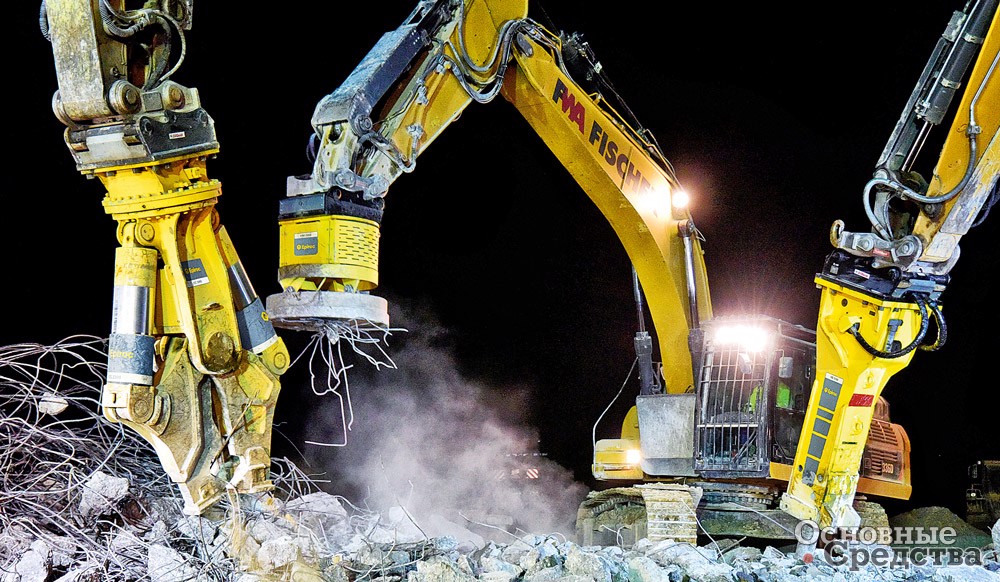
Обзор новых моделей навесного оборудования для спецтехники
Значимым событием последнего времени стало объявление одной из ведущих компаний по производству навесного оборудования Atlas Copco о завершении формирования бренда Epiroc. Название бренда состоит из сочетания греческого epi – «близко», и латинского rocca, что переводится как «скала». Новая компания, в которую вошло подразделение гидравлического навесного оборудования Atlas Copco, возникла в результате разделения бизнеса индустриального лидера в области горнодобывающих технологий и машиностроения Atlas Copco на два независимых направления.
Целью разделения ставилось повышение эффективности сотрудничества с заказчиками за счет фокусирования на целевой группе клиентов. Таким образом, компания Epiroc с годовым оборотом 3 млрд евро и штатом более чем 11 000 работников сосредоточится на горнодобывающем оборудовании. Epiroc выходит на рынок как обновленная инновационная международная компания с глобальными ресурсами. Новая структура позволит быстрее принимать решения и реагировать на рыночные изменения. Россия объявлена одним из ключевых рынков для компании Epiroc.
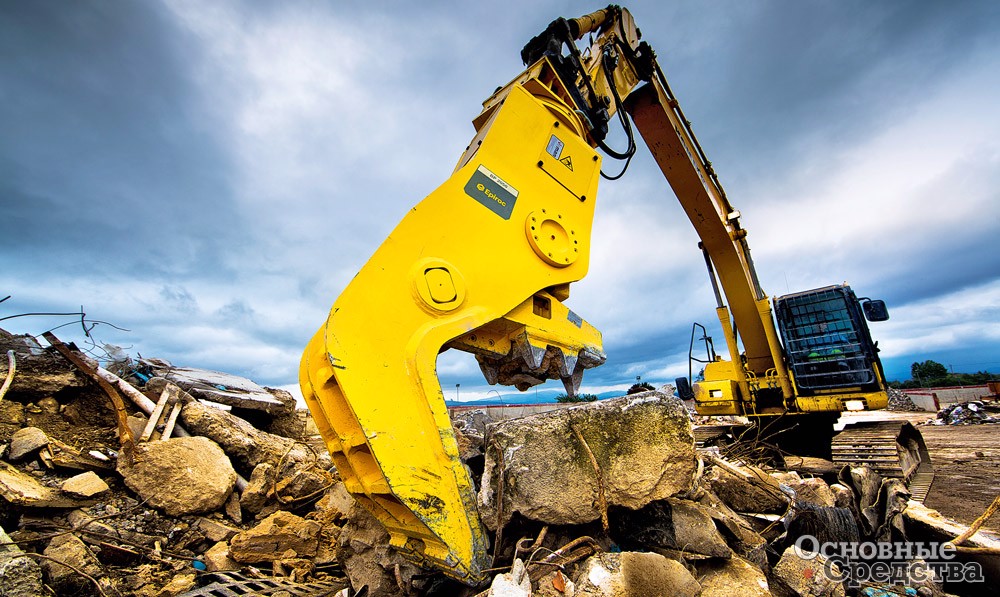
Отличительной особенностью оборудования Epiroc является его бесперебойная работа, которая обеспечивается круглосуточной доступностью запчастей и высоким уровнем клиентского сервиса. Продукция компании Epiroc превращает машину-носитель в универсальный инструмент для выполнения множества задач, например, для сноса и реновации. Множество старых зданий требуют сноса для освобождения пространства для новой инфраструктуры.
