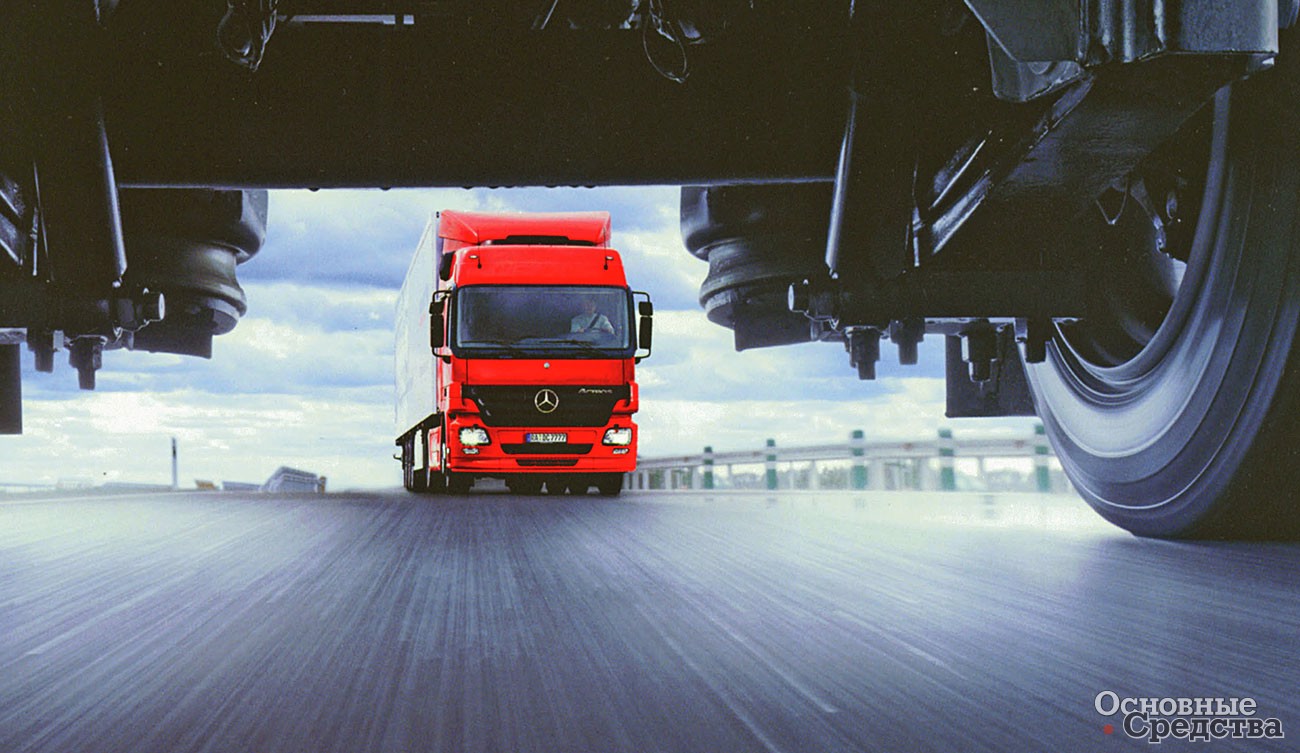
Восстановление шин
Обзор способов продлить ресурс шины
Шина приходит в негодность по двум главным причинам. Одна из них – максимальный износ рисунка протектора, другая – разрушение каркаса. Износ рисунка проектора изменяет поведение шины. Ухудшаются ее сцепные качества, а значит, и безопасность, особенно при движении по мокрой дороге. Встает вопрос: может быть, вообще нужны шины с увеличенной высотой протектора? Действительно, казалось бы, чем толще протектор, тем лучше. Но это совсем не так. Исследования показали, что самые первые миллиметры протектора изнашиваются в полтора, а иногда и в два раза быстрее, чем это требуется последним миллиметрам. Свойства резины здесь не причем. Выяснилось, что чем выше рисунок протектора, тем сильнее он изнашивается, да и топлива при этом расходуется больше. Интересно, что грузовик с изношенными шинами на 7…10% экономичнее своего «собрата», обутого в новую резину. Описанная ситуация складывается из-за повышенных вибраций и увеличенного нагрева шины с новым протектором. К тому же инерционные силы приводят к дополнительной деформации высокого протектора. Чтобы избежать этих негативных моментов, современные грузовые шины имеют относительно небольшую глубину протектора, но зато увеличенный подканавочный слой, а благодаря восстановлению за небольшие деньги пробег шины увеличивается порой до 40%. Делают этой с единственной целью – увеличить ходимость шины с помощью ее нарезки на последних этапах эксплуатации.
