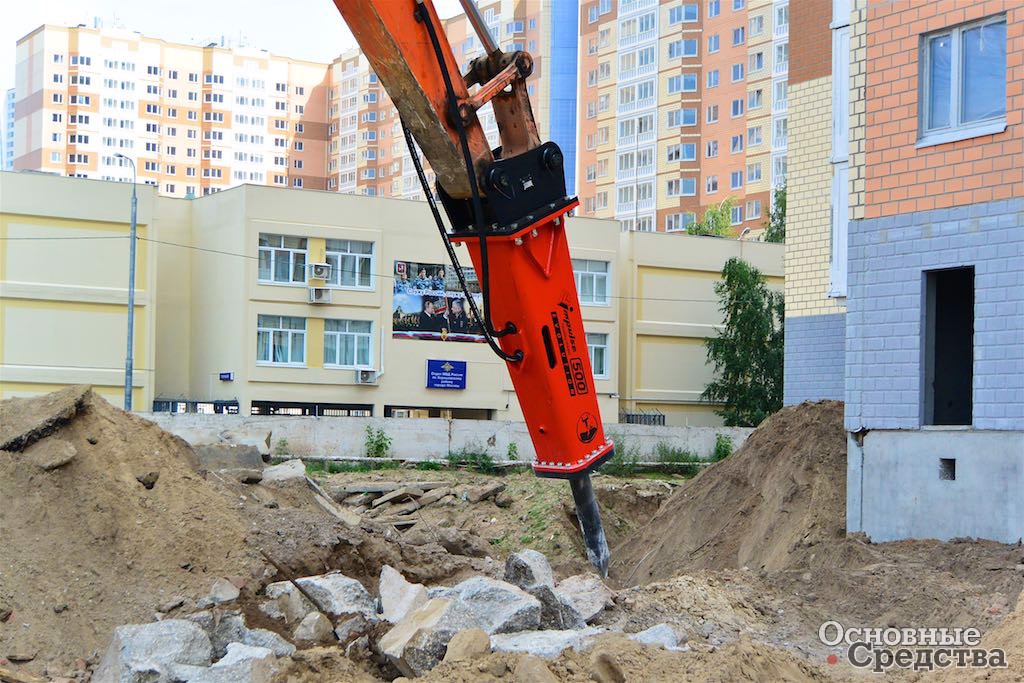
Гидромолоты Impulse Evolution
Отсутствие стяжных болтов
Оба этих конструктивных решения, при всех различиях, имеют ряд сходных элементов – в частности, это наличие шпилек, стягивающих центральный блок. 99% существующих гидромолотов структурно выглядят именно так. Стяжные болты у них могут отличаться только формой и длиной. Сами шпильки гидромолота довольно прихотливы в обслуживании, ведь протягивать их нужно минимум раз в неделю, а при активной работе – и вовсе раз в два дня. И здесь для эксплуатирующей организации есть сразу две трудности: первая – то, что оператор в России инструкцию не читает и стяжные болты не протягивает; вторая – то, что на средних и тяжелых гидромолотах в закрытых корпусах для протяжки шпилек необходимо снимать подвеску. Последнее требует от оператора потери рабочего времени и остановки рабочего процесса на 4-5 часов. И при всем желании оператора дать оборудованию должный уход – не всегда есть такая возможность на объекте, где горят сроки. И что в итоге? В итоге мы имеем лопнувшие шпильки – одну, а за ней и вторую (обычно находящуюся по диагонали). Если гидромолот при работе совершает много холостых ударов, когда вся его энергия попадает не на разрушаемый материал, а остается в самом молотке, тогда шпильки центрального блока испытывают растяжение и, в конце концов, лопаются. Или в случае с не вовремя протянутыми стяжными болтами: при разном моменте затяжки шпильки испытывают разную нагрузку друг относительно друга, в связи с чем наиболее нагруженный элемент лопается. При этом лопнувшую шпильку при работе оператор даже не заметит, ведь гидромолот работает шумно. Лопается вторая, а за ней идет перекос во всей конструкции молота, задирается боек и гильза, неравномерную нагрузку принимает на себя инструмент. Это капремонт в половину стоимости нового молота.