Одной из проблем, с которой сталкиваются горнодобывающие предприятия, расположенные в освоенных промышленных районах, является ограничение на ведение взрывных работ. Поэтому в этом случае при добыче полезных ископаемых целесообразно использовать гидромолоты. Кроме того, данный инструмент используется для строительных работ, устройства траншей для прокладки трубопроводов, в металлургии для переработки материалов и для подводных работ по углублению дна в портах и на реках.

Мощность одного удара гидромолота Epiroc HB10000 эквивалентна давлению, которое создается при посадке аэробуса А380. А он наносит 380 таких ударов в минуту. Тяжелые гидравлические молоты Epiroc, которые монтируются на мачту, оснащаются интеллектуальной системой защиты (IPS). Системы AutoControl и StartSelect были внедрены на гидромолотах Atlas Copco несколько лет назад, но сейчас в Epiroc их объединили с IPS, что гарантирует запуск гидромолота в режиме AutoStart. Когда контактное давление пики увеличивается, AutoControl переключает ход поршня с короткого на длинный.
Система IPS автоматически переключается в режим AutoStop. Когда пика прорывается сквозь материал, гидромолот автоматически отключается и предотвращает работу вхолостую. IPS упрощает работу оператора и автоматически адаптирует рабочий режим к любым условиям. При этом сокращается время простоя, поскольку не требуется вмешательства оператора. Модели гидромолотов Atlas Copco HB 2000, HB 2500, HB 3100, HB 3600 и HB 4700 уже оснащены системой IPS. Остальные гидромолоты получат данную опцию в течение 2018 г. Навесные фрезы Epiroc могут работать под водой на глубине до 30 м без дополнительной доработки.
К одной из самых интересных тенденций последнего времени можно отнести распространение тилтротаторов. Еще сравнительно недавно их использовали в основном в странах Северной Европы, но сейчас полезность этих устройств, которые служат для вращения навесного оборудования в двух плоскостях, признана и за пределами этих стран.

Чтобы удовлетворить растущий спрос и сократить сроки поставки, один из ведущих производителей данного вида оборудования – шведская компания Engcon построила недавно новый завод. Этим летом будет запущен в производство новый тилтротатор Engcon EC233 для экскаваторов массой до 33 т. Эта модель второго поколения с углом наклона 45° обладает прочной конструкцией, оборудована централизованной системой смазки и износостойкими подшипниками вала для увеличения срока службы. EC233 также подготовлена для работы с системой позиционирования Engcon ePS. Сигналы от ePS передаются в бортовую информационную систему экскаватора. Engcon стремится к тому, чтобы как можно больше бортовых информационных систем различных производителей могло обмениваться информацией с ePS.
