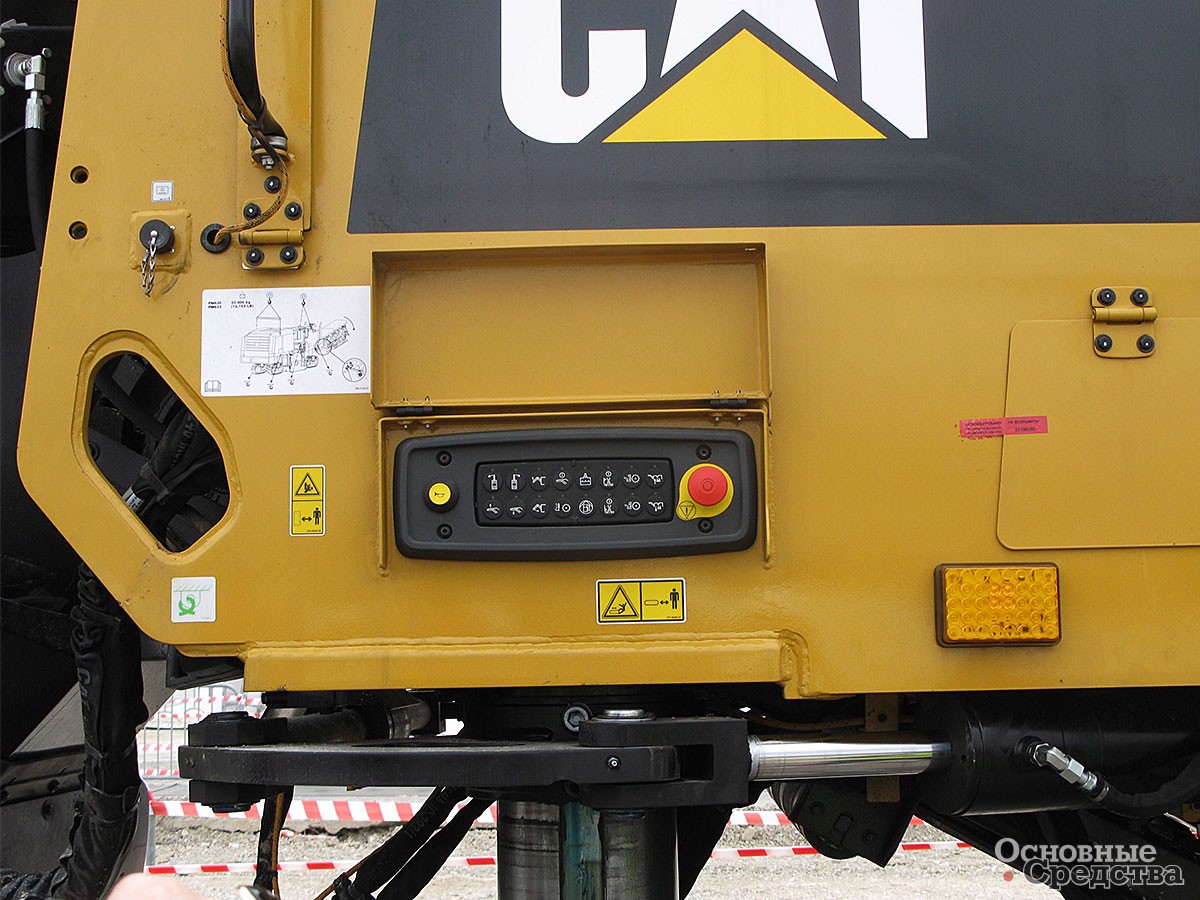
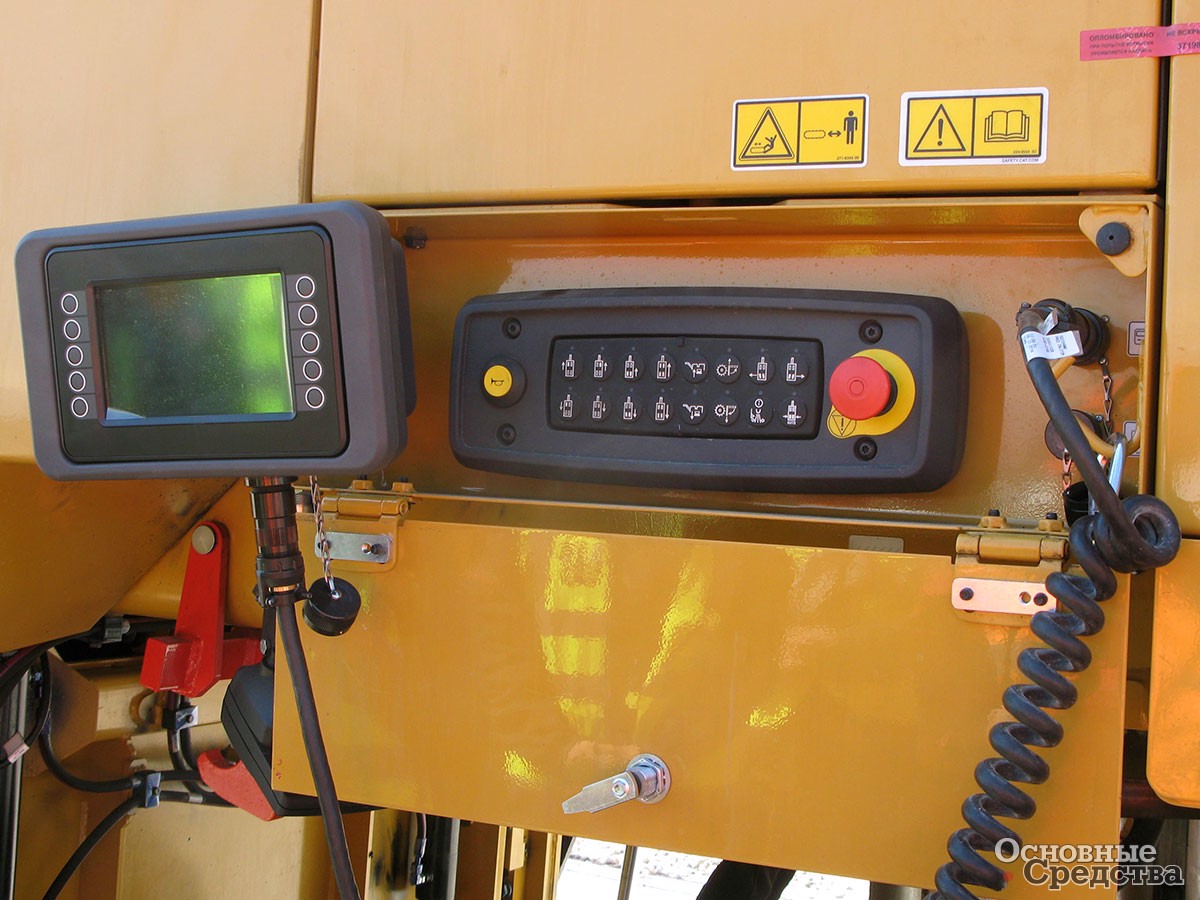
Появились новые функции управления — в т. ч. «переезд препятствий» при фрезеровании Jump Hold. Раньше нужно было выключить систему нивелирования, поднять машину, переехать препятствие, опять включить систему нивелирования. Сейчас все это выполняется нажатием 2-3 кнопок. «Поднять машину» - система нивелирования автоматически выключается. После проезда препятствия снова нажимается кнопка — и машина возвращается на позицию непосредственно перед поверхностью и запрашивает оператора, хочет ли он вернуться к фрезерованию. После подтверждения система нивелирования включается и машина автоматически возвращается к прежнему режиму фрезерования.
Одна из полезных опций системы нивелирования — плавный автоматический вход/выход в режим при фрезеровании. Глубина фрезерования и на какой дистанции нужно врезаться вводится в параметры фрезерования. Дальше, машина выполнит врезку автоматически. То же самое при выходе из фрезерования.
С помощью комбинации датчиков можно настроить машину, чтобы она регулировала нивелирование по обеим сторонам или с одной стороны и уклон с другой. Ультразвуковые датчики обеспечивают постоянную точность ± 3 мм.
Теперь у фрезы нет руля, бесступенчатое управление скоростью и изменение направления движения осуществляется джойстиком. Конструкция рулевого управления (система True-track) обеспечивает изменение углов схождения гусеничных тележек в зависимости от радиуса поворота и движение гусеничных тележек в поворотах по независимым траекториям. Левая и правая гусеничные тележки соединяются рулевой тягой с гидроцилиндром, оснащенным датчиком положения, гидроцилиндр изменяет длину рулевой тяги и схождение гусениц — от параллельного положения до различных углов схождения в зависимости от выполненного маневра. В результате при движении в повороте каждая гусеничная тележка всегда движется перпендикулярно радиусу поворота, исключаются боковые нагрузки на ходовую часть, износ гусениц уменьшается, машина движется плавно, радиус поворота самый малый среди машин данного класса, снижается нагрузка на двигатель и расход топлива. На фрезах предыдущих поколений этой системы не было и при выключении режима фрезерования и включении крабового хода машина буквально «прыгала», т. к. ходовая часть обеспечивала нормальное плавное движение при фрезеровании, а остальные режимы движения (в т.ч. крабовый ход) считались вспомогательными и на них особого внимания не обращали. В результате эти режимы приводили к большому износу ходовой части. Теперь новая фреза движется плавно во всех режимах за счет изменения кинематики. Электронный блок обеспечивает 4 режима рулевого управления и автоматически выравнивает задние гусеницы по центру при выборе режима рулевого управления, в котором используются только передние гусеницы.



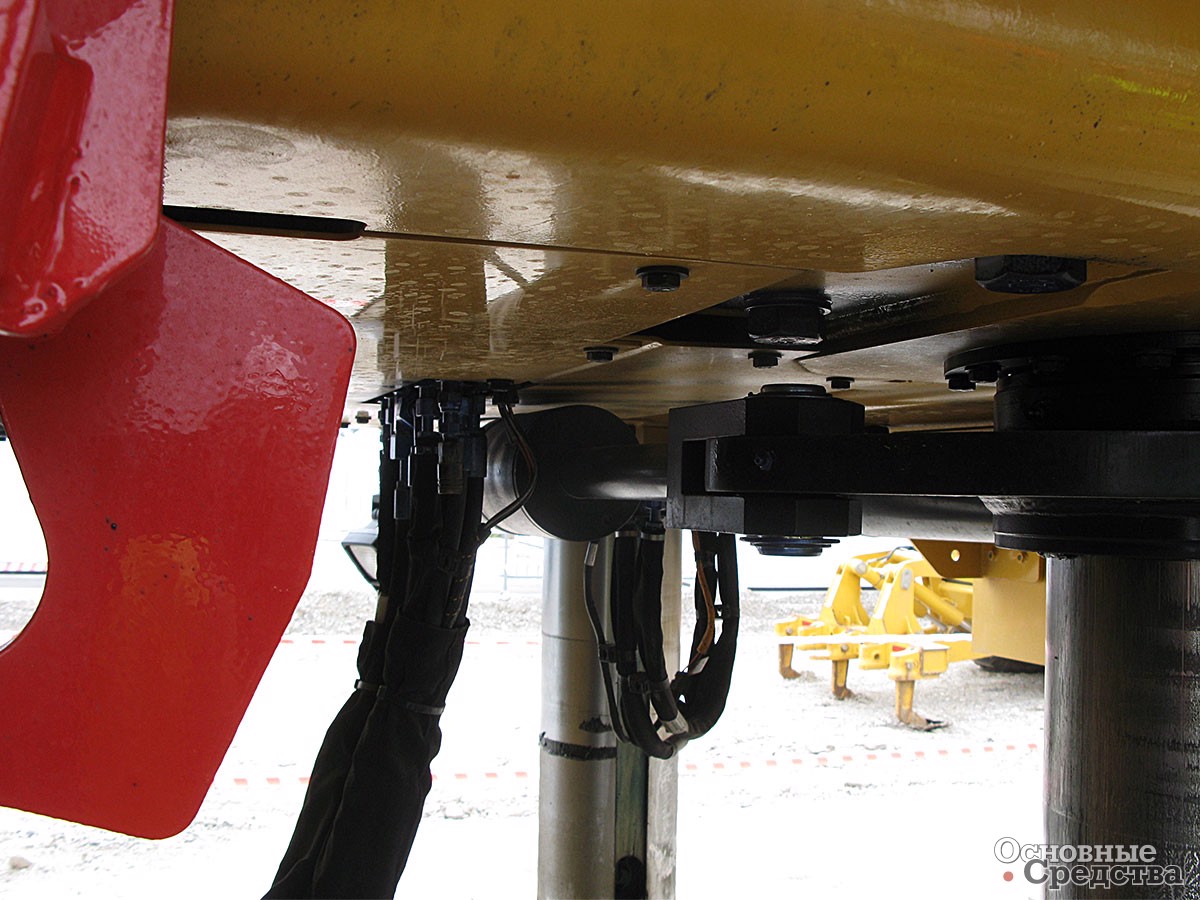
Впервые в данной машине реализован привод из двух независимых контуров типа «два гидронасоса, 4 гидромотора». Аналогов в данном классе ему нет. Каждый аксиально-поршневой насос переменной производительности питает два гидромотора, расположенных по диагонали, т. е. один гидронасос приводит заднюю правую и переднюю левую гусеницы, второй — остальные две. Это очень эффективная реализация привода хода. Система имеет сложное электронное управление. На каждой гусенице стоит датчик скорости и в каждом контуре — по датчику давления (всего — 2), это дает возможность оптимизировать работу ходовой части, контролировать тягово-сцепные характеристики и обеспечивать управление тяговым усилием на гусеницах не только по разнице скоростей. При потере сцепления, пробуксовке какой-либо из гусениц система регулирует тяговое усилие, изменяя производительность как гидромотора, так и гидронасоса. У конкурирующих моделей в системе хода как правило один гидронасос питает 4 гидромотора. Машина оснащена системой автоматического контроля скорости хода, своеобразным круиз-контролем, которая позволяет задавать рабочую скорость для обеспечения стабильного фрезерования, это облегчает работу оператора. Конструкция гусеничных тележек выполнена на основе тележек бульдозера Cat D3. Гусеницы имеют функцию автоматического натяжения.
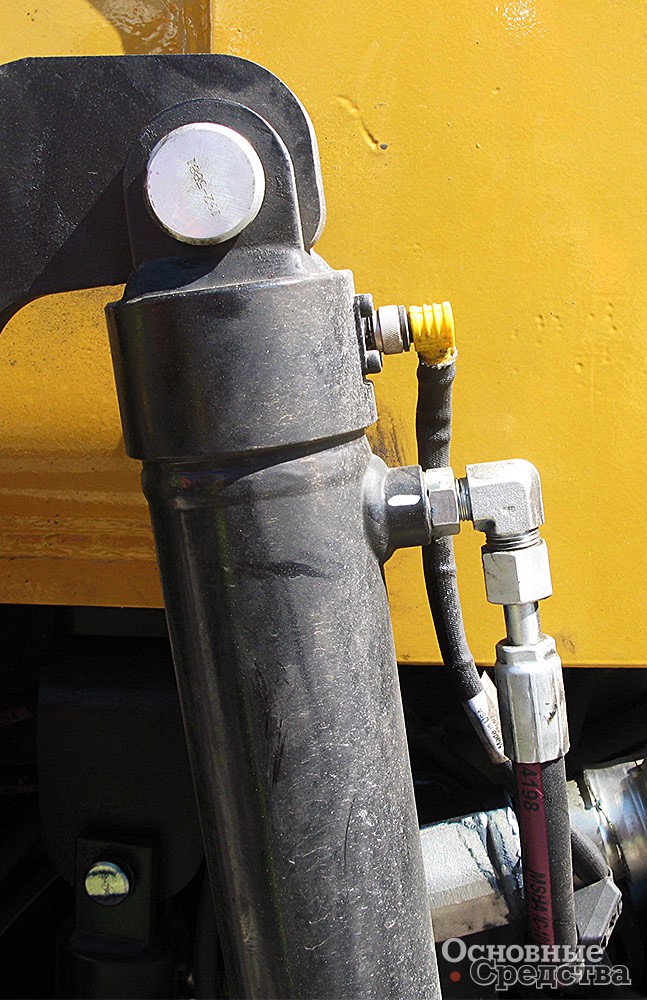
Одна из новинок в конструкции машины — датчики продольного уклона расположены в гидравлических цилиндрах подъёма боковых щитов, используемых в качестве лыжи, по которым измеряется глубина фрезерования. Тросовые датчики теперь не используются, т.к. с ними постоянно были проблемы, точность их не всегда устраивала, трос часто повреждался в ходе работы, когда его задевали инструментом, при обрыве трос втягивался в корпус датчика и приходилось датчик заменять. Теперь в гидроцилиндрах боковых щек (створок) фрезы (которые зачастую является элементом системы нивелирования) стоят надежные датчики положения. Цифровой датчик поперечного профиля помогает с высокой точностью поддерживать заданный профиль фрезерования при работе совместно с одним из боковых щитов. Система может быть расширена дополнительными ультразвуковыми датчиками – большой ультразвуковой лыжей, а также дополнительным механическим датчиком в зоне работы фрезерного ротора. Эти датчики являются элементами системы нивелирования, они калибруются один раз и больше не нуждаются в калибровке. Новые датчики положения надежны при условии своевременного проведения техобслуживания, если вовремя меняется гидравлическая жидкость (каждые 3000 моточасов).