Наше конструкторское бюро ценой десятилетних исследований и поисков нашло решение этих проблем. Мы создали новое поколение гидромолотов без стяжных болтов. Ударный блок в них – это единый цилиндр. Сейчас мы можем предложить своим клиентам оборудование, не требующее протяжки шпилек, а потому более дешевое в использовании! Главная проблема отрасли нами решена!
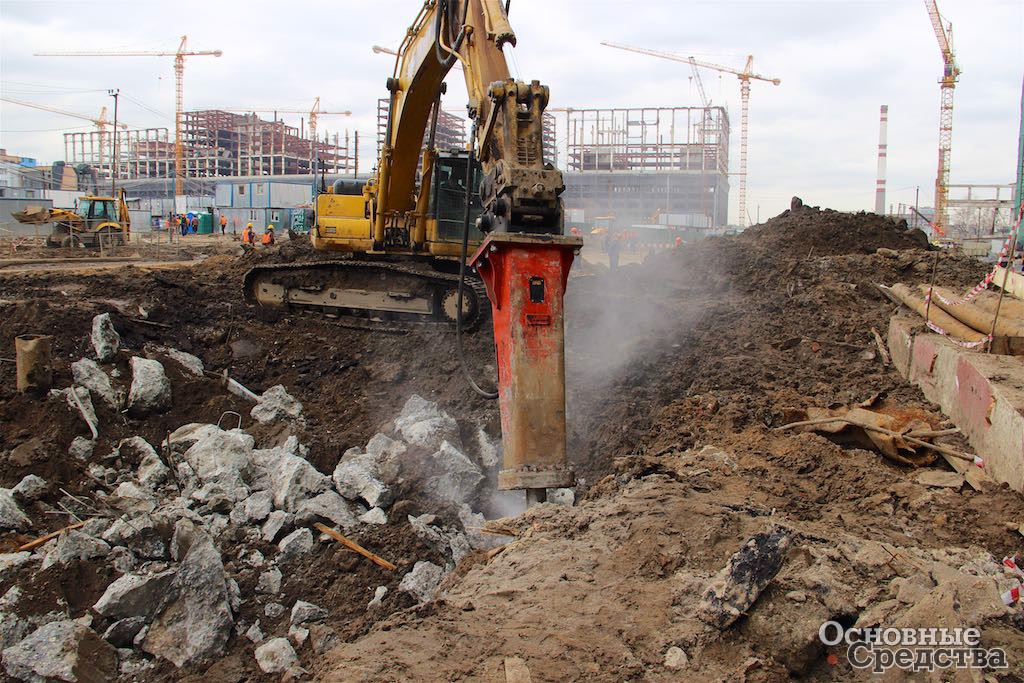
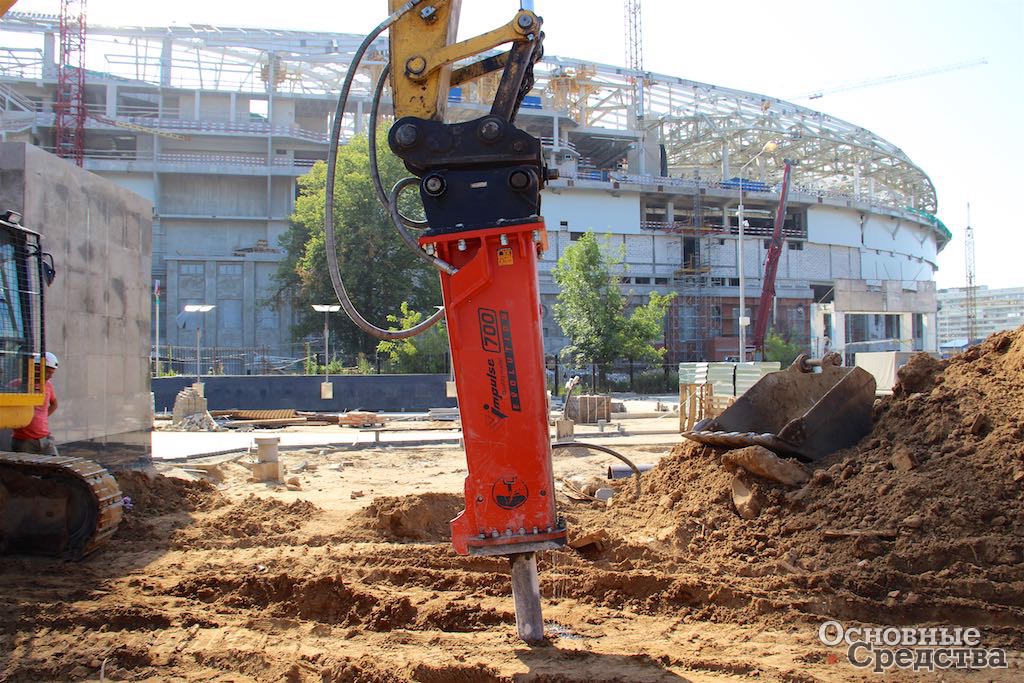
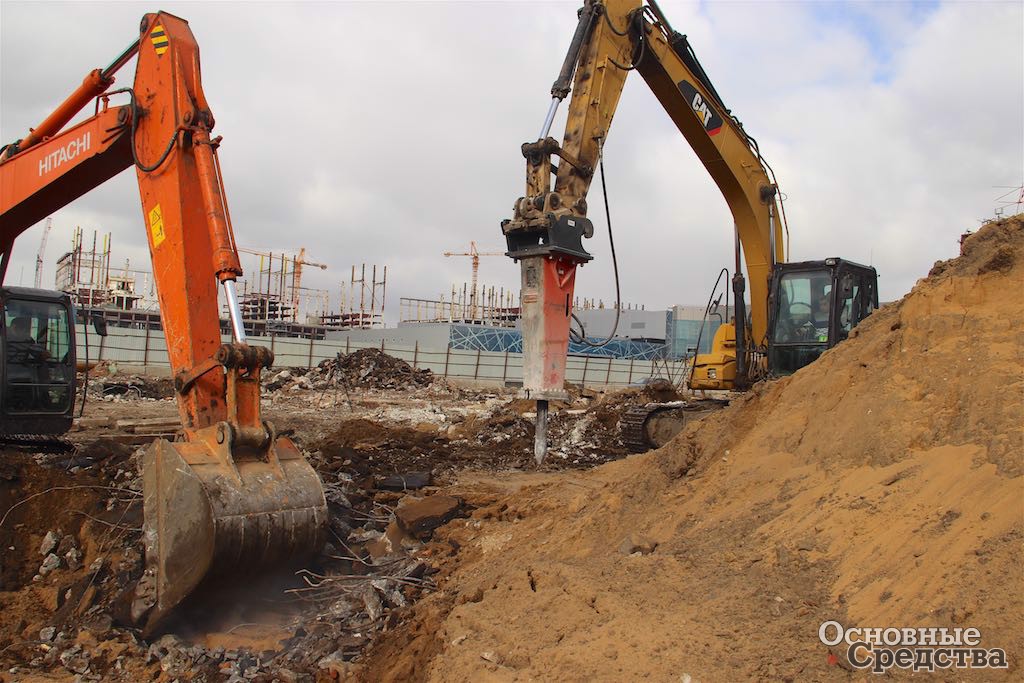
Сниженный уровень шума и вибрации
Что важно для вас при покупке нового гидромолота? Его цена, наличие на складе поставщика, производительность. При этом мы упускаем кое-что существенное – уровень производимого шума и вибрации, которые вредят здоровому слуху людей и снижают безопасность на стройплощадке. На что обращают внимание сами операторы в работе гидромолота? Вибрационная нагрузка на рабочие органы экскаватора, отдающаяся в кабину, и высокий уровень шума, снижающий общую производительность труда, а значит и вашу прибыль!
Ведущие инженеры ООО Технопарк «Импульс» ценой трехлетних изысканий и полевых испытаний нашли решение обеих этих проблем! Более ста конструкторских решений было опробовано нами перед тем, как мы нашли то, что искали! Уровень шума почти на 20% ниже самых тихих импортных гидромолотов, а вибрация почти не ощутима в кабине машиниста. Судите сами!
Решение – в использовании полиуретана, который одинаково хорошо показывает себя как в звукоизоляции, так и в гашении вибрации. Мы нашли собственную технологию изготовления полиуретана, сохраняющего жесткость структуры: многие месяцы мы обменивались опытом с американскими и европейскими производителями компонентов. Сейчас мы предлагаем вам совершенно новое поколение гидромолотов, в которых общий объем демпфирующего полиуретана увеличен до 4х раз по сравнению с любыми другими гидромолотами мира! В итоге, вы получаете значительно сниженный уровень шума и вибрации, более комфортные условия для работы оператора, больший срок службы сочленений рабочего оборудования машины, а следовательно – беспрецедентно высокую производительность!
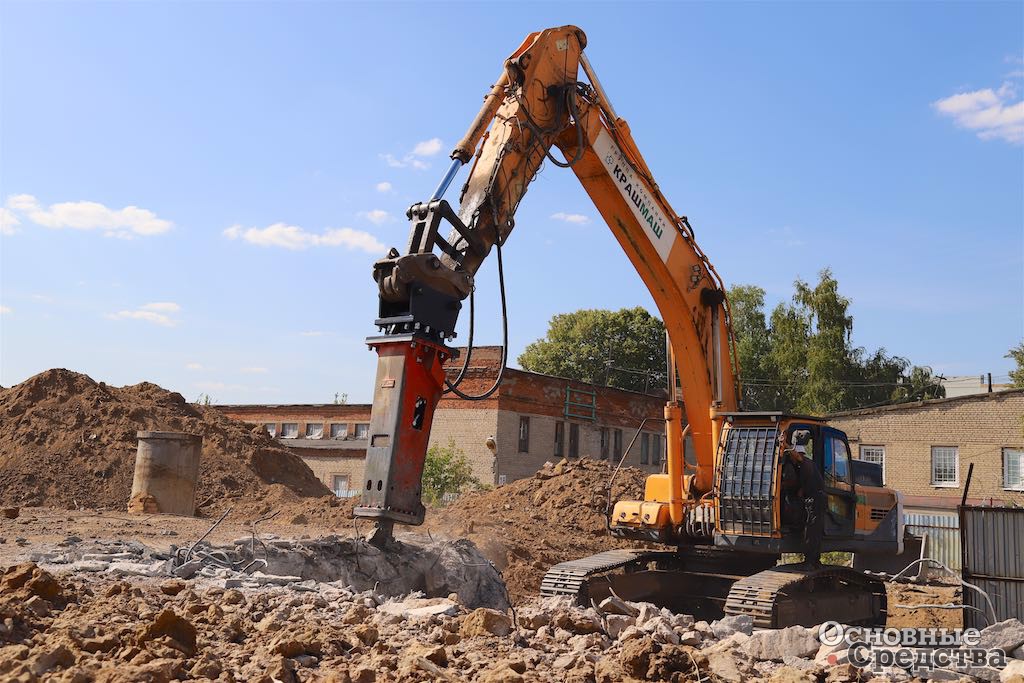
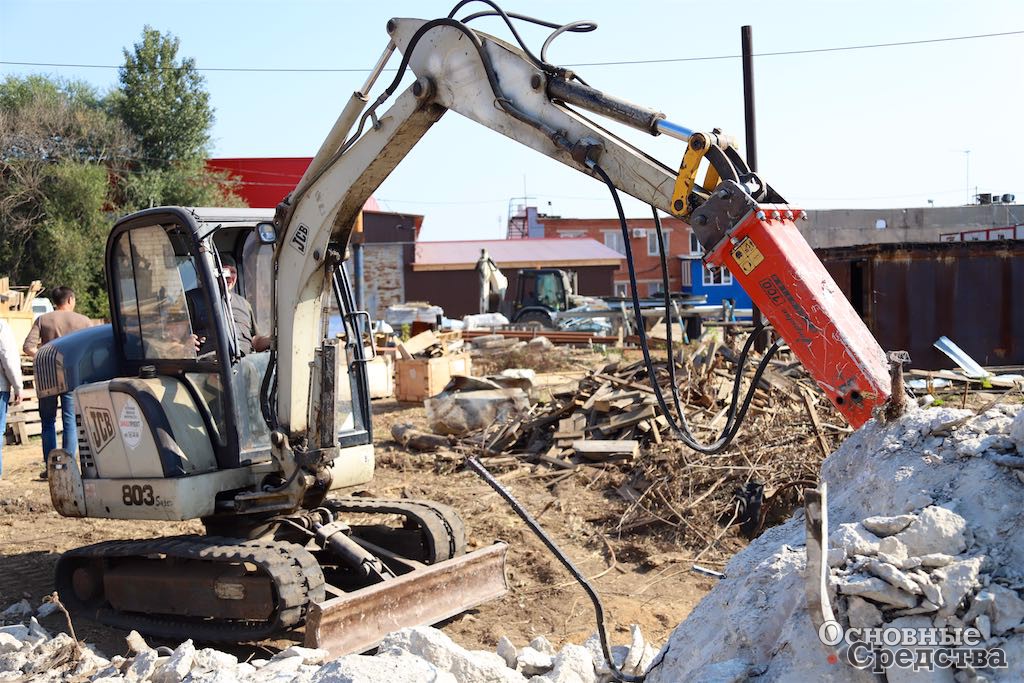
Автосмазка гидромолота
Инструкция по эксплуатации любого гидромолота гласит: необходимо смазывать втулки через пресс-масленку каждые 2-3 часа работы. Но во всем мире операторы этого не делают. И в России это - тоже хорошо знакомая нам ситуация. Поэтому ведущие производители гидромолотов стали комплектовать свои изделия системами автосмазки. Это – небольшой насос, подающий смазку из картриджа и находящийся на корпусе молота. Минусы у этого решения тоже есть:
- смазочный картридж нужно заменять в среднем раз в 10-12 часов;
- на объекте необходимо поддерживать складской запас этих картриджей, иначе по их окончании придется возвращаться к ручной схеме смазки;
- высокая стоимость картриджей, аналог к которым подобрать невозможно;
- нет защиты системы автосмазки от механических повреждений.
Как быть, если вы не готовы тратить полмиллиона рублей ежегодно на оригинальные картриджи для автоматической смазки, но хотели бы пользоваться этим удобным решением в работе?
ООО Технопарк «Импульс» готов предложить вам кардинально новое решение, в котором:
- межсервисный интервал увеличен до 500 часов! Сравните с 2-3 часами при использовании ручной смазки и с 10-12 часами при работе с автосмазками других производителей гидромолотов!
- вся система запатентованной автосмазки ImLube спрятана в корпусе молота и защищена от механических повреждений
- для дозаправки контейнера вам подойдет консистентная смазка для гидромолотов – от любого производителя ГСМ!
- автосмазка ImLube будет комплектоваться с гидромолотами Impulse Evolution в закрытых корпусах для полноповоротных экскаваторов от 12 тонн и выше
- насос автосмазки защищен от остановок из-за изменения в консистенции смазки (очень низкая или очень высокая температура окружающей среды)
Принцип максимальной отдачи гидромолота Impulse Evolution на каждый инвестированный в него рубль – во главе угла!