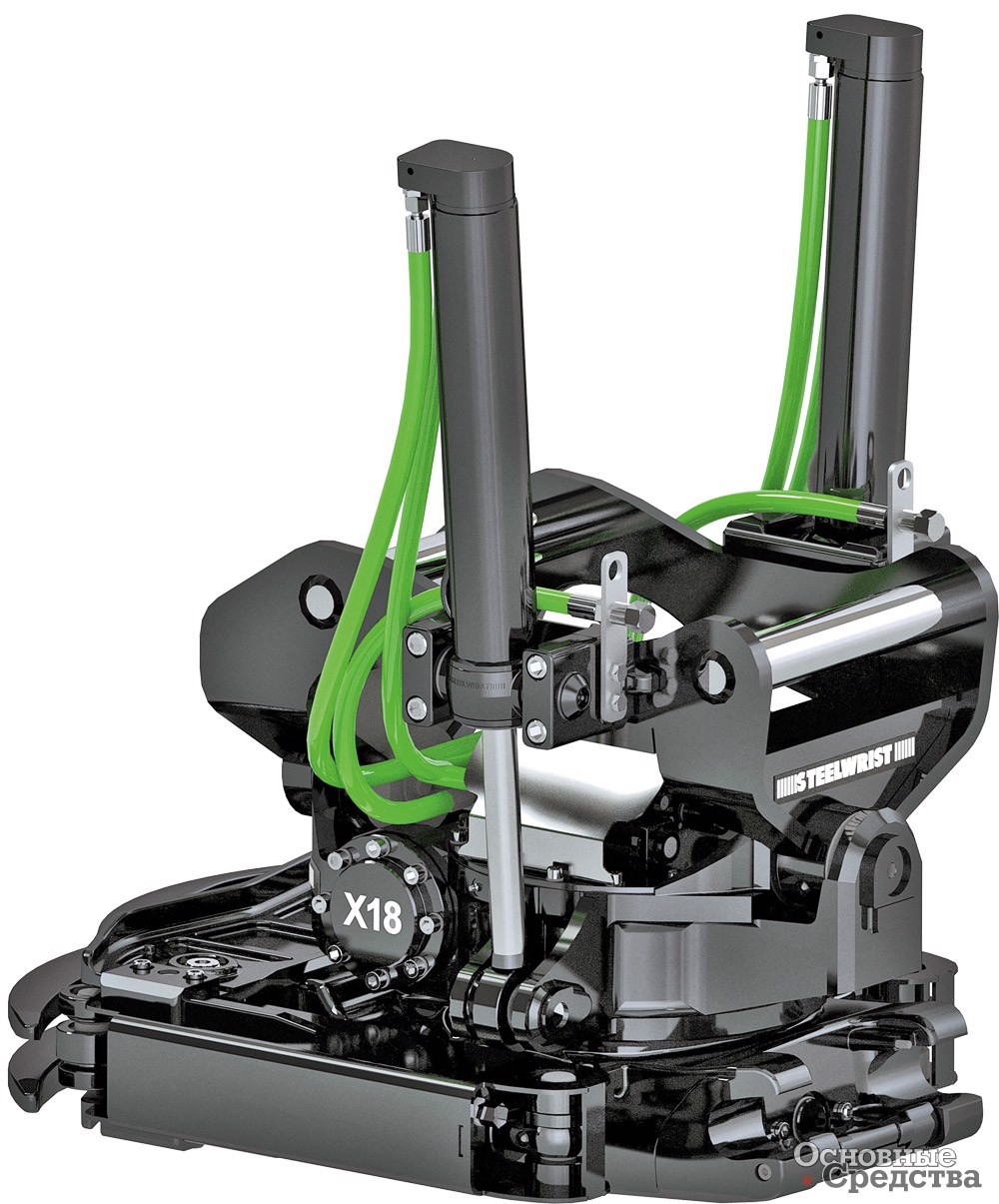
В стандартной комплектации тилтротатор включает в себя наклонные цилиндры с обратными клапанами. Устройство быстрой смены Q-Safe обеспечивает максимальную безопасность за счет системы блокировки QSC, стандартизированной для работы в составе различных машин. Особенностью системы блокировки QSC является требование о положительном давлении на грунт перед началом работы. Это означает, что ковш должен быть помещен на землю до того, как устройство быстрой смены может быть отсоединено, что в свою очередь снижает риск травм, вызванных падением оборудования.
Другой шведский производитель тилтротаторов – компания Steelwrist в ближайшее время тоже планирует расширить свои производственные площади и инвестировать в новое, полностью автоматизированное производство. Steelwrist продает свои продукты в более чем 25 стран мира. Технология Front Pin Lock (FPL), которую разработали в Steelwrist для безопасной смены оборудования, позволяет оператору видеть, когда рабочий инструмент находится в безопасном положении. Красный механический индикатор на устройстве означает, что блокировка снята, а зеленый сообщает о надежном закреплении ковша. Поскольку технология FPL не зависит от датчиков, она позволяет работать со всеми типами систем управления и не зависит от размеров экскаватора или его года выпуска.