Нарезка канавок
Суть этого способа состоит в углублении имеющегося рисунка протектора, когда беговая дорожка изношена до 3…4 мм. Узнать, подходит ли данная шина для такой процедуры, просто. Достаточно взглянуть на боковину покрышки и найти надпись «Regroovable». Если она на месте, можно смело браться за дело. Лучшим помощником здесь, как уже отмечалось, является толстый слой специальной резины, находящийся под протектором. Если разобраться повнимательнее, то упомянутый слой не что иное, как часть протектора, изначально предназначенная для продления срока службы шины. Практически все ведущие изготовители шин на своих изделиях предусматривают такую возможность. Современные шины некоторых отечественных заводов также можно подвергать нарезке.

Безусловно, эту операцию должны проводить квалифицированные специалисты с использованием соответствующего оборудования и инструмента. Для нарезки применяют специальный аппарат, представляющий собой обыкновенный трансформатор, который вырабатывает ток большой величины для разогрева профилированного термоножа из специальной стали. Работа не требует специального помещения, а для нарезки одной шины при умелом обращении с резаком требуется не более часа. Прежде чем приступить к углублению протектора, шину осматривают, чтобы убедиться в отсутствии повреждений, таких как трещины, многочисленные порезы, разрывы блоков протектора. Если их нет, можно быть уверенным в успехе мероприятия. Ширина нарезки (7…10 мм) и ее глубина (2…5 мм) учитывает каждый типоразмер и особенности рисунка протектора. Обычно после окончания работы над брекером остается 2…3 мм резины для защиты каркаса шины. Необходимая информация о нарезке приводится в фирменных каталогах.
Чрезмерное углубление приводит к отрыву грунтозацепов, разрушению каркаса и невозможности дополнительной наварки шины. Зато соблюдение технологии заметно продлевает жизнь шине, пробег которой увеличивается не менее чем на 10%. На столько же снижаются расходы на обновление шин.