В конструкции машины теперь нет ни одной механической шкалы уровня. Раньше были шкалы на задних лапах (стойках) и на боковых щеках, которые нужно было выставлять при фрезеровании. Теперь всё выполняется при помощи электронного управления и высокочувствительных датчиков, имеется функция автоматического выравнивания, обеспечивающая плавную регулировку высоты, выполняющуюся в один прием. У фрезы запрограммировано несколько положений, при которых она останавливается: если оператор нажимает кнопку «опускание фрезы вниз» - она опустится на 4-х лапах и остановится на расстоянии 2 см от поверхности покрытия в положении начала фрезерования. После этого оператору достаточно ввести только необходимые параметры в систему нивелирования, фреза на всех 4-х лапах автоматически опускается и заглубляется. После того, как задние лапы входят в зону, где покрытие уже сфрезеровано, система выставит лапы автоматически, обеспечивая правильное положение фрезы, работа оператора сведена к минимуму. Задача оператора- только контролировать направление движения и правильно выставить параметры системы нивелирования.
На данной машине установлен усиленный ротор специальной конструкции, которая способствует увеличению срока службы резцов до 30 – 40 м2 в расчете на 1 резец. Доступно три скорости фрезерования. На ротор могут устанавливаться алмазные резцы. Caterpillar — единственная компания, которая предлагает алмазные резцы на полную глубину фрезерования. Существуют аналоги, но у них ограничена глубина фрезерования. Ходимость алмазного резца в 40-50 раз больше обычного карбидного, его хватает на весь сезон, заменять не нужно. Как известно, корректировка системы нивелирования производится на величину износа зубьев, в ходе работы они изнашиваются на величину до 8-10 мм. Если используются алмазные зубья, никакой корректировки не требуется.

Применяются уникальные быстросменные конические резцедержатели, они не требует никаких болтов крепления и уплотнений — резцедержатель просто вставляется в базу и забивается молотком. Такая конструкция упрощает смену резцов (если эксплуатация проводится правильно резец легко освобождается из крепления, когда необходимо), обеспечивает правильное вращение резца, тем самым продлевая срок его службы и улучшая характеристики фрезерования, обеспечивает защиту ротора и его привода. Предлагается опционная система отведения и подавления пыли от ротора. Разрежение засасывает пыль из сборного конвейера и переходной зоны между сборным и погрузочным конвейерами. Пыль выталкивается через погрузочный конвейер вместе с выгружаемым материалом. По заказу может быть установлена дополнительная видеокамера, помогающая оператору наблюдать за работой ротора и замечать препятствия. Опыт эксплуатации показал: при работе видеокамера не засоряется пылью.
Еще одна особенность конструкции РМ620: между задними гусеницами расстояние меньше, чем между передними. На фрезах предыдущего поколения и у конкурентов между передними и задними гусеницами расстояние одинаковое. Это неудобно — задние гусеницы идут по сфрезерованному материалу и находятся недалеко от кромки сфрезерованного материала. При поворотах гусеницы касаются этой кромки, что приводит к повышенному износу гусениц. У новой фрезы задние гусеницы установлены гораздо уже, при поворотах не касаются кромок сфрезерованного материала. На устойчивости машины это практически не отразилось. Поддерживать корпус машины параллельно поверхности в транспортном режиме помогает функция Ride Control.

Для работы фрезы требуется много воды, чтобы охлаждать ротор. Бак машины вмещает 3 т воды, но при работе каждые 30-40 мин его приходится дозаправлять. Поэтому у новой фрезы увеличено количество заправочных горловин — сверху, сзади и т. д. Установлена дополнительная водяная помпа, которая позволяет закачивать воду из водоема.
Эксплуатационная масса, кг | 33 330 |
Транспортировочная масса, кг | 29 400 |
Мощность двигателя (брутто) кВт (л.с.) | 470 (630) |
Ширина фрезерования (номинальная), мм | 2010 (2000-2200) |
Количество резцов | 178 |
Максимальная глубина фрезерования, мм | 330 |
Частота вращения ротора, об/мин | 100/109/118 |
Минимальный внутренний рабочий радиус поворота, мм | 2000 |
Гусеничные тележки, длина/ширина, мм | 1788/305 |
Рабочая скорость, м/мин | 100 |
Максимальная транспортная скорость, км/ч | 5,9 |
Чтобы увеличить универсальность машины изменили конструкцию конвейера. Раньше он складывался вверх, теперь складывается вниз. Это удобно для работы в туннелях — вверх сложить конвейер в туннеле невозможно. К тому же упрощена кинематика конвейера, теперь он управляется одним гидроцилиндром. Раньше было 2 гидроцилиндра, они должны были работать в определенном порядке. Оператор и снизу, и сверху может управлять конвейером: складывать, поворачивать вправо-влево, контролировать весь процесс загрузки самосвалов. Есть полезная опция — перевод конвейера кратковременно на увеличенную скорость: если расстояние между фрезой и самосвалом увеличилось (не уследил водитель самосвала) и материал начинает просыпаться с конвейера на землю, оператор нажимая кнопку включает повышенную на 50% скорость и материал начинает лететь дальше с конвейера — в кузов. Оператор отпускает кнопку — и конвейер возвращается к прежней скорости. В случае ожидания подачи следующего грузовика оператор может нажатием одной кнопки «Пауза» приостановить все ходовые и рабочие функции машины, при этом двигатель перейдет в режим холостого хода. При повторном нажатии машина вернётся к фрезерованию с плавным набором скорости до рабочей величины.

Еще особенность конструкции: ширина подборочного конвейера сейчас увеличена, составляет 850 мм. Скорость конвейера регулируется, как и раньше, но теперь это делается не потенциометром, а кнопками, это намного проще. Предлагается опционная система регулировки натяжения ленты конвейера при помощи гидроцилиндра, а не регулировочного винта. Система распыления воды оснащена тройной фильтрацией и комплектом оборудования для эксплуатации зимой, которая предоставляет возможность с легкостью продуть линию подачи воды сжатым воздухом. Есть вывод-порт для подключения пневмоинструмента для обработки ротора.
Дорожные фрезы Cat оснащаются резервной системой вспомогательного гидропривода с электрическим насосом, которая может поддерживать минимально необходимую функциональность машины (для её буксировки из рабочей зоны) даже в случае остановки основного двигателя. Это повышает безопасность работы и снижает риск простоев на строительном объекте.
Компания Caterpillar планирует в 2017-2018 гг. представить на российском рынке полностью обновленный и значительно расширенный модельный ряд дорожных фрез с учетом современных технологических требований к этому виду оборудования.
Асфальтоукладчик Cat AP655F
На семинаре был представлен первый в России гусеничный асфальтоукладчик Cat AP655 нового поколения F высокой производительности, предназначенный для работы на взлетно-посадочных полосах, автомагистралях, шоссе и других крупных объектах.
Асфальтоукладчик оснащен новым двигателем Caterpillar мощностью около 200 л.с. с электронной системой управления. Топливная экономичность двигателя улучшена на 5% по отношению к предыдущей серии и на 20% - по отношению к некоторым моделям других производителей. При включении автоматического управления частотой вращения коленчатого вала двигателя данная частота снижается до оборотов холостого хода 1000 об/мин, когда рычаг перемещается в нейтральное положение, или до 1300 об/мин при включенном нагреве вибробруса.



Система охлаждения оснащена вентилятором с гидроприводом, частота вращения вентилятора регулируется электронным управлением в зависимости от потребности. Система располагается вверху подкапотного пространства и эффективно отводит тепло из моторного отсека, с операторской платформы, а также от мест нахождения работников бригады по бокам машины. Выброс отведенного тепла осуществляется по направлению бункера асфальтоукладчика.
На платформе оператора имеется два взаимозаменяемых рабочих места, которые могут выдвигаться за пределы рамы для улучшения обзора. Все четыре панели управления: две на платформе оператора, две на плите, - имеют ударопрочное, пылевлагозащищенное исполнение. Любой пульт с цветным сенсорным монитором позволяет управлять и подачей материала (регулировать скорость конвейера), и системой нивелирования Cat Grade&Slope Control, и подогревом плиты (на пульте показывается температура), отслеживать показания системы диагностики. Кнопки управления подсвеченные, с ресурсом в 1 млн. нажатий. Команды на пульте переведены на русский язык.
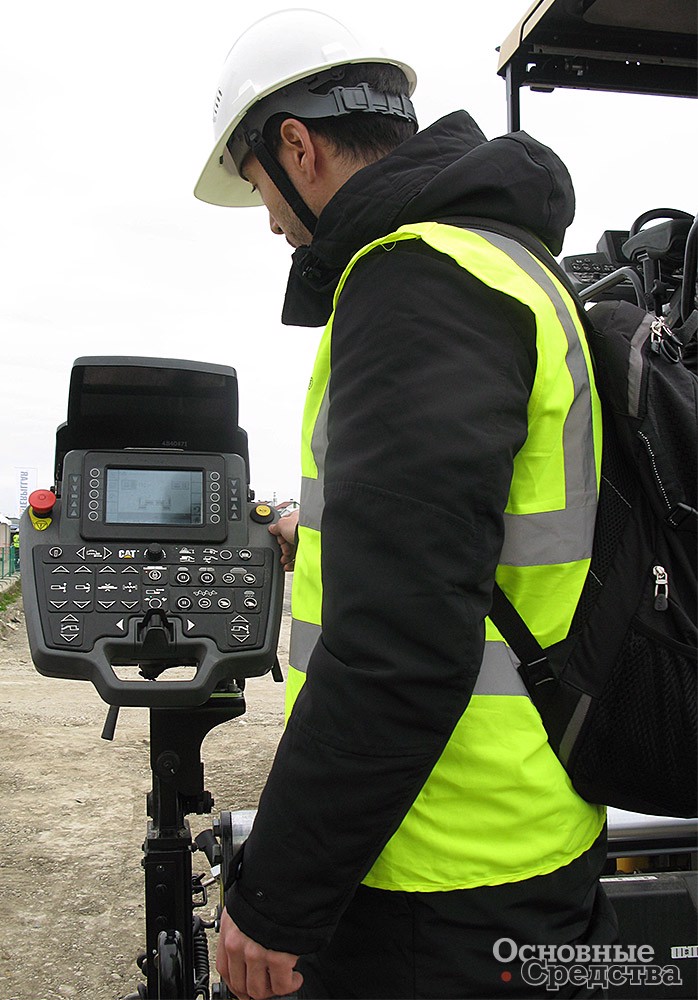
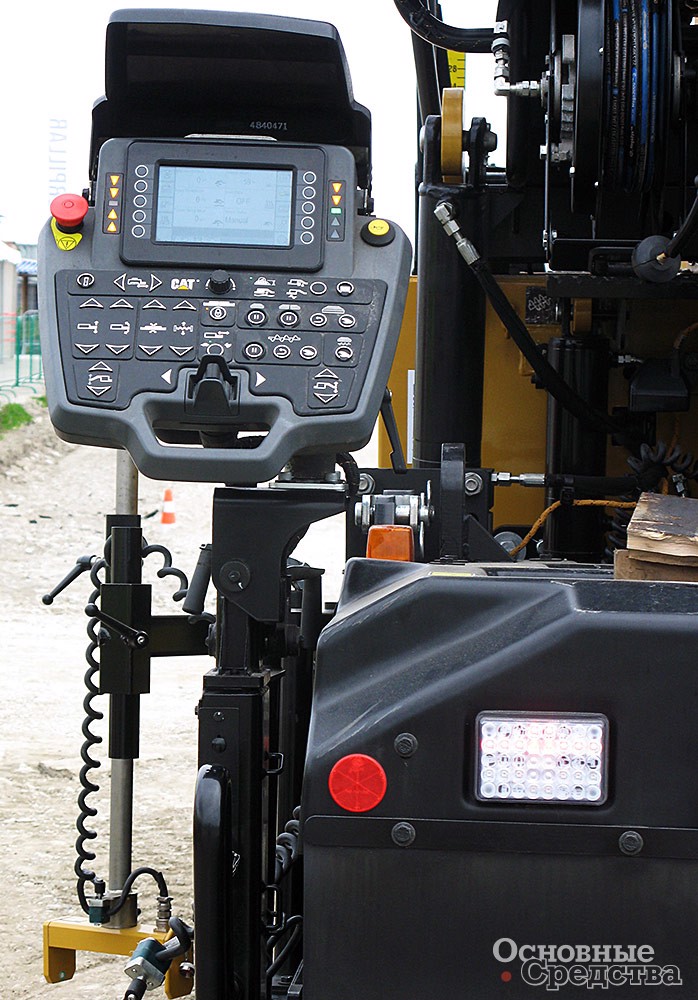
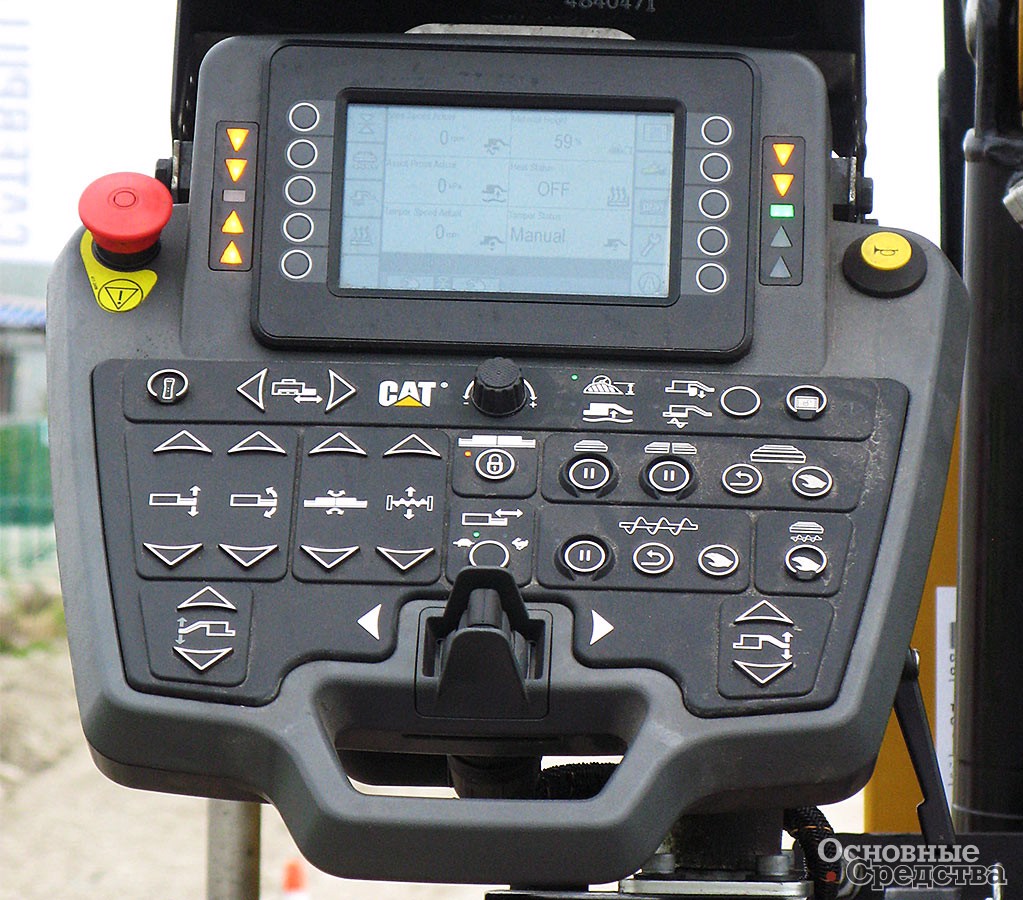
Асфальтоукладчик имеет интегрированную систему нивелирования, которая может строиться как на основе контактных датчиков, так и ультразвуковых датчиков продольного уклона, работающих совместно с цифровым датчиком поперечного профиля. В качестве опции также доступна система на основе лазерного сканирования и система 3D.
Система управления машиной в стандартной комплектации имеет автоматические функции заполнения шнековой камеры, управления подачей материала, поднятия шнеков и стенки шнековой камеры совместно с плитой. Два шнека и два конвейера могут включаться автоматически при помощи одной кнопки с предварительно заданными настройками. При необходимости каждым шнеком и конвейером можно управлять по отдельности. Крылья бункера и фартук с гидроприводом могут складываться нажатием одной кнопки. Система может быть настроена для параллельной или раздельной активации левого и правого крыла, совместно с передним фартуком, оснащенным гидроприводом, или для активации всех трех компонентов.
Заниженная конструкция бункера асфальтоукладчика позволяет выгружаться самосвалам с длинным свесом. Длина бункера также увеличена, не позволяя длинному кузову грузовика упираться в дальнюю стенку бункера.
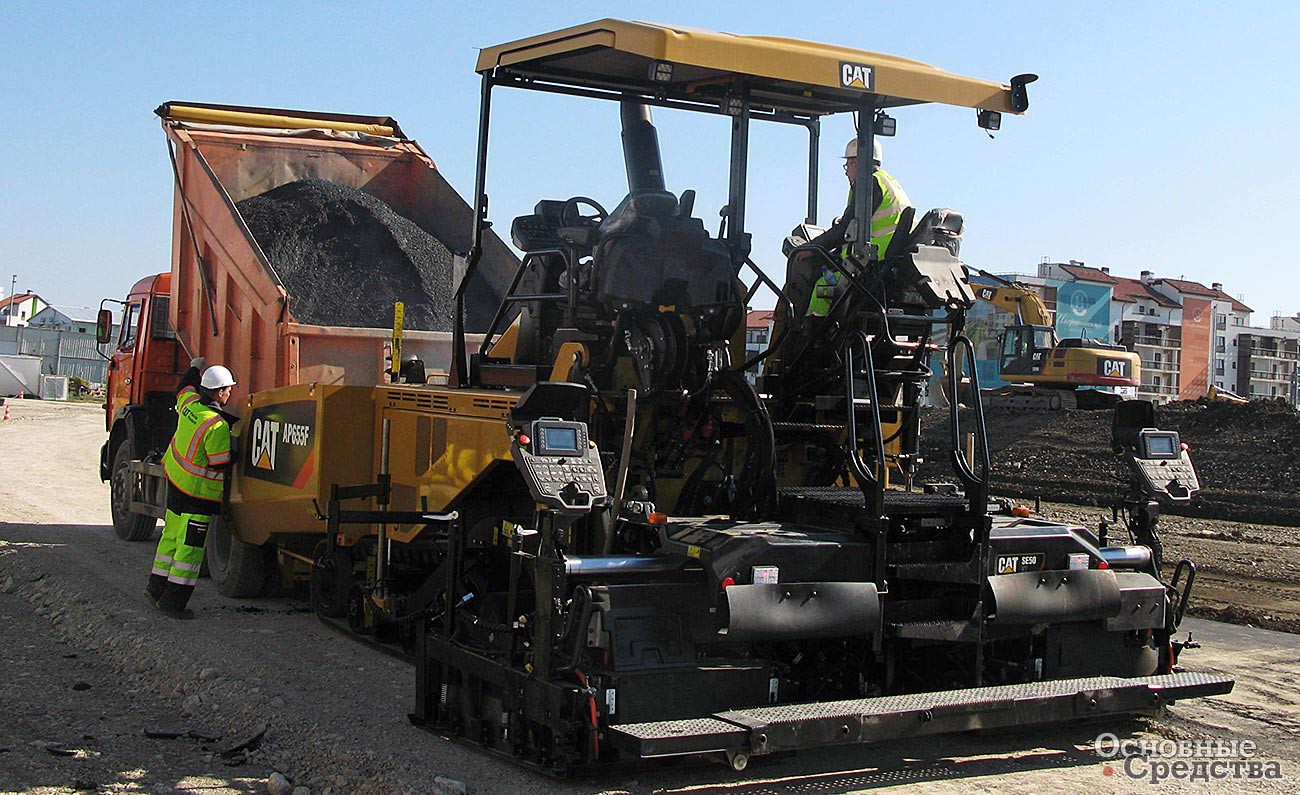
Днищевые плиты выполнены из высокопрочной стали твердостью HB≥500. Установлена плита Caterpillar принципиально новой конструкции, с трамбующим брусом и с гидравлическим уширением. Время подогрева плиты — самое короткое в своем классе. Электрогенератор прямого привода с масляным охлаждением мощностью 70 кВт обеспечивает высокую скорость нагрева плиты от +5...10ºС ºС до рабочей температуры в +130ºС за 15 мин. при отсутствии уширения. Нагрев плиты на полную ширину в 10 м займет всего 25 мин. Система электрообогрева плиты включает собственную систему диагностики с индикацией на сенсорном ЖК дисплее. Имеется два режима нагрева — постепенный и быстрый. Три заданных варианта нагрева обеспечивают широкий диапазон температур для различных типов смесей; низкий 110 °C, средний 130 °C, высокий 160 °C. Нагревательные элементы можно быстро заменять благодаря их модульной конструкции. Caterpillar уже не выпускает плит с газовым нагревом по соображениям безопасности. Конструкция плиты обеспечивает высокую жесткость за счет новой схемы необслуживаемого узла гидравлического уширения, выполненного на основе цельных балок, опирающихся при выдвижении на две массивные литые проушины рамы. Не у всех конкурирующих моделей балка опирается на две проушины. Управление гидравлическими уширителями 2-скоростное, пропорциональное. При укладке полосы шириной свыше 3500 мм необходимо устанавливать удлинители шнеков и уширение рамы машины. В данной машине это реализовано при помощи гидропривода. Дополнительные удлинители основной рамы с гидроприводом длиной 457 мм крепятся к шнеку и обеспечивают плавный поток материала к удлинителям. Они убираются вместе с уширителями вибробруса при уменьшении ширины укладки.
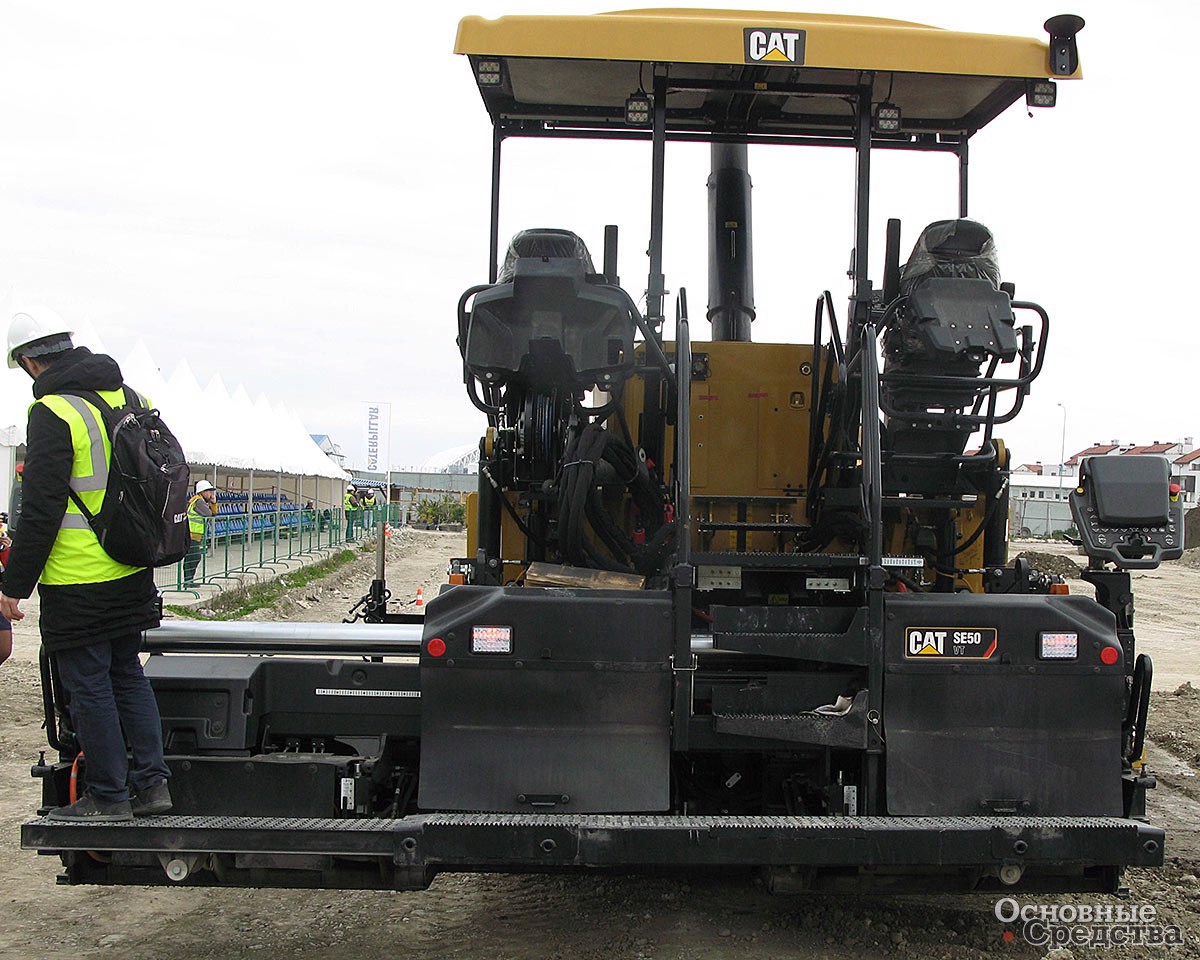

Есть возможность изменять частоту вибрации трамбующего бруса в диапазоне 700–1800 мин-1. В гидроприводе трамбующего бруса установлен аксиально-поршневой насос, при помощи которого производится объемное регулирование производительности. Конструкторы Caterpillar отказались от дроссельного регулирования, недостатками которого являются наличие в конструкции дополнительных узлов — клапанов, а также повышенный износ гидравлической жидкости.
Асфальтоукладчики Caterpillar имеют три режима движения: рабочий, транспортный и режим маневрирования, позволяющий машине выполнять разворот на месте. Благодаря этому они отличаются высокой маневренностью и мобильностью. Машина имеет специальную функцию блокировки руля, на виражах при укладке руль блокируется в повернутом положении и машина полностью копирует вираж.


Эксплуатационная масса (только асфальтоукладчик), кг | 15 584 |
Мощность двигателя, кВт (л.с.) | 151 (205) |
Ширина укладки (в зависимости от комплектации), м | 2,55-10,0 |
Максимальная скорость укладки (в зависимости от комплектации), м/мин | 25,0-64,0 |
Максимальная скорость хода, км/ч | 14,5 |
Внутренний радиус поворота, м | 0,5 |
Вместимость бункера, м3 | 7,1 |
Пропускная способность, т/ч | 1300 |
Ходовая часть машины со сверхпрочными резинометаллическими гусеничными лентами имеет оригинальную запатентованную конструкцию Mobil-Trac System (MTS). Гусеницы не требуют технического обслуживания. Колесные тележки качающиеся, за счет этого уменьшаются колебания точки буксировки выглаживающей плиты при наезде на препятствие и при движении по неровному основанию. Стальные обрезиненные опорные катки обеспечивают плавность хода, высокий КПД передачи тягового усилия, а также равномерно распределяют массу асфальтоукладчика по всей длине ленты. Машина, оснащенная MTS, устойчиво движется как по твердому, так и по рыхлому основанию за счет увеличенной на 13% по сравнению с обычной гусеницей площадью контактной поверхности. Гусеничная лента снабжена системой автоматического натяжения. Caterpillar дает гарантию на резинометаллическую гусеницу 4000 моточасов или 4 года.
Точки смазки сгруппированы. Периодичность замены гидравлической жидкости на данной машине — 3000 мтч. Гарантия на машину — 1 год без ограничения наработки. Можно приобрести продленную гарантию на узлы трансмиссии, двигателя, гидросистемы.
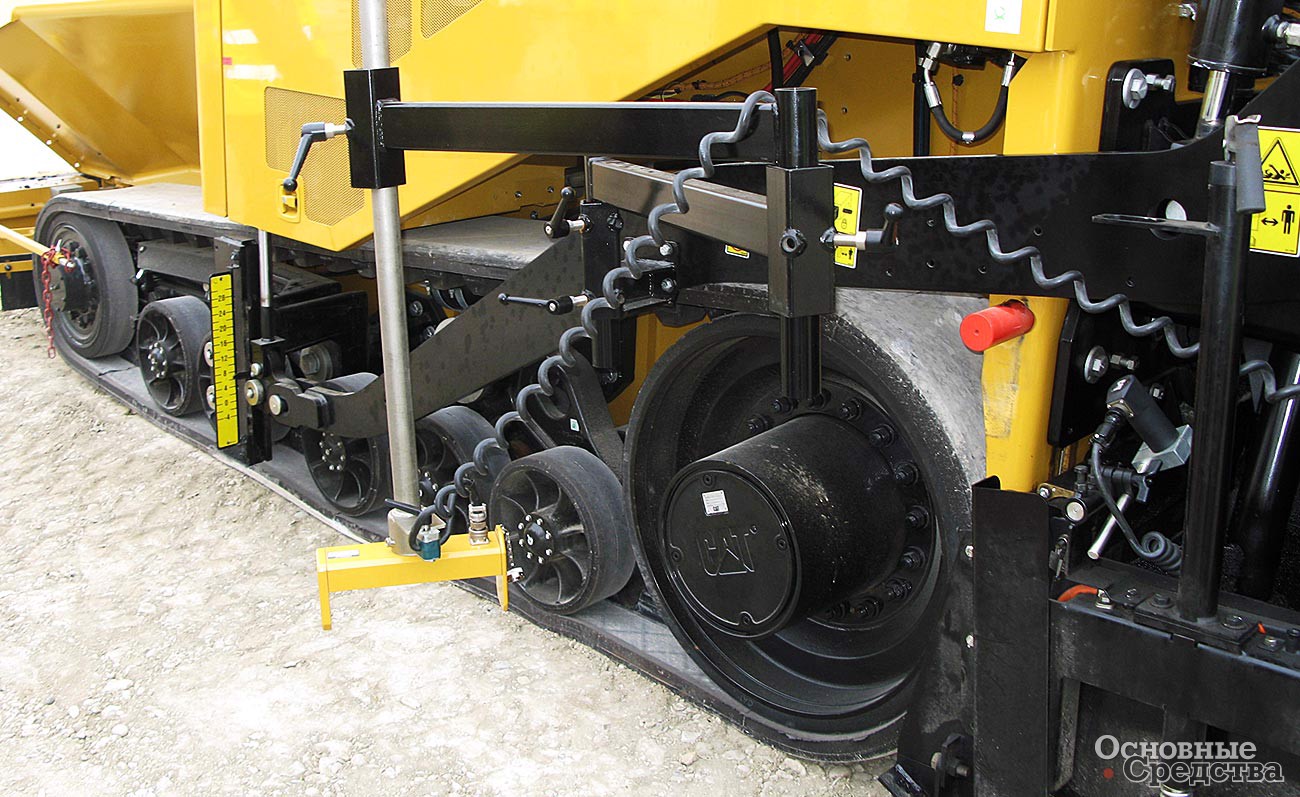
Бульдозер Cat D5R2
Бульдозер D5R2 – новинка 2016 г. Интерфейс монитора системы управления упрощен и интуитивно-понятен. Система управления электрогидравлическая, благодаря этому любая система нивелирования встраивается в бульдозер без внедрения в гидравлику. В стойки кабины встроены элементы защитной конструкции ROPS/FOPS/
Оснащается полноповоротным отвалом с гидроприводом, по заказу предлагается складной отвал, у которого боковую часть можно сложить и уменьшить габарит до допустимого для транспортировки. Также может оснащаться полусферическим отвалом.
Увеличилась производительность машины по сравнению с моделью предыдущего поколения. Гидросистема оснащена двумя аксиально-поршневыми гидронасосами, один — в контуре дифференциальной системы поворота, второй - в контуре рабочего оборудования. Благодаря наличию двух контуров машина может одновременно выполнять поворот противовращением гусениц и поднимать/опускать отвал.

Эксплуатационная масса (в зависимости от комплектации), кг | 16032-18504 |
Мощность двигателя (в зависимости от комплектации), кВт (л.с.) | 114, 130 (155, 177) |
Производительность гидронасоса, л/мин | 135 |
Рабочее давление в системе, кПа | 6900 |
Ширина отвала (в зависимости от комплектации), мм | 3154-4165 |
Высота отвала (в зависимости от комплектации), мм | 1031-1238 |
Глубина копания (в зависимости от комплектации), мм | 420-505 |
Ширина колеи, мм | 1890 |
Дорожный просвет, мм | 419 |
Давление на грунт (в зависимости от комплектации), кПа | 54,2-57,5 |
Фронтальный погрузчик SEM 656D
Китайское предприятие SEM стало частью Caterpillar в 2008 г. Ранее оно называлось Shandong Engineering Machinery – отсюда бренд SEM. Американская компания вложила большие средства в расширение и модернизацию производства. Это самый современный завод в Китае из всех предприятий Caterpillar. Производство организовано согласно стандартам и опыту Caterpillar. Выпускаются колесные фронтальные погрузчики, автогрейдеры, бульдозеры и грунтовые катки. Производятся машины и отдельные компоненты. Есть учебный центр и КБ.
В линейке фронтальных погрузчиков SEM имеются машины г/п 2,0; 3,0; 5,0 и 6,0 т. В Сочи был представлен фронтальный погрузчик нового поколения SEM 656D. Эта модель выпущена взамен очень популярной прежней машины SEM650В, их было продано в странах СНГ несколько сотен.
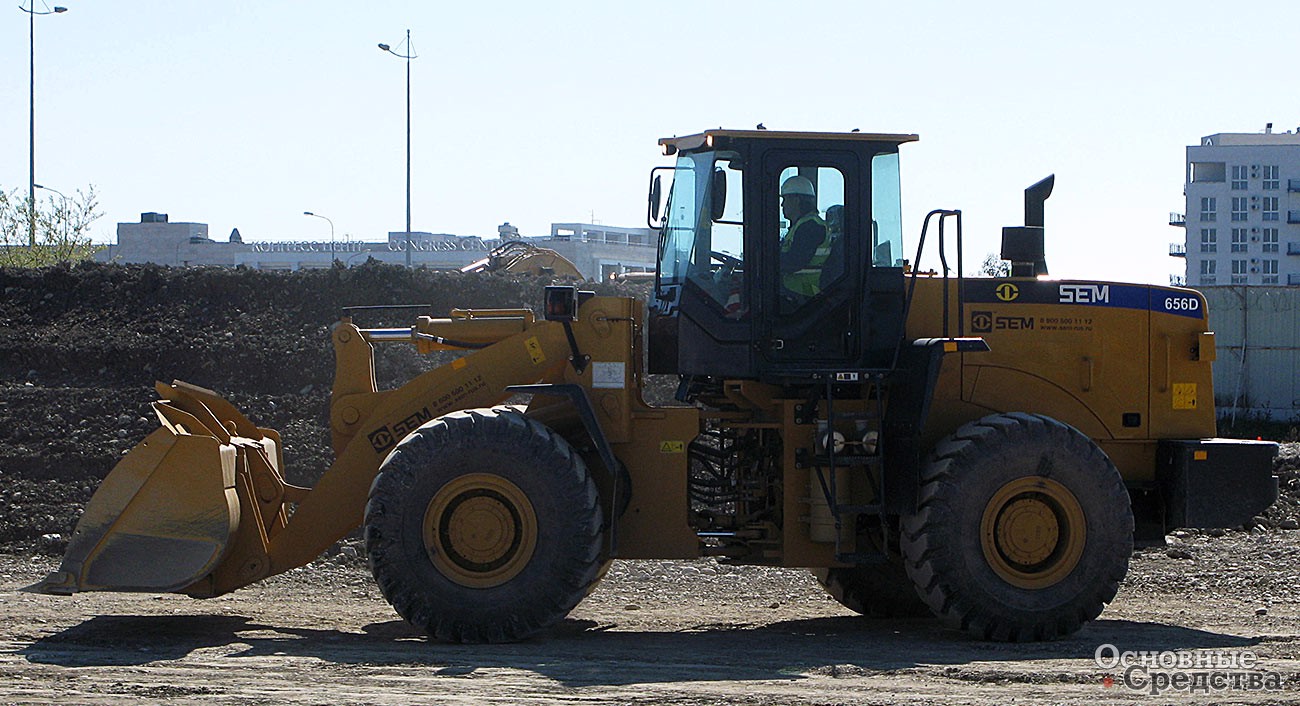
Кабина — одна из самых комфортных на рынке среди китайских конкурентов, большого объема, с кондиционером в штатной комплектации и шумоизоляцией, с высокочувствительным джойстиком управления.
Преимуществом новой машины является ковш новой серии Cat Performance, имеющий повышенную наполняемость за счет увеличенных щек и формы дна. Геометрия ковша позволяет набирать в него материал так, что он не слипается, не спрессовывается и легко выгружался. Только за счет этого конструкторского решения производительность машины возросла на 10%. Z-образный рычажный механизм обеспечивает радиальную траекторию подъема ковша.
Также преимуществами являются и ряд компонентов собственного производства, например, мосты SEM с допустимой динамической нагрузкой 32 т, тогда как в среднем в данном классе китайских погрузчиков этот параметр равен 27 т. Поскольку допустимые нагрузки у мостов SEM выше на 5 т, надежность и долговечность у них существенно выше, чем у конкурентов.
У тормозной системы имеется функция «помощь при трогании с места на подъеме». Опционно возможна установка маслопогруженных тормозов и дифференциалов повышенного трения.

Трансмиссия SEM — многовальная, с гидротрансформатором, без разрыва потока мощности при переключениях, с увеличенным количеством передач: 4/4 переднего и заднего хода в отличие от конкурентов, у которых планетарные КП. В результате использования такой конструкции и возможности широкого выбора передач для движения на коротком и длинном плечах ресурс у КП погрузчиков SEM вдвое больше, чем у планетарных КП конкурентов.
Применена оригинальная схема гидросистемы с двумя насосами: в рулевом контуре аксиально-поршневой, в контуре рабочего оборудования шестеренный. В системе имеется клапан приоритета, поэтому, если рулевой механизм не используется (когда машина врезается в, набирает грунт, поднимает, разгружает), то клапан приоритета перенаправляет гидропоток от аксиально-поршневого насоса в гидроконтур рабочего оборудования. В результате повышается вырывное усилие и существенно снижается длительность рабочего цикла по-сравнению с конкурентами — до 9,3 сек. Среднее время по данной отрасли — около 11 сек. К тому же гидросистема рулевого управления имеет регулировку производительности в зависимости от нагрузки за счет аксиально-поршневого насоса. Гидросистема комплектуется компонентами как китайского, так и американского производства Caterpillar.

Эксплуатационная масса (в зависимости от комплектации), кг | 16 800-17 100 |
Мощность двигателя, кВт | 162 |
Емкость ковша, м3 | 2,7-4,5 |
Грузоподъемность ковша, кг | 5000 |
Усилие вырыва ковша, кН | 173 |
Высота разгрузки, мм | 3113 |
Рабочее давление в гидросистеме, МПа | 18 |
Угол качания заднего моста, град | ± 11 |
Угол поворота шарнирного сочленения рамы, град | 38±1 |
Максимальная скорость переднего/заднего хода, км/ч | 43/43 |
Частота вращения вентилятора динамической системы охлаждения регулируется при помощи гидромуфты в зависимости от потребности.Это обеспечивает экономию до 3% топлива. Система с гидромуфтой устанавливается не на всех моделях этой линейки — некоторые комплектуются обычным механическим приводом вентилятора.
В конструкции используются подшипники мирового уровня качества: NSK, SKF (оба - Япония), Timken (США). Гидравлические компоненты Eaton, Parker и др.
На всех машинах SEM устанавливается полуцентрализованная система смазки. Может быть и полностью централизованная полуавтоматическая, когда все точки смазки группированы в одном месте. Может быть установлена полностью автоматическая централизованная система, когда оператору нужно только регулярно заполнять резервуар со смазкой.
Ковш производства завода в Тосно
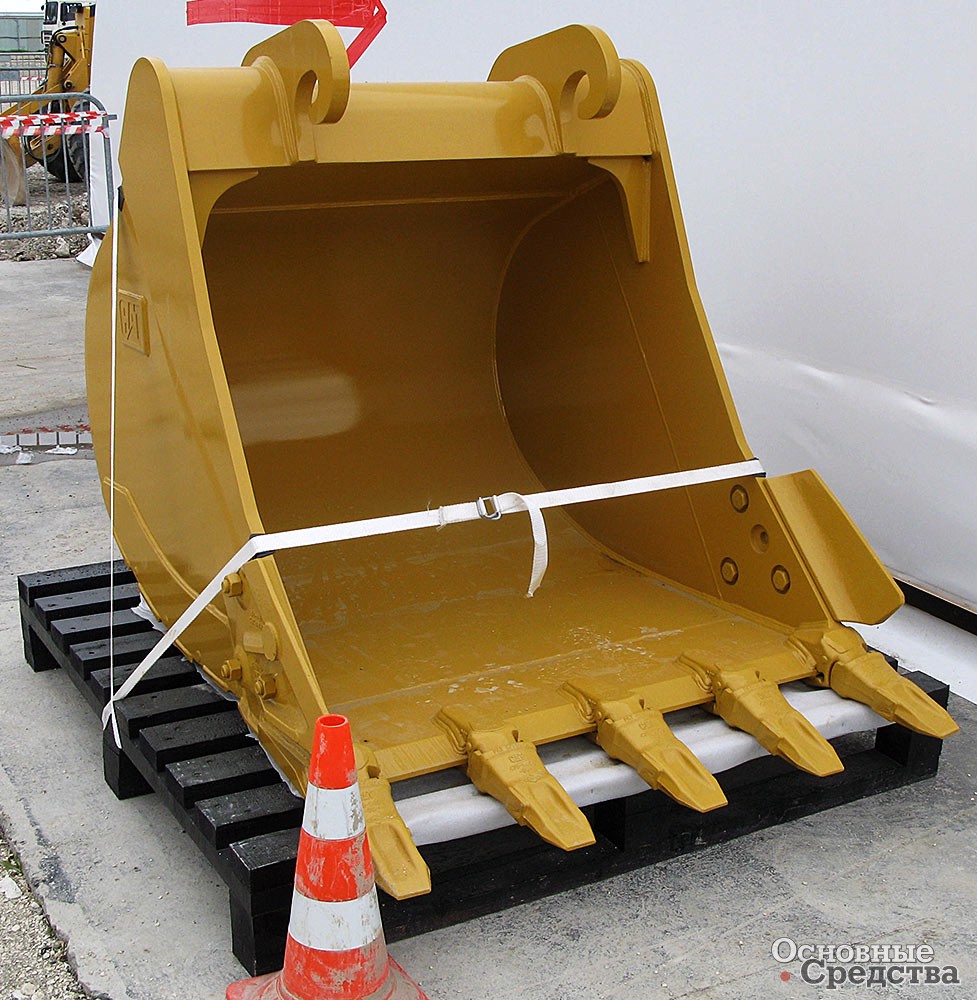
На семинаре был представлен экспериментальный экскаваторный ковш, производство которого компания локализует на заводе в Тосно. Он выполнен по всем технологиям и соответствует всем требованиям качества компании Caterpillar. В настоящее время завершается его сертификация. Затем планируется внедрить производство и другого навесного оборудования.

Объемное проектирование смесей Superpave
Очень интересным и познавательным был доклад о методе проектирования асфальтобетонных смесей Superpave, который позволяет учитывать требования к рабочим характеристикам асфальтобетонного покрытия в зависимости от интенсивности движения по будущей дороге и особенностей климатической зоны, где будет применяться покрытие. Superpave – это новый подход к проектированию асфальтобетонных смесей, а именно – оценка качества всех материалов, которые применяются для этого проектирования, т.е. новый подход к полимерным битумным вяжущим и к каменному материалу. Эта методика облегчает комбинирование битумного вяжущего и минерального заполнителя для получения смесей с необходимыми эксплуатационными характеристиками.
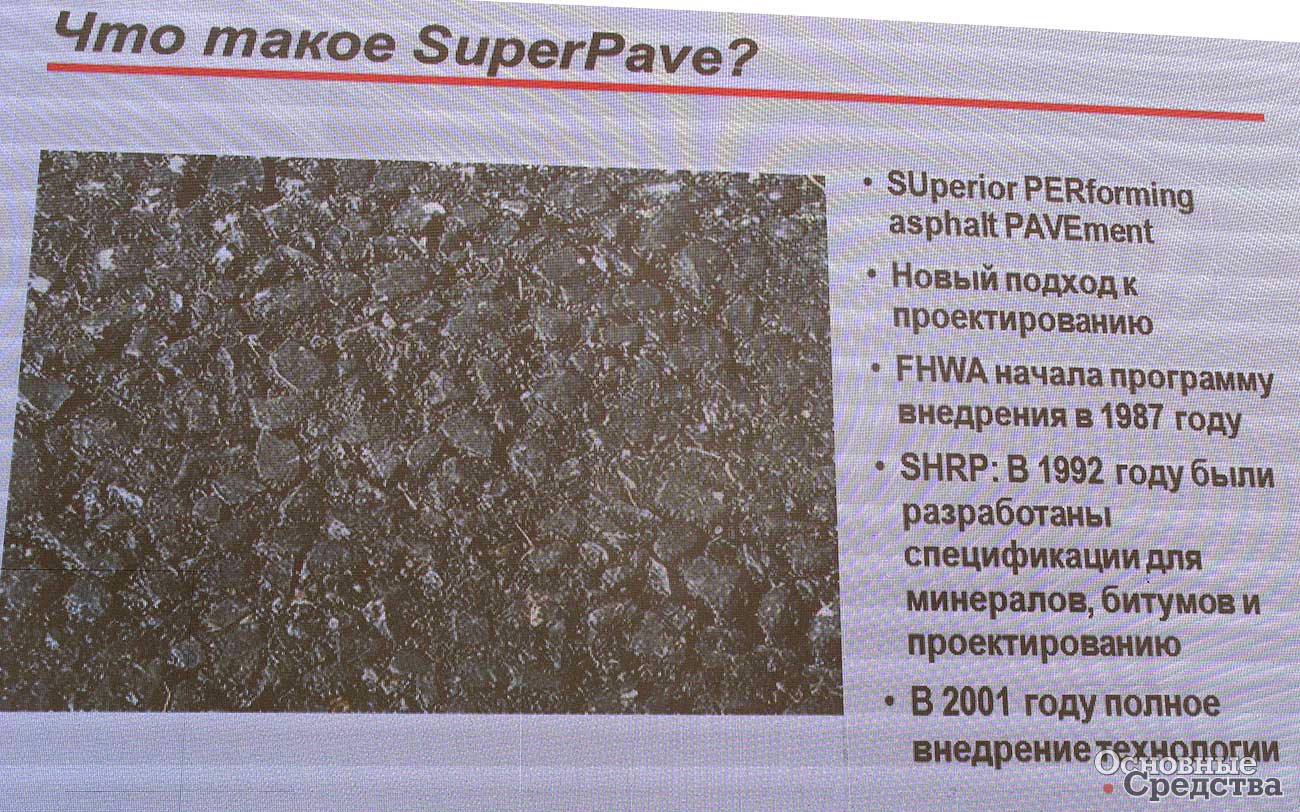
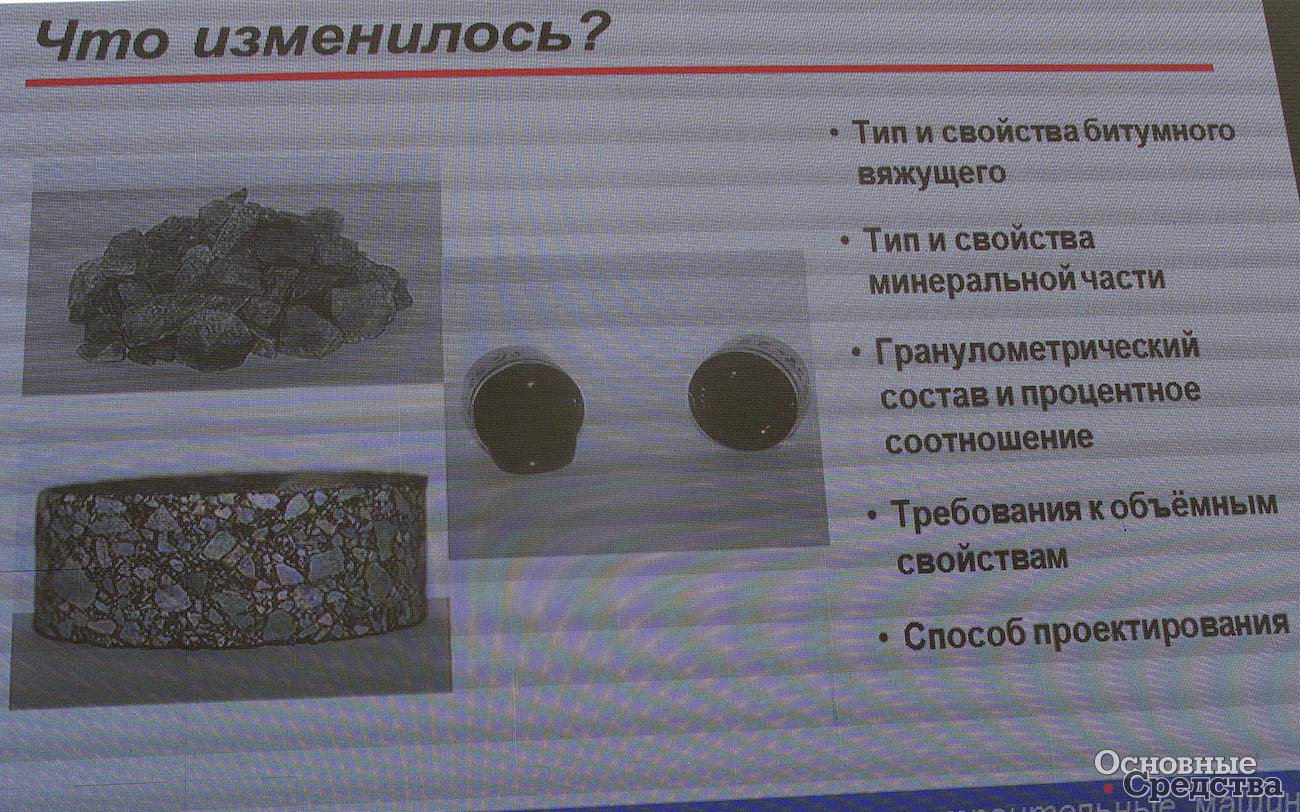
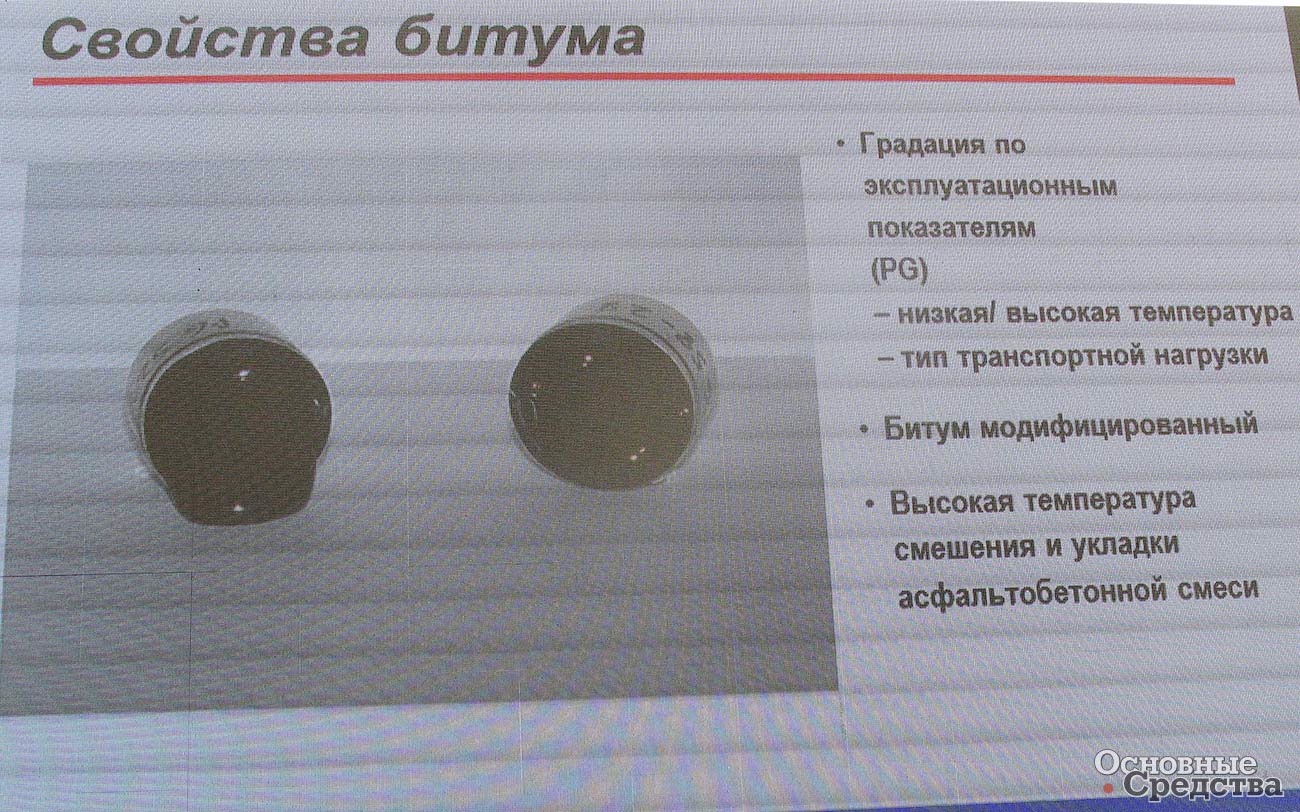
Первое, с чего начинается проектирование – это подбор битумного вяжущего в зависимости от интенсивности движения и особенностей климатической зоны. Полимерно-битумное вяжущее выбирается исходя из нижней и верхней температурных границ его использования, т. е. температур хрупкости и размягчения, а также адгезии, устойчивости к старению и т. д. Конечной целью работы является устранение температурного и усталостного трещинообразования в будущем дорожном покрытии.
Для оценки эксплуатационных качеств вяжущего (и вообще - подбора и определения качеств всех материалов, а также готовой асфальтобетонной смеси) применяется лабораторное оборудование, показанное на слайде и фото.
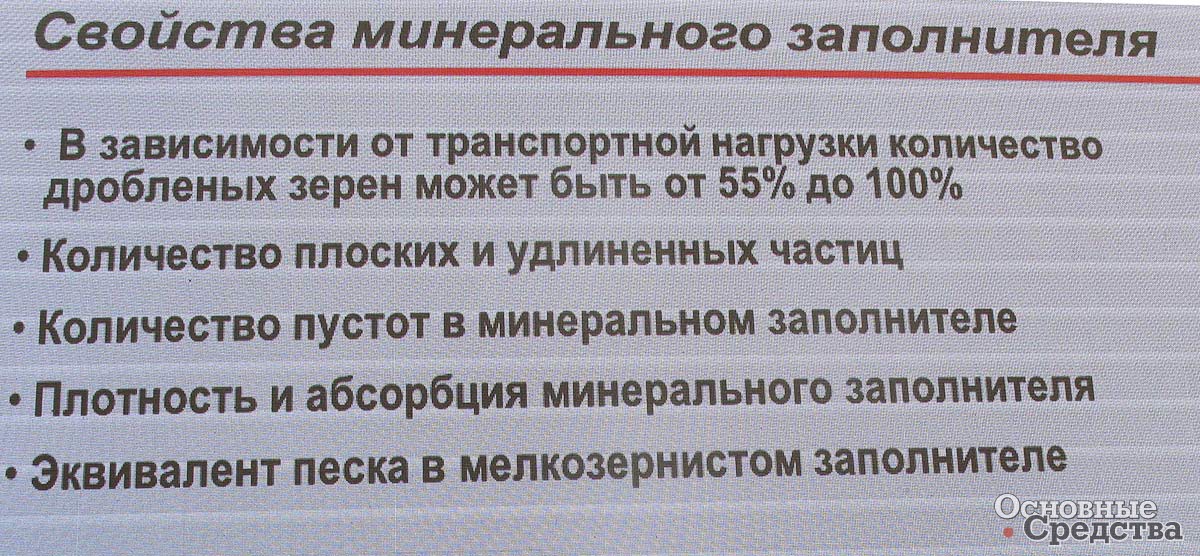
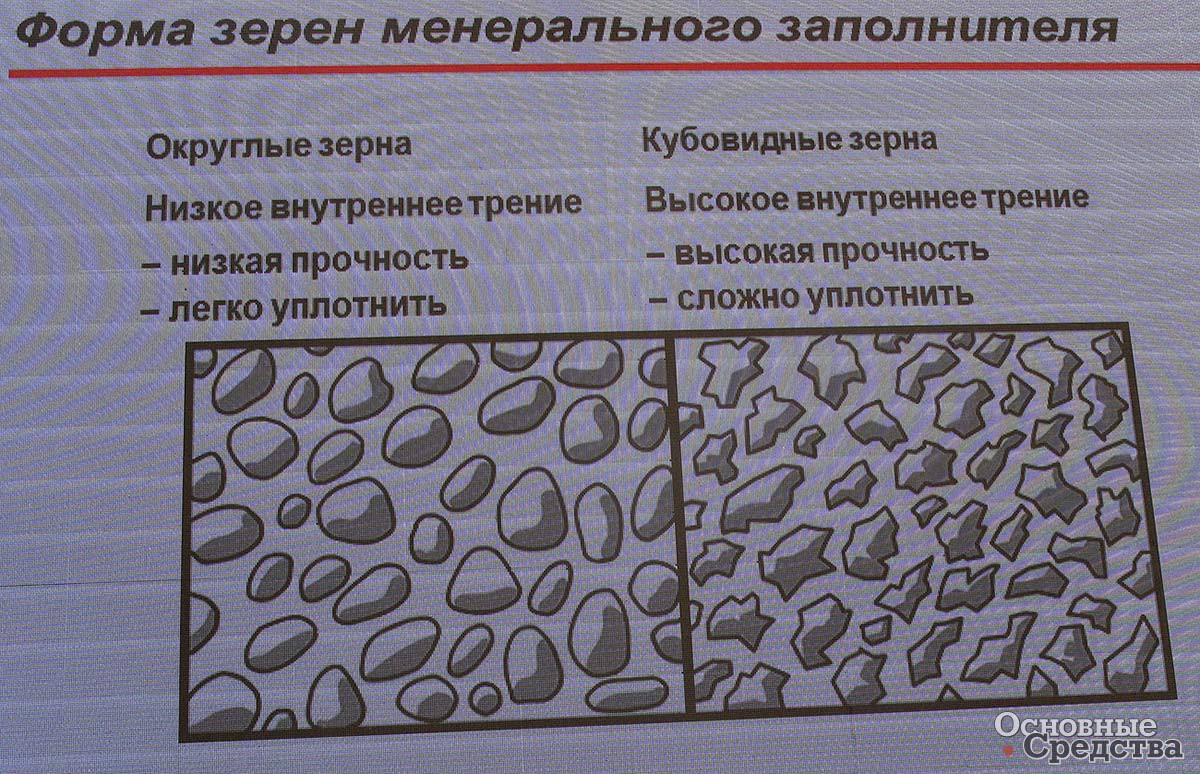
После того, как подобрано битумное вяжущее, подбирается каменный материал. На слайдах представлены основные параметры, которые подбираются и проверяются. Кубовидные зерна щебня имеют большое количество граней. Благодаря наличию этих граней после уплотнения зерна лучше расклиниваются и слой в дальнейшем дольше сохраняет прочность. Но уплотнять такой формы щебень сложнее. Округлые зерна легко уплотняются, но слой имеет низкую прочность, долговечность дорожного покрытия уменьшается.
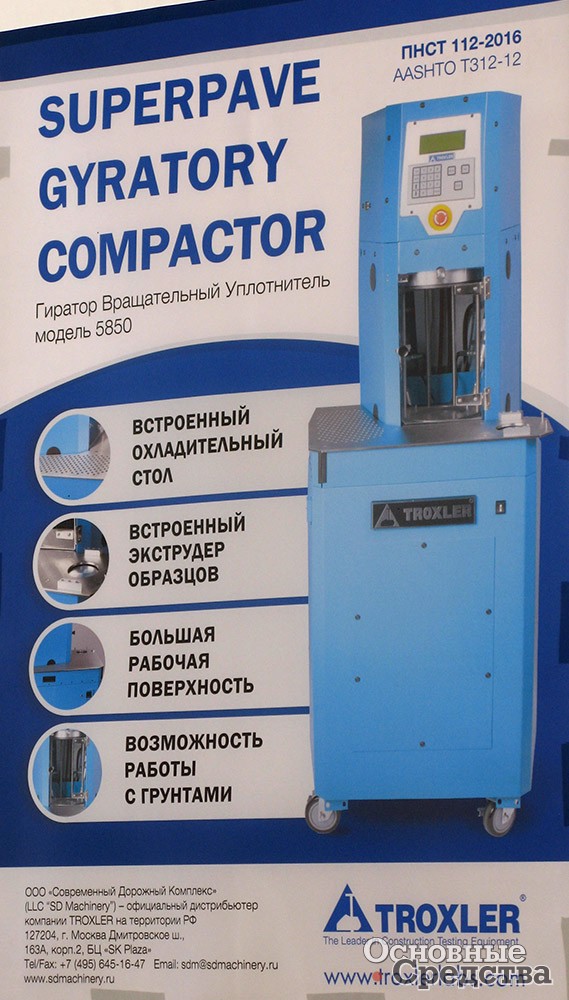
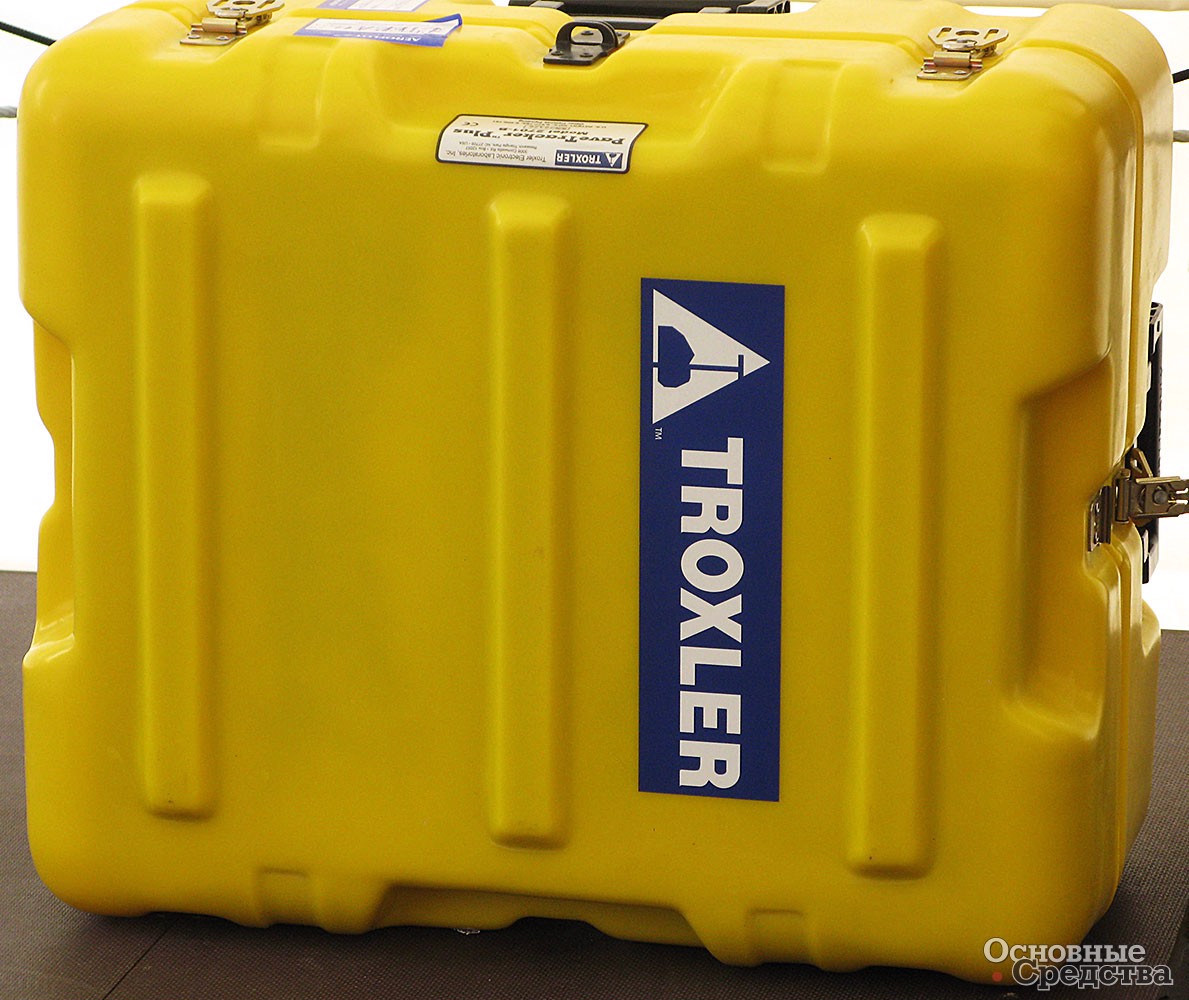
После того, как подобраны полимерно-битумное вяжущее и каменный материал, приступают к проектированию асфальтобетонной смеси, в этом помогает прибор-гиратор Troxler, который моделирует покрытие и позволяет оценить его состояние через 5, 10, 15 и даже 20 лет эксплуатации в заданных условиях. Вообще гиратором можно оценивать качество любой смеси. В некоторых модификациях этот прибор работает даже с эмульсией. Но работая по технологии Superpave без гиратора обойтись невозможно.
После того, как смесь подобрана и проведены все испытания, документация поступает на асфальто-бетонный завод. Смесь производится в заводских условиях по заданной рецептуре, ее испытывают по полной программе исследований, чтобы убедиться, что все характеристики соответствуют требованиям нормативной документации. После того, как испытания подтвердят, что смесь соответствует всем требованиям, ее можно укладывать.
Рассмотрим передовые современные технологии укладки асфальтобетонного покрытия.
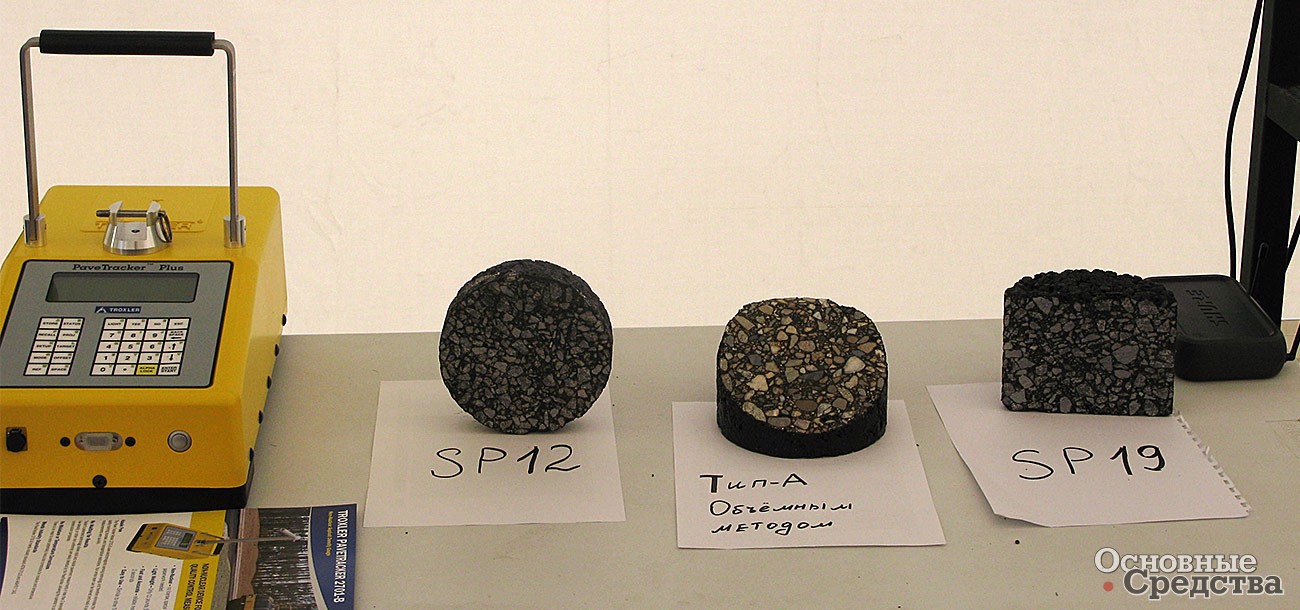
Уплотнение слоев дорожной одежды
«Зона податливости». Особенность применяемых асфальтобетонных смесей – это явление «зона податливости»: при остывании от температур 140-160ºС до температур менее 135ºС, в определенном температурном диапазоне данные смеси становятся более чувствительными к воздействию давлением и налипают на пневмошины катков. Это явление обычно возникает на промежуточном этапе уплотнения.
На данный момент кардинального решения проблемы «зон податливости» нет, его ищут и для того, чтобы избежать негативных последствий этого явления, рекомендуется использовать дорожные катки в порядке, указанном на слайдах или просто не выполнять уплотнения, дождавшись, пока материал чуть остынет ниже «зоны податливости» и затем выполнить уплотнение. Следует учесть: в таком случае уплотнение необходимо компенсировать увеличением степени уплотнения на начальном этапе укладки, обеспечивая заранее высокую плотность.
Кроме того, если при укладке асфальтобетонной смеси есть вероятность встретиться с явлением «зон податливости», необходимо применять специальную аппаратуру — инфракрасные термометры, которые в режиме реального времени определяют температуру асфальтобетонной смеси и дают оператору на экране дисплея наглядную картину распределения температур по зонам на данном участке, по которой он может контролировать «зоны податливости» и видит, когда катку следует приступать к уплотнению слоя и когда прекращать уплотнение этого слоя, может избегать больших перекрытий при проходах. Система считает количество проходов, регистрирует, при каких температурах сделаны проходы с привязкой к географическим координатам, технолог по этим данным может определить, сколько нужно сделать проходов машине, чтобы обеспечит необходимую степень уплотнения. Система регистрирует не состояние материалов, поскольку оно меняется с изменением температуры, а их качество — а плотность будет измеряться ближе к окончанию работы, когда опустится температура.
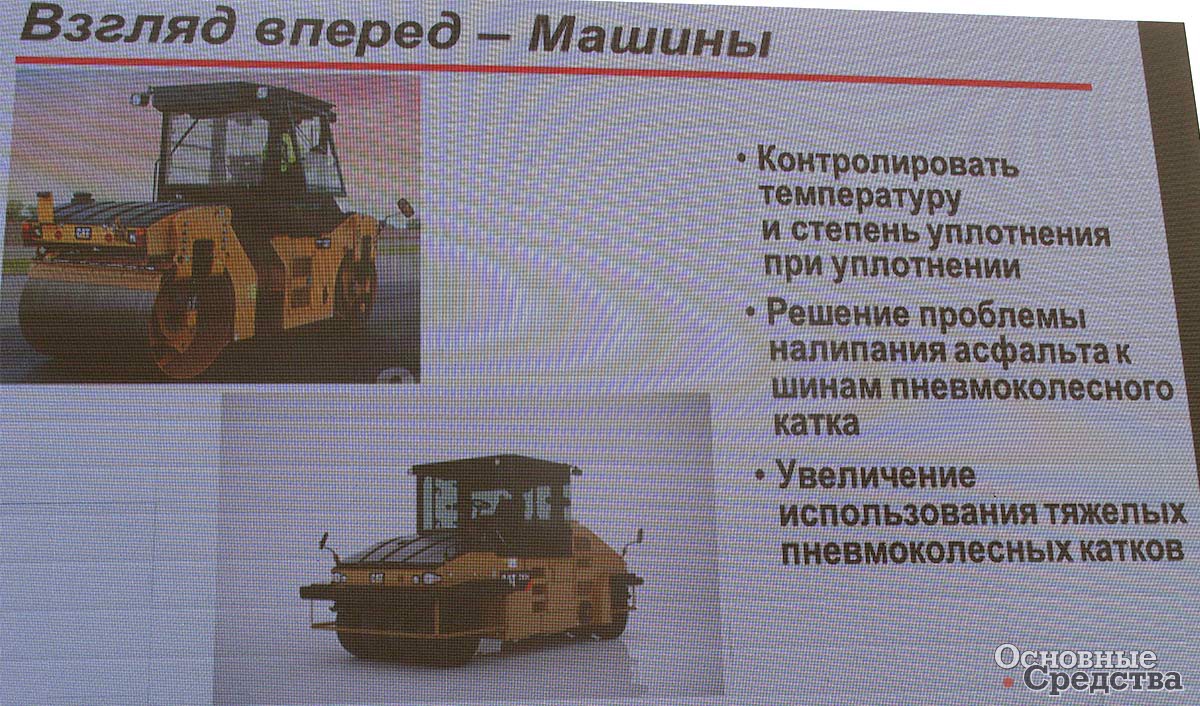
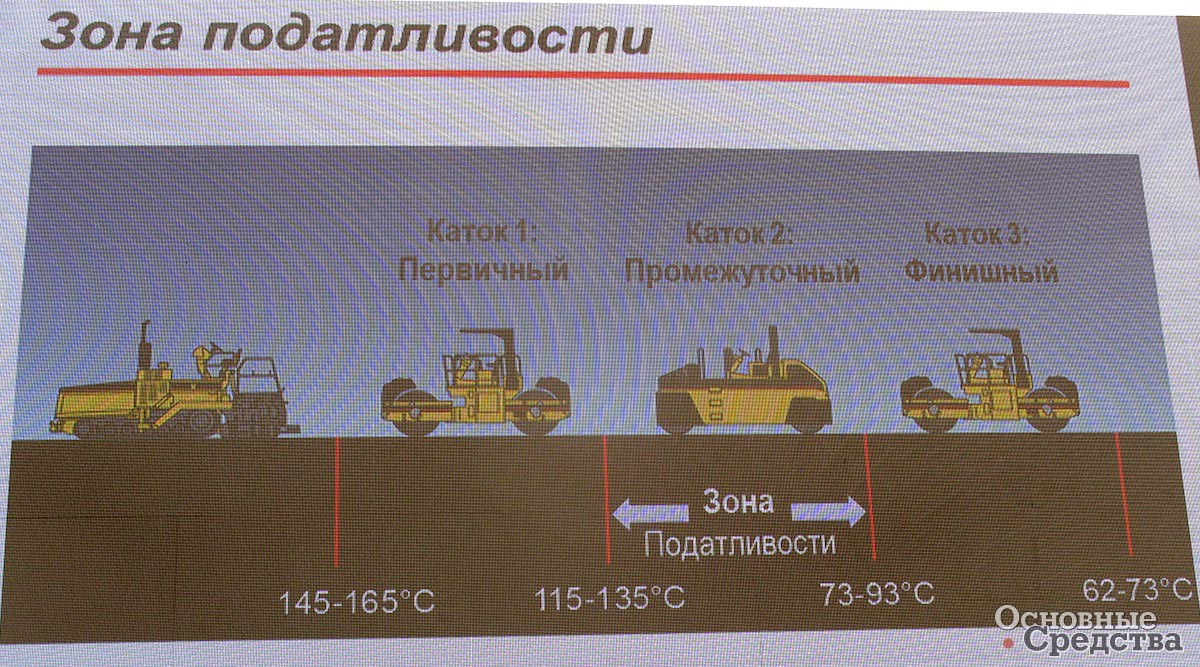
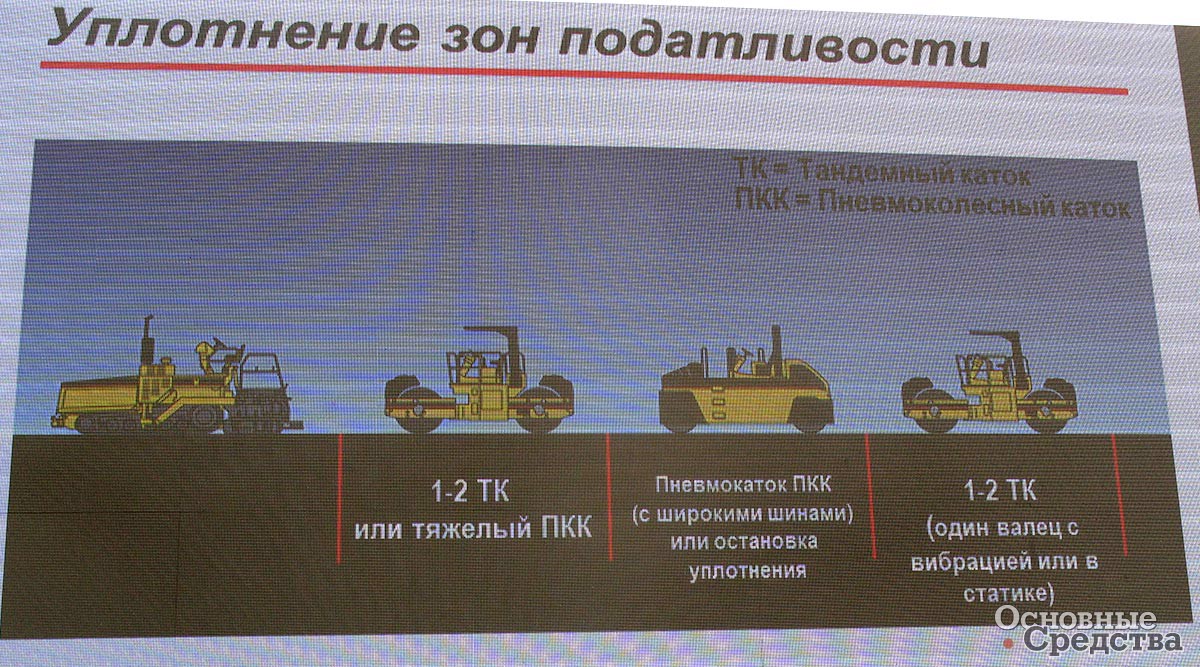
Борьба с сегрегацией смесей при укладке. Одна из особенностей смесей, спроектированных по технологии Superpave — большое содержание щебня-заполнителя. Этот заполнитель склонен к сегрегации, т. е разделению на фракции по крупности, размеру зерен или по другим признакам. Вся же смесь склонная к сегрегации по температуре. Гранулометрическая сегрегация имеет место в больших объемах. Смеси с большим процентным соотношением крупных зерен также имеют склонность к сегрегации. На семинаре было представлено несколько приемов, позволяющих минимизировать сегрегацию при укладке данных смесей традиционным методом: «самосвал-асфальтоукладчик». Подчеркнем - исключить сегрегацию полностью невозможно, ее можно только минимизировать. Чтобы минимизировать гранулометрическую сегрегацию, рекомендуется:
- выгружать смесь из самосвала полностью, избегая порционного ссыпания смеси в бункер, чтобы этого добиться, нужно отладить четкую работу всей бригады;
- медленно поднимать кузов самосвала при перемещении смеси ближе к заднему борту до того, как он откроется и смесь посыпется в бункер асфальтоукладчика;
- минимизировать движения створок бункера асфальтоукладчика (практически это почти невозможно).
Чтобы минимизировать температурную сегрегацию, рекомендуется постоянно поддерживать некоторое количеств смеси в бункере и шнековой камере. Чтобы успешно реализовать все эти приемы, бригады должны быть слажены, люди должны понимать друг друга с полуслова.

Уплотнение катками. От качества уплотнения материалов дорожных одежд зависит несущая способность будущей дороги и ее долговечность. Современные катки оснащаются бортовыми системами контроля степени уплотнения материала. Существуют следующие варианты оснащения для контроля степени уплотнения.
1)На базе акселерометра. При помощи акселерометра измеряется ускорение отскока вальца от поверхности, чем плотнее поверхность — тем больше отскакивает валец. Недостатки этой системы в том, что она может работать только при включенной вибрации и только на несвязных грунтах, т. к. связные грунты хорошо поглощают энергию удара и корректных данных не получается. К тому же, измерения производятся на глубину до 1,0-1,2 м, т. е. глубже нового уплотняемого слоя, показания уплотнения как бы осредняются на указанную глубину. Зато при таком методе измерения можно обнаружить пустоты и скрытые в глубине объекты — валуны, стволы деревьев.
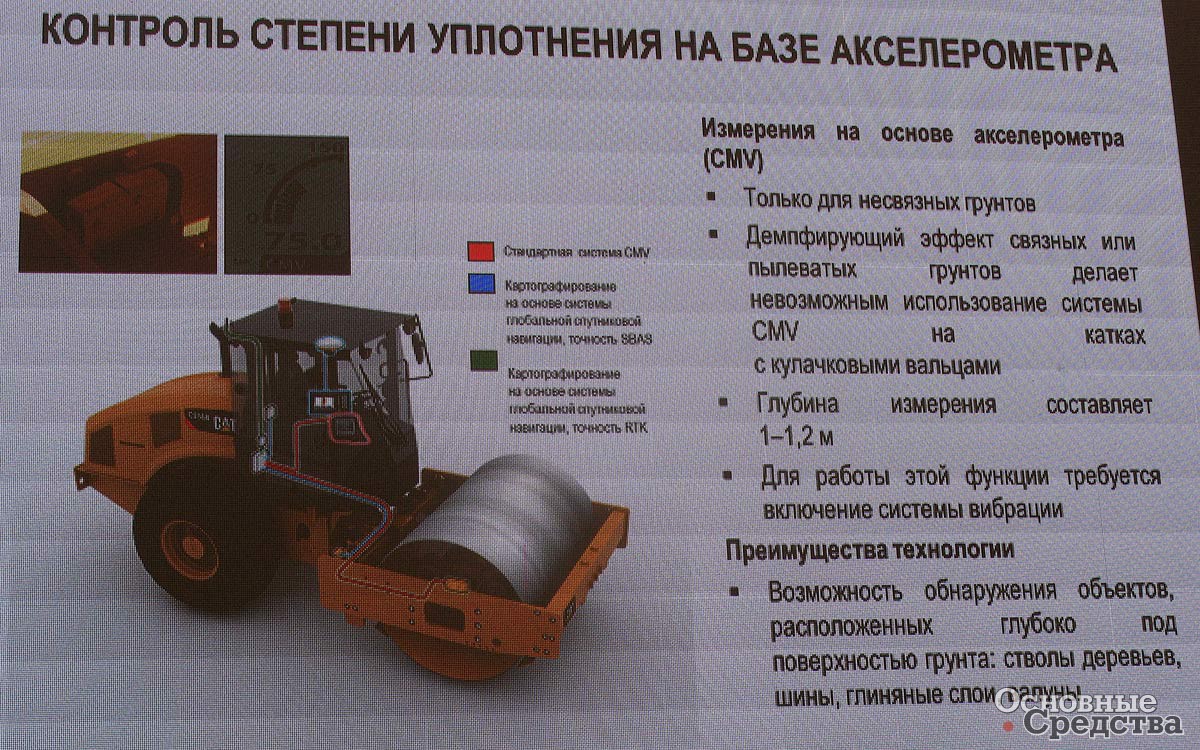
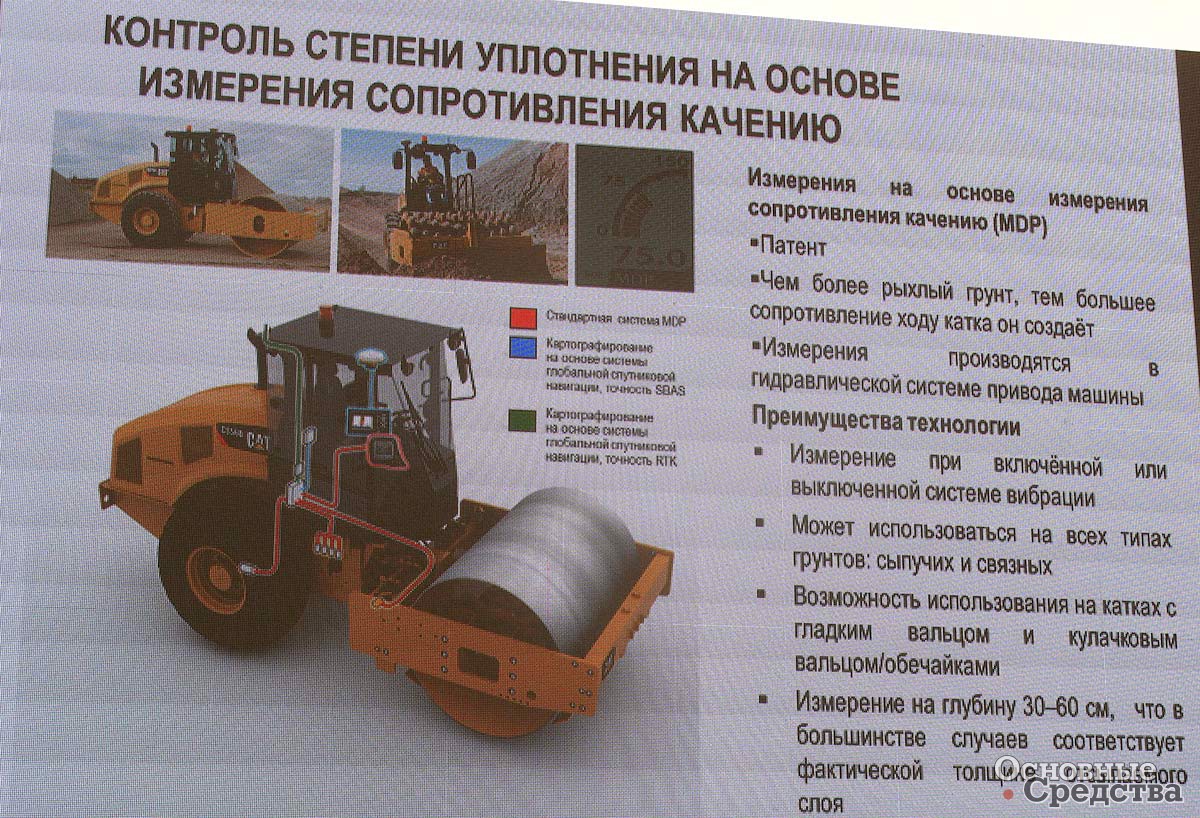
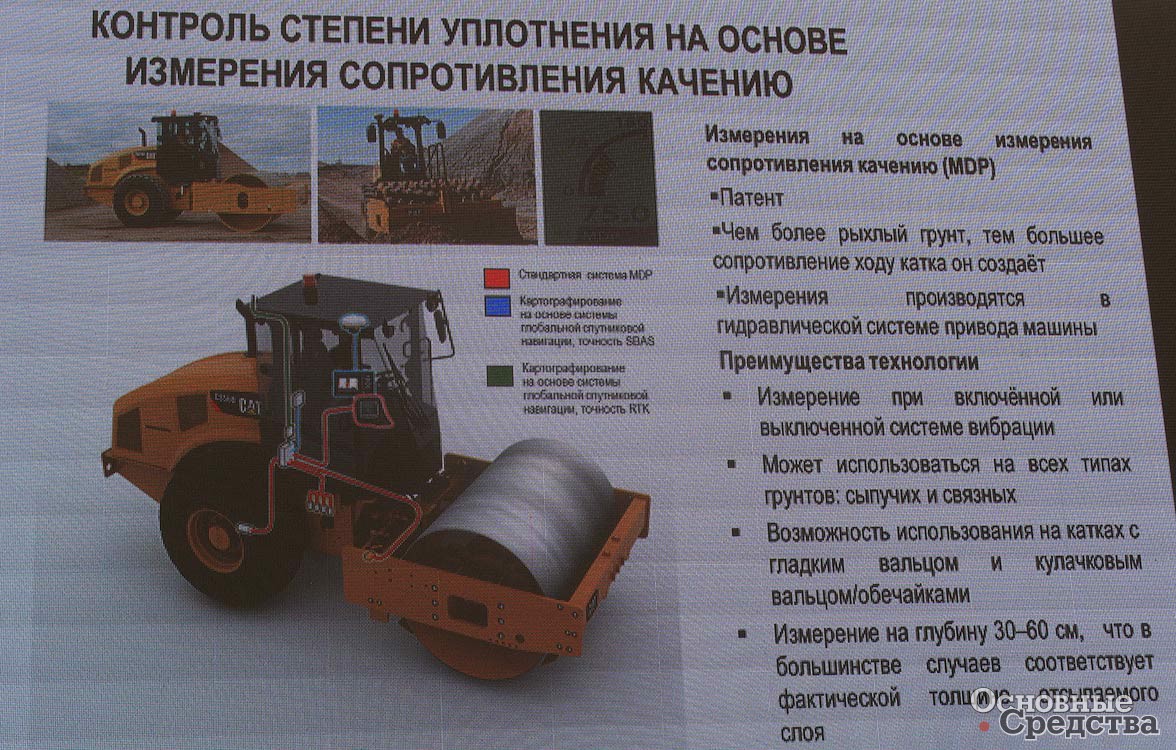
2)На базе измерения сопротивления качению работает запатентованная система Caterpillar MDP. В гидросистемы переднего и заднего приводов встраиваются датчики давления. Давление в приводах изменяется в зависимости от сопротивления качению. Электронная система анализирует показания датчиков и оценивает степень уплотнения материала. Данная система точнее и универсальнее, чем система с акселерометром, потому что измеряет и при включенной вибрации, и без нее, может работать на грунтах любых типов: зернистых, полусвязных и связных, на грунтовых катках и с гладкими, и с кулачковыми вальцами. Измерения производятся на глубину 30-60 см, что часто соответствует слою отсыпки. Отсыпая материал, мы контролируем именно уплотнение этого слоя.
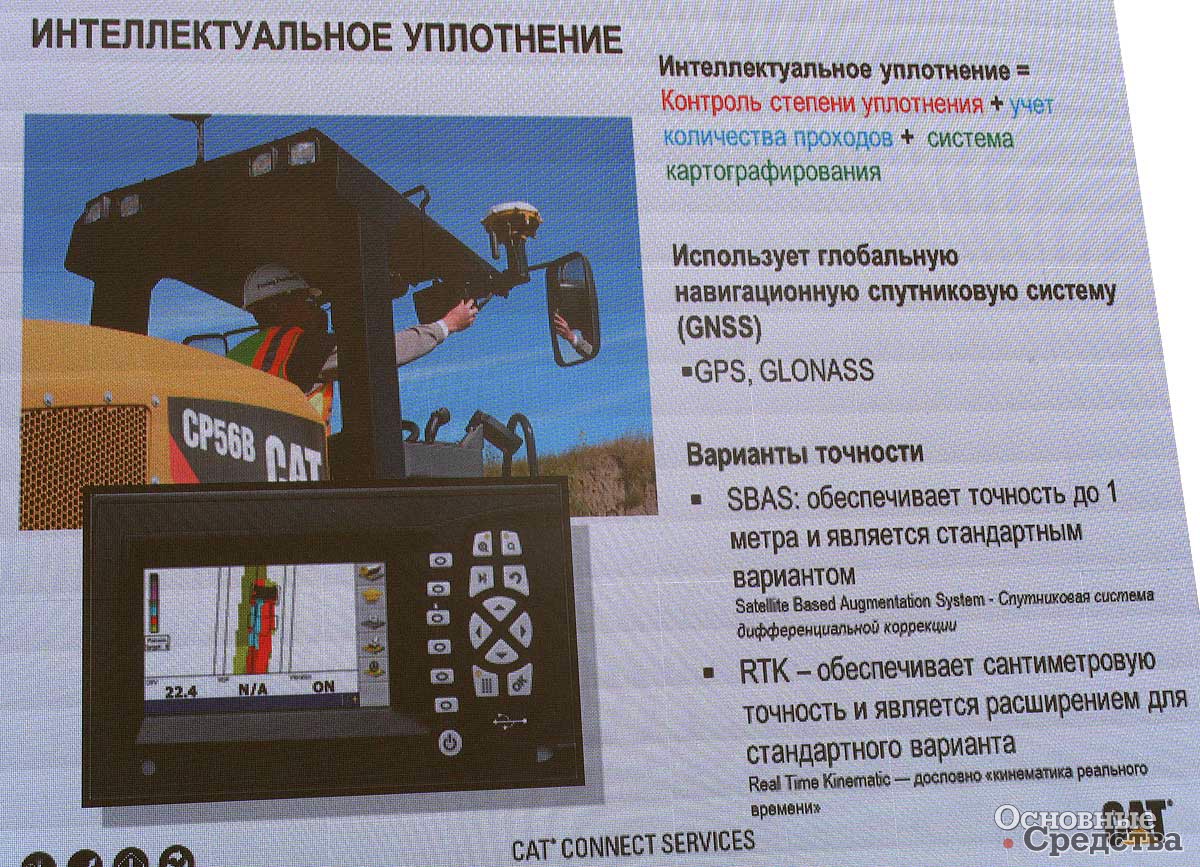
3)Комплексная интеллектуальная система измерения, включающая в себя функции учета количества проходов, картографирования и удаленного контроля данных. Измерение производится обеими системами - на основе акселерометра и по сопротивлению качению. Система картографирования использует спутниковое ориентирование GPS/ГЛОНАСС, чтобы привязываться к конкретным географическим координатам. Существует два уровня точности — стандартные протоколы, обеспечивающие до 1-3 м погрешности, и при использовании базовой станции GPS/ГЛОНАСС с поправками от специальной инфраструктуры на объекте точность увеличивается до 1,5-2,0 см по горизонтали и вертикали. На экране дисплея оператор видит движение катка, степень уплотнения отдельных участков отображается разными цветами. Эту информацию можно удаленно получать и в центральном офисе компании. Система позволяет фиксировать и хранить в памяти данные по качеству выполнения работ по каждому конкретному объекту. Если отсыпаются толстые слои дорожных одежд, например, песка в 1 м, то включается система на базе акселерометра. Обе системы могут работать одновременно и уточнять показания друг друга.
Все упомянутые системы дают возможность измерить уплотнение на всем участке, а не в отдельных точках, как при контроле пробами-кернами, и выполнить привязку результатов к географическим координатам. Следует помнить, что показания этих систем — относительные величины, т. е. сначала в лаборатории нужно калибровать ее показания, получить — какой степени уплотнения по Проктору на данном материале соответствуют показания системы. Система предварительно калибруется при помощи лабораторного оборудования на основе оценки уплотнения контрольного участка, по которому каток выполняет несколько проходов до необходимой степени уплотнения материала.
Подчеркнем, что все описанные системы измеряют степень уплотнения грунтов, но не горячей асфальтобетонной смеси. В процессе изменения температуры качество и свойства асфальтобетонных смесей сильно изменяются. Через какое-то время после прохода катка характеристики смеси существенно изменятся и результаты измерений будут неактуальны. Поэтому имеет смысл измерять уже результат работы, а не делать измерения в процессе уплотнения.
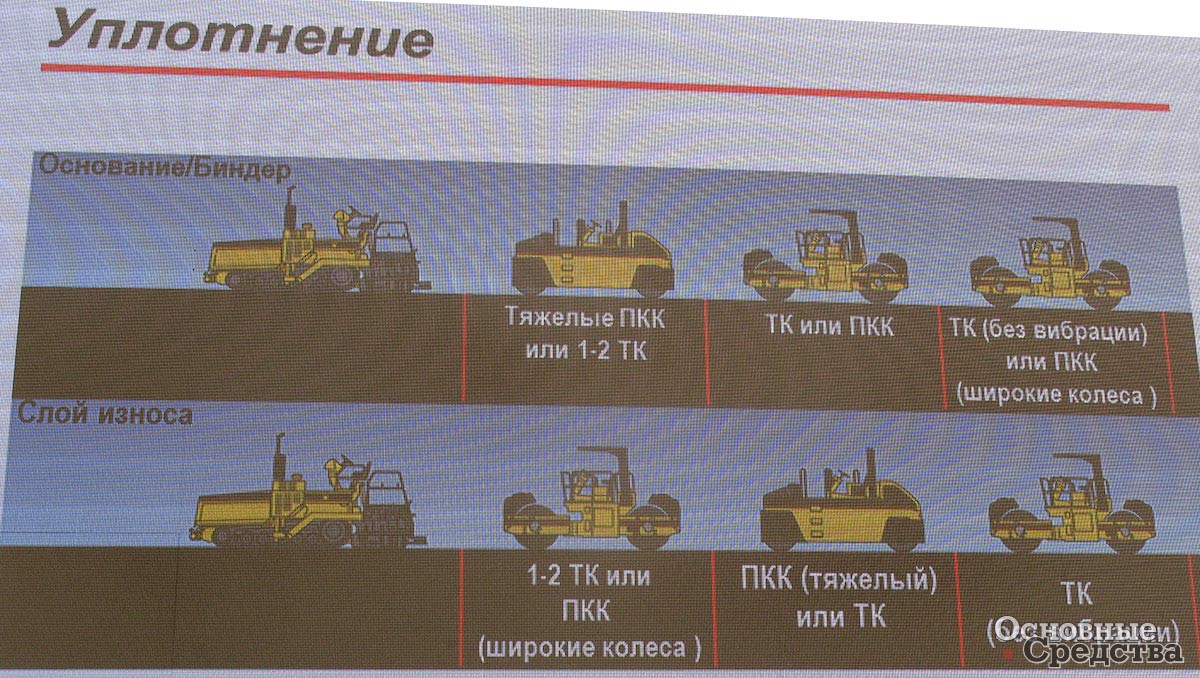
Степень уплотнения смеси зависит от ее температуры, параметров вибрации вальца и статической линейной нагрузки. Все это учитывается при выборе амплитуды уплотняющего воздействия, а также такие факторы, как толщина слоя, отношение номинального размера фракции к толщине слоя. На слайде несколько примеров подбора асфальтоуплотняющей техники в зависимости от того, это слой основания, биндер или слой износа. Процесс уплотнения можно разделить на 3 этапа.
1)Первоначальный, при котором достигается максимальная плотность. Смеси Superpave содержат модифицированный битум и чем ниже температура этих смесей, тем сложнее их уплотнять. Чтобы достичь необходимой плотности, нужно уплотнять смесь быстро. Поэтому при укладке данных смесей сразу после асфальтоукладчика идут тяжелые тандемные катки.
2)Промежуточный этап. Тут можно использовать пневмоколесные катки.
3)На финишном этапе в зависимости от того, что это за слой, также могут использоваться пневмоколесные катки. При уплотнении основания или биндера допускается использование пневмоколесных катков с широкими колесами. Естественно, при уплотнении верхнего слоя и слоя износа нельзя использовать пневмоколесный каток.
В отрасли имеется тенденция к увеличению использования тяжелых пневмоколесных катков. Некоторые производители, и в т. ч. Caterpillar разработали специальные компьютерные программы для подбора моделей катков, амплитуды вибрации и других параметров процесса уплотнения для определенных смесей. Также имеется приложение для смартфона, которое помогает построить график укладки таким образом, чтобы уплотнять слой асфальтобетонной смеси при определенных температурах и не попадать в температурный диапазон «зоны податливости», при этом обеспечивая непрерывную подачу при подобранной оптимальной скорости укладки.
Интеллектуальное управление парком техники
На слайде приведен неполный список самых распространенных цифровых технологий Caterpillar по управлению парком техники. Первая в этом списке — технология Caterpillar Link, которая предназначена для управления парком техники, косвенно может влиять на производительность, безопасность и экологичность. Caterpillar производит телематические устройства-блоки небольшого размера Product Link. Линейка телематического оборудования Product Link достаточно широка. Оно может устанавливаться не только на машины крупные, средние и малые, но и на навесное оборудование, на строительную, горнодобывающую, энергетическую технику, подключается к питанию и шинам CAN, собирает информацию о работе машины, определяет свое местоположение по GPS (ГЛОНАСС — в перспективе), эти данные передает по сети сотовой связи или через спутники на серверы хранения данных несколько раз в день. По GSM данные передаются гораздо чаще — через каждые несколько минут, частота передачи зависит от объема данных. Оттуда эту информацию можно считать и делать с ей, что нужно, например, визуализировать посредством различных on-line систем. В компьютере руководителя день за днем создается база данных, которые потом можно анализировать. С 2017 г. разработана новинка —упрощенная система ProdLink для компактных машин, имеющих двигатели с механическим управлением. Телематическая система может фиксировать и передавать ограниченное число параметров: местоположение машины и «двигатель включен-выключен». Сейчас эта система проходит сертификацию и после ее получения будет поставляться на всех машинах Cat.
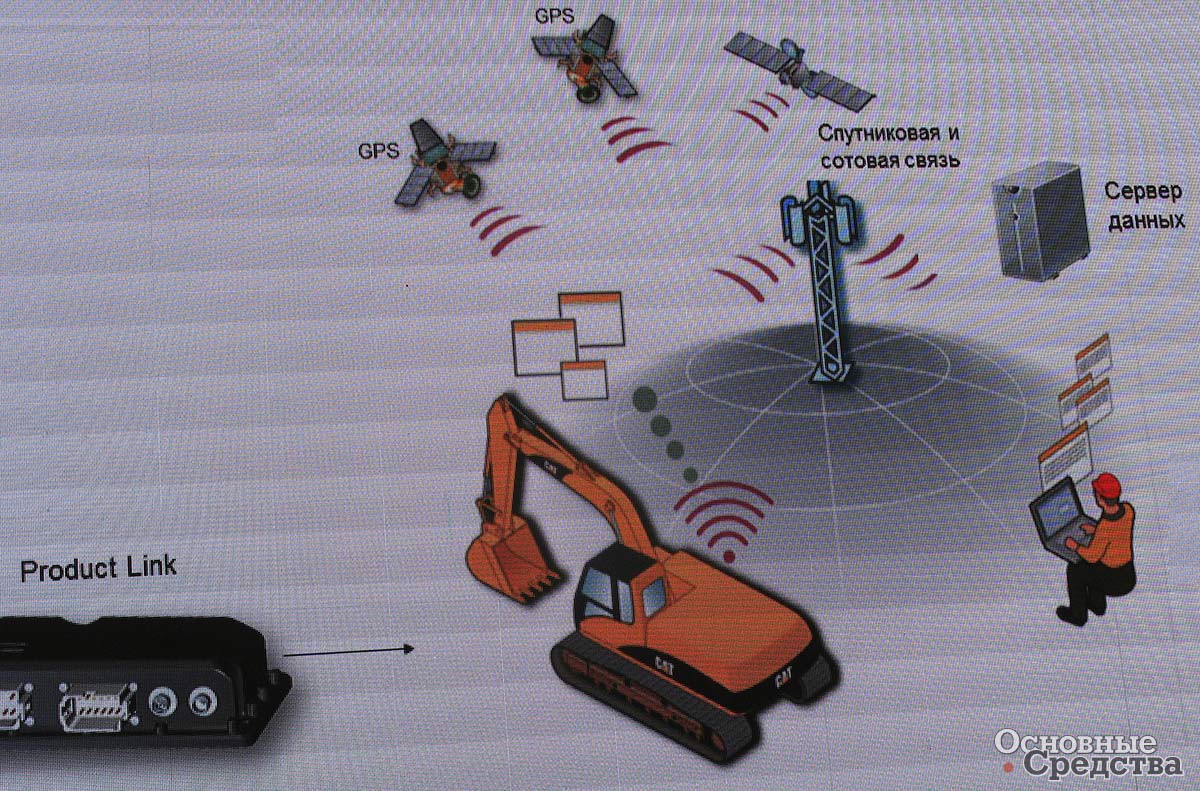
Самая распространенная из линейки Product Link — VisionLink, флагманская версия, которая объединяет в себе множество функций просмотра, позволяет заблаговременно выявить неисправность и сокращает затраты на ремонт. Можно выявить машины, которые много времени работают на холостом ходу. Также у Caterpillar имеется ряд других систем – например, PL Web, версия, адаптированная для энергетических установок, ее функционал отличается от VisionLink.
Недавно Caterpillar разработал новую on-line систему: my.cat.com – ее можно открыть в любом вэб-браузере, это система среднего класса по отношению к премиум-системе VisionLink с небольшими ограничениями — например, данные с электронных блоков обновляются всего 1-2 раза в сутки, но по опыту для многих клиентов этого достаточно. Данные представляются в интуитивно-понятном виде таблиц и графиков. Система переведена на русский язык. Можно видеть, какие были коды неисправностей, результаты анализа технических жидкостей, расход топлива, время работы под нагрузкой и на холостом ходу и т. д. Нажатием одной кнопки владелец может заказать проведение ТО или ремонта. На технику, приобретенную с 1 января 2017 г. предоставляется бесплатная 5-летняя подписка на эту систему. Какие же преимущества обеспечивает данная система?
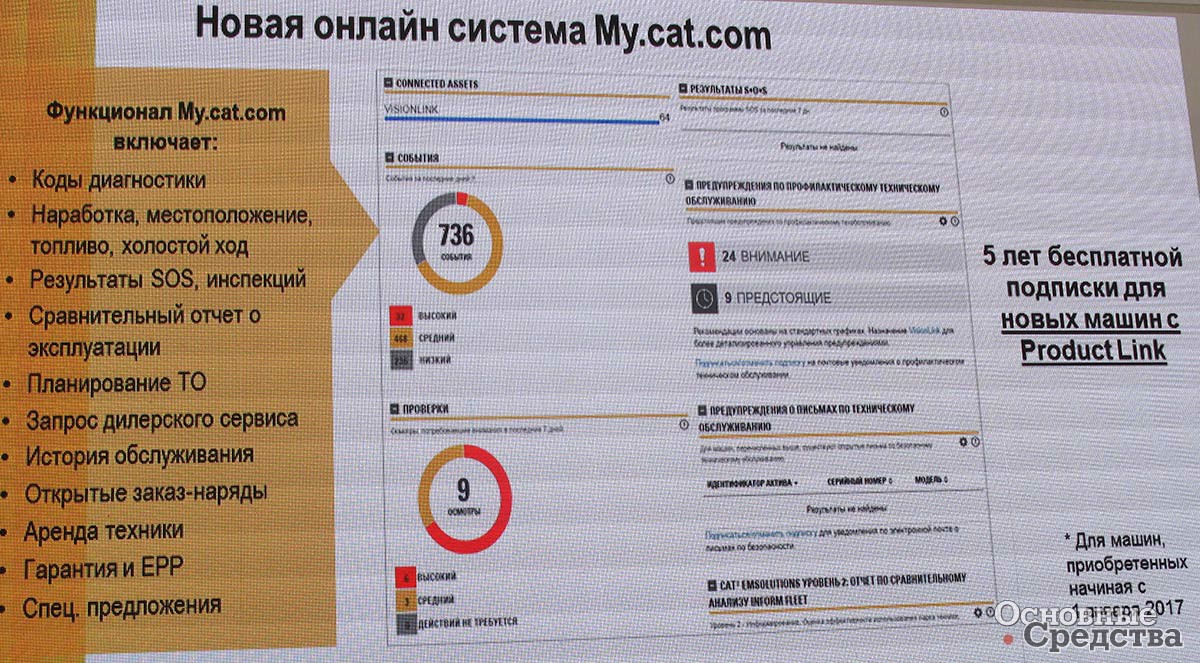
1)Снижение расходов: показывается время работы на холостом ходу и его можно снизить, получается экономия до 9% топлива. Можно видеть состояние техники и предотвратить дорогостоящие ремонты, сэкономив 50% расходов и более.
2)Управление парком техники: всегда видно, где работает техника, как, какая работает больше и правильно распределять нагрузку, перебрасывать на другие участки, планировать ТО в удобное время, получается экономия на обслуживании, запчастях и расходных материалах. При использовании программы отбора проб масел SOS можно увеличивать интервалы техобслуживания, в основном это актуально для гидравлической жидкости и тоже дает немалую экономию.
3)Управление персоналом: система показывает ошибки операторов, какие операторы совершают больше ошибок.
4)Снижение рисков опасных поломок, предотвращение выезда техники за пределы рабочей площадки и выполнение операторами «левых» работ. Уведомления могут поступать в виде СМС или e-mail. Точнее расчеты на расход топлива и прочие ресурсы, это очень удобно для участия в тендерах.
В разработке у специалистов Caterpillar находятся программы, при помощи которых можно будет дистанционно подключаться с диагностическим оборудованием к новым сменным рабочим органам машины. В результате уменьшится количество выездов механиков на место, диагностика будет выполняться быстрее. За счет применения таких программ повышается стоимость машины на вторичном рынке.
Предложение Caterpillar по сервису теперь оптимизировано до 3-х уровней (вместо прежних 5-ти).
1)«Информация»: при помощи телематической системы Product Link ежемесячно автоматически рассылаются отчеты, информация о показателях машин, но все решения по обслуживанию парка и проведению ТО принимает сам руководитель и сервисная служба парка. Поэтому данный уровень сложен для руководителя.
2)«Советы»: квалифицированный сервисный аналитик от дилера Caterpillar на основе различных данных и знания техники может порекомендовать, как можно оптимизировать работу и как привести технику в исправное состояние. Но окончательное решение остается за клиентом.
3-й уровень - «Партнер»: дилер сам выполняет необходимое обслуживание по договору, предоставляются запчасти, увидев сигнал о неисправности механик выезжает и выполняет необходимое обслуживание, возможна гарантия на коэффициент технической готовности машин.
АСУ ремонта и восстановления техники
Все технологии и услуги, которые позволяют увеличить эффективность работы техники на строительном объекте объединены под общим брендом CatConnect. Неотъемлемой частью технологий CatConnect является ремонт и восстановление машин. Машины должны быть в исправном состоянии, чтобы они могли реализовать свою максимальную производительность.
«Вторая жизнь» машины или компонента обеспечивается путем ее сертифицированного восстановления. «Сертифицированное Caterpillar восстановление строительной техники» - уникальный продукт. Программа началась в 1985 г., изначально была разработана для горнодобывающей отрасли, но с течением времени по запросам клиентов и дилеров была расширена практически на всю линейку машин Caterpillar. Чем крупнее и дороже машина — тем экономически выгоднее проводить ее восстановление. Сертифицированное восстановление (а не просто ремонт) начинается примерно с машин массой 25-30 т. Могут восстанавливаться и более легкие машины, но массово это относится к указанной границе — свыше 25-30 т. Сегодня лишь самые малые машины и машины для дорожного строительства не входят в эту программу.
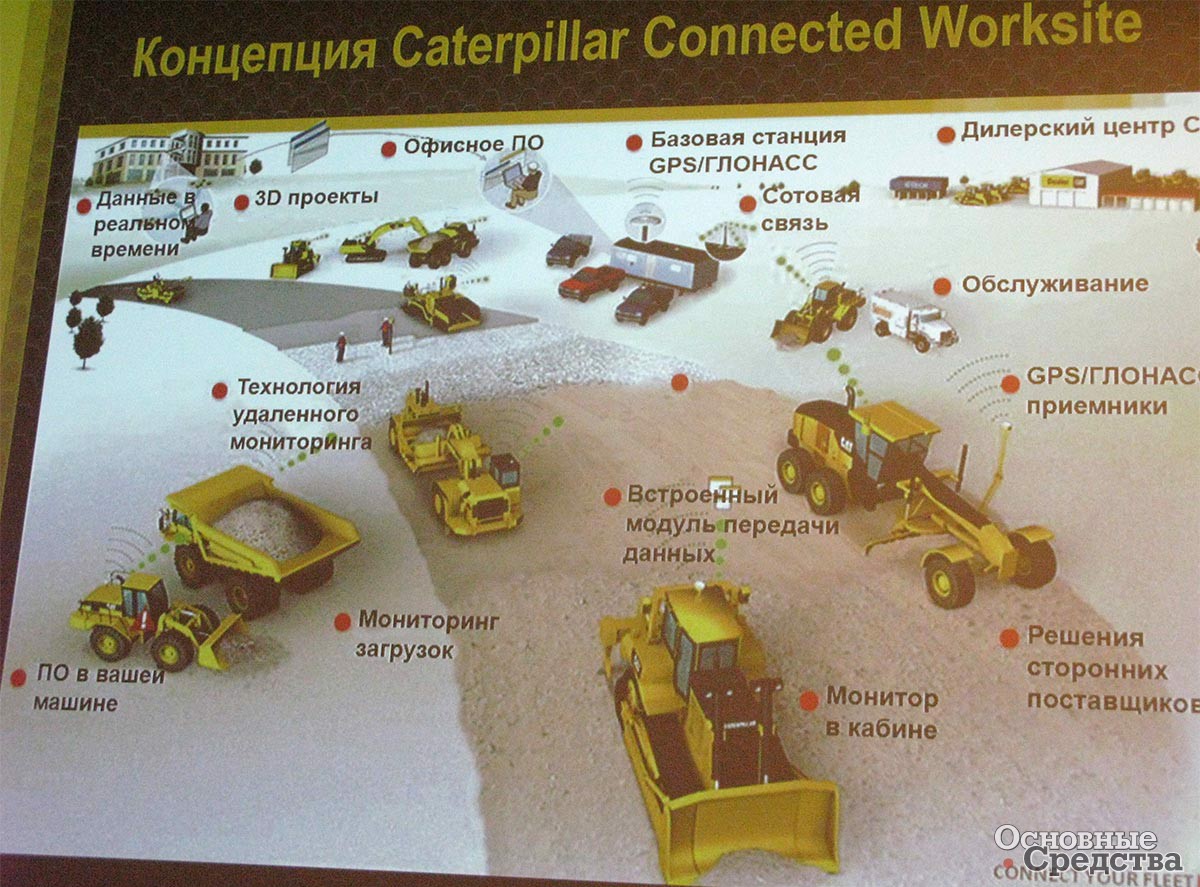
Certified Rebuild (около 10% всех таких работ, выполненных на территории СНГ). Восстанавливается вся машина целиком. Заказчик получает машину в состоянии новой не только внешне, но и по рабочим характеристикам и даже может получить новый порядковый заводской номер. Гарантия — как на новую машину, 12 месяцев без ограничения наработки, можно продлить гарантию до 5 лет либо 10000 моточас. Компания разработала спецификации по ремонту практически на каждую машину существующей линейки, т. е. все дилеры выполнят этот ремонт единообразно по одним и тем же техническим документам и требованиям. В конструкцию ремонтируемой машины будут вноситься все обязательные инженерные улучшения, которые выпускались с момента приобретения данной машины. Например, отдав на ремонт 8-летнюю машину, вы получите ее уже со всеми новыми, появившимися за эти годы системами безопасности, с усовершенствованиями в кабине, повышающими комфортность условий, с повышением производительности и топливной экономичности.
Certified Powertrain Rebuild (около 40% всех работ по программе Rebuild ). Восстановление силовой линии: двигатель, трансмиссия, гидротрансформатор, гидромоторы, мосты с бортовыми передачами, все основные компоненты, отвечающие за движение машины и работу ее навесного оборудования. Кабина не восстанавливается, машина не красится, новый порядковый номер не выдается. Но ресурс машины существенно увеличивается — вплоть до «как у новой». Удобно, когда уже не выпускается машина в такой комплектации, а она встроена в технологический процесс — восстанавливают старую и не нужно ничего перестраивать. Можно произвести «апгрэйд» машины — например, установить более мощный двигатель новой модели.
Certified Component Rebuild - сертифицированное восстановление отдельных компонентов (около 50% работ). Восстанавливаются и даже изготавливаются на заказ практически любые компоненты двигателя, трансмиссии, бортовых передач, снятые с производства. Компании приходилось изготавливать детали даже с помощью 3D-принтера, т. к. уже не было таких поставщиков. Возможны варианты расширенной гарантии на 5 лет или на 10 тыс. моточасов.
В России и СНГ самые популярные виды восстановления: Powertrain Rebuild и Component Rebuild. И самый востребованный — это двигатель. А трансмиссию достаточно просто отремонтировать на уровне дилерского ремонта.
Имеются различные опции ремонта компонентов по фиксированной стоимости. Эта программа сейчас внедряется у всех дилеров Caterpillar по всему СНГ. Это ремонты сравнительно небольшого объема и короткие по времени, фиксированного объема с простой и предсказуемой схемой оплаты, можно удобно планировать расходы на него. Объем запчастей и сервиса фиксирован. Такие ремонты дают машине возможность доработать какой-то срок, выполнить какую-то срочную работу, доработать второстепенному компоненту до окончания ресурса важного агрегата — двигателя, трансмиссии. Уровень надежности зависит от выбранного уровня ремонта.
Первые два уровня ремонта направлены на продление срока службы компонента, когда машина находится на середине рабочего цикла, у компании контракт на какую-то работу и при наличии некоторых признаков неисправности — например, повышение расхода топлива, подтекание масла, изменение цвета выхлопных газов — можно эти проблемы минимизировать, выполнив ремонт по одному из первых двух уровней. А когда проект будет выполнен, провести уже полноценный ремонт.
Следующие три уровня — с 3 по 5-й направлены на то, чтобы обеспечить новую жизнь неисправному компоненту. 3-й уровень — дилерское восстановление. Стоимость восстановленного компонента составляет 30-50% от нового в зависимости от состояния исходного узла. Даже при дилерском восстановлении гарантия идет такая же, как на новые детали, гарантируется такой же ресурс, как у новых деталей.
На 4-м уровне Reman предлагается замена на компонент, восстановленный по технологии Reman на заводе Caterpillar до состояния нового. Заводы у Caterpillar имеются и в Великобритании, и в США. Преимущество — быстрая замена и ввод машины в строй, если агрегат Reman имеется на складе. На детали, восстановленные по программе Reman дается такая же гарантия, как на новые детали, а цена ниже за счет того, что компонент обменивается на неисправный.
А 5-й уровень — замена компонента на новый, это в случае, когда необходимо выполнить ремонт очень быстро и надежно.
Правительством поставлена задача привести к 2018-2022 гг. федеральные дороги в России в нормативное состояние. Применение в дорожно-строительной отрасли передовых инновационных технологий, в частности таких, которые были представлены на семинаре Caterpillar, позволяет осуществить эти планы.