Компания Bobcat недавно добавила два типоразмера к имеющейся линейке фрез для использования с мини-погрузчиками Bobcat с усиленной системой гидравлики: PSL50 шириной 50 см и PSL120 шириной 120 см. Эти фрезы дополняют набор навесного инструмента Bobcat для выполнения широкого спектра дорожных работ. Фреза с механизмом бокового смещения и возможностью наклона PSL50 может использоваться с мини-погрузчиками Bobcat S530H, S550H, S570H, S590H, S630H, S650H, S770H и S850H. Фреза SL120 подойдет для моделей S630H, S650H, S770H и S850H. Новые фрезы SLP50 и SLP120 массой 870 и 1145 кг соответственно обеспечивают глубину резки со стандартными барабанами 17 и 13 см. Фрезы имеют гидравлический привод, поэтому все функции можно контролировать с рабочего места оператора. Автоматическая система нивелирования поддерживает постоянную глубину резки независимо от положения фрезы.
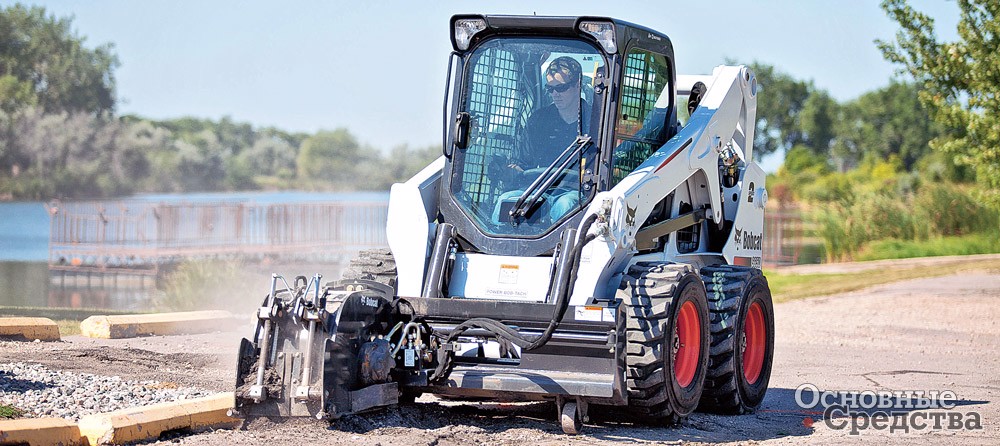
Новейшая разработка финского производителя ALLU – это серия G ковшей Transformer для просеивания и дробления, которая рассчитана на работу с горнодобывающими экскаваторами. Считается, что на сегодняшний день это самое большое в мире подобное устройство массой 32 т, высотой 3781 мм, шириной 4760 мм и глубиной 3746 мм. С помощью ковшей ALLU Transformer серии G обработка и загрузка материалов завершаются за одну стадию. Этот процесс исключает дополнительную перевалку материала, а также уменьшает потребность в промежуточном складировании материалов.
Трансформеры ALLU серий M и G являются универсальными инструментами для горнодобывающей и обрабатывающей отраслей промышленности. Эти гидравлические приспособления, навешенные на экскаватор, помогают предотвратить образование заторов в желобах и другие проблемы с подачей материала, а также облегчают транспортировку замороженных материалов. Это происходит за счет устранения проблемных и разрушающих кусков породы на начальном этапе процесса.