Нельзя забывать и том, что шины с углубленным рисунком протектора методом нарезки согласно российским Правилам эксплуатации автомобильных шин не допускаются к установке на переднюю ось грузовых автомобилей. Не стоит и экспериментировать, подвергая нарезке обычные шины, при этом ссылаясь на то, что на ряде моделей российских шин несколько завышена толщина подканавочного слоя. Последствия таких действий могут быть опасными.
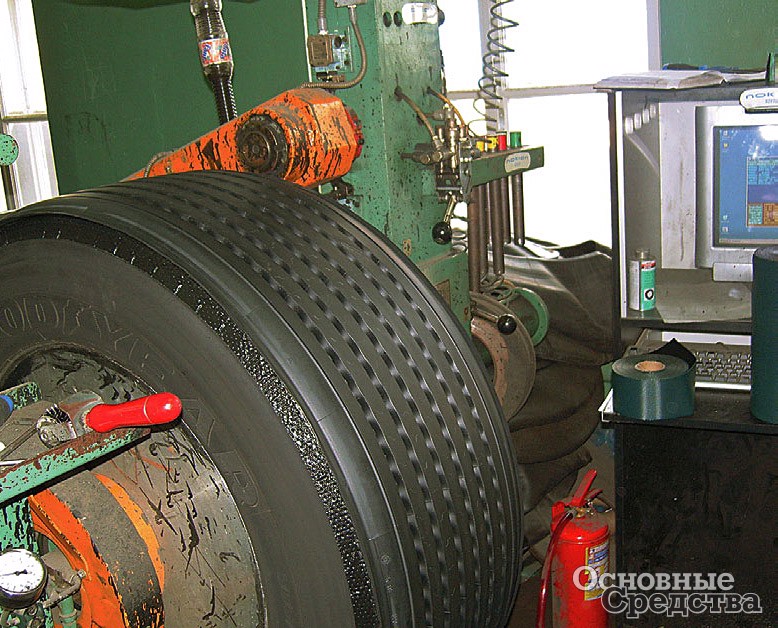
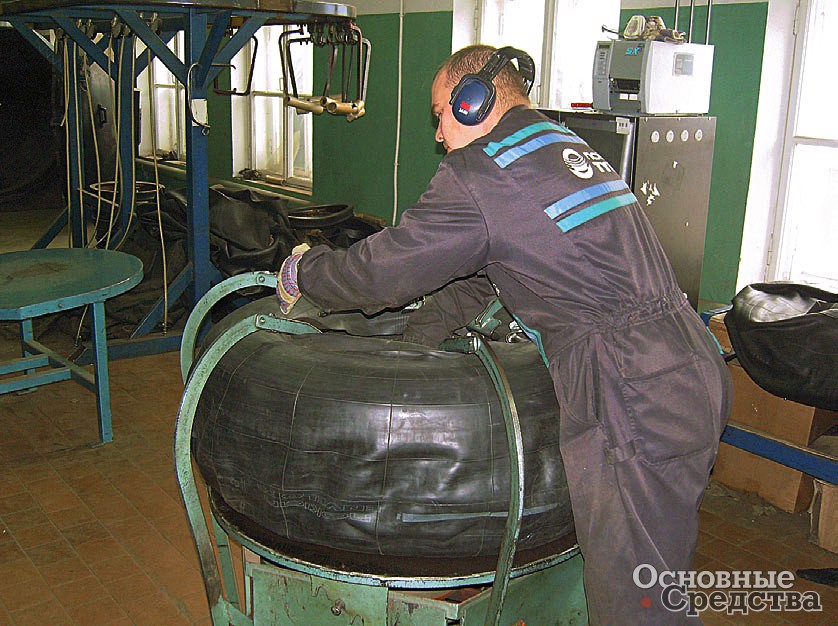
Вторая жизнь шины
Одним из действенных способов продлить ресурс шины является ее восстановление наваркой. Во всем мире восстановлению шин придают огромное значение. Более того, в экономически развитых странах грузовики, а также прицепной состав, находящиеся в эксплуатации, на 40…70% комплектуют восстановленными шинами.
В настоящее время существуют два основных способа восстановления шин наваркой – горячий и так называемый холодный. Оба они подразумевают присоединение к изношенной покрышке нового протектора методом вулканизации. В первом случае температура нагрева достигает 120…160 °С, во втором – 100 °С.
В нашей стране восстановленные шины получают горячим методом. Их ходимость и цена приблизительно в два раза меньше, чем новых. Более высокие показатели присущи оборудованию по восстановлению шин производства западных компаний. Сегодня лидерами в этой области являются такие фирмы, как Bandag, Maragoni, Goodyear, Nokian, Kraiburg, Kargro, Cima. Достижения современных технологий значительно повышают качество восстанавливаемых шин.
Производственный цикл восстановления холодным способом состоит из нескольких основных операций. Первая – это контроль состояния каркаса перед началом процесса восстановления. Затем происходит шероховка каркаса до опасной толщины резины над первым слоем корда, не более 1...1,5 мм, потому что каждый дополнительный миллиметр, оставленный над слоем корда, дает дополнительный нагрев резины в этом слое на 5 °С, что имеет большое значение при движении летом в жарком климате. Если не выдерживать этот параметр, возможен перегрев и отслаивание протекторной ленты. И только после шероховки шины можно окончательно дать заключение – пригодна она к восстановлению или нет, поскольку только в этом случае открываются все дефекты, которые накопились за период эксплуатации в результате механических повреждений. Кроме того, становится видна коррозия, если шины, имеющие повреждения, эксплуатировали достаточно долго.