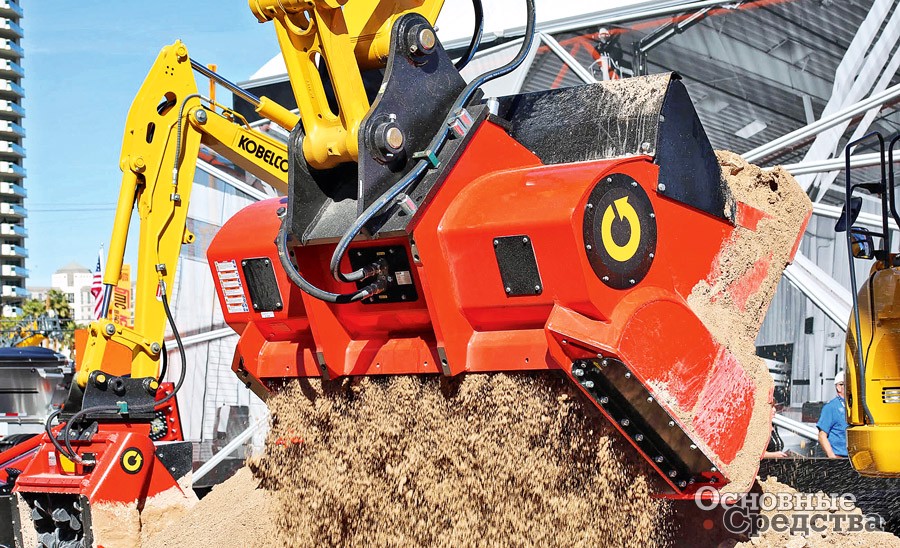
ALLU Processor – это навесной гидравлический миксер, который, как утверждает изготовитель, превращает экскаватор в универсальный инструмент для смешивания различных сложных материалов: от глины, ила, торфа, отстоя до выемного или загрязненного грунта. Мод. 500 HD, работающая на глубине до 5 м, имеет массу 2445 кг (плюс масса монтажной пластины 400 кг). Он может смешивать материалы везде, где пройдет экскаватор. Связующие вещества или химические реагенты подаются в область интенсивного смешивания через трубу диаметром 80 мм методом впрыска через сопло, расположенное между смесительными барабанами.
Устройство оснащено автоматическими клапанами для распределения крутящего момента между двумя гидравлическими двигателями, а также счетчиками оборотов, датчиками температуры и датчиками обнаружения протечек масла внутри корпуса. Оператор экскаватора управляет направлением вращения барабанов, обеспечивая эффективное смешивание. В качестве опции для увеличения рабочей глубины доступны дополнительные трубы длиной 2 и 3 м.
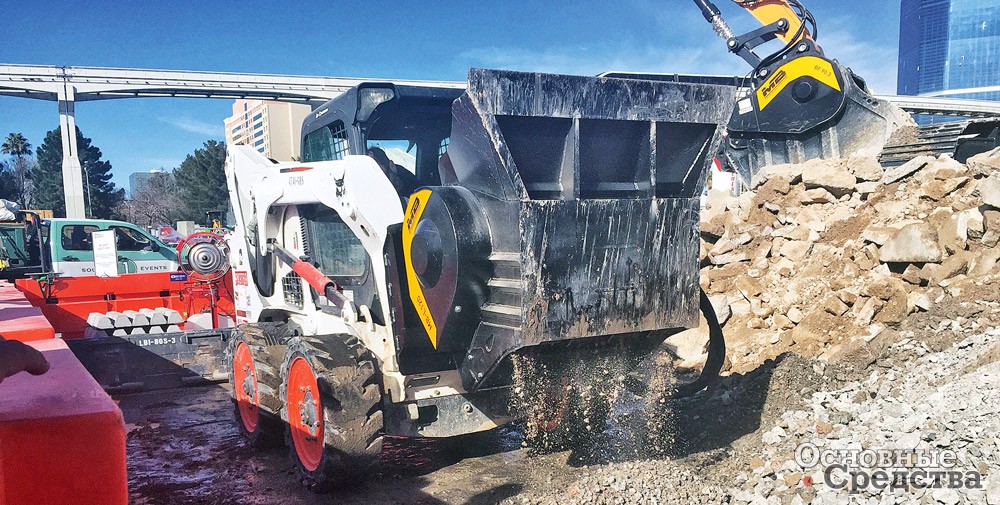
По мнению компании MB Crusher, отходы и остатки, которые когда-то утилизировались, теперь с помощью оборудования MB трансформируются в новый источник прибыли с существенной выгодой для экологии. Специалисты MB Crusher разработали и изготовили машины, которые превращают погрузчики, мини-погрузчики и экскаваторы-погрузчики в мобильные дробилки и грохоты. Дробильные ковши MB-L и просеивающие ковши MB-LS могут использоваться с машинами массой от 2,4 до 25 т.
В компании Idromeccanica Italiana заявляют, что к ее и так достаточно большому диапазону продукции были добавлены еще три гидромолота из серии IMI: два для машин массой от 4 до 10 т и один для машин массой от 14 до 22 т. Первые два, IMI 28HP и IMI 38HP, доступны в закрытой, малошумной и виброзащищенной версиях. Третья модель может работать с автоматической системой смазки, а также обеспечивает возможность регулировки давления и энергии удара.
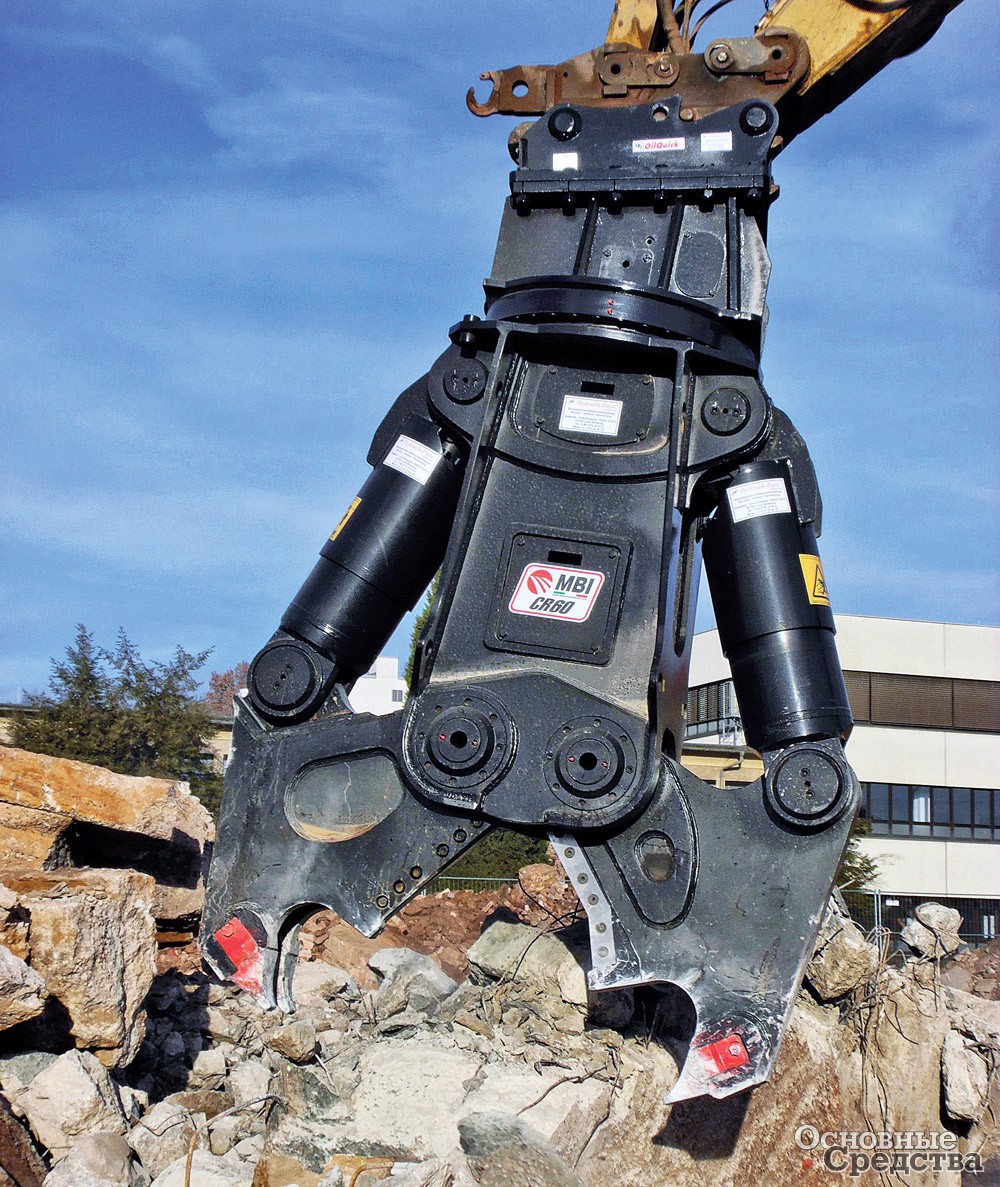
Другой итальянский производитель гидромолотов – компания Mantovanibenne заявила, что новые гидроножницы для сноса CR60R Combi были протестированы в течение 2017 г. и официально запущены в производство в январе 2018 г. Пробный экземпляр разрабатывался для одного из крупнейших подрядчиков в Германии с учетом его специфических потребностей. Mantovanibenne CR60R Combi весит 6,65 т и сочетает в себе конструктивные особенности двух различных линеек продукции MBI: гидроножниц CR для строительных конструкций и ножниц для резки металла SH Eagle II. Этот новый инструмент был создан специально для разрушения армированных железобетонных конструкций, а также для бетонных зданий со стальным каркасом.
Срубка оголовков свай всегда была трудоемким и сложным процессом. По своей натуре резка свай производится зачастую довольно грубыми способами. Наиболее распространенными методами являются использование подвешенной к экскаватору на цепях круглой насадки с соединенными по кругу гидравлическими цилиндрами или ручного инструмента, например отбойного молотка. Оба эти метода имеют существенные недостатки. Насадка оставляет армирующую сталь и много мусора, а также может оставить трещины в теле сваи. Выполнение этой задачи вручную происходит очень медленно (20–30 оголовков за смену) и небезопасно для рабочего. Концепция финской компании MotoCut подразумевает использование режущего инструмента с гидравлическим приводом и парой алмазных кругов, который устанавливается на экскаватор с помощью тилтротатора. Не удивительно, что впервые это оборудование было опробовано в Скандинавии. Производительность при новом методе составляет около 150 свай в день.
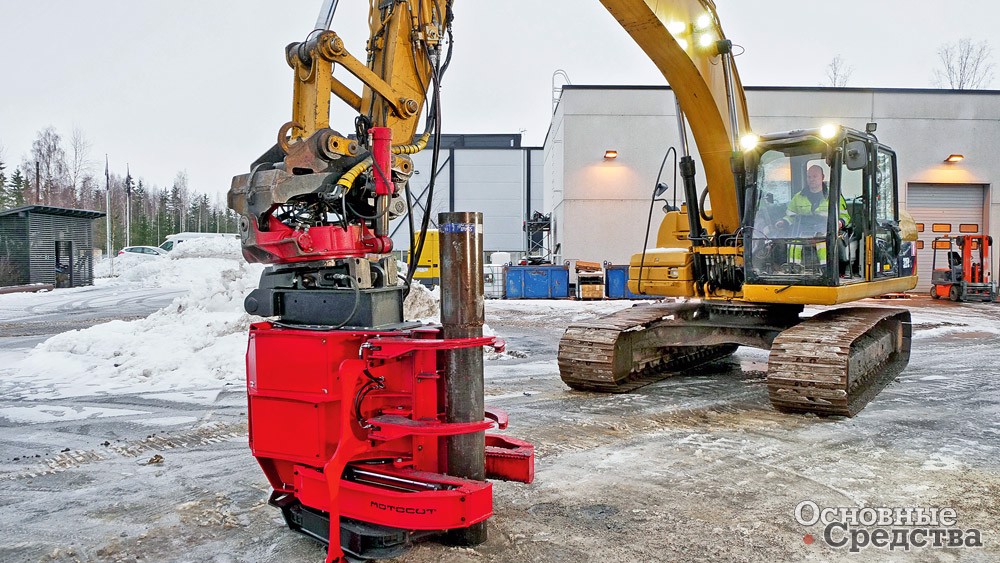
MotoCut Q350 – самый маленький резак в линейке из четырех моделей. Он предназначен для резки квадратных свай со стороной от 200 до 350 мм. MotoCut Q350 массой 465 кг подходит для экскаваторов весом от 8 до 25 т с расходом масла в гидроконтуре 60 л/мин. В дополнение к опции автоматической резки оператор может выбрать различные виды резки или срубку по шаблону, в том числе возможность резать с обеих сторон одновременно или только с одной стороны. В зависимости от размера сваи для резки одного оголовка требуется менее одной минуты. Когда резка закончена, оператор использует челюсти, чтобы переместить отрезанную верхнюю часть сваи. Для удаления пыли и охлаждения алмазных кругов из пластикового резервуара, установленного в задней части экскаватора, подается вода. Комплекта алмазных кругов хватает на полтора-два дня работы для срубки от 200 до 300 свай.
Однако это не единственный инновационный продукт от MotoCut. Также впервые в мире предлагается плазменная навеска для резки трубчатых стальных свай и труб диаметром от 166 до 406 мм с толщиной стенки до 25 мм для экскаваторов массой от 13 до 20 т, оборудованных гидролинией и тилтротатором. Управление процессом плазменной резки полностью автоматизировано. Как ожидается, это решение будет интересно не только подрядчикам, которые занимаются обрезкой свай, но и компаниям, занятым в индустрии сноса.
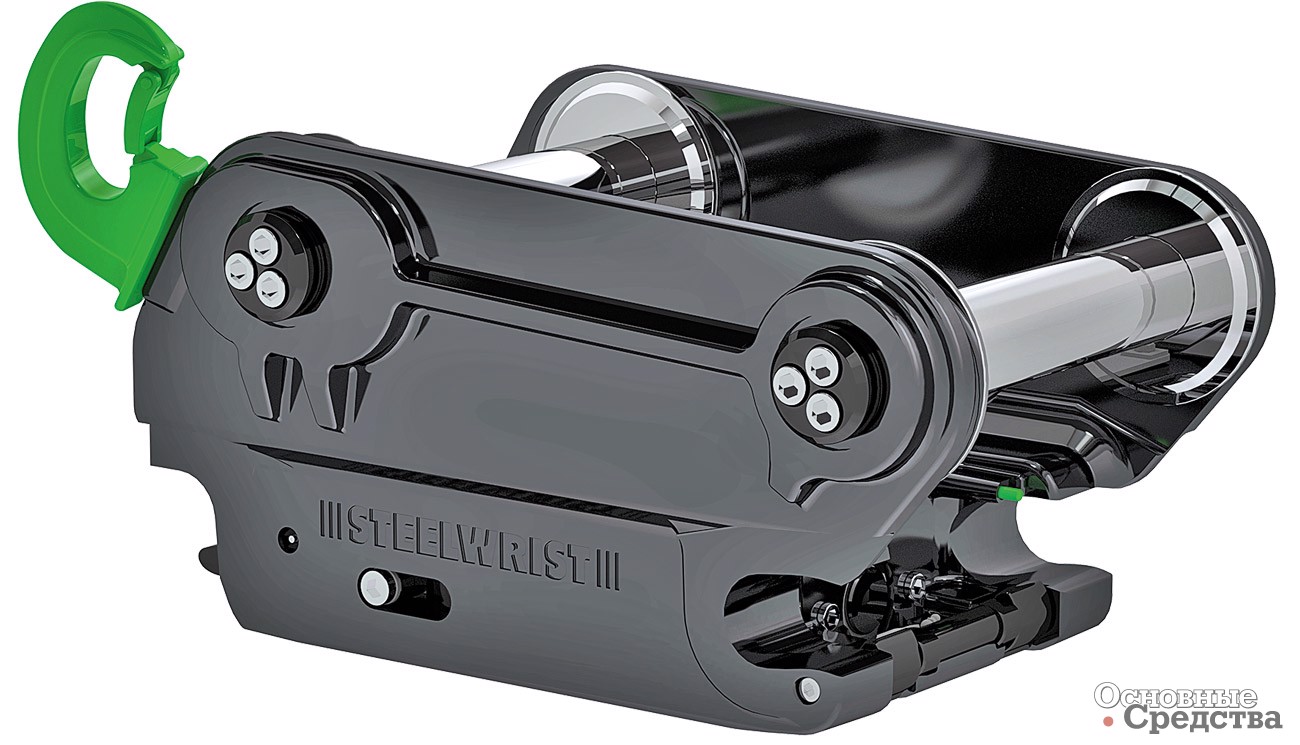
При подборе навесного оборудования необходимо учитывать ряд особенностей. Во-первых, следует подбирать инструмент, который лучше всего подойдет для конкретного применения. Если речь идет о демонтаже, надо понимать, будет оборудование использоваться для первичных работ, например для разборки конструкций, или для вторичных, таких как резка арматуры, разрушение и измельчение бетона и железобетона. Если рассматривать гидроножницы, надо проанализировать, для каких целей они предназначены: для демонтажа или для резки лома.
Общение с дилером или производителем поможет определить, какое устройство подойдет лучше всего для конкретных работ. Навесное оборудование должно соответствовать массе и размеру носителя. Для тяжелых навесных моделей требуются более тяжелые носители.
Важно убедиться, что машина-носитель имеет достаточную гидравлическую мощность для обеспечения нормальной работы соответствующего навесного оборудования. Недостаточный расход увеличивает время рабочего цикла инструмента, в то время как слишком малое давление приводит к более низкому усилию закрытия или уменьшению крутящего момента в зависимости от типа оборудования. Наконец, нужно проверить, оборудована ли машина-носитель достаточным количеством дополнительных гидравлических контуров.