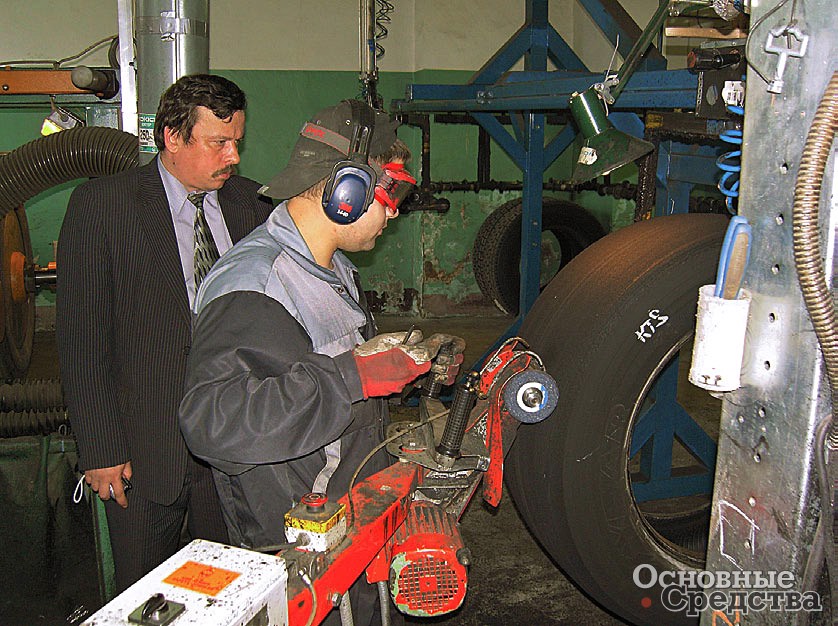
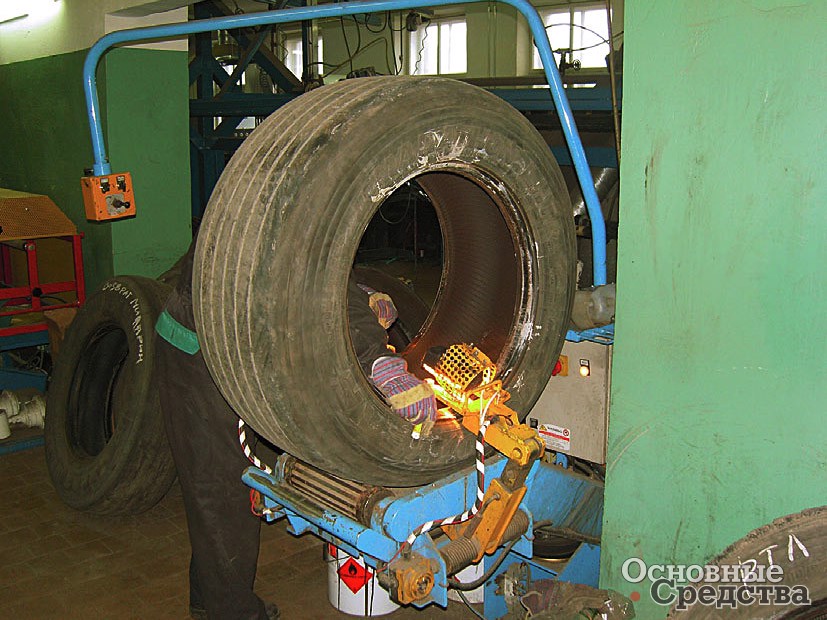
Следующей операцией является разделка и ремонт поврежденных участков, выявленных при шероховке. Каждый поврежденный участок тщательно разделывают и закрывают дополнительным пластырем из сырой резины. Затем в специальной камере наносится связывающий раствор, который укрепляет связь между каркасом и соединительной резиной. Следом за этим на подготовленный каркас наносят слой соединительной резины и нового протектора. Надо подчеркнуть, что именно химический состав соединительной резины является ноу-хау каждого производителя материалов для восстановления шин. Например, при холодном способе восстановления температура вулканизации составляет всего 100 °С. Таким образом, этот процесс не ускоряет сколько-нибудь существенно старение резины, каркаса и протектора. При горячем способе наварки температура достигает 123…125 °С и выше. В результате после вулканизации резина каркаса стареет, покрывается сеткой мелких трещин, сам каркас частично утрачивает эластичные и прочностные свойства.
После того как произведена операция наложения протектора на подготовленный каркас, шину помещают в оболочку, затем эту оболочку подключают к вакуумной системе и из-под оболочки откачивают воздух, после чего колесо оказывается в автоклаве.
По внешнему виду восстановленные шины не отличаются от новых. Для восстановления используют высококачественные материалы от известных поставщиков. На всех стадиях очень точно соблюдается технология.
О надежности восстановленных шин
Из опыта работы следует, что брак составляет 0,06%, и то все случаи возникли по причине разрушения каркаса и дефекта, который был пропущен при осмотре колеса. Конечно, не все можно продефектовать, но надежность качественно восстановленной шины соизмерима с надежностью нового изделия. По опыту эксплуатации можно констатировать тот факт, что при установке на ведущем мосту автомобиля и осях полуприцепа восстановленные шины проходят 180…200 тыс. км. В отдельных случаях ходимость восстановленной шины такая же, как у новой, а стоимость на 15% ниже.
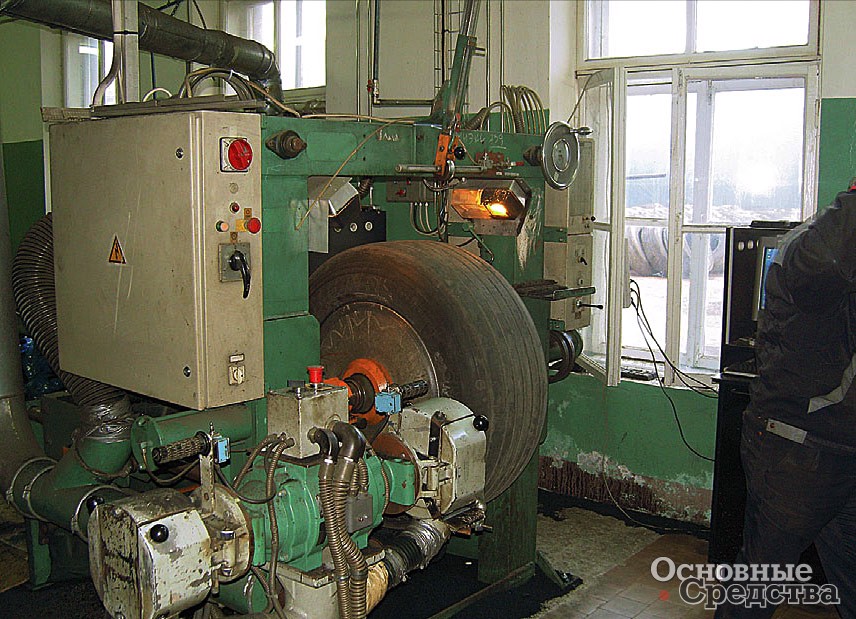
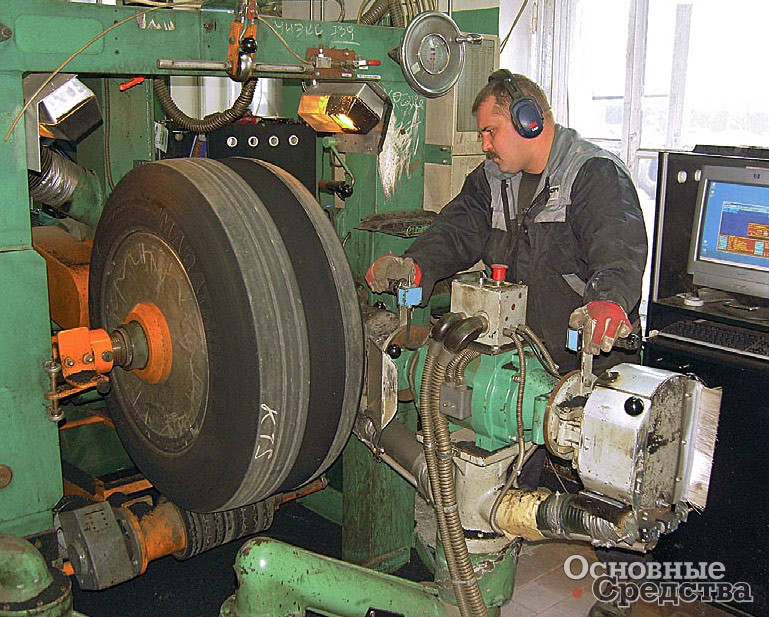
При горячем способе восстановления после процессов дефектовки, мойки и сушки производится срезание старого протектора и шероховка поверхности. Обработанная покрышка позволяет провести окончательный контроль с использованием сканеров разного типа. Затем на зашерохованную часть распыляют клеевой раствор и наносят промежуточный тонкий слой соединительной резины.
Протектор можно наносить двумя способами. Первый предусматривает наложение одного слоя толстой нерифленой резины и невулканизированной протекторной ленты. Второй способ заключается в навивке нескольких слоев жгута из невулканизированной протекторной резины. После этого покрышку с новым слоем укладывают в специальный формовочный аппарат, где и происходит вулканизация и опрессовка протектора. Технология изготовления близка к той, что используется при производстве новых шин. Пробег шин, восстановленных по такой технологии, составляет 60…80% пробега новых шин.
Теперь приведем ценовой баланс. Среди некоторых перевозчиков бытует мнение, что лучше всего ездить на дорогих, но надежных шинах верхнего по качеству изготовления эшелона брендов, таких как Michelin, Bridgestone, Continental, Goodyear, Pirelli и др. Вместе с тем ходимость восстановленных импортных шин на хороших каркасах (Michelin, Bridgestone, Continental) больше, чем новых шин, более низкой ценовой группы, таких как Kormoran, Barum, Matador. Из опыта эксплуатации, например, для шин размера 385/65 Р22,5 пробег новой покрышки Michelin составляет примерно 250 тыс. км, аналогичные цифры для нового Barum – 160 тыс. км, восстановленные шины в среднем проходят по 190 тыс. км. Посмотрим, сколько стоит 1000 км пробега. Оказывается, что самое дорогое соотношение цены на 1000 км пробега имеют шины брендов условно третьего класса, таких как Kormoran, Barum, Matador. Несколько дешевле покупать и ездить на Michelin. И самыми выгодными в эксплуатации оказываются восстановленные шины. Причем, их эксплуатация дешевле приблизительно на 50